Benninghoven’s Ralf Port talks about the German firm’s development with partner BAM of its counter flow parallel drum system for RAP material The asphalt industry constantly searches for new solutions in order to optimise processes within the asphalt plant. A major subject is the increase of RAP content in all recipes. Recycling Parallel Drum Systems work in various sizes and at various power levels. This technique has been established by different producers over the decades. However, all kinds of concepts
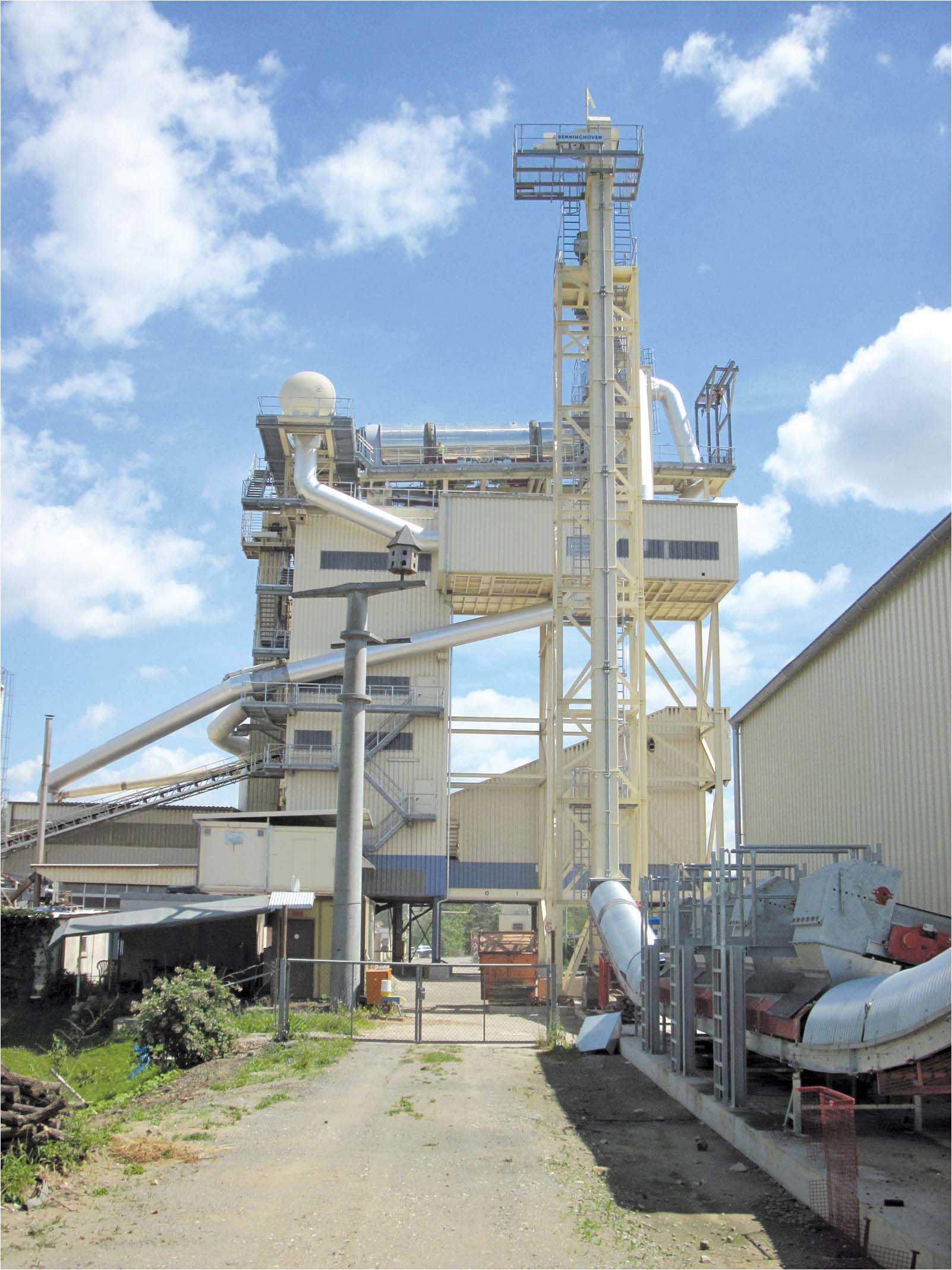
Asphalt mixing plant with the new RAP Drum systems
Benninghoven’s Ralf Port talks about the German firm’s development with partner BAM of its counter flow parallel drum system for RAP material
The asphalt industry constantly searches for new solutions in order to optimise processes within the asphalt plant. A major subject is the increase of RAP content in all recipes.
Recycling Parallel Drum Systems work in various sizes and at various power levels. This technique has been established by different producers over the decades. However, all kinds of concepts for heating up RAP material in the parallel flow system have their limits.
The physical properties of the parallel flow drum system came with some less positive characteristics, such as high exhaust gas temperatures to reach the RAP material product temperature and higher emission levels; this led us into a new development with our long term partner BAM (Bavarian Asphalt Plant Works) to find a different way forward for this technology.
In the mid-1980s, the technique of indirectly heating the RAP utilising a hot gas generator was introduced but not perfected, unlike the new system. For167 Benninghoven’s Development Technical Team, the biggest challenge was to configure the fan arrangements for recirculation and exhaust conditions based on theoretical values.
Out of this the following values were estimated:
Utilising the hot gas generator system a constant capacity of 11.800kW has to be generated.
By adjusting the burner configuration (ype “EVO-JET 3-2 Coal/Diesel Inverter”) the applicable Air- and Fuel streams have been set. At a flame temperature of 1.200°C with applicable air over ratio result in 89.700 m³ hot gas/h.
The density of the hot gas at 1.200°C is 0.24 kg/dm³. Hot air entering the RAP drum is restricted to a maximum temperature of 450°C.
The calculation was based on the following formula: mUL=mHG*(cpHG*THG-cpGes*TGes)/(cpGes*TGes-cpUl*TUl)
Hot Gas amount: 21.500 kg/h
Total Amount: 76.500 kg/h result in 650 °C:154.000 Bm³/h
Exhaust Gas value:result in 110 °C:54.000 Bm³/h
Fan Rating Circulation: 70.000 Bm³/h (110 °C)
Fan Rating Exhaust: 70.000 Bm³/h (110 °C)
Based on these calculated theoretical values, the system was technically configured. Some specific specialties were also taken into consideration.
A real challenge for the Development Team was how to handle the fine particles in the exhaust gas.
A simple and ingenious solution was found. The dirt gases first reach a generously sized expansion chamber where the air speed is reduced.
The particles then fall into a collection hopper and they are transferred by a screw conveyor into the hot recycling buffer silo.
In late spring time 2013, the plant began its trial operation.
The development teams from BAM and Benninghoven were astonished that the estimated values were exceeded.
During the testing phase the system was closely monitored, emission tests were taken, samples were analysed, with recipes created modified accordingly, and processes were optimised with the result that the plant performed to 100% of the specification.
Looking at the computer monitor screen, it shows a filter exhaust gas temperature of 90°C and a cycling product temperature of 172°C.
The C Total value had been constantly recorded to be below 50mg, therefore these values are well below the applicable norm of Germany’s TA-Air.
After one season of successful operation, small modifications were made to further optimise the system.
Our partner BAM is fully satisfied with this new technology, and we are happy that we were selected for this project.
We are certain that the counter flow parallel drum system will fully change the market outlook.
The asphalt industry constantly searches for new solutions in order to optimise processes within the asphalt plant. A major subject is the increase of RAP content in all recipes.
Recycling Parallel Drum Systems work in various sizes and at various power levels. This technique has been established by different producers over the decades. However, all kinds of concepts for heating up RAP material in the parallel flow system have their limits.
The physical properties of the parallel flow drum system came with some less positive characteristics, such as high exhaust gas temperatures to reach the RAP material product temperature and higher emission levels; this led us into a new development with our long term partner BAM (Bavarian Asphalt Plant Works) to find a different way forward for this technology.
In the mid-1980s, the technique of indirectly heating the RAP utilising a hot gas generator was introduced but not perfected, unlike the new system. For
Out of this the following values were estimated:
1. Heat Demand
Based on a configuration of 180 t/h capacity of3 % moisture, a temperature increase by 150K, on exhaust gas temperature of 110°C the heat demand is:11.800 kW (inclusive loss)2. Exhaust gas volume:
At 110°C the volume for the drying-heating process results in 54.000 Bm³/hUtilising the hot gas generator system a constant capacity of 11.800kW has to be generated.
By adjusting the burner configuration (ype “EVO-JET 3-2 Coal/Diesel Inverter”) the applicable Air- and Fuel streams have been set. At a flame temperature of 1.200°C with applicable air over ratio result in 89.700 m³ hot gas/h.
The density of the hot gas at 1.200°C is 0.24 kg/dm³. Hot air entering the RAP drum is restricted to a maximum temperature of 450°C.
The calculation was based on the following formula: mUL=mHG*(cpHG*THG-cpGes*TGes)/(cpGes*TGes-cpUl*TUl)
Parameters:
Recirculation Air: 55.000 kg/h result in 110 °C:64.000 Bm³/hHot Gas amount: 21.500 kg/h
Total Amount: 76.500 kg/h result in 650 °C:154.000 Bm³/h
Exhaust Gas value:result in 110 °C:54.000 Bm³/h
Fan Rating Circulation: 70.000 Bm³/h (110 °C)
Fan Rating Exhaust: 70.000 Bm³/h (110 °C)
Based on these calculated theoretical values, the system was technically configured. Some specific specialties were also taken into consideration.
A real challenge for the Development Team was how to handle the fine particles in the exhaust gas.
A simple and ingenious solution was found. The dirt gases first reach a generously sized expansion chamber where the air speed is reduced.
The particles then fall into a collection hopper and they are transferred by a screw conveyor into the hot recycling buffer silo.
In late spring time 2013, the plant began its trial operation.
The development teams from BAM and Benninghoven were astonished that the estimated values were exceeded.
During the testing phase the system was closely monitored, emission tests were taken, samples were analysed, with recipes created modified accordingly, and processes were optimised with the result that the plant performed to 100% of the specification.
Looking at the computer monitor screen, it shows a filter exhaust gas temperature of 90°C and a cycling product temperature of 172°C.
The C Total value had been constantly recorded to be below 50mg, therefore these values are well below the applicable norm of Germany’s TA-Air.
After one season of successful operation, small modifications were made to further optimise the system.
Our partner BAM is fully satisfied with this new technology, and we are happy that we were selected for this project.
We are certain that the counter flow parallel drum system will fully change the market outlook.