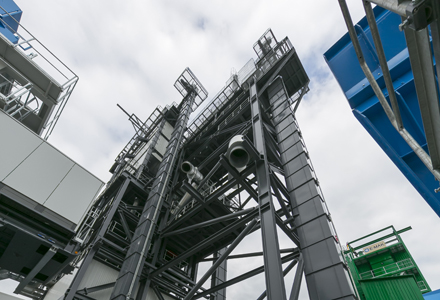
“This has been designed to optimise recycling,” said Benninghoven’s head of marketing Lars Henrich. “It can produce mixes with over 90 per cent recycled material.”
The secret to handling such a high proportion of RAP is the new heating system. The material is heated in counterflow by air from a hot gas generator. “Normally we have the burner directly in the drum. Here we use the burner to create hot gas so that the flame does not come into contact with the material,” explained Henrich.
The plant has the facility to produce hot recycled mixes and cold recycled mixes, with the cold process able to handle up to 40 per cent RAP. The ‘multi variable cold system’ provides flexibility and is useful when smaller quantities are required, said Henrich.
Every plant is bespoke, designed to suit the needs of a particular customer. Once dismantled at the end of the show, the Benninghoven plant will be heading to a road construction company in Germany. “The customer expects high production rates and the plant has to operate for 30 years, so they need the latest technology,” said Henrich.
Benninghoven expects Germany and other central European countries to be the biggest market for these 4000kg plants. New legislation in Germany relating to air quality and emissions, to be introduced in 2017, will be a driving force behind sales. To date, Benninghoven has delivered three plants, and expects demand to ramp up this year.