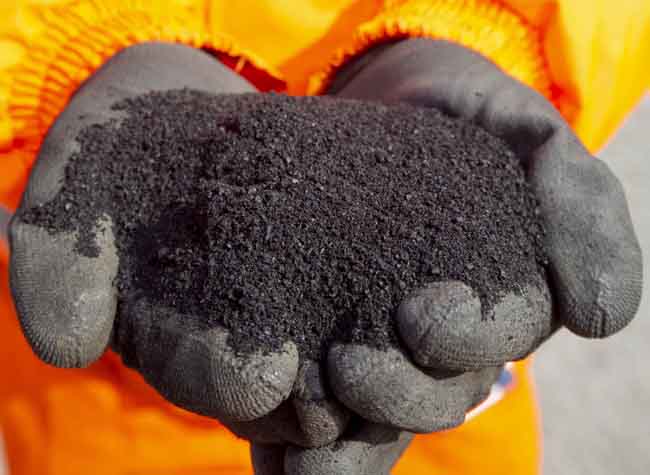
"Local authorities want to be green, sustainable and environmentally friendly,” said
Around 40 million tyres are worn out every year in the UK. Though some are burnt for fuel at cement kilns, others turned to crumb rubber and used for sports pitches and to create items like car mats, there is still a surplus of 120,000tonnes of rubber waste. Currently these are shipped abroad.
Tarmac has modified seven of its 72 asphalt plants so that 1% of crumb rubber by weight can be added to mixes. This is combined with a warm-mix additive, Evotherm, so that the harmful emissions are not produced during the manufacturing process. Tarmac reckons this equates to 750 waste tyres/km of road resurfaced.
The company started investigating the use of end-of-life tyres (ELT) in asphalt back in 2011. They chose a method has been used successfully in the US for over a decade, said Kent.
This process is somewhere between the wet and dry processes for adding rubber to asphalt mixes. The rubber become part of the asphalt matrix, melting at first and then resolidifying to act “like a glue”, said Kent.
The result is a mix that is better than one created with standard bitumen, but not as enhanced as one made with a polymer-modified bitumen. Kent did not provide any test results to demonstrate its performance, saying that there were no tests that adequately mimicked ageing.
“Talking to colleagues in America, they have come to the conclusion that because rubber is in the material, it is helping to delay crack propagation and that means the roads are lasting longer,” said Kent. He added that where rubber is used in SMA (stone mastic asphalt) mixes, the crumbs sit in some of the air voids, improving waterproofing and hence enhancing durability.
The first UK authority to trial the mix was Coventry, with national authority Highways England also carrying out a trial on the M1 motorway near the East Midlands Airport. Authorities in London, Nottingham and Leicester are also planning trials with several others expressing interest.
Modifications to the asphalt plants involve adding an automated system to the plant which includes a silo, a screw to mix and making modifications to the software. The cost for modifications varies, depending on the plant but costs tens of thousands of pounds. Other plants will be upgraded, depending on market demand, says Kent.