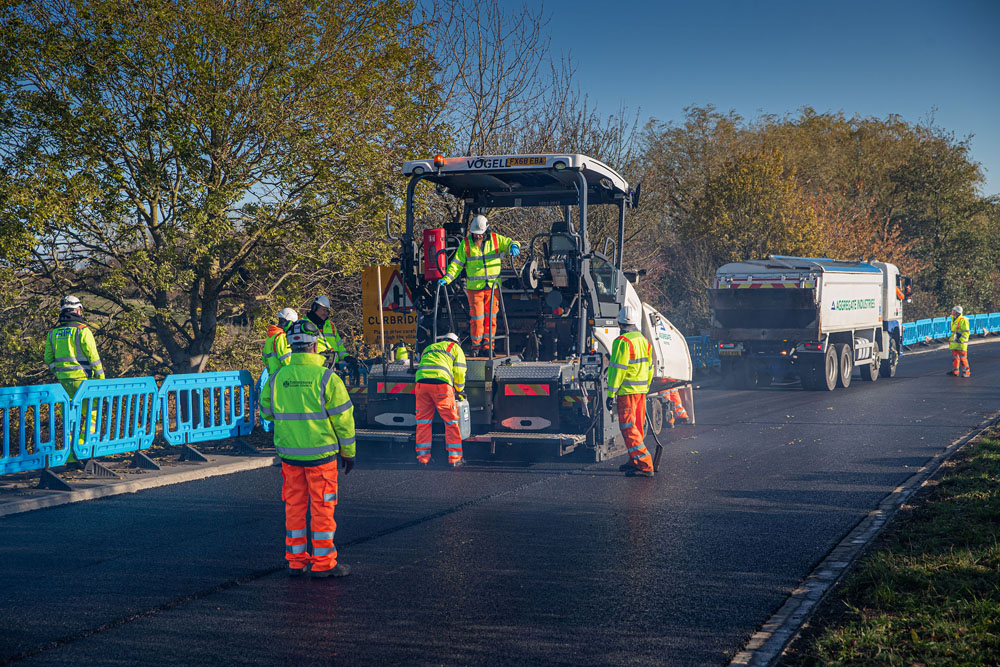
Graphene-enhanced roads trialled in UK
Graphene-enhanced asphalt has been used for the first time outside Italy, where it was developed. Contractor Skanska laid a trial section of Gipave, developed by road additive specialist Iterchimica and graphene-based product supplier Directa Plus, in November last year for Oxfordshire County Council.
The 750m section of main road in the village of Curbridge in Oxfordshire takes 6,000 vehicles/day, 300 of those commercial vehicles. One side of the single-carriageway road has been paved with a standard mix while the other side has been paved with asphalt containing Gipave – either in the binder course only, the wearing course only, or both. Aggregate Industries supplied the asphalt.
“We chose it because it was the most heavily trafficked road that we had in our forward programme for Oxfordshire County Council,” explained Richard Lovewell, Skanska’s business director for Oxfordshire where the contractor has a £40 million/year contract to maintain the county’s roads.
Gipave is an additive for asphalt which is made up of three components: technically selected waste plastics, an active compound made of additives from Iterchimica, and G+ graphene from Directa Plus. Graphene makes the asphalt stronger without making it more susceptible to cracking.
“Based on laboratory and on-site results and using software to predict the life of pavements, we can say that a pavement made with Gipave can be two or three times more durable than a pavement with PMB,” said Lorenzo Sangalli, product manager for Iterchimica. Laboratory tests have shown that asphalt made using Gipave has up to 300% better fatigue performance and 80% less rutting than standard PMB.
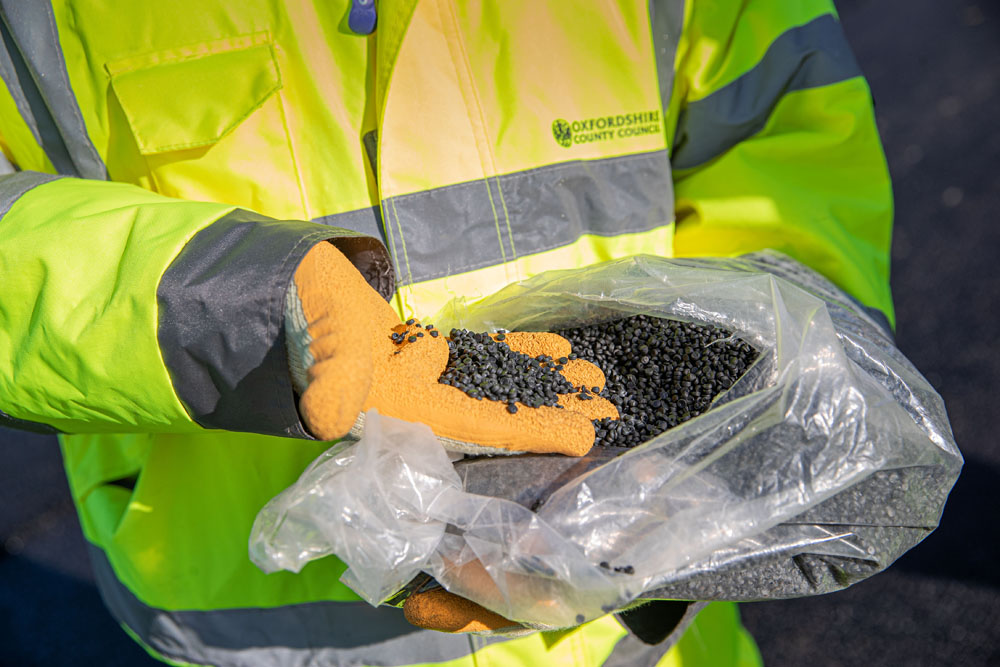
The waste plastics used in Gipave are a specific type of hard plastics, which would not normally be recycled, usually ending up in an energy-to-waste plant. “These plastics need to have a specific chain of polymers,” explains Sangalli. “We tried several types of plastics for the modification of the asphalt mixtures, for example plastic from toys and chairs, but not all of them are suitable for use in asphalt mixtures.”
Gipave was developed during a four-year European Regional Development Fund project called Ecopave. The partners in the project were Iterchimica, Directa Plus, waste company G.ECO which was responsible for providing plastic waste, and the University of Milan Bicocca which is carrying out testing and analysis. In addition to identifying plastic waste with the right polymer components, another challenge was how to disperse the graphene throughout the additive. “When using nano materials, there is always the challenge of how to produce a uniform final product,” explained Dr Shahin Eskandarsefat, a senior researcher at Iterchimica. “You are working with a very, very low quantity that you need to disperse homogeneously in the mixture.”
The Gipave additive comes in pellets, less than 5mm in diameter, which can be added at the asphalt plant. “It is a dry method, so you don’t need to pay huge amounts for transportation,” said Eskandarsefat. “Polymer modified binders are difficult to transport, and you need energy to keep the bitumen heaters. With this method, you save a lot of energy for heating and for transportation.”
Gipave has already been deployed at a number of locations around Italy: at Fiumicino and Cagliari Airports and on the SP03 Via Ardeatina in Rome. It was also laid on Milano-Meda, a heavily trafficked freeway close to Milan.
In the UK, Skanska is in early discussions with Highways England about using Gipave on a section of London’s heavily trafficked orbital motorway, the M25. Iterchimica also sees North America and the Middle East as good potential markets, with discussions underway with US companies. Cost savings over the lifetime of a road paved using Gipave will vary depending on the costs of paving and maintenance in each country, said Sangalli. Calculations based on costs in Italy show that the material costs when using Gipave are 15-20% more than using a standard SBS (styrene butadiene styrene) PMB. However, after seven or eight years of road life, whole-life cost savings start to kick in, rising to up to 25% after 20 years, according to Iterchimica. These savings do not take into account the additional value due to fewer disruptions to road users and businesses during resurfacing or the aspects related to eco-sustainability and waste recycling.
A 15-20% uplift in material costs would equate to around a 10percent overall increase in paving costs, says Lovewell which would make good sense. “If costs go up by 10% and you get a 50%-plus life extension, that’s good value,” he says. “If we can get that additional durability, we can focus our efforts on real preventative management. If you get 20 years’ life, that’s a massive boon.
“There are some heavily trafficked primary roads out of Oxford, and most of our cities. If we can potentially reduce traffic disruption by 50%, that’s huge.”
Research work carried out at the University of Milan Bicocca has demonstrated that asphalt containing Gipave can be successfully recycled without any additional harmful emissions. The University has almost completed a life cycle assessment for Gipave.
Hanson tackles air pollution with reduced emission asphalt
Hanson has launched a new range of reduced emission asphalt (REA) which lowers harmful air pollutants produced during production and paving by an average of 40%. For authorities in dense, urban areas, this is another tool to help fight peaks in poor air quality.
“There are pressures currently with air quality in London, and in other cities,” said Adrian Hadley, head of technical (asphalt and aggregates) at Hanson. “We saw this as an opportunity to help and support not only our direct customers – the contractors – but also local authorities and road users.”
According to King’s College London, one area in Vauxhall, London had already exceeded yearly limits set by the EU for PM10 (particulate matter) by the end of February 2020. In such locations, any additional pollution from roadworks increases the risk to public health.
In a bid to reduce air pollution, London imposed an ultra-low emission zone (ULEZ) – where drivers of all but the cleanest vehicles must pay a daily charge – in April 2019. It may extend the zone to Greater London by 2021, with Birmingham and Leeds planning to introduce similar zones this summer, and Greater Manchester looking to phase in a similar approach from 2021.
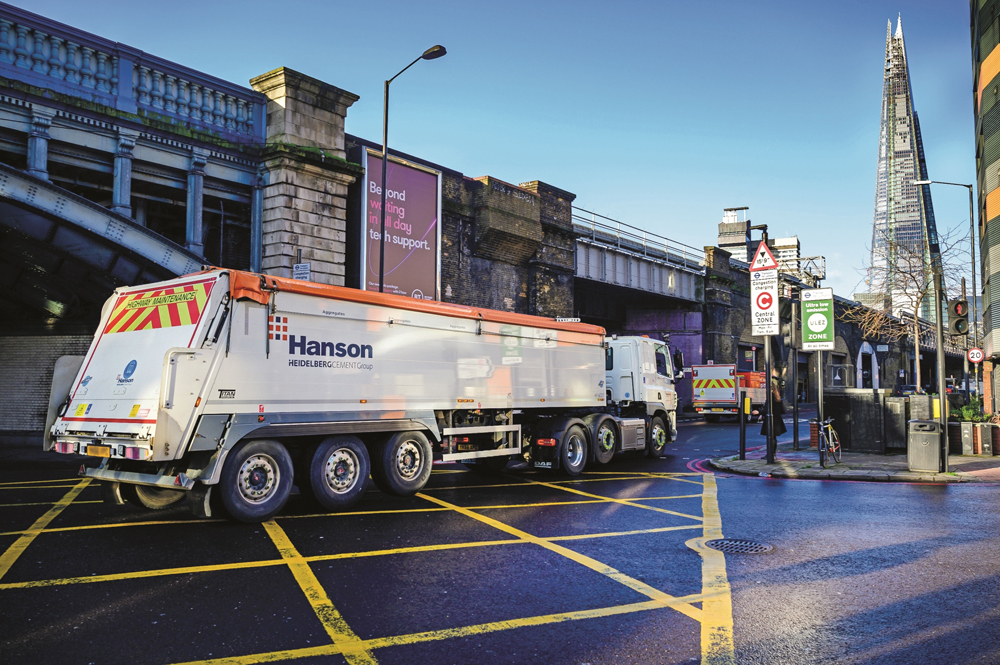
Working with Shell Bitumen, which developed the FreshAir additive which goes into REA, Hanson carried out two trials in London in Summer 2018, one on a road close to a primary school, the other adjacent to a wetlands park and playing field.
“We now have other sites that we are about to supply to,” said Hadley. “We are working with some key contractors in London and two or three London boroughs who are interested in using REA.”
Shell launched its FreshAir additive, which it supplies to Hanson already mixed into the bitumen, last year following trials in the UK, the Netherlands, France, Thailand and Hong Kong. Hanson’s project formed part of the trial process. The trials demonstrated that FreshAir reduces emissions of nitrogen oxides, sulphur dioxide, volatile organic compounds (VOCs), particulate matters at 2.5 and 10 microns and carbon monoxide by up to 40% compared to conventional asphalt.
REA can be used in conjunction with other bitumen technologies, such as polymer modification or other additives. “There are no restrictions and it can be combined with the entire product range that we supply,” said Hadley.
The combination of REA and Hanson’s warm mix technology ERA (energy reducing asphalt) is likely to be an attractive proposition, said Hadley. “If we combine the low-carbon effect of our energy reducing asphalt with the reduced emissions from REA, that really is a win-win,” he said. Using warm mix reduces some fumes and odours, but it does not cut specific gases and particulates or minimise their release into the air during production and paving. Hanson could supply REA from any one of its 36 UK plants. The UK team is also talking to colleagues in North America, Australia, Israel and Malaysia about the new technology.
Strong performance for Cargill’s bio-based rejuvenator
A parallel testing programme, with pavements in the North and South of the US, aims to encourage more widespread use of RAP. Cargill, which produces bio-based rejuvenator Anova, wants to provide DOTs countrywide with the data and confidence they need to increase recycled content in their pavements.
Two sections of test pavement containing 45% RAP and the Anova rejuvenator were laid in 2018, one on the test track at NCAT, the National Centre for Asphalt Technology at Auburn University for Virginia DOT, the other on the Minnesota Department of Transportation test track (MnRoad) for Minnesota DOT.
“It has become apparent that the agencies need some infrastructure to allow them to depart from their recipe-based specifications,” said Hassan Tabatabaee, global technical manager for asphalt at Cargill. “We looked around the county and saw that different agencies in different regions are trying in local pockets to work some of this out. We found there was certainly a need to provide unified, credible information that can tie this stuff together for those agencies to be able to support their work.”
Initial results from NCAT after around 18 months and 5.5 million equivalent single axle loads (ESALS) show that the section surfaced with asphalt containing Anova and 45% RAP have shown 0percent cracking, lower loss of roughness compared to the control section and the same level of rutting as the control section.
Anova is based on chemically modified vegetable oil. Cargill developed it around five years ago and has brought it to the market in North America, Europe, and South America. According to Tabatabaee, the rejuvenator has been used in millions of tonnes of hot mix asphalt. However, in the US, its use has been limited to smaller roads, private roads and parking lots where specifications are more flexible.
“There is a big distinction between what is being used in the private market and what is allowed and used by agencies and public roads,” said Tabatabaee. “The volumes have really come about from being able to provide technology and reliability and savings to contractors, but when it comes to the public sector, the process for change is a lot slower, and the requirements are quite different.”
Cargill estimates that the savings from being able to use 45% RAP equate to between 50 Cents and $1.50/ton, which amounts to $750,000/year for a medium-sized contractor. Lower capital cost attractive is an important part of the sustainability jigsaw, said Tabatabaee:
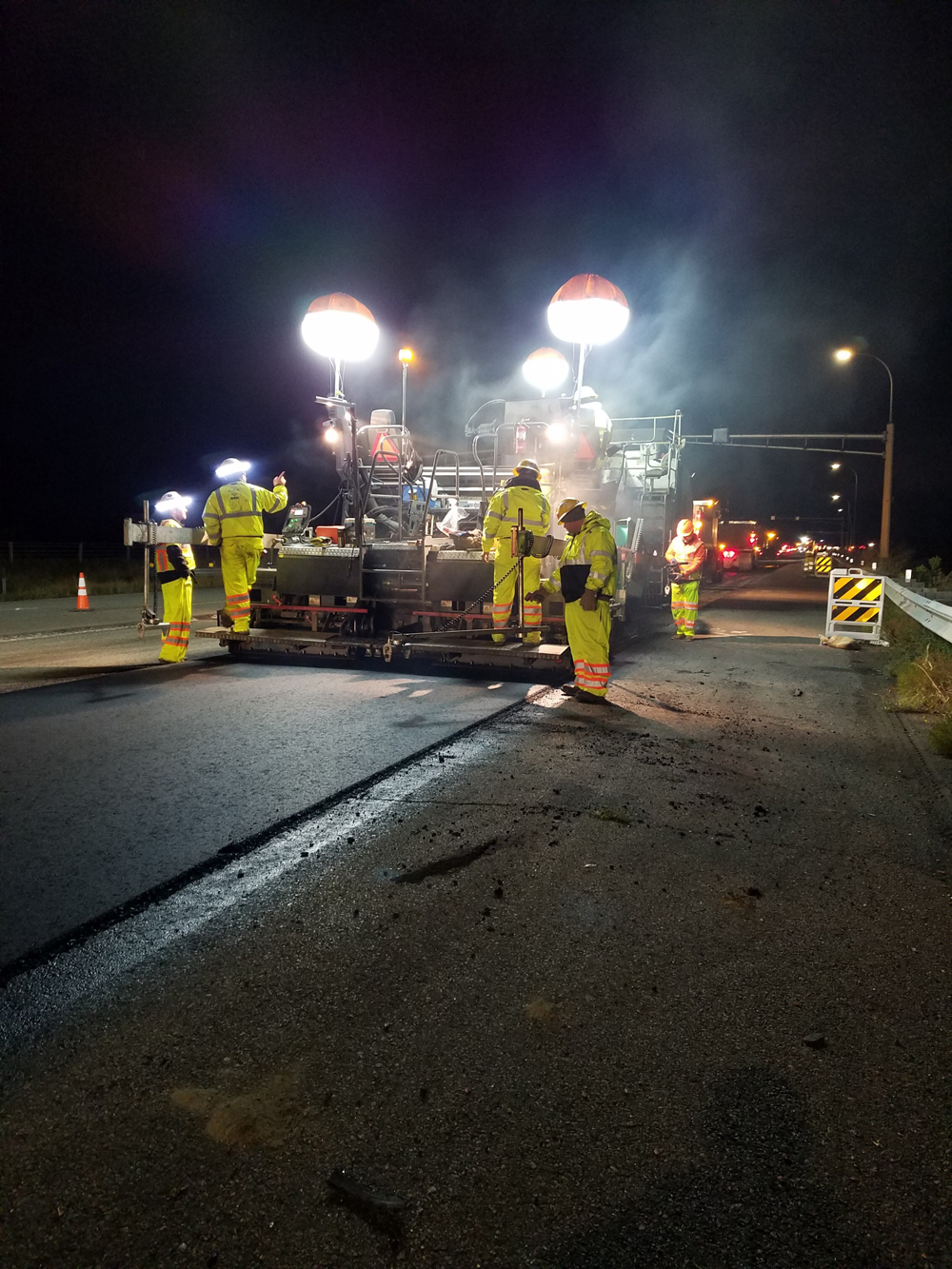
“Beyond the fact that we are recycling, we are enabling that recycling with an additive that comes from a renewable agricultural source, we are enhancing performance and we are saving cost. It’s one of those rare instances where there’s not a lot of compromise.”
The use of the rejuvenator also improves workability and compactability. “Our contractor on the MnRoad project, even with a 45-minute haul at zero degrees, managed to get his density bonus,” says Tabatabaee.
In Minnesota, the test section includes the 45% RAP and the Anova rejuvenator in both the base course and the wearing course. Laid in 2018, the section will be monitored for three years. “After the monitoring period, the pavement will stay in place as long as it is performing,” said Susan Listberger, global product manager for asphalt at Cargill.
At the NCAT track, only the wearing course is under test. This also contains 45% RAP, with the section to be tested for three years, in line with NCAT’s testing cycles.
A huge array of tests will be carried out on the mixes used on both test facilities. “NCAT is running a full battery of tests, all the specification tests we know of,” said Tabatabaee. “It’s going to give a unique set of data which will tie different regional specifications together.”
Cargill chose to work with 45% RAP because this is the maximum proportion that can be used with a conventional continuous batching plant without making modifications. At this level, the RAP can be added cold with the virgin aggregate superheated.
At a continuous plant – the type most commonly used in the US – the Anova rejuvenator would be injected into the bitumen at the plant. For batch plants, which are more widely used in Europe, it can be added to the RAP on the belts, added to the virgin bitumen or injected into the mill itself.
Cargill works with the contractor and asphalt supplier to getting the dosing of the Anova right, taking samples of the RAP that will be used and conducting tests in its laboratory. Because RAP is, by its nature, variable, it is important to keep monitoring to ensure homogeneity of mixes, according to Tabatabaee:
“Contractors should not focus only on performance data and comparisons,” he said. “Performance is important, but you should not just be looking at buying the chemical, you should find a partner that can allow you to bring reliability to the system.”