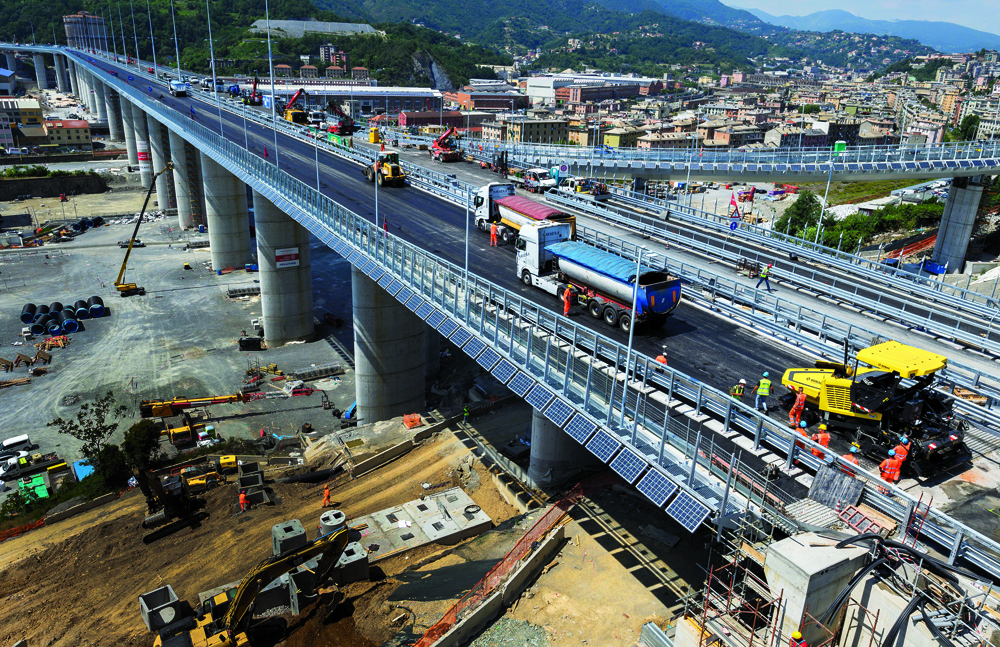
Among the papers at this year’s Eurasphalt & Eurobitume (E&E) Congress, held virtually from 15th – 17th June, is one from Italian road additive specialist Iterchimica. Its authors are Iterchimica technical director Loretta Venturini, scientific technical development expert Shahin Eskandarsefat and technical area manager Lorenzo Sangalli.
With two patents in its hand for its new GiPave technology, which combines recycled plastics and nanotechnology in the form of Graphene, Iterchimica presented information about how GiPave-enhanced asphalt performs compared to other modified mixes. The paper details the results of a three-year in-field and laboratory testing programme on the first trial section of GiPave laid on the Via Adreatina in Rome and demonstrates that GiPave’s green material credentials are complemented by its ability to extend pavement life.
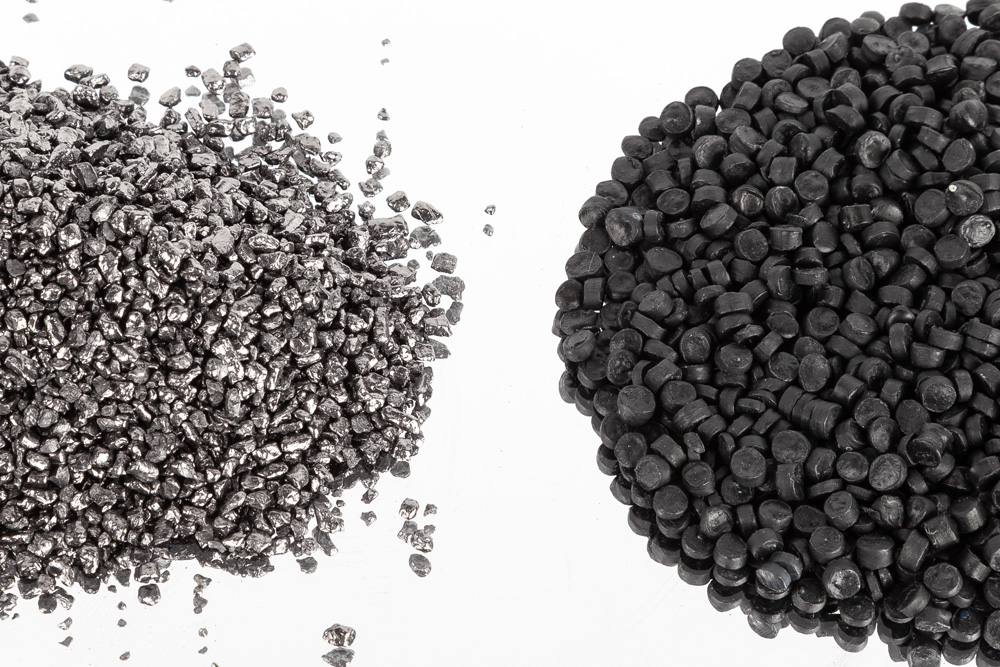
GiPave is the result of a six-year R&D programme by Iterchimica, conducted in collaboration with the University of Milan-Bicocca, graphene supplier Directa Plus and plastics recycling specialist G.Eco, part of the A2A Group. It is a graphene-enhanced polymeric supermodifier for asphalt combining specially selected waste plastics, GraphenePlus nanoplatelets and a functional base created by Iterchimica.
Various forms of graphene, including Graphite Nano Platelets (GNP) and Carbon Nanotubes (CN), have been shown to increase resistance to low-temperature cracking as well as high-temperature permanent deformation when added to asphalt mixes. GNP, in which layers of graphene are stacked on top of each other, is significantly more cost-effective than other forms of graphene, says Iterchimica, which makes it ideal for this application.
Iterchimica is keen to underline the fact that GiPave uses plastics that are not normally recycled; they would usually end up in a waste-to-energy plant. A 1km, 15m-wide road, 250mm thick, would use around 18tonnes of specially selected hard waste plastic.
GiPave’s carbon footprint is impressive too. Compared to SBS polymer modifier, GiPave’s carbon footprint is 92% lower, according to calculations by the University of Milan-Biocca. When considering its impact on a road in service (with the same parameters as mentioned above), the University calculated that GiPave’s carbon-equivalent emissions are 70% less than for conventional asphalt, whereas SBS-modified asphalt produces 30% lower emissions.
GiPave is added through a dry process at the asphalt plant, rather than being added to bitumen as is the case for Polymer Modified Bitumen (PMB). As well as contributing to the lower carbon footprint, this removes the storage and logistics demands required for PMB, namely elevated temperatures and agitation to keep the modified bitumen in a homogenous form. From a practical perspective, a dry process is easier to use, says Iterchimica, which in turn should encourage wider use.
Testing regime
Four different types of asphalt mix were compared in both the base and wearing courses on the test section of the Via Adreatina: one with no modification; one with a polymeric compound modifier; one modified with SBS PMB; and the GiPave-modified section. Like GiPave, the polymeric compound was added using the dry method. All mixes used a 70/100 bitumen binder, the base courses contained 40% RAP, the wearing courses 30% RAP and all had a vegetable-based rejuvenator added. The results presented in the paper refer to the wearing course test results only.
The following tests were carried out to characterise the performance of the different types of mix:
Falling weight deflectometer (Figure 1) tests carried out in-situ on the road. Data from these tests is used to calculate stiffness-related parameters. The results showed that the average estimated Modulus of Elasticity for asphalt made with the graphene-based modifier at 20˚C was 6424 MPa, almost double that for neat bitumen which is 3855 MPa. This is also 20% higher than the modulus for the SBS modified mixture (5435 MPa) and 40% higher than the mixture containing the polymeric compound.
Indirect tensile strength (Figure 2) carried out on specimens in the laboratory. These characterise resistance to fatigue and permanent deformation. Iterchimica only presents results from the non-modified asphalt and the graphene-modified asphalt as it says that for the other two samples “the results are not applicable”.
Indirect tensile stiffness modulus (Figure 3) tests were also carried out on specimens. Results demonstrate the load distribution capability and, since they are conducted at various temperatures (in this case 5, 20 and 40°C), the thermal sensitivity of asphalt mixes. The results showed that the graphene-based super modifier showed the highest values of ITSM at all three temperatures. The modulus of the mixture containing graphene-based modifier at 40˚C was 72% higher than the neat bitumen mixture and the polymeric compound modified mixture, and 30% higher than the SBS modified mixture. This shows that the mix modified with graphene will have a higher resistance to permanent deformation, says Iterchimica.
Wheel tracking device (Figure 4) testing was also used to assess resistance to permanent deformation. The graph shows the permanent deformation depth versus the number of wheel passes and demonstrates that the graphene-modified mix performs better than the other mixes.
Indirect tensile fatigue test, a repeated load indirect test, was used to assess the fatigue characteristics of the asphalt mixtures.Iterchimica also notes that the number of cycles to failure was 410,080 for the graphene-modified mix, 255,847 for polymeric compound, 135,122 for SBS and 52,312 for neat bitumen.
The Via Ardeatina was the first-ever trial section of GiPave to be laid. Since then, GiPave has been laid on ten more sections, seven in Italy and three in the UK. One of the most recent applications was on the new Ponte San Giorgio bridge in Genoa, where GiPave was used in the SMA wearing course and the binder layer. The prediction is that the service life of the road surface on the bridge will increase by 250%, thanks to the application of the GiPave technology.