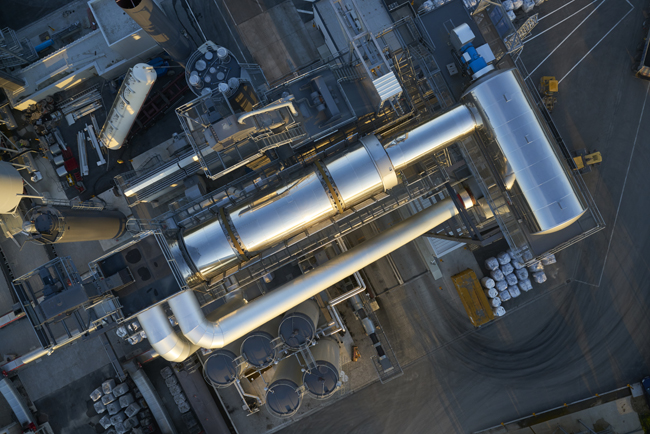
A key feature of the plant is the hot gas generator with counterflow parallel drum system, which allows high RAP content and minimal emissions. The plant supplies some 2,000tonnes/day of hot mix to job sites across the region. Depending on the formula, up to 1,800tonnes of the mixes can consist of RAP and also deliver a reduction in emissions.
In industrialised nations such as Germany most road sections are rebuilt rather than built from new. This means that millions of tonnes of asphalt have to be removed, largely by milling machines. At their peak these can load up to 3,000tonnes of milled material onto lorries in a single shift, while waste from road milling has long posed a challenge for road contractors.
But recycling technologies can transform RAP into a usable material. In many countries, almost every lorry delivering material to a job site carries a proportion of recycled asphalt. The German market uses a total of 40 million tonnes asphalt/year, of which 12 million tonnes/year is recycled asphalt. Across the world, too, RAP is increasingly being used as a resource so Benninghoven developed its counterflow parallel drum system with hot gas generator.
To benefit from using recycled material, Max Bögl invested in a new plant rather than modernising its existing one. The BA RPP 4000 comes with a second recycling technology as well – the multivariable cold feed system, which allows up to 40% RAP to be fed cold into the production process. This means that even small mix quantities from 2tonnes can be produced, allowing versatility for mixing plant supervisors.
The counterflow parallel drum system with hot gas generator is able to heat recycling material to the optimum asphalt processing temperature of 160°C in a parallel drum – in counterflow, as with aggregate obtained from quarries.
Unlike in conventional asphalt production, the burner heats the RAP indirectly, with hot gases, to ensure that the bitumen contained in the asphalt does not burn while keeping emission levels within the normal range.