An urgent need to improve and extend its road network means that Brazil is open to innovation and new ideas - the timing looks good for Kraton and its highly modified asphalt. Kristina Smith reports On 15th August Brazilian president Dilma Rousseff announced a US$66 billion (BRL 133 billion) investment package for the country’s road and rail networks. Of that, $21 billion (BRL 42 billion) is earmarked for the upgrade or construction of 7,500km of highways through a series of concessions. “We’re starting an
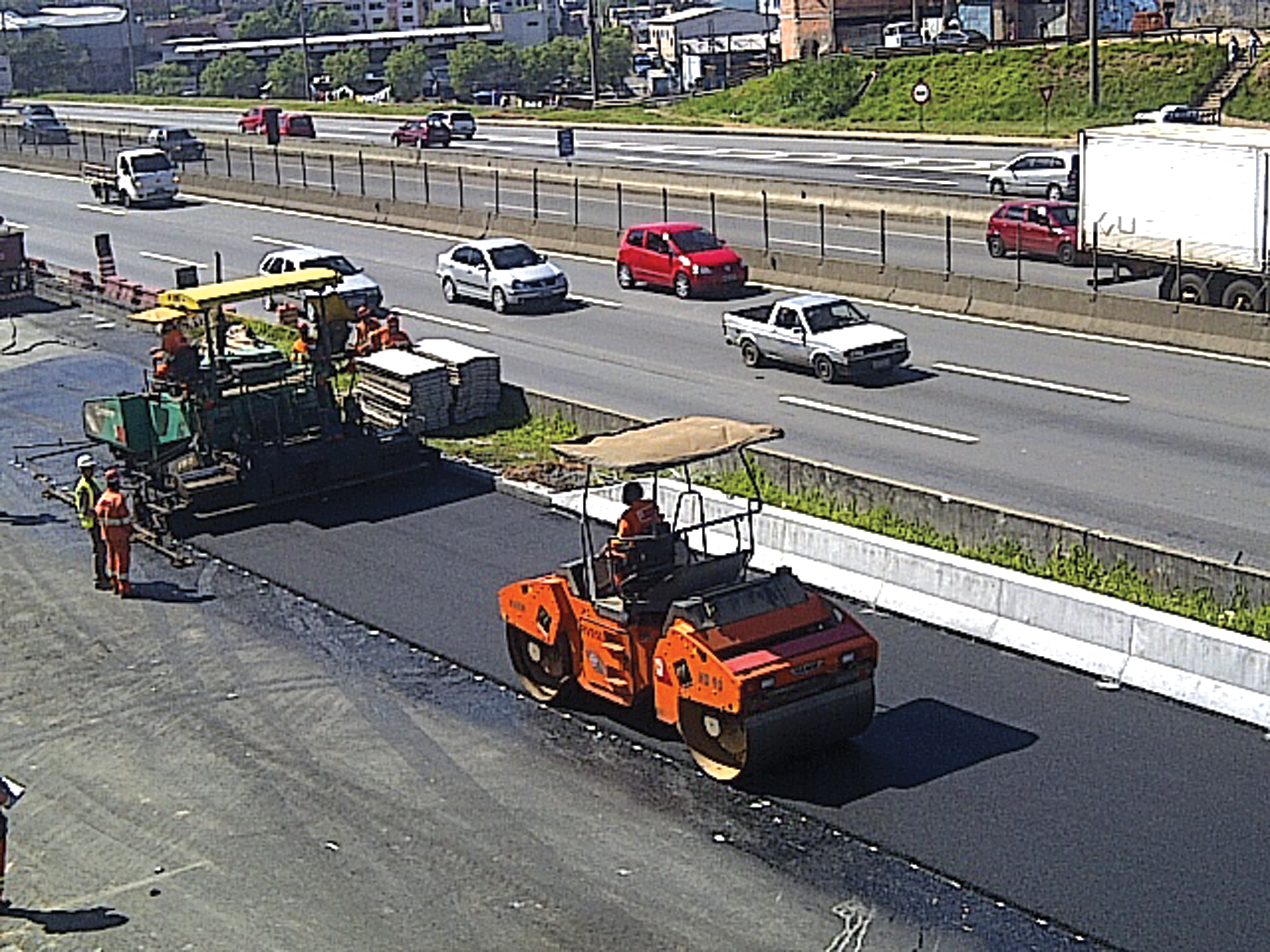
Nova Dutra in Sao Paulo City, where CCR Group is constructing three additional lanes
An urgent need to improve and extend its road network means that Brazil is open to innovation and new ideas - the timing looks good for Kraton and its highly modified asphalt. Kristina Smith reports
On 15th August Brazilian president Dilma Rousseff announced a US$66 billion (BRL 133 billion) investment package for the country’s road and rail networks. Of that, $21 billion (BRL 42 billion) is earmarked for the upgrade or construction of 7,500km of highways through a series of concessions.“We’re starting an initial stage from which Brazil will emerge richer and stronger,” Rousseff said as she made the announcement. “Brazil will have an infrastructure that’s compatible with its size.”
As Brazil looks forward to the 2014 World Cup and the Olympics in 2016, one of its most pressing tasks is to upgrade its infrastructure. Without improvements to its transport networks, economists warn that the country’s growth with be stifled. A burgeoning consumer society means more cars and more goods vehicles, in a country where 60% of transportation relies on roads and only 12% of roads are paved.
With the highways sector focussed on the nation’s need, there is a spirit of innovation in the air. “They are very collaborative, the people in Brazil, and willing to share information because they all know they need to speed infrastructure up,” said Michelle Mason, global industry manager for
The willingness to innovate is helped by the fact that an increasing proportion of Brazil’s roads are run by concessionaires. Introduced around 15 years ago as a way of increasing investment in roads, the concession system has gained momentum in the last five or six years. There are now 55 concessionaire road companies, running more than 15,000km or 7% of Brazil’s paved roads – much higher than the world average of 2%.
Concessionnaires are better placed to accept the potential risk attached to new technologies, said Kraton’s senior research scientist Dr Robert Kluttz. “With a build-only system, the only incentive is to meet the specification in the bid. There’s never the incentive to go out and make it better,” he said. “For that reason, agencies are very risk averse: they are very reluctant to go out and open bid new technology.
“But if the contract is to build and manage that road for 25 years, whoever gets that contract has to make that road perform in the most economic manner over a long period of time. They have the incentive to try new things.”
With successful projects for HiMA and full scale test results under its belt in the US, Kraton hopes that the trials it is conducting now in Brazil will give it a foothold in the country. Success here could also speed up acceptance in other parts of South America; potential projects in Peru, Bolivia and Argentina could all get a boost.
One of the reasons why HiMA may be an attractive proposition for Brazil is that it can offer the best of both worlds, says Kraton: less cost up front and a longer life. This contrasts with traditional wisdom which says: pay more now to have a longer lasting road.
HiMA contains 7-8% SBS polymer, compared to 2-4% for a standard polymer modified bitumen (PMB) giving it properties more akin to rubber than bitumen. And while most PMBs would become unworkable with this amount of polymer, Kraton’s D0243 SBS polymer means that HiMA doesn’t. The result is a binder which feels like a standard PMB to work with but which tests have shown can give improved performance for rutting resistance and fatigue at reduced thicknesses.
Kraton’s usual modus operandi when introducing new technology to a country would be to improve on traditional ways of working, changing the pavement design so that direct comparisons can be made with existing materials. However Hernando Faria, Kraton’s market development manager in South America, believes that there could be scope to go further in Brazil; people may be willing to reconsider the whole structure of the pavement.
“We need a new kind of structure here which will provide better performance compatible with the high traffic on our highways,” said Faria. “The traditional way is to use a base course made from aggregate and cement, it is a cultural thing. But when you use a cement base course, this base will crack very soon and the crack reflects into the asphalt layer.”
The very first trial of HiMA in Brazil, a small test section on highway PR-092 in the state of Paraná, aims to demonstrate how a total rethink could benefit the country’s roads. Contractor Compasa, which supplied the PMB, mixed and laid the road, had a contract with the Paraná Department of Transport to rebuild around 60km of the 383km highway connecting the port of Paranaguá in Paraná State to Sao Paulo State.
“We were looking for alternatives which would allow us to do the work in less time and to reduce the cost,” said Compasa’s technical director Rafael Reis.
HiMA promises improvements in performance, initial cost and time. New roads in Brazil with heavy traffic volumes like BR-101 and 116 last less than two years without a strong maintenance regime said Reis.
In startling contrast, the HiMA solution, with its vastly improved fatigue and deformation resistance is predicted to last for 20 years.
The standard solution proposed by DOT of Paraná State for Compasa’s rebuild of PR-092, after planing off around 15cm of the old asphalt wearing course, is a 20cm base course of RAP with cement; a 2.5cm SAMI (stress absorption layer intermediate) to block cracks from the base layer; a 4cm binder course; and a 4cm PMB wearing course. Total thickness is 30.5cm.
The trial alternative is simply a 16.5cm dense grade HiMA. Compasa found that this could be laid in two layers, offering huge time savings compared to the standard solution.
Laid in November 2011, CT Vias, a private road technology company, is now monitoring the road’s performance for Compasa. “I believe that in one year’s time, we will have positive feedback about it,” said Reis.
Success here would be significant. PR-092 is one of Brazil’s busiest and one of the most important roads in Paraná State, carrying 6,000 vehicles/day, 70% of which are heavy agricultural trucks.
Reis said, “If this trial goes well, there will be more projects coming, both in Parana and in other parts of Brazil.”
The fact that HiMA can be used in a wide range of applications is reflected in the variety of trial projects on the go in Brazil. These include work on a section of the 402km Via Dutra which runs between Sao Paulo and Rio de Janeiro.
Here CCR Group, a concessionaire which runs 15% by mileage of Brazil’s concession highways, is constructing three additional lanes as the highway reaches Sao Paulo. A HiMA wearing course will be compared to a standard modified asphalt one, with CCR due to evaluate the relative performance in a year’s time.
Another of the trials takes place on a section of Rio de Janeiro’s new Bus Rapid Transit (BRT) system which will see the construction and adaptation of roads to take bus lanes. On a section of the Transoeste BST, where the existing road is being overlaid with a binder course and wearing course, HiMA will be put through its paces. With 700km of roads around Rio requiring this type of overlaying operation, HiMA’s successful performance on the BRT trial section could open many more doors.
Despite Brazil’s relative willingness to try new technology, convincing all the stakeholders to take the plunge remains a challenge. “We have got to influence many different people,” said Faria. “The government agency, the concessionaire, the constructor, the designer. I have to work to connect their different views and influence all of them. This is a big challenge.”
For Reis, it is the technical people within the federal and state road departments – DNIT and DERs - who must be convinced in order for new technologies such as HiMA to take off. However, the road agencies and public administrators do realise that drastic solutions are required, he says.
An emerging model, said Reis, is for the government to work in partnership with the private sector on less busy roads which would not be attractive as concessions. The government would provide funding for a proportion of the maintenance, with private companies having the option to increase the number of lanes.
Partnerships are more conducive to innovation and HiMA could benefit from this type of arrangement, said Reis. “It not only offers better durability, the maintenance can be carried out so much more quickly,” he said.
Kraton believes that its five trials in Brazil – and their successful performance – will push HiMA up to the next stage. “We are at the inflection point,” said Mason. “We hope to have a full-scale commercial trial awarded to us before the end of the year.”
Compasa definitely has plans to use
HiMA again. In fact it is already proposing it on other stretches of road. “I don’t think it will take too long for HiMA to be accepted,” said Reis, “because of the great demand for new roads and the need to maintain and fix the old ones.”