High production concrete paving is proving a key feature at the new Berlin airport facility currently under construction The new Berlin-Brandenburg International Airport will soon provide improved links by air to the city. Work started in mid 2006 with the redevelopment of the existing Berlin Schönefeld Airport.
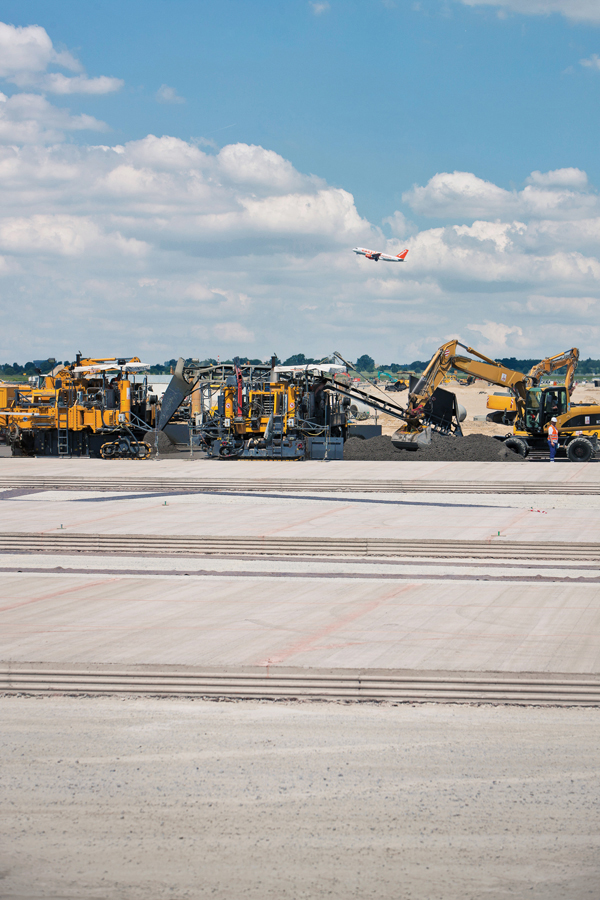
Aircraft still land and take off at the existing Schonefeld Airport, some 2km to the south
High production concrete paving is proving a key feature at the new Berlin airport facility currently under construction
The peoject is being aided by a fleet of
To handle the project, contractors
Senior site engineer Christoph Hofmeister for Max Bögl said, "We will be placing some 600,000m3 of pavement concrete altogether over the entire project. If everything goes smoothly, a large Wirtgen paver is capable of processing 6,000m3 of concrete within 24 hours." This huge project requires efficient planning and logistics, which is a complex task given the number of personnel at the site. Of the 350 people working for the joint venture each day around 90 are directly involved in the concrete paving operation, with 15 on each paving train. These also include personnel carrying out work such as installing and removing the vertical formwork, cutting joints or supplying dowel bars.
The new southern runway will cover an area of 240,000m2, with a length of 4km and a width of 60m. To enable large aircraft like the Airbus A380 to land and take off at the airport, a 1.3m thick pavement structure was designed for the southern runway and for all the other movement areas. In a first step, the 500mm thick bottom layer, which contained both non-cohesive and cohesive soil, was stabilised using cement. The next 150mm thick layer features a stabilised mixture of hydrophobic cement and frost-proof sand. The contractors used Wirtgen machines for this work also and the job was carried out by several WR2500S soil stabilisers. This next layer is a 250mm thick hydraulically bound base layer. For the final step, the slipform pavers placed a 400mm thick concrete layer between vertical formwork with sinusoidal cross-section. Planning and realisation specified a non-reinforced concrete design with longitudinal and transverse joints.
Airport runways require first rate finish and load bearing capacity and the materials and processes needed to meet high standards. An air-entrained crushed aggregate concrete capable of taking extremely high loads has been used as this material is able to withstand the tremendous mechanical loads imposed by the big aircraft just as easily as the high temperatures generated during landing or the application of de-icing agents in winter.
The concrete is being supplied by Europe's most modern mixing plant, located in the immediate vicinity of the construction site. In up to six high-performance concrete plants, which are in operation around the clock, up to 11,000m3 of concrete/day can be produced for both pavement and building construction. Cement, sand and aggregate are supplied by rail to reduce road congestion by minimising the heavy vehicle movements.
The raw materials needed for concrete production are ordered on the basis of monthly and weekly requirements planning. The specified quality of concrete is then produced and supplied to the paver based on detailed day-to-day planning and current weather forecasts. Up to 50 trucks are available for the job. A quality assurance plan ensures the specified concrete quality by means of several accompanying material tests.
The paving gangs working at the slipform pavers are responsible for the paving quality. At times all three large slipform pavers, the SP1500L, SP1500 and SP1600, are in operation on the runways and taxiways at the same time. They are paving the concrete in a single-course, dual-layer operation, which means that one and the same type of concrete is used for both concrete layers. This features a 330mm bottom layer and a 70mm top layer. Between the two layers, the dowel bars are positioned at evenly spaced intervals by the automatic dowel bar inserter (DBI). Evenness is ensured by a finishing beam and super smoother. Two TCM1800 texture cure machines follow behind the pavers, applying the broom finish as well as a liquid curing agent. Depending on weather conditions, these two operational steps are performed separately by two separate machines.
With a peak-to-valley depth of more than 1mm, the concrete pavement offers good tyre adhesion. Premature drying of the concrete is prevented by applying a layer of approx. 220grammes of curing agent/m2. Constant wind and the high peak-to-valley depth require this amount of curing agent to be applied to reliably prevent the formation of cracks.
Repositioning and reconfiguration of the pavers are important factors in the job and the veratility of the machines has been crucial. The concrete pavement has been laid down at different widths in the various sections and this has required the machines to be converted several times to working widths ranging from 12.5-15m.
The concrete was paved between vertical formwork with sinusoidal cross-section, which enabled compliance with the high demands placed on the longitudinal compression joints. To produce the correct level and slope, the airport builders used transducers scanning a stringline or slab tracers scanning the previously paved concrete slab. This enabled them to comply with the evenness requirements and to produce the necessary cross slope of 0.7-1.5%.
The Wirtgen machines have proven reliable and versatile in this tricky application and Wirtgen also supplied training to the paving teams as necessary to ensure they could meet the tough quality and productivity demands of the job.