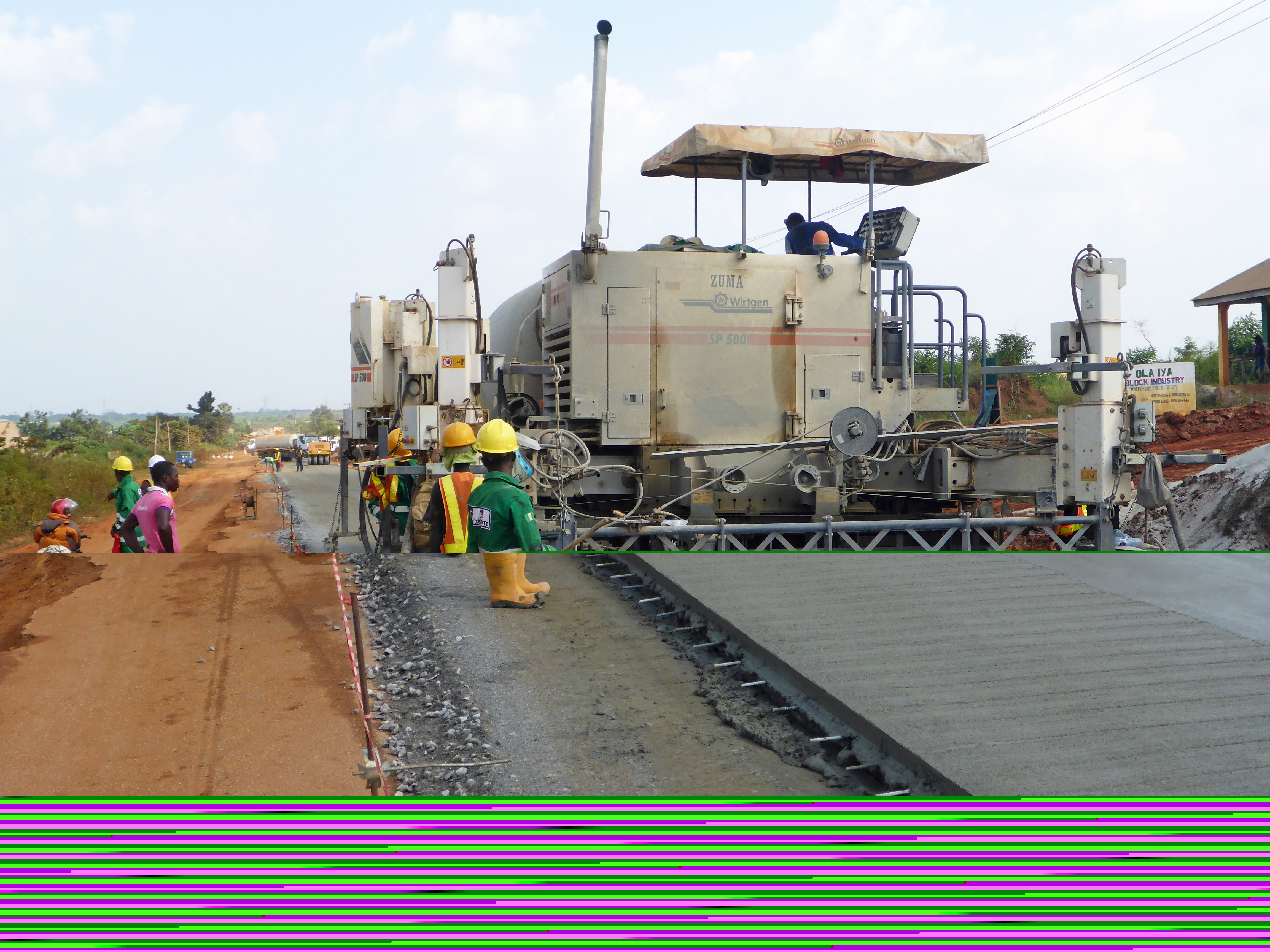
AG-Dangote Construction Company used an SP 500 model to repave the road connecting Itori with Ibese, In Nigeria’s Ogun State.
For this project, the contractor, a joint venture between the Brazilian company
For the inset application, the concrete is either deposited right in front of the slipform paver or is fed in front of the machine from the side via a belt conveyor or side feeder. In the next step, the concrete is distributed evenly across the full paving width by a spreading auger or spreading plough. Integrated electrical or hydraulic vibrators ensure homogeneous compaction of the concrete. The inset mold forms the concrete slab to the specified thickness and width while the slipform paver advances. In addition, a dowel bar inserter can be integrated which inserts the dowel bars into the concrete as specified parallel to the paver’s direction of travel. Central tie bars or side tie bars can be inserted transverse to the concrete pavement. The surface is levelled off transverse to the paver’s direction of travel by the finishing beam. The grinding movement produces a small concrete roll in front of the beam which boosts the quality of the concrete surface. In the next step, a super smoother, oscillating in
a combination of lateral and longitudinal movements, ensures the final surface accuracy. Texture curing machines then deliver the surface, applying a dispersion to the concrete surface that prevents the surface and edges from drying too quickly.
Before the slipform paver was able to begin work in Itori, the substrate first had to be prepared. The construction company used compacted laterite and a 200mm layer of crushed rock. “The SP 500 then paved the concrete quickly," explained Ashif Juma, managing director of AG-Dangote Construction Company. Juma added that the machine’s production quality met the specifications for surface evenness. The SP 500 laid down the new 7.5m-wide and 200mm-thick roadway in two separate passes. Extending over 24km, the new road is the longest stretch of concrete roadway in Nigeria.
To provide the concrete paver with sufficient material, a convoy of up to 15 concrete-mixing trucks drove to the job site. The Dangoye Group is itself one of Africa’s largest producers of cement and supplied the raw materials needed to make the concrete from its limestone quarry in Ibese, where the material is extracted using the firm’s 14 Wirtgen surface miners. These 2500 SM surface miners cut, crush and load the rock in one single operation. The rock is broken down directly during the extraction process into grain sizes that are suitable for belt conveyors, so there is no need to use a crusher.
“The SP 500 not only ensured that the construction project processing went off without a hitch, but also produced a paving result that impressed both us and the client. We processed more than 35,000m³ of concrete using the Wirtgen slipform paver, and produced a very even surface,” said Juma.
Work on the 24km concrete roadway was completed after six months of construction. After completion of the paving work, a concrete cutting machine cut slits at right-angles into the road surface at intervals of 3.65m so that the resulting joints could be filled with expandable material. These predetermined breaking points prevent potential tension cracks. “With professional maintenance, this will ensure that the roadway lasts for at least 40 years," said Juma, explaining the last step of the construction procedure. Pleased with the success of the project, Juma also decided to acquire additional concrete equipment from Wirtgen. AG-Dangote Construction Company Limited has expanded its fleet of road construction machines, purchasing two of the last SP 500 pavers produced, along with a TCM 95 texture curing machine.