Now part of the Wirtgen Group, Benninghoven is introducing new recycled asphalt pavement (RAP) developments. The firm says that its counterflow parallel drum system with hot gas generator offers considerable benefits for RAP applications. The new design ensures that the recycled material is heated in a counterflow cycle, flowing against the heat source in the drum. The design achieves a high material temperature while lowering exhaust gas temperature. The material no longer has to be run overheated, which c
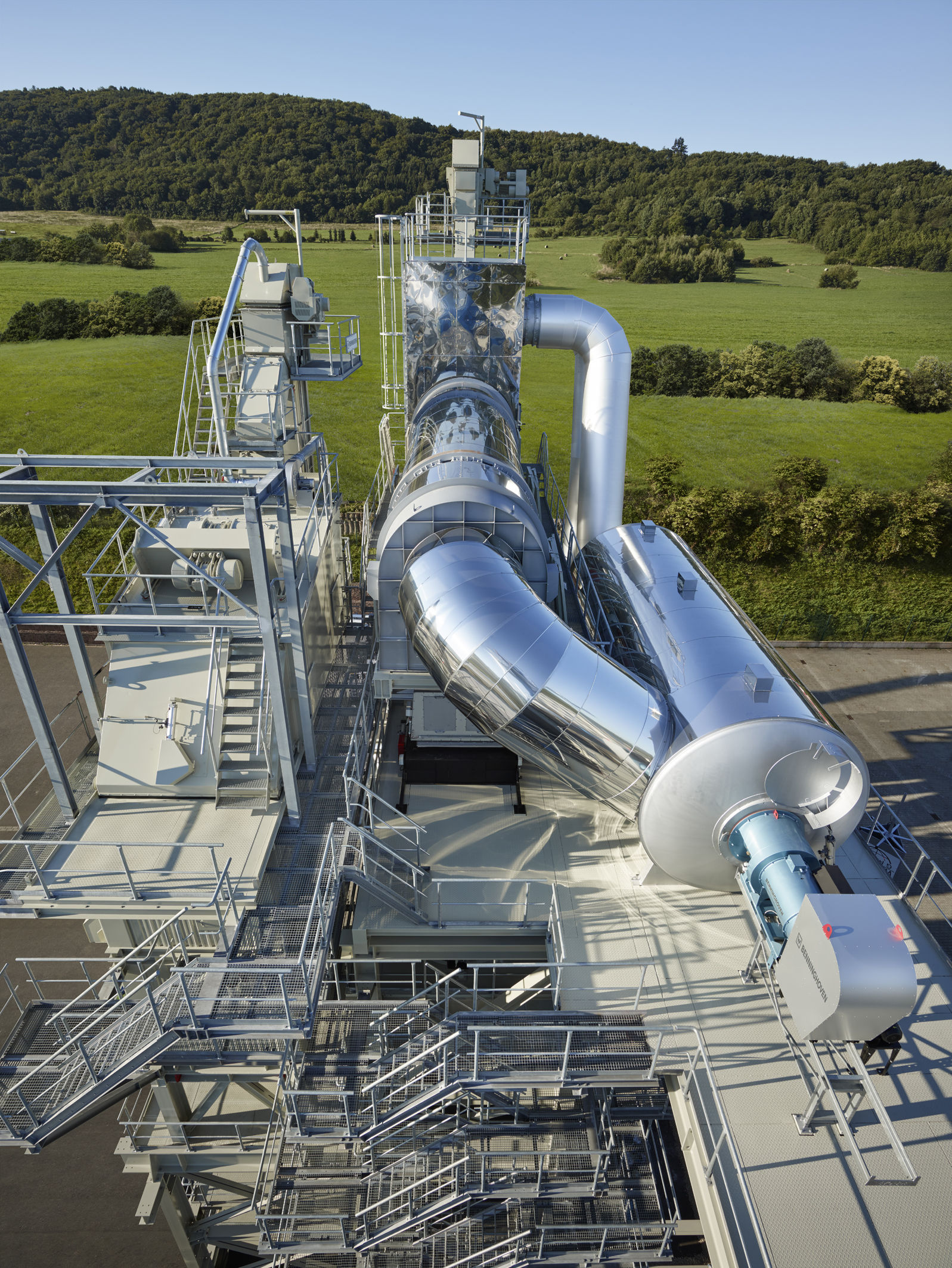
Benninghoven offers new asphalt plant innovations
Now part of the 364 Wirtgen Group, 167 Benninghoven is introducing new recycled asphalt pavement (RAP) developments. The firm says that its counterflow parallel drum system with hot gas generator offers considerable benefits for RAP applications. The new design ensures that the recycled material is heated in a counterflow cycle, flowing against the heat source in the drum. The design achieves a high material temperature while lowering exhaust gas temperature.
The material no longer has to be run overheated, which cuts energy use. Head of marketing Lars Henrich said, “The burner is installed in a separate hot gas generator.”
This process is only possible due to the use of the hot gas generator as direct firing would damage the RAP and make it unusable. Burner, hot gas generator, dryer drum, separator cover and circulating air system are said to be precisely balanced. Henrich added that the system also produces low CO2 emissions while allowing a much higher percentage of hot RAP in the mix (up to 90%) than with earlier generation plant designs. Also new is the potential for an additional cold RAP circuit for its plants, using a different elevator than for the hot RAP.
The material no longer has to be run overheated, which cuts energy use. Head of marketing Lars Henrich said, “The burner is installed in a separate hot gas generator.”
This process is only possible due to the use of the hot gas generator as direct firing would damage the RAP and make it unusable. Burner, hot gas generator, dryer drum, separator cover and circulating air system are said to be precisely balanced. Henrich added that the system also produces low CO2 emissions while allowing a much higher percentage of hot RAP in the mix (up to 90%) than with earlier generation plant designs. Also new is the potential for an additional cold RAP circuit for its plants, using a different elevator than for the hot RAP.