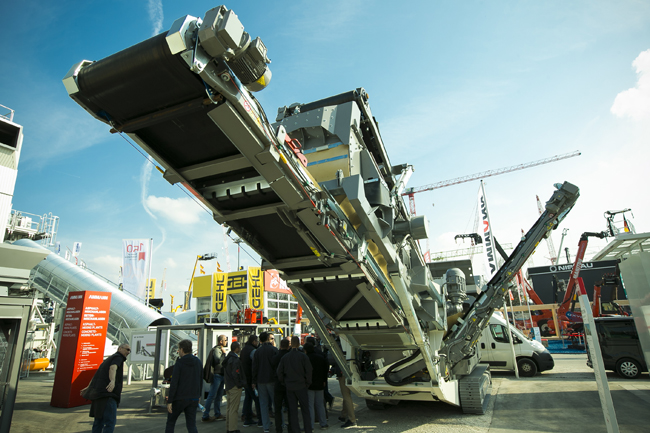
It is evident that several key trends are to the fore in the asphalt plant sector. Manufacturers have been investing a lot of time and money in developing new asphalt plant solutions that meet the demands of their customers, as well as important industry requirements.
First and foremost, there is a worldwide demand for recycling asphalt. It is abundantly clear that simply trucking milled road cuttings to landfill sites is both costly and a shameful waste of reusable material. All the leading asphalt plant manufacturers now offer equipment with some form of recycling capability. The degree of recycled asphalt pavement (RAP) use varies widely, with the most compact mobile plants able to be configured to use 15-20% of RAP in the feed. Some large and highly sophisticated asphalt plants (both continuous and batching types) meanwhile can use as much as 100% RAP in the feed, as long as necessary quality requirements are met.
Secondly, the need for ease of transport and faster commissioning has resulted in firms developing compact plants that fit in standard shipping containers and can be trucked to site. These generally come ready fitted with electrics so that installation may just mean clearing a suitable space, loading one container on top of the other, connecting the cables and erecting the materials storage and transport units.
Thirdly, modular design ensures that plants can be erected to best meet customer requirements, with different components available as required. Additional containers, materials storage or feed bins, conveyors and even RAP feeds can be added or removed to suit the needs of a particular installation. With this in mind, it is worth noting that asphalt plant specifications (whether continuous or batching types) vary widely from one customer to another, as purchasers will be selecting from a long list of available options.
Ensuring RAP quality is optimised is crucial. For this, both
Ammann’s solution is its RSS 120-M RAP recycling machine. This unit can produce up to 120tonnes/hour when using milled cuttings in the feed or 80tonnes/hour when using RAP in slab form. Weighing 35.5tonnes and measuring 13m long by 2.55m wide, the machine is said to be easy to transport while also being quick to commission onsite. The machine offers high quality due to its primary shredder, which features counter-rotation at speeds of just 10rpm. At this speed, lumps of RAP are broken up but without fracturing stones or generating fines. Furthermore, the bitumen coating around each piece of aggregate remains integral. A magnetic separator removes tramp iron or steel from the conveyor belt. Mesh sizes on the screens can be selected to suit customer needs, with the machine producing two feed sizes. Oversize material can be fed to the secondary shredder and recirculated into the feed, or can be used as sub-base.
A rather larger piece of equipment is E-MAK’s Megaton, which has been designed for quarries or aggregate processing facilities with multiple customers serving multiple sectors. This has been developed for use in quarries in or near large conurbations, where cities have spread out to meet industrial areas and the machine makes a substantial reduction in dust emissions from these working sites. It also cuts energy consumption since it keeps aggregates dry. This reduces the heat required to produce asphalt because there is less moisture. The Megaton uses quarried rock as a feed, crushes it in a vertical shaft impactor, lifts it using a vertical elevator and then puts it through a variety of screening units to produce the grading of aggregate required for a concrete or asphalt mix. The aggregates then go into huge storage silos with a capacity of 3,000tonnes.
The new BG series includes models with outputs of 100-240tonnes/hour. The modular design means that the plants can be tailored to meet local market requirements, while also meeting the need for recycling by handling up to 40% RAP in the mixer.
The machine is designed for ease of maintenance and features comparatively few moving parts so as to lower maintenance needs. Meanwhile, the plant also features Astec’s patented V-flights inside the drum, made from stainless steel for extended working life. Options include a collar system so that RAP can be added into the drum, while an alternate option is to add RAP into the mixer.
Benninghoven says that its ECO asphalt mixing plants can produce 100-320 tonnes/hour of asphalt but can also handle rapid location changes. The modular design of the ECO series also allows components to be integrated afterwards so that users can react to future market requirements. All main ECO plant components are designed for simple transport in standard container dimensions. The throughput capability is said to be ideal for supplying major projects such as motorway construction. An integrated mixed material loading silo ensures a sufficient buffer while also providing storage capacity for up to seven different asphalt types. Thanks to the modular system, this can be expanded or retrofitted at any time with one or two secondary towers. Versatility is claimed, while logistics costs are low and commissioning times are short.
CMI Roadbuilding Limited has developed its Magnum Bullet plant, which is designed to be highly portable for ease of transport, reducing haulage costs. The plant can be assembled and commissioned speedily onsite, being made ready for use in a short period of time. The plant can then be taken apart quickly also, ready for transport to another site. According to CMI its counterflow plant can use up to 35% recycled asphalt pavement (RAP) in the feed and is able to produce up 150tonnes/hour of asphalt.
Lintec & Linhoff Holdings says that versatility and modularity are key features of its CSE3000 asphalt plant, due to its modular, containerised design. This offers an average capacity of 220-240tonnes/hour, at 3% moisture content.
The firm says that the modular design means that customers can add additional features or upgrade components. The basic plant can be modified with the addition of the