Bitumen technology is benefiting from years of research and development - Kristina Smith. On a 2.7km loop of road in Auburn in Alabama, US, a lorry driver drives his triple-truck round and round. During his eight-hour shift, he will have covered 544km, with another driver waiting to take over from him for the next shift. Their mission is to seriously damage the road. This is the National Center for Asphalt Technology (NCAT), where sponsors from states and private companies pay to test out new materials and
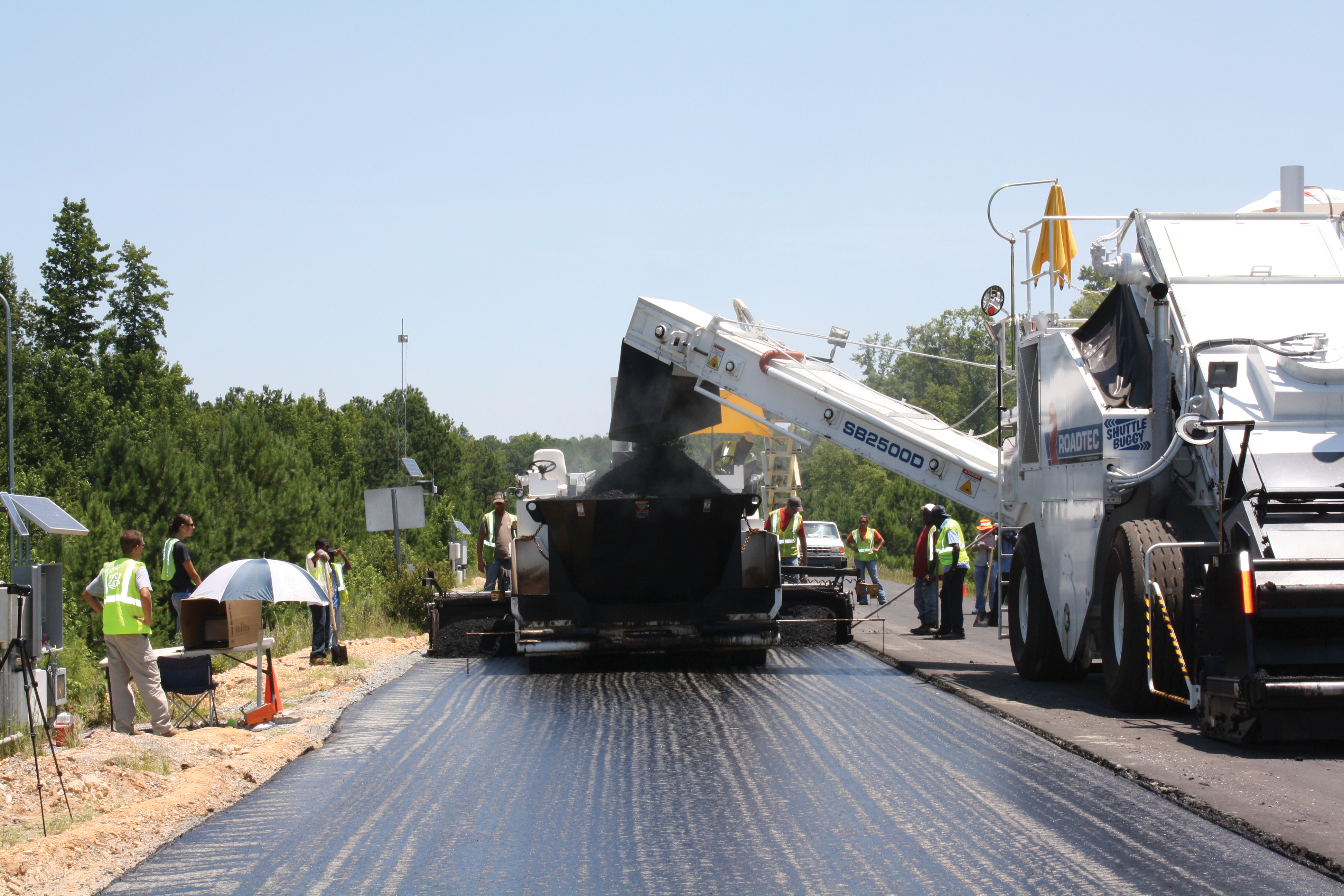
The NCAT test facility in Alabama is used to monitor the performance of road materials using heavily laden trucks being driven continuously over the track to simulate highway conditions
Bitumen technology is benefiting from years of research and development - Kristina Smith
On a 2.7km loop of road in Auburn in Alabama, US, a lorry driver drives his triple-truck round and round. During his eight-hour shift, he will have covered 544km, with another driver waiting to take over from him for the next shift. Their mission is to seriously damage the road.This is the National Center for Asphalt Technology (NCAT), where sponsors from states and private companies pay to test out new materials and pavement designs. NCAT’s fleet of trucks operate for five days a week from 5am to 11pm, cramming a design life’s worth of loading into two years.
On section N7 on the North side of the track,
Kraton calls its technology HiMA (highly modified asphalt). “Usually in asphalt paving, you are stuck between a rock and a hard place: the things you do to a pavement to make it not rut are exactly the opposite to the things you do to make sure it doesn’t crack,” said Bob Kluttz, senior staff scientist, research and development, who has been working for Kraton on asphalt modification for the past 20 years. “What we have in HiMA is something that’s crack resistant and rut resistant.”
This trial in Alabama is testing out a structural pavement construction which mimics the conventional design against which it is being compared in all but thickness and bitumen. Rather than 178mm thick, this pavement is 146mm thick, a reduction in thickness of around 20%. HiMA could allow even thinner layers, said Kluttz: “Some of the modelling work we have done says that we could reduce the thickness by 50% and still get good or better performance, on a very good soil or if we were paving over a solid base.”
The vital ingredient in Kraton’s innovative binder is D0234, a styrene-butadiene-styrene (SBS) polymer. What makes D0234 special is that it allows more SBS polymer to be added to bitumen without it becoming too stiff to work with: the HiMA used on this trial contains 7% SBS, which with standard SBS would produce an intractable mixture. Kraton expects to publish results from the NCAT trial in late February. At the same time it has other trials running in several different States in the US and in different countries around the world.
At NCAT – uniquely – the pavements are designed to fail, hopefully towards the end of the compressed design life cycle. Going out into the real world, Kraton searches for problem roads where clients are in need of a new solution. “We look for the worst cases where agencies are scratching their heads, where they are having to fix a road every year or two,” said Kluttz. “That way, we don’t have to wait 10 years to find out if the project worked.”
In the US, the majority of Kraton’s trials are not in the structural layers of the road but in thin overlays. A change in philosophy in the US and Canada, away from capital outlay and towards service life and asset management, means that roads authorities are willing to pay more for a longer-lasting product.
“Because of their budget considerations, there’s a lot of emphasis being placed on the performance value of the asphalt mixes that are used and there’s a willingness not to just look at initial cost,” said Peter Montenegro, market development manager, paving and roofing, for Kraton. “If it can gain for them additional service life and greater durability, there’s an acceptance of the idea of paying an additional premium.”
Beyond North America, Kraton predicts there is a worldwide market for HiMA, which will encompass both structural and surfacing elements of pavements. “It has potential applications anywhere where liquid asphalt would be used,” said Kluttz. One of the first trials was at Port Napier in New Zealand, where the pavement had been suffering catastrophic rutting due to the movement of sea containers (see
Elswehere, Kraton has trials in Australia, two chipseal trials in Brazil with a further two structural trials planned there, and several trials in Western Europe, Eastern Europe and the Middle East.
Meanwhile as contractors in Qinzhou City, Guangxi Province in China laid the one hundredth road to use
“This next generation is going to be completely targeted at the upper layers,” said John Read, Shell technology manager for bitumen. “Thiopave can already be used there – and has been - but we think further improvements can be made that will give us that next generation.”
The new surfacing product has been put through its paces in Shell’s extensive research and development facility in Bangalore and then in its Solution Centres around the world which customise technologies to local markets. And in November 2011, Shell laid the first trial surface in Bejing. “We will be looking to monitor that trial and to lay several other trials for the next 18 months to two years,” said Read.
Shell concentrated first on the structural layers of the road with Thiopave, because this is where its benefits of significant increase in load bearing capacity, combined with the same or better fatigue life come to the fore. It is the crystallisation of elemental sulphur throughout the mixture which brings the improved structural rigidity.
It was in the late 1990s-early 2000s that Shell returned in earnest to develop the technology of combining bitumen and sulphur in a binder. The development process began in the 1970s due to the oil crisis, when 100 roads in the US, Canada and the UK were laid using a combined sulphur and asphalt binder, but then was discontinued as oil supply increased again.
The trigger for dusting off the development work was the increasing demands being put on pavements around the world. “It became very obvious that the volume of traffic was growing exponentially, and the axle loadings of lorries which cause the majority of the damage on roads, was increasing,” said Read.
Back in the ‘70s sulphur was tricky to work with, delivered as a liquid which required dedicated tankers, storage and pipework. Now, Thiopave comes in pellet form, containing a plasticiser to keep the pellets intact, Hydrogen Sulphide scavengers to mop up any gas which might be produced and other additives which will vary depending on the country.
Since the first pellets rolled off the production line in 2002, Thiopave has been used on 50 projects in China, 30 in the US and Canada, 10 in Europe and 10 in India and the Middle East. The size of project has grown over that period, with the project in Guangxi using 10,000tonnes of asphalt on a 3km stretch of the Nanning-Beihai Expressway 2, being Thiopave’s biggest to date.
The next generation, aimed at surfacing, will have its greatest market initially in the developed world where dwindling maintenance budgets mean that clients are on the lookout for new ideas, says Read: “Client authorities are ever-more receptive to finding ways to extend the value we can get from our pavements.”
And additive specialist
“The fibres offer several advantages when used in the reinforced base and wearing course for highly trafficked areas or airport runways,” said Iterchimica engineer Filippo Montanelli. “In addition, in areas where PMB is not easily available, such as developing countries, these fibres are a viable solution for durable pavements. They could also be useful in countries like the UK where only small quantities of material are needed.”
The fibres come in a pellet form which can be safely and easily stored. They can also be used with PMB to enhance its performance.
Iterchimica has been working with Milan University for four years to develop and test a range of fibres. The first to be available commercially is Iterfibra CS, which is a mixture of cellulose and synthetic fibres.
The fibres have been used on several projects in Italy, including main roads and Milan’s Malpensa and Bergamo airports where they were added respectively to the binder course and high friction wearing course on new parking areas for the Airbus A380 airliner. Overseas, Iterfibra CS has been used on a main highway in Ukraine and projects in Mexico and Algeria. Cellulose fibres have traditionally been used in Splittmastix or stone mastic asphalt (SMA) to increase the viscosity of the bitumen. This prevents bleeding of the asphalt in warm weather and increases the strength of the pavement.
Tests at Milan University have shown that the cellulose and synthetic mix fibres raise the softening point of bitumen. “The material has the flexibility of 50/70 bitumen but has the capacity to withstand higher temperatures of up to 100 degrees C which means it is less prone to rutting,” said Montanelli.
The next round of research for the fibres will be to prove them as a reinforced wearing course which will provide a stronger resistance to crack propagation. This will be useful in situations where the binder course is partially cracked but authorities only have the budget to replace the wearing course, said Montanelli.