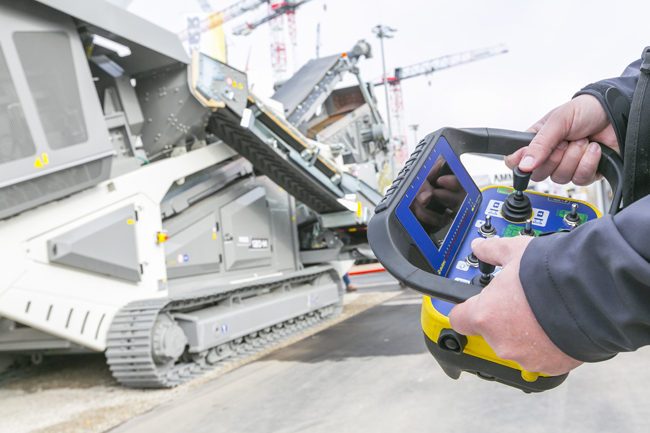
Asphalt plant manufacturers have introduced a range of new technologies and systems that will help deliver greater cost efficiency for customers. New plants can now utilise higher quantities of recycled asphalt pavement (RAP) or offer greater ease of transport for instance.
There are also key developments for coping with materials for use in asphalt production.
Ammann claims that its new RSS 120-M RAP recycling machine offers high quality output. According to Ferdinando Dell’Orto, global strategy manager shredders, “It doesn’t tear material apart like other recycling machines.”
The machine can produce up to 120tonnes/hour when using milled cuttings in the feed or 80tonnes/hour when using RAP in slab form. Weighing 35.5tonnes and measuring 13m long by 2.55m wide, the machine is said to be easy to transport while also being quick to commission onsite.
The machine offers high quality due to its primary shredder, which features counter-rotation at speeds of just 10rpm. Dell’Orto explained, “You have to keep the structure of the grain with the bitumen coating but without generating fines.”
He said that at this speed, lumps of RAP are broken up but without fracturing stones or generating fines. Furthermore, the bitumen coating around each piece of aggregate remains integral. A magnetic separator removes tramp iron or steel from the conveyor belt. Dell’Orto said that customers can choose mesh sizes on the screens to suit their needs, with the machine producing two feed sizes. Oversize material can be fed to the secondary shredder and recirculated into the feed, or can be used as sub-base. The machine is said to be cost-effective and productive and Dell’Orto added, “The return on investment is short.”
Power comes from a kW FPT diesel, which drives the generator feeding the electric motors. Options include weighing sensors on the output conveyors, allowing users to collate data on material flow rates for use within the Ammann telematics technology.
Meanwhile, E-Mak’s aggregate factory takes rock from a quarry, crushes it, sorts material into sizes and delivers this in the quantities required. Called Megaton, it can be used for aggregate production and cold mix production.
Megaton has been designed to operate in major materials production facilities, close to large conurbations. “The inspiration came from Istanbul, where there is a huge quarry, used by multiple construction companies, which is now surrounded by houses. In situations like that Megaton would be ideal,” said Onur Recepgil, brand and marketing manager for E-Mak.
As well as limiting dust, Megaton prevents aggregates from taking on moisture, reducing fuel used in asphalt production. Due to the controlled aggregate storage environment, it can also provide higher-quality materials, according to E-Mak.
Stone is fed through a VSI crusher with a capacity of 450tonnes/hour. The aggregate is lifted by a vertical elevator into the sieving units for grading and is stored according to size in the 3,000tonne-capacity silo.
As well as benefits to air quality and energy savings due to having dry aggregates, the Megaton could also make production more efficient. E-Mak international sales manager Muhammed Elhatip said, “The machine could run all night, so that you have 3,000tonnes of clean aggregate ready for production in the morning.”
Numerous asphalt plant developments are coming to market at present.
The new BG series includes models with outputs of 100-240tonnes/hour and because of the modular design, the plants can be tailored to meet local market requirements. Raji Elmawla, vice president international sales & marketing at Astec said, “We will produce them in Brazil and the US also as each market has its own regulations on emissions and recipes. You have to tailor-make the products to meet the demands of the local market but the basic specifications remain the same.”
The machine is designed for ease of maintenance and features comparatively few moving parts so as to lower maintenance needs.The plant also features Astec’s patented V-flights inside the drum, made from stainless steel for extended working life. The special flights ensure effective mixing, while lowering energy use. Options include a collar system so that RAP can be added into the drum, while an alternate option is to add RAP into the mixer.
Because of the modular design, the plant is said to be easy to transport and commission and Elmawla said, “You only need a small crane to erect it.”
In addition, Astec has a new mobile asphalt plant called the Voyager 140. This plant is designed to be quick to assemble and commission onsite as well as being equally quick to disassemble for transport. The firm says that the plant can produce up to 140tonnes/hour of asphalt, with a sophisticated control system that allows the user to switch between delivering base, binder and wearing course mixes. An important feature of the plant is that it can also handle feed material containing up to 50% recycled asphalt pavement (RAP).
Benninghoven is introducing its ECO asphalt mixing plant concept. The ECO asphalt mixing plants can produce 100-320tonnes/hour of asphalt but can also handle rapid location changes.
The modular design of the ECO series also allows components to be integrated afterwards so that users can react to future market requirements. All main ECO plant components are designed for simple transport in standard container dimensions. The throughput capability is said to be ideal for supplying major projects such as motorway construction. An integrated mixed material loading silo ensures a sufficient buffer while also providing storage capacity for up to seven different asphalt types. Thanks to the modular system, this can be expanded or retrofitted at any time with one or two secondary towers.
All the main ECO plant components are designed in ISO standard container dimensions, easing transport and allowing installation and commissioning in just five weeks. Versatility is claimed, while logistics costs are low and commissioning times are short.
CMI Roadbuilding Limited is widening its range with the introduction of the new Magnum Bullet plant. Highly portable, the plant is designed for ease of transport, reducing haulage costs. The plant can be assembled and commissioned speedily onsite, being made ready for use in a short period of time. The plant can then be taken apart quickly also, ready for transport to another site. According to CMI its counterflow plant can use up to 35% RAP in the feed and is able to produce up 150tonnes/hour of asphalt.
Also being unveiled by the firm is its E3-300 RAP-Star plant, which is able to produce 300tonnes/hour of material. This counterflow plant is able to handle up to 50% RAP in the feed material.
Asphalt plant manufacturer
The Flow Mix range continuous plant range consists of a drier and separate mixer. The driers have a ring towards the end of the chamber where up to 50% RAP can be added, which is also an important feature for the US market, said Hodge.
Intrame can also supply parallel drum technology that can work with 75% RAP and, in special cases, even higher. Such a plant has just been installed in Poland. “It has a gas generating chamber so that the flame never touches the RAP,” explained Hodge. “It can be used with an existing plant to reach around 70% RAP or you can use the parallel drum as an autonomous unit, add a mixer and it becomes a 100% RAP plant.”
Versatility is claimed for the latest mobile asphalt plant being offered by Lintec & Linhoff Holdings. The firm’s latest CSE asphalt plant is the CSE3000 model, with an average capacity of 220-240tonnes/hour, at 3% moisture content.
The company claims that the plant offers high versatility and mobility due to its modular, containerised design. The firm says that its modular design will also allow the asphalt plant to be retrofitted and upgraded in the future. The basic plant can be upgraded easily with the addition of the Lintec Ecological Processing (LEP95) warm asphalt mix system, hot or cold recycling system, environmental protection system for the bitumen fumes, filler silo or integrated hot storage silo.
Heat from the first drum is transferred efficiently to the second drum, allowing the RAP to be heated effectively. Meanwhile, insulated piping from the end of the second drum reroutes remaining heat back to the first drum for efficiency. Because the plant has a single burner, it requires less maintenance and uses 30% less fuel than a similarly-sized plant with twin burners.
The Master Tower’s filtration system is said to ensure that this plant has amongst the lowest emissions of any asphalt production facility. And sophisticated software allows the user to switch recipes from batch to batch.
Marini-Ermont claims that its new Explorer is the most mobile asphalt plant on the market. This continuous plant is said to be easy to commission and install and can be supplied to site in just six shipping containers. These contain the cold feeder, the dryer, the bag filters, the bitumen tank, the hotmix stage and the cabin, along with belts.
Thierry de Sars, product development and marketing director at the firm explained that the plant can also be erected without the need for a crane, due to a patented design featuring an onboard hydraulic raise system.
The plant is offered in a parallel flow version with an output of 150tonnes/hour as well as a counterflow variant with an output of 160tonnes/hour. The parallel flow variant can handle up to 35% RAP in the feed while the counterflow variant can cope with 50% RAP in the feed. Asphalt quality is said to be good from the plant, which utilises the same components and technology as the larger machines from the firm. The plant is fast to erect and commission as well as being quick to disassemble and make ready for transport.
Marini is also now offering four variants for the Xpress line, which previously featured just the Xpress 2500. The firm is widening choices for the customers with its Xpress 1500, 1500P, 2000 and 2000P models. These plants are designed for maximum mobility and can be transported in just two trailers, allowing high mobility.
The existing Xpress 2500 model provides an output of up to 200tonnes/hour. However, the new Xpress 1500 and 1500P offer outputs of 120tonnes/hour, while the larger Xpress 2000 and Xpress 2000P offer outputs of up to 160tonnes/hour.
These are designed for high mobility and retain similar features to the existing Xpress 2500 model. The 1500 variants feature 1.5tonne capacity mixers while the 2000 machines have 2tonne capacity mixers. The various models feature different burners to suit their throughput capacities.
All the Xpress models share the same ease of transport and fast erection capabilities. Just 3m wide, 21m long and with the trailers weighing 40tonnes, there are no transport restrictions when moving the separate units by road.
Meanwhile the machine is also easy to commission and can be erected in a single day. A simple recycling circuit can be added if required, allowing the plants to use up to 25% RAP inside the ring, 30% RAP into the mixer. Using a combination of both systems, up to 40% RAP can be used. Other capabilities include a warm mix output, as well as an optional foamed bitumen kit.