Leading formwork manufacturers have secured some impressive contracts in Africa, as the continent’s transport infrastructure continues to improve at a rapid pace. Meanwhile, other bridgework equipment companies are also seeing their products in demand in Africa, as well as North America and Australia. Guy Woodford reports
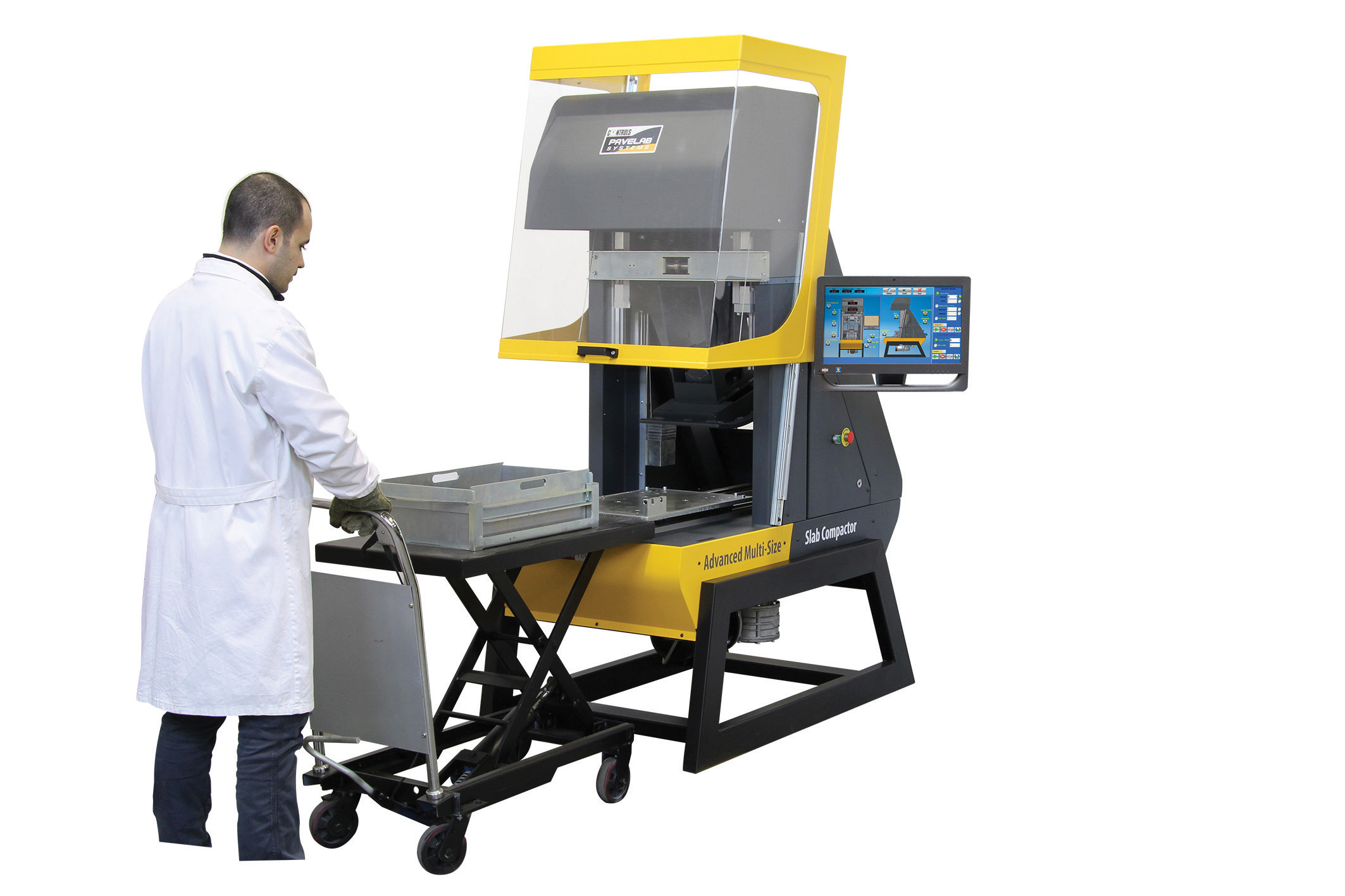
The electro-mechanical slab compactor from PaveLab is said to offer high accuarcy
Our materials testing news includes interesting developments: one-off machines for experiments and research, a Hamburg wheel tracker which can perform two different tests simultaneously, and non-destructive concrete testing devices which could make assessing bridges faster and more efficient - Kristina Smith reports
The Asphalt Institute in the US is about to take delivery of a novel testing machine: a twin-headed four- point bending roller compactor from5941 Cooper Technology. The experimental machine has been designed to manufacture roller compacted beams for four-point bending tests.
“The traditional way of creating beams is time-consuming,” explained Cooper managing director Peter Grafton. “If the beams could be created using a roller compactor, testing laboratories could save time and money.”
Engineers at Cooper Research Technology’s head office in Ripley, UK, have spent three months developing the machine, working with Asphalt Institute senior research engineer Phil Blankenship. Blankenship, with Cooper’s director of Research Andrew Cooper, is working on the development of an AASHTO standard for roller compaction.
The roller compactor uses loads equivalent to those of full-scale compaction equipment to create beams with the target mixture densities. According to Cooper, this method of creating laboratory specimens results in properties that most closely simulate those of materials in the highway.
Cooper Research Technology has a history of developing new machines and standards. Founder and inventor Keith Cooper developed the very first dynamic testing machine, the Nottingham Asphalt Tester back in 1988, with son Andrew continuing the tradition today.
“When people are looking for something out-of-the-ordinary, they come to us,” said Grafton. “We can produce equipment designed to measure variables that standard equipment cannot. The products recently developed by Cooper will never sell in numbers, but they will help with true research which hopefully in turn will help move asphalt testing forward.”
Another one-off machine made recently by Coopers is a large hydraulic four point bending machine which is fitted with camera recognition, aimed to help researchers better understand what is happening to the material when under test. This 12-month project for the University of Limoges is still ongoing.
“Customers like this are true researchers,” said Grafton, “and because of our years of experience creating original machines, we can work with them to exactly satisfy their needs.”
7056 ELE International has launched two new machines for soil testing: the Automatic Soil Compactor for producing test specimens and the Digital Tritest 50 for carrying out triaxial tests. The Automatic Soil Compactor has been designed for ease of use and longevity. Conforming to a range of standards, including BS1277-4 and ASTM D698, the compactor can be used for both Proctor and California Bearing Ratio (CBR) tests.
The machine’s vertically mounted Rammer can be adjusted for drop height and weight and its mould table automatically rotates through 40° after each blow as the Rammer rises. The compactor can be used to compact samples in 100mm moulds, where each blow acts on a single radius, and in 150m moulds, where consecutive blows are struck on an inner and outer radius.
ELE’s machine differs from several of its competitors’ in its turntable movement. Most rotate and move laterally, where as ELE’s only rotates, using a single heavy duty bearing, with the Rammer alignment changed using a solenoid controlled mechanism.
“This configuration offers greater simplicity and reliability with a considerably longer operating life,” said ELE.
The Digital Tritest 50 triaxial load frame provides the uniform rate of axial loading required in triaxial tests used to determine the strength and stress-strain relationships on a cylindrical specimen of soil. Total or effective stress can be measured, depending on application; effective stress being both time and permeability dependent and offering a more accurate measurement of strength.
The Tritest 50 has been designed for a range of applications from site assessment for highways agencies and public works departments, to private laboratory testing, and the teaching of soil mechanics in colleges and universities. Its 50kN capacity and speed range of between 0.00001 - 9.99999mm/min make it flexible enough for a variety of research environments, while a microprocessor-controlled digital stepper motor drive system allows variable speed control with no gear changes or maintenance required.
Unlike other load testing frames on the market, the Tritest 50 has a return-to-datum facility that returns the loading platen to the height at which the previous test was initiated, saving engineers valuable time when setting up new tests.
Designed for use with ELE test accessories and DataSystem 7 (DS7) data acquisition hardware and software, the load frame is able to accommodate test samples of up to 100mm in diameter and 200mm long. According to ELE, “The Digital Tritest 50 offers the highest specification on the market at a competitive price.”
2139 Controls Group has unveiled four new testing machines: automatic roller compactors for creating slabs in the laboratory; the Automax E-Modulus Power and Console for measuring Elastic Modulus; the Vicmatic-2 for measuring setting times; and an Automatic Consolidation Oedometer for soils.
The group’s asphalt testing division, Pavelab Systems, has developed an automatic roller compactor which can produce slabs of bituminous mixes in the laboratory. These slabs can then be used for wheel tracking tests or can be cut into beams to be used for a variety of tests. The compactor is available in two versions: the standard 77-PV42A05 version, designed to compact slabs of up to 500mm x 300mm to UNI EN 12697-33 standards, and a research version, 77-PV40b05, which has some additional features.
Slabs can be compacted to a defined thickness or density. And the compactor can also be equipped with a vibrating system to simulate the action of a vibrating roller compactor.
The new Automax E-Modulus Power and Control Console helps measure static modulus of elasticity, required to predict the behaviour of a structure under load. The console, when connected to a suitable test frame, will perform test cycles conforming to a new EN standard which is currently under development.
Currently there are several different national standards which define how Elastic Modulus should be measured: DIN 1048/1, ASTM C469, BS 1881:121, ISO 6784, UNI 6556. Parameters such as the number of cycles, the cycle wave shape, and accuracy verification vary between the standards and a CEN committee is now developing a new EN standard to bring together the different approaches.
For cement, mortar and gypsum, Controls has launched its second generation setting time tester, the Vicmatic-2. Improvements when compared to its predecessor include its interface and software, large accessibility to the test space, a practical accessory for in-water testing, and the ability to create a network of 32 independent units controlled through a single PC through LAN hubs.
Suitable for standard tests and for research, a range of test options are available with the Vicmatic-2 including test start delay, varying penetration points positions, manual or automatic penetration rate, free or driven falling mode, automatic end-test detection, and automatic determination of initial and final setting time at depths which can be selected.
Wykeham Farrance, the soil mechanics division of Controls Group, has developed the Automatic Consolidation Oedometer (ACE) 26-WF3120. The machine determines the rate and magnitude of consolidation of a soil specimen restrained laterally and subject to a number of successive increments of vertical loads and can test all standard consolidation cells between 50.47mm and 112.80mm diameter.
The compact load frame houses two coaxial pneumatic cylinders, the smallest for low loads and the other for higher loads, with an automatic switch-off from one to the other. The load is controlled by a high precision pneumatic servo-valve. The ACE has two analogue channels, one for the displacement transducer and the other for the load cell with closed loop feedback control.
The test end can be programmed either on time or step base. The software Controls up to 60 ACE units from a PC.
Test parameters are programmed by the operator with test results recorded and displayed in real time. Test data can be processed by the Geo-Analysis Templates conforming to BS or ASTM Standards.
282 Matest has added a Hamburg Wheel Tracker to its range of asphalt testing machines. The SmarTracker can switch between wet and dry testing, as can some competitor machines, but what makes this tracker unique, according to Matest, is the fact that it can perform both tests simultaneously.
“SmarTracker is the most versatile and innovative wheel tracker on the market,” said Matest marketing director Paola Maestroni.
The machine has been developed in association with US materials testing equipment manufacturer InstroTek. “We worked with InstroTek scientists and engineers to develop this machine by listening to people who really know about this test, many of them in the US industry,” said Maestroni.
The Hamburg Wheel Tracker is used to evaluate resistance of asphalt mixes to rutting and moisture damage. A loaded steel wheel tracks back and forth on a rectangular sample, while rut depth is continuously measured; the SmarTracker uses displacement transducers to measure ruts between 0 and 25mm deep to Plus or minus 0.1mm.
The European code, EN 12697-22, requires that the test be performed either dry or wet, whereas for the US code, AASHTO T324, samples must always be submerged in water. In addition, the EN code calls for a rubber wheel and the AASHTO for a steel one.
Because of the differences in test requirements it can be useful for Hamburg Wheel Trackers to be able to switch between the test versions. The SmarTest’s two tracking wheels operate independently to allow different tests to be carried out at the same time, which could be of use in a research situation.
“We are always looking to innovate, to offer something more,” said Maestroni. “But what is important to people buying these machines is that they are reliable, sturdy and user friendly.”
Some of the SmarTracker’s features highlighted by Matest include its wheel roll-off mechanism which does not require special tools or a lifting mechanism to remove the wheel after each test or during sample loading. The machine also has a sliding positioning mechanism to ease placement of samples in the machine. When wet tests are performed the temperature of the water must be kept constant. For the Smartest, a mechanical water recirculation bath maintains temperatures to Plus or minus 1°C.
The SmarTracker’s touch screen Controls are based on the windows operating system and data can be stored and transferred using a USB drive.
1417 Tecnotest’s latest development is the T 100/E02, a 100kN variable speed testing machine. The multitest machine can be used in both compression and tension at any speed between 0.01mm per minute to 52mm per minute.
“Different tests require different speeds,” says Tecnotest R&D engineer Pierpaolo Violo. “This is a flexible and modular system which will allow laboratories to test many materials."
Applications will include: compression tests on soil-bituminous mixes, asphalt, soil-cement mixes; flexural tests on concrete, mortar, Stone, blocks and tiles; and quick triaxial tests.
For tests requiring a constant deformation rate, the speed is input at the start. The closed loop control then maintains this speed during the test, irrespective of load. Tests which require a constant load rate can also be performed, by setting that rate at the beginning of the procedure.
The machine has a maximum vertical Span of 800mm and a minimum of 100mm, a horizontal Span of 380 mm and a 100mm cylinder stroke. The Eurotronic control unit is a four-channel microprocessor which Controls the test, data acquisition, processing and display and can download the test data to a PC.
2884 Humboldt Manufacturing has partnered with Giatec Scientific to supply several novel pieces of equipment for the non-destructive testing of concrete.
Giatec RCON and Giatec Surf measure the bulk and surface electrical resistivity of concrete, respectively. The devices can be used to test concrete specimens, such as those used for compressive strength tests, in the laboratory quickly and non-destructively.
Electrical resistivity of concrete has been shown to have a direct correlation with durability characteristics such as the chloride diffusion coefficient and rapid chloride permeability test results. AASHTO TP 95-11 ‘Standard Method of Test for Surface Resistivity Indication of Concrete’s Ability to resist Chloride Ion Penetration’, published in 2011, is the first standard test method to use resistivity.
According to Humboldt’s general manager, sales and marketing John Lamond, ASTM and AASHTO are due to release other test methods based on this concept shortly with some Departments of Transportation in the US already using it.
“The wide acceptance of the easy and fast measurements by the resistivity test methods in the concrete industry will result in significant improvements in concrete quality control,” said Lamond, “and ultimately helps with addressing the sustainability issues in the construction sector.”
Giatec has also developed the Giatec iCOR aimed at the concrete inspection industry. A hand-held device, the iCOR detects rebar corrosion when placed on the surface of a structure and also calculates the rate of corrosion.
According to Humboldt, this solution will be much more accurate and reliable than current inspection methods: traditional techniques involve dragging chains across bridge decks, or tapping with a hammer; more specialised field techniques such as the half-cell potential method are not always reliable and only give an indication that there might be corrosion.
The Asphalt Institute in the US is about to take delivery of a novel testing machine: a twin-headed four- point bending roller compactor from
“The traditional way of creating beams is time-consuming,” explained Cooper managing director Peter Grafton. “If the beams could be created using a roller compactor, testing laboratories could save time and money.”
Engineers at Cooper Research Technology’s head office in Ripley, UK, have spent three months developing the machine, working with Asphalt Institute senior research engineer Phil Blankenship. Blankenship, with Cooper’s director of Research Andrew Cooper, is working on the development of an AASHTO standard for roller compaction.
The roller compactor uses loads equivalent to those of full-scale compaction equipment to create beams with the target mixture densities. According to Cooper, this method of creating laboratory specimens results in properties that most closely simulate those of materials in the highway.
Cooper Research Technology has a history of developing new machines and standards. Founder and inventor Keith Cooper developed the very first dynamic testing machine, the Nottingham Asphalt Tester back in 1988, with son Andrew continuing the tradition today.
“When people are looking for something out-of-the-ordinary, they come to us,” said Grafton. “We can produce equipment designed to measure variables that standard equipment cannot. The products recently developed by Cooper will never sell in numbers, but they will help with true research which hopefully in turn will help move asphalt testing forward.”
Another one-off machine made recently by Coopers is a large hydraulic four point bending machine which is fitted with camera recognition, aimed to help researchers better understand what is happening to the material when under test. This 12-month project for the University of Limoges is still ongoing.
“Customers like this are true researchers,” said Grafton, “and because of our years of experience creating original machines, we can work with them to exactly satisfy their needs.”
ELE offers two new testing units
The machine’s vertically mounted Rammer can be adjusted for drop height and weight and its mould table automatically rotates through 40° after each blow as the Rammer rises. The compactor can be used to compact samples in 100mm moulds, where each blow acts on a single radius, and in 150m moulds, where consecutive blows are struck on an inner and outer radius.
ELE’s machine differs from several of its competitors’ in its turntable movement. Most rotate and move laterally, where as ELE’s only rotates, using a single heavy duty bearing, with the Rammer alignment changed using a solenoid controlled mechanism.
“This configuration offers greater simplicity and reliability with a considerably longer operating life,” said ELE.
The Digital Tritest 50 triaxial load frame provides the uniform rate of axial loading required in triaxial tests used to determine the strength and stress-strain relationships on a cylindrical specimen of soil. Total or effective stress can be measured, depending on application; effective stress being both time and permeability dependent and offering a more accurate measurement of strength.
The Tritest 50 has been designed for a range of applications from site assessment for highways agencies and public works departments, to private laboratory testing, and the teaching of soil mechanics in colleges and universities. Its 50kN capacity and speed range of between 0.00001 - 9.99999mm/min make it flexible enough for a variety of research environments, while a microprocessor-controlled digital stepper motor drive system allows variable speed control with no gear changes or maintenance required.
Unlike other load testing frames on the market, the Tritest 50 has a return-to-datum facility that returns the loading platen to the height at which the previous test was initiated, saving engineers valuable time when setting up new tests.
Designed for use with ELE test accessories and DataSystem 7 (DS7) data acquisition hardware and software, the load frame is able to accommodate test samples of up to 100mm in diameter and 200mm long. According to ELE, “The Digital Tritest 50 offers the highest specification on the market at a competitive price.”
Controls develops four innovative testers
The group’s asphalt testing division, Pavelab Systems, has developed an automatic roller compactor which can produce slabs of bituminous mixes in the laboratory. These slabs can then be used for wheel tracking tests or can be cut into beams to be used for a variety of tests. The compactor is available in two versions: the standard 77-PV42A05 version, designed to compact slabs of up to 500mm x 300mm to UNI EN 12697-33 standards, and a research version, 77-PV40b05, which has some additional features.
Slabs can be compacted to a defined thickness or density. And the compactor can also be equipped with a vibrating system to simulate the action of a vibrating roller compactor.
The new Automax E-Modulus Power and Control Console helps measure static modulus of elasticity, required to predict the behaviour of a structure under load. The console, when connected to a suitable test frame, will perform test cycles conforming to a new EN standard which is currently under development.
Currently there are several different national standards which define how Elastic Modulus should be measured: DIN 1048/1, ASTM C469, BS 1881:121, ISO 6784, UNI 6556. Parameters such as the number of cycles, the cycle wave shape, and accuracy verification vary between the standards and a CEN committee is now developing a new EN standard to bring together the different approaches.
For cement, mortar and gypsum, Controls has launched its second generation setting time tester, the Vicmatic-2. Improvements when compared to its predecessor include its interface and software, large accessibility to the test space, a practical accessory for in-water testing, and the ability to create a network of 32 independent units controlled through a single PC through LAN hubs.
Suitable for standard tests and for research, a range of test options are available with the Vicmatic-2 including test start delay, varying penetration points positions, manual or automatic penetration rate, free or driven falling mode, automatic end-test detection, and automatic determination of initial and final setting time at depths which can be selected.
Wykeham Farrance, the soil mechanics division of Controls Group, has developed the Automatic Consolidation Oedometer (ACE) 26-WF3120. The machine determines the rate and magnitude of consolidation of a soil specimen restrained laterally and subject to a number of successive increments of vertical loads and can test all standard consolidation cells between 50.47mm and 112.80mm diameter.
The compact load frame houses two coaxial pneumatic cylinders, the smallest for low loads and the other for higher loads, with an automatic switch-off from one to the other. The load is controlled by a high precision pneumatic servo-valve. The ACE has two analogue channels, one for the displacement transducer and the other for the load cell with closed loop feedback control.
The test end can be programmed either on time or step base. The software Controls up to 60 ACE units from a PC.
Test parameters are programmed by the operator with test results recorded and displayed in real time. Test data can be processed by the Geo-Analysis Templates conforming to BS or ASTM Standards.
Matest widens asphalt testing range
“SmarTracker is the most versatile and innovative wheel tracker on the market,” said Matest marketing director Paola Maestroni.
The machine has been developed in association with US materials testing equipment manufacturer InstroTek. “We worked with InstroTek scientists and engineers to develop this machine by listening to people who really know about this test, many of them in the US industry,” said Maestroni.
The Hamburg Wheel Tracker is used to evaluate resistance of asphalt mixes to rutting and moisture damage. A loaded steel wheel tracks back and forth on a rectangular sample, while rut depth is continuously measured; the SmarTracker uses displacement transducers to measure ruts between 0 and 25mm deep to Plus or minus 0.1mm.
The European code, EN 12697-22, requires that the test be performed either dry or wet, whereas for the US code, AASHTO T324, samples must always be submerged in water. In addition, the EN code calls for a rubber wheel and the AASHTO for a steel one.
Because of the differences in test requirements it can be useful for Hamburg Wheel Trackers to be able to switch between the test versions. The SmarTest’s two tracking wheels operate independently to allow different tests to be carried out at the same time, which could be of use in a research situation.
“We are always looking to innovate, to offer something more,” said Maestroni. “But what is important to people buying these machines is that they are reliable, sturdy and user friendly.”
Some of the SmarTracker’s features highlighted by Matest include its wheel roll-off mechanism which does not require special tools or a lifting mechanism to remove the wheel after each test or during sample loading. The machine also has a sliding positioning mechanism to ease placement of samples in the machine. When wet tests are performed the temperature of the water must be kept constant. For the Smartest, a mechanical water recirculation bath maintains temperatures to Plus or minus 1°C.
The SmarTracker’s touch screen Controls are based on the windows operating system and data can be stored and transferred using a USB drive.
Variable speed testing from Tecnotest
“Different tests require different speeds,” says Tecnotest R&D engineer Pierpaolo Violo. “This is a flexible and modular system which will allow laboratories to test many materials."
Applications will include: compression tests on soil-bituminous mixes, asphalt, soil-cement mixes; flexural tests on concrete, mortar, Stone, blocks and tiles; and quick triaxial tests.
For tests requiring a constant deformation rate, the speed is input at the start. The closed loop control then maintains this speed during the test, irrespective of load. Tests which require a constant load rate can also be performed, by setting that rate at the beginning of the procedure.
The machine has a maximum vertical Span of 800mm and a minimum of 100mm, a horizontal Span of 380 mm and a 100mm cylinder stroke. The Eurotronic control unit is a four-channel microprocessor which Controls the test, data acquisition, processing and display and can download the test data to a PC.
Non-destructive tester from Homboldt and Giatec
Giatec RCON and Giatec Surf measure the bulk and surface electrical resistivity of concrete, respectively. The devices can be used to test concrete specimens, such as those used for compressive strength tests, in the laboratory quickly and non-destructively.
Electrical resistivity of concrete has been shown to have a direct correlation with durability characteristics such as the chloride diffusion coefficient and rapid chloride permeability test results. AASHTO TP 95-11 ‘Standard Method of Test for Surface Resistivity Indication of Concrete’s Ability to resist Chloride Ion Penetration’, published in 2011, is the first standard test method to use resistivity.
According to Humboldt’s general manager, sales and marketing John Lamond, ASTM and AASHTO are due to release other test methods based on this concept shortly with some Departments of Transportation in the US already using it.
“The wide acceptance of the easy and fast measurements by the resistivity test methods in the concrete industry will result in significant improvements in concrete quality control,” said Lamond, “and ultimately helps with addressing the sustainability issues in the construction sector.”
Giatec has also developed the Giatec iCOR aimed at the concrete inspection industry. A hand-held device, the iCOR detects rebar corrosion when placed on the surface of a structure and also calculates the rate of corrosion.
According to Humboldt, this solution will be much more accurate and reliable than current inspection methods: traditional techniques involve dragging chains across bridge decks, or tapping with a hammer; more specialised field techniques such as the half-cell potential method are not always reliable and only give an indication that there might be corrosion.