Russia needs polymer-modified bitumen; the UK is embracing US-style pavement preservation technology and gearing up to import more bitumen; and Italy prepares to export innovative modifying technology; plus a look at the market in Asia Pacific and the Middle East – Kristina Smith reports. The Total Group has announced two recent deals which underline the changing bitumen market around the world. In Moscow, it is constructing a new type of polymer-modified bitumen (PMB) plant in joint venture with Gazprom Ne
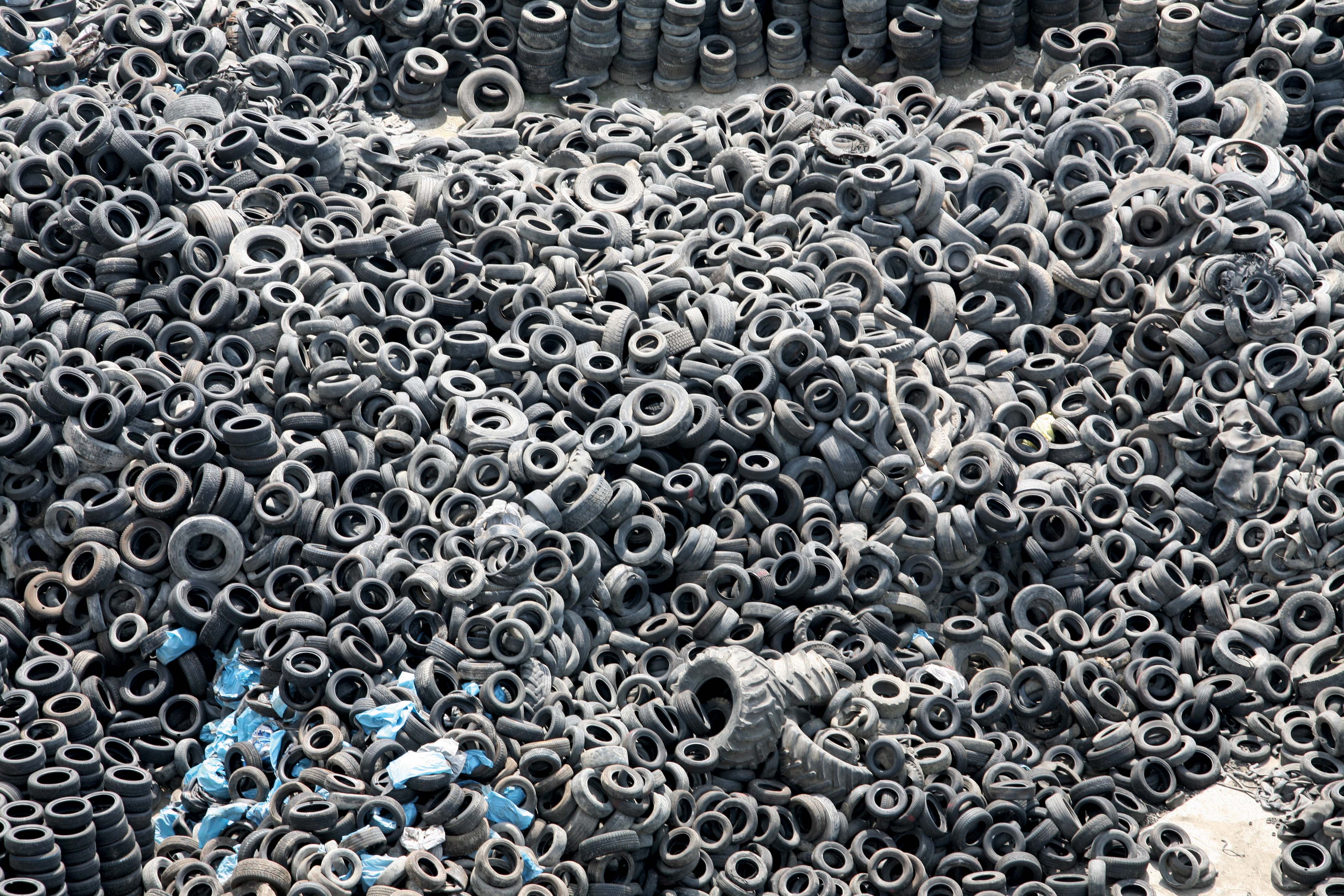
Scrap tyres from Liberty Tire Recycling provide a useful material source for Lehigh Technologies
Russia needs polymer-modified bitumen; the UK is embracing US-style pavement preservation technology and gearing up to import more bitumen; and Italy prepares to export innovative modifying technology; plus a look at the market in Asia Pacific and the Middle East – Kristina Smith reports
The344 Total Group has announced two recent deals which underline the changing bitumen market around the world. In Moscow, it is constructing a new type of polymer-modified bitumen (PMB) plant in joint venture with 1270 Gazprom Neft, while in the UK it has signed a deal to construct a new bitumen terminal near London.
In September last year pilot production of a new type of PMB, branded G-Way Styrelf, began at the Gazprom Neft Moscow Refinery. Total’s Styrelf technology is being used to produce the polymer, the first of this type to be made in Russia.
Gazprom Neft is preparing for an expected growth in demand for PMB over the next decade. The chairman of Gazprom Neft’s management board Alexander Dyukov said, “Experts expect the use of PMBs in road construction in Russia to increase three-fold by 2025. Gazprom Neft is implementing the most cutting-edge technology to allow not just the construction of world-class roads, but also a significant reduction in the costs associated with maintaining them.”
The Styrelf process adds a special binding agent (PAXL) which increases bonding at a molecular level. The aim is to make road surfaces more resistant to cracking and fracturing, even in challenging climatic conditions, such as those experienced in Russia.
The PMB facility has the capacity to produce 60,000tonnes of PMBs and 7,000tonnes of emulsified bitumen/year. Raw materials for G-Way Styrelf PMBs will come from the Gazprom Neft Moscow refinery, which was fully reconstructed in 2012, to increase production and decrease its environmental impact.
November 2014 saw Total’s UK business sign a deal with Royal Vopak, which specialises in storage and handling of oil products, liquid chemicals and gases. Bitumen from the Total Group’s network of production facilities will arrive by sea at Vopak Terminal, London’s oil products terminal in Grays on the Thames where it already has land and jetties.
The move was prompted by the UK’s infrastructure plans, said Richard Laden, Total UK’s managing director. “The decision to develop a new supply point comes at an important time when the UK government has announced plans for the biggest investment in road infrastructure since the 1970s,” he said. “The market is already becoming reliant on imports due to the closure of several bitumen facilities over the last five years so this agreement demonstrates Total’s commitment to supply chain security and the consolidation of a sustainable business in the UK market.”
Total already supplies bitumen and bitumen products to the UK, including emulsion, clear binder and Total Styrelf PMB. Royal Vopak is the world’s largest independent tank storage company by capacity with 80 terminals in 28 countries. Vopak will build and operate the storage facility, which is due to be opened in the second quarter of 2016.
8021 Bituchem began producing FortSeal, a polymer-modified bitumen emulsion in 2012 and has seen its use rise dramatically since. It is currently the only manufacturer to offer this particular product type in the UK.
“We’ve seen a ten-fold increase over the last three years,” says contract manager Phillip Humphreys. “We are in our fourth season now, and have repeat customers all over the country. Some will be using it for the fourth year this time.”
With a little more money in the maintenance budgets, councils are able to take a longer-term, proactive approach rather than a reactive one as problems occur.
“Councils across the UK are having to find new and innovative ways of maintaining their highway network to achieve the same high standard of roads but with reduced resources,” said Andrew Whailing, senior technician at Leicestershire County Council which is trialling FortSeal on a country road in the village of Burton on the Wolds. “As such, the focus is on a proactive approach towards preservation of existing assets rather than reactive work such as resurfacing.”
The bitumen emulsion works to seal the surface to prevent the effects of oxidisation and ravelling which helps to stop or slow down further deterioration. As well as extending the life of the road, the emulsion, which is applied by sprayer, gives the roads a fresh, blackened appearance similar to a new road surface, creating a positive impression for road users.
It is important to apply FortSeal before roads start to deteriorate. “The intervention level is quite early,” explains Humphries. “If you’ve got a hot-rolled asphalt road and you’re losing chips heavily, you could argue it’s already gone too far.”
FortSeal has been used successfully on many SMA surfaces, which in the UK tend to fail after around five years if left to their own devices, says Humphries. Treating them with FortSeal at four years extends their life to eight years.
If the Leicestershire trial is successful, other roads in the county could receive the same treatment, said Whailing, “We are very pleased with the initial application of FortSeal and will now carefully monitor its performance. If the trial suggests that FortSeal provides a cost-effective means of extending the life of the surface, then we anticipate applying it to other roads in Leicestershire.”
252 Iterchimica is to launch an innovative new bitumen modifier range at the first ever Pavement Preservation & Recycling Summit (PPRS) to be held in Paris on 22nd-25th February. The new product line ITER PPS (Poly-functional Polymeric Systems) is a series of pellet types, containing both polymers and fibres.
The pellets are added directly into the pugmill of the asphalt plant using a calibrated dosage system, eliminating the cost and logistical challenges of manufacturing and storing polymer-modified bitumen (PMB). In remote locations or for smaller contractors, or smaller jobs, ITER PPS could make the use of modified bitumen a much more cost-effective and viable solution.
“This technology represents a real step forward,” said Iterchimica’s laboratory manager Loretta Venturini. “The combination of polymer and fibre means that ITER PPS can act simultaneously to improve several properties at the same time.”
In its research laboratories, Iterchimica has developed four lines of pellets. The ITER PPS 1000 series contains plastomers and either natural cellulose or synthetic microfibers. ITER PPS 1000 has been used on several roads in Italy for SMA (stone mastic asphalt) applications and is attracting interest from other countries.
The ITER PPS 2000 is based on elastomers with fibres and has been designed for environments where there is a large variation in temperatures. ITER PPS 3000 with paraffinic derivatives and elastomeric polymers has been designed for use in mixes with a large proportion of recycled asphalt. With the addition of a specific additive, it can also be used for warm mix asphalt.
ITER PPS 4000 comprises elastomers and natural bitumen from Selenizza. It has been designed on use for pavements requiring a high stiffness modulus.
The cylindrical fibres are around 10mm in diameter and are added in doses of between 0.2% and 0.6% before the bitumen goes in. The dosage depends on the aggregate, bitumen and required performance of the mix. Iterchimica can also custom-make pellets to meet the particular materials and specification of a contract.
“The pellets can be formulated according to project requirements to achieve the technical specifications,” said Venturini. “We can change the components, put in some additives and take out others, like a chef.”
Iterchimica has been trialling the ITER PPS pellets on projects and contracts in Italy for the last two years and is now ready to launch them worldwide. It has already been in conversation with highways authorities in several countries and is going through the process of accreditation in a number of them.
Lehigh’s Rheopave system combines ground tyre rubber and a special additive to produce RMA which can match the performance of asphalt modified with SBS polymer. The agreement with Liberty Tire Recycling will see Liberty, which recycles 140 million tyres/year, selling the Rheopave RMA systems alongside its ground tyre rubber.
By spreading technology which provides higher-performing RMA highways, Lehigh believes it can also increase the volume of RMA used around the US.
“The hope is that it will increase the confidence that state agencies have in RMA’s performance,” says Tom Rosenmayer,7875 Lehigh Technologies VP of technology. “We now have an RMA system which can meet the most demanding specifications. That’s never happened before. In the long term, we hope it can grow the market for RMA.”
Until now, RMA has had difficulty in meeting all parts of the US’ PG (Performance Graded) and MSCR (Multiple Stress Creep Recovery) testing requirements, says Rosenmayer. “This system was formulated to help the stability and address other areas where ground tyre rubber does not hit all the specifications.”
Lehigh launched the Rheopave system last year. Specialist firm Rheopave developed the additive, called Rheopave XP10, with Lehigh which now manufactures it under licence.
Performance benefits from using Rheopave RMA are longer fatigue cracking life and also enhanced elastomeric properties allowing the pavement to combat cold cracking, according to Lehigh. It is also easier to handle as the mix is less tacky than one made with ground tyre rubber alone.
For US states that require that a certain proportion of road to include recycled rubber, Rheopave offers the opportunity to meet environmental targets while increasing the life of a road. The product also provides an alternative to SBS polymers which, though low in price at the moment, have historically suffered from quite dramatic price fluctuations.
Rosenmayer says that sales during the product’s first commercial year have been encouraging. Lehigh has also spoken to interested parties in Europe, Asia and South America. “There’s a lot of interest in the way the product performs,” says Rosenmayer.
The
In September last year pilot production of a new type of PMB, branded G-Way Styrelf, began at the Gazprom Neft Moscow Refinery. Total’s Styrelf technology is being used to produce the polymer, the first of this type to be made in Russia.
Gazprom Neft is preparing for an expected growth in demand for PMB over the next decade. The chairman of Gazprom Neft’s management board Alexander Dyukov said, “Experts expect the use of PMBs in road construction in Russia to increase three-fold by 2025. Gazprom Neft is implementing the most cutting-edge technology to allow not just the construction of world-class roads, but also a significant reduction in the costs associated with maintaining them.”
The Styrelf process adds a special binding agent (PAXL) which increases bonding at a molecular level. The aim is to make road surfaces more resistant to cracking and fracturing, even in challenging climatic conditions, such as those experienced in Russia.
The PMB facility has the capacity to produce 60,000tonnes of PMBs and 7,000tonnes of emulsified bitumen/year. Raw materials for G-Way Styrelf PMBs will come from the Gazprom Neft Moscow refinery, which was fully reconstructed in 2012, to increase production and decrease its environmental impact.
November 2014 saw Total’s UK business sign a deal with Royal Vopak, which specialises in storage and handling of oil products, liquid chemicals and gases. Bitumen from the Total Group’s network of production facilities will arrive by sea at Vopak Terminal, London’s oil products terminal in Grays on the Thames where it already has land and jetties.
The move was prompted by the UK’s infrastructure plans, said Richard Laden, Total UK’s managing director. “The decision to develop a new supply point comes at an important time when the UK government has announced plans for the biggest investment in road infrastructure since the 1970s,” he said. “The market is already becoming reliant on imports due to the closure of several bitumen facilities over the last five years so this agreement demonstrates Total’s commitment to supply chain security and the consolidation of a sustainable business in the UK market.”
Total already supplies bitumen and bitumen products to the UK, including emulsion, clear binder and Total Styrelf PMB. Royal Vopak is the world’s largest independent tank storage company by capacity with 80 terminals in 28 countries. Vopak will build and operate the storage facility, which is due to be opened in the second quarter of 2016.
FortSeal
Local authorities in the UK are turning to fogseal-type applications, already popular in the US, to help extend the life of local roads. Bitumen product specialist“We’ve seen a ten-fold increase over the last three years,” says contract manager Phillip Humphreys. “We are in our fourth season now, and have repeat customers all over the country. Some will be using it for the fourth year this time.”
With a little more money in the maintenance budgets, councils are able to take a longer-term, proactive approach rather than a reactive one as problems occur.
“Councils across the UK are having to find new and innovative ways of maintaining their highway network to achieve the same high standard of roads but with reduced resources,” said Andrew Whailing, senior technician at Leicestershire County Council which is trialling FortSeal on a country road in the village of Burton on the Wolds. “As such, the focus is on a proactive approach towards preservation of existing assets rather than reactive work such as resurfacing.”
The bitumen emulsion works to seal the surface to prevent the effects of oxidisation and ravelling which helps to stop or slow down further deterioration. As well as extending the life of the road, the emulsion, which is applied by sprayer, gives the roads a fresh, blackened appearance similar to a new road surface, creating a positive impression for road users.
It is important to apply FortSeal before roads start to deteriorate. “The intervention level is quite early,” explains Humphries. “If you’ve got a hot-rolled asphalt road and you’re losing chips heavily, you could argue it’s already gone too far.”
FortSeal has been used successfully on many SMA surfaces, which in the UK tend to fail after around five years if left to their own devices, says Humphries. Treating them with FortSeal at four years extends their life to eight years.
If the Leicestershire trial is successful, other roads in the county could receive the same treatment, said Whailing, “We are very pleased with the initial application of FortSeal and will now carefully monitor its performance. If the trial suggests that FortSeal provides a cost-effective means of extending the life of the surface, then we anticipate applying it to other roads in Leicestershire.”
Iterchimica
Italian bitumen additive specialistThe pellets are added directly into the pugmill of the asphalt plant using a calibrated dosage system, eliminating the cost and logistical challenges of manufacturing and storing polymer-modified bitumen (PMB). In remote locations or for smaller contractors, or smaller jobs, ITER PPS could make the use of modified bitumen a much more cost-effective and viable solution.
“This technology represents a real step forward,” said Iterchimica’s laboratory manager Loretta Venturini. “The combination of polymer and fibre means that ITER PPS can act simultaneously to improve several properties at the same time.”
In its research laboratories, Iterchimica has developed four lines of pellets. The ITER PPS 1000 series contains plastomers and either natural cellulose or synthetic microfibers. ITER PPS 1000 has been used on several roads in Italy for SMA (stone mastic asphalt) applications and is attracting interest from other countries.
The ITER PPS 2000 is based on elastomers with fibres and has been designed for environments where there is a large variation in temperatures. ITER PPS 3000 with paraffinic derivatives and elastomeric polymers has been designed for use in mixes with a large proportion of recycled asphalt. With the addition of a specific additive, it can also be used for warm mix asphalt.
ITER PPS 4000 comprises elastomers and natural bitumen from Selenizza. It has been designed on use for pavements requiring a high stiffness modulus.
The cylindrical fibres are around 10mm in diameter and are added in doses of between 0.2% and 0.6% before the bitumen goes in. The dosage depends on the aggregate, bitumen and required performance of the mix. Iterchimica can also custom-make pellets to meet the particular materials and specification of a contract.
“The pellets can be formulated according to project requirements to achieve the technical specifications,” said Venturini. “We can change the components, put in some additives and take out others, like a chef.”
Iterchimica has been trialling the ITER PPS pellets on projects and contracts in Italy for the last two years and is now ready to launch them worldwide. It has already been in conversation with highways authorities in several countries and is going through the process of accreditation in a number of them.
Lehigh Technologies
Lehigh Technologies had joined forces with Liberty Tire Recycling in a bid to distribute its rubber modified asphalt (RMA) technology to more states in the US.Lehigh’s Rheopave system combines ground tyre rubber and a special additive to produce RMA which can match the performance of asphalt modified with SBS polymer. The agreement with Liberty Tire Recycling will see Liberty, which recycles 140 million tyres/year, selling the Rheopave RMA systems alongside its ground tyre rubber.
By spreading technology which provides higher-performing RMA highways, Lehigh believes it can also increase the volume of RMA used around the US.
“The hope is that it will increase the confidence that state agencies have in RMA’s performance,” says Tom Rosenmayer,
Until now, RMA has had difficulty in meeting all parts of the US’ PG (Performance Graded) and MSCR (Multiple Stress Creep Recovery) testing requirements, says Rosenmayer. “This system was formulated to help the stability and address other areas where ground tyre rubber does not hit all the specifications.”
Lehigh launched the Rheopave system last year. Specialist firm Rheopave developed the additive, called Rheopave XP10, with Lehigh which now manufactures it under licence.
Performance benefits from using Rheopave RMA are longer fatigue cracking life and also enhanced elastomeric properties allowing the pavement to combat cold cracking, according to Lehigh. It is also easier to handle as the mix is less tacky than one made with ground tyre rubber alone.
For US states that require that a certain proportion of road to include recycled rubber, Rheopave offers the opportunity to meet environmental targets while increasing the life of a road. The product also provides an alternative to SBS polymers which, though low in price at the moment, have historically suffered from quite dramatic price fluctuations.
Rosenmayer says that sales during the product’s first commercial year have been encouraging. Lehigh has also spoken to interested parties in Europe, Asia and South America. “There’s a lot of interest in the way the product performs,” says Rosenmayer.