Among the new developments in materials testing highlighted this month is a brand new idea from one manufacturer: in-depth training to help upskill technicians in developing countries - Kristina Smith reports
CONTROLS has added another dimension to its business with the launch of a specialist training service: CONTROLS Academy Centre. In what the construction testing equipment manufacturer believes is a first for the industry, CONTROLS will be providing in-depth theoretical and practical training to thos
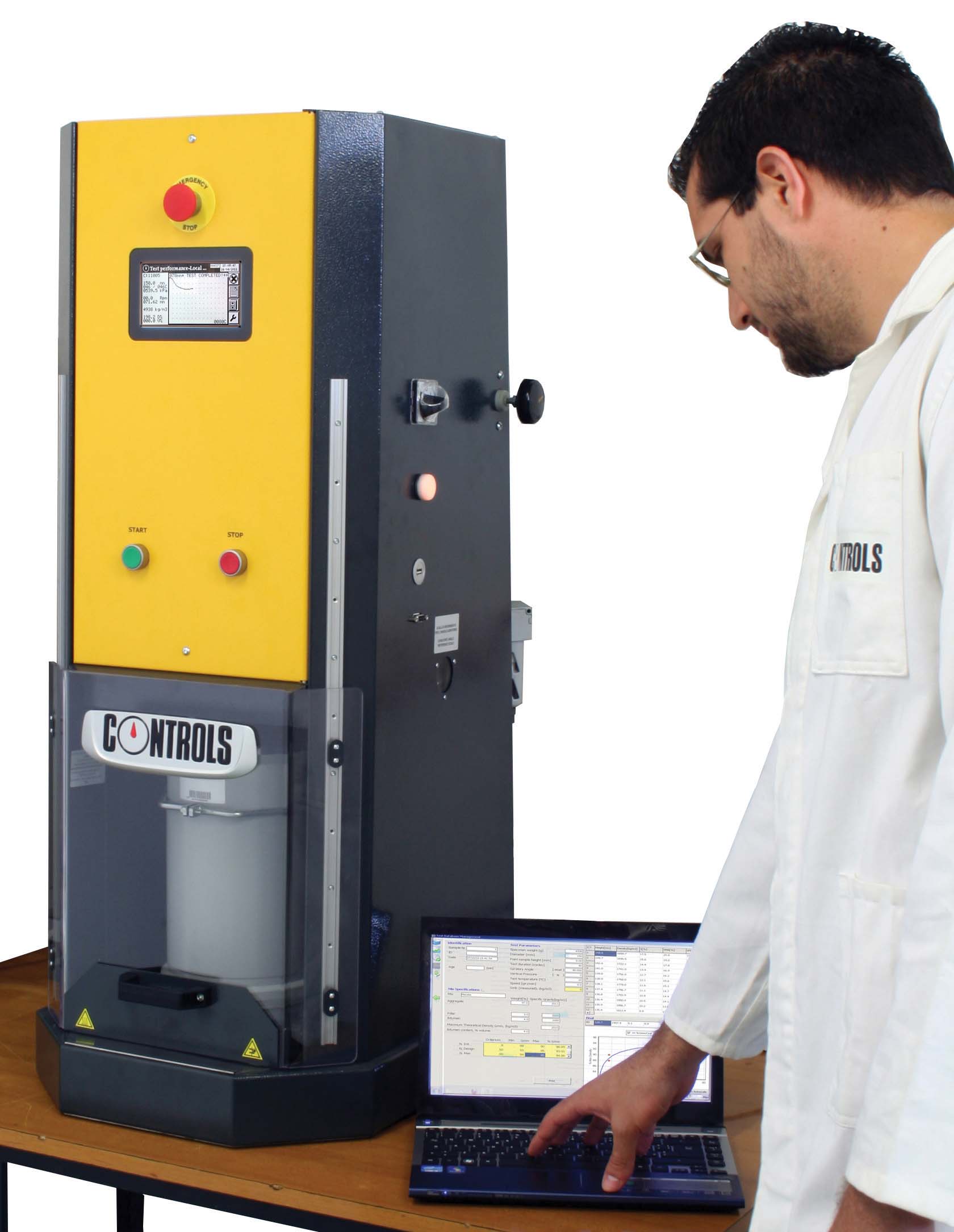
CONTROLS says that its Gyratory Compactor offers high accuracy in testing
Among the new developments in materials testing highlighted this month is a brand new idea from one manufacturer: in-depth training to help upskill technicians in developing countries - Kristina Smith reports
2139 Controls has added another dimension to its business with the launch of a specialist training service: Controls Academy Centre. In what the construction testing equipment manufacturer believes is a first for the industry, Controls will be providing in-depth theoretical and practical training to those working in testing laboratories.
“There is nothing like this on the market,” said Matteo Dal Ben, road business unit product specialist for Controls who heads up the new centre. “It fills a gap between basic training and university courses.”
Controls has set up the new service in response to enquiries from customers in both the public and private sectors, according to Dal Ben. In particular countries such as Iraq and Dubai in the Middle East and emerging African countries such as Kenya and Tanzania are keen for this type of training.
“The aim is to help people to use the machines better, with a critical knowledge of testing and materials,” said Dal Ben. “It’s not just about how to operate the machines and which buttons to press.”
In many regions, trained and experienced people are in short supply, and this service aims to help laboratories upskill their employees and in turn provide a better service to their customers. For Controls it is also an opportunity to increase its presence in developing markets around the world.
Over the past four months, Controls has developed two modules, both of which are focussed on road paving, as this is the area where it receives most requests for training, according to Dal Ben. The first module provides an overview of the road structure: subgrade, sub-base and an introduction to hot mix asphalt. The second looks at hot mix asphalt, with a focus on Superpave specifications.
The courses will cover current practice, new developments and recent innovations in laboratory testing as well as other construction or pavement engineering topics relevant to the particular organisation. As well as training new recruits to the testing industry, Controls aims to help laboratory managers and technicians meet their Continuing Professional Development (CPD) commitments.
Each of the two-week modules will be a mix of theoretical and practical learning. Around a week will be spent in the classroom and a week in the laboratory, although Controls can adapt the training to suit the needs of the particular client.
Though Controls is able to run courses based round its own head office in Milan, it is more likely that it will be providing the training in its customers’ test laboratories. “This is likely to be a more cost-effective way of delivering training for most customers,” said Dal Ben, who estimates the cost of the teaching will be around US$700/module for each student.
Controls will be drawing on its in-house expertise from within its PAVELAB SYSTEMS division, set up to focus on road pavement testing equipment and techniques. Employees will bring experience gained in sitting on standards committees, setting up testing regimes and offering practical solutions in countries around the world. Professors Maurizio Crispino and Emanuele Toraldo from Politecnico Milano will also be involved in the face-to-face teaching of the courses, which will equip attendees with knowledge of the relevant major international specifications such as ASTM/AASHTO, BS and EN.
Dal Ben expects to deliver the first of the training courses overseas later this year. If the new academy is popular, Controls could develop further modules in the areas of concrete and soil testing. “I am very confident that this will be a success because people are asking for this service and no one else provides it,” he said. “We have had very good feedback so far, from both the lower and upper levels of ministries and large companies.”
282 Matest has developed the B039A Asphalt Shear-box Compactor (ASC), a high performance servo-hydraulic shear-box compactor that can apply a maximum vertical force of 100kN and a maximum shear force of 50kN.
Shear-box compactors have gained popularity over the past few years due to the fact that they can produce specimens that are more representative of those taken from roads. The shearing action of the shear-box compactor replicates field compaction in order to reproduce the properties of field-compacted asphalt in a laboratory.
“Nowadays, there is increasing concern about particle orientation in laboratory compacted hot mix asphalt specimens,” said Matest marketing director Paola Maestroni. “Although the gyratory compactor can produce cylindrical specimens that can be used for several tests, the particle orientation does not resemble a field compacted specimen, and this has resulted in great interest in alterative sample preparation techniques.”
In addition to the shear-box’s ability to produce specimens with more authentic particle orientation, it can also provide a measure of workability. This method also allows a wide range of samples to be produced – a 150mm by 450mm by 185mm piece can be cut into beams, slabs for Wheel Tracking or cored to produce cylinders for AMPT or other tests requiring cylinders.
Matests’s B039A ASC is fully automatic with a touch screen display. It has been designed for ease of use in entering test parameters, acquiring and processing data and generating test reports and data files, says Matest.
Roller compactors also produce specimens with a similar particle orientation to those produced in the field. Matest’s B039 Asphalt Roller Compactor (ARC), which it has recently updated, has several noteworthy features, according to the manufacturer.
Matest’s ARC has an electro-mechanical system, rather than requiring a compressor or hydraulic pressure. Matest was the first to do this, says Maestroni, with benefits including reduced noise compared to a hydraulic roller and elimination of the ‘bounce-back’ issues which used to affect pneumatic machines. The B039 ARC can also compact larger slabs than some competitor machines: 500mm by 400mm.
Another important feature of its ARC, according to Matest, is that a heated roller can be installed on the machine to help make the compacting process more similar to that on site. A vibrating action, sometimes required by researchers, can also be added to the compacting process.
A limitation with roller compactors is that they can only be used for thin slabs. “Once you go above a thickness of 75mm, the uniformity and air void distributions begin to suffer as the specimen becomes less homogeneous,” said Maestroni. “It cannot produce thick slabs that are representative of field compacted asphalt.”
This is where the shear- box compactor comes in as it can be used to produce much thicker specimens. “These machines must be considered as different but complementary,” said Maestroni. “Whilst both are excellent machines, it must be pointed out that they are ideally suited to different specimen geometries.”
1417 Tecnotest is to launch a new T644Automatic CBR/Proctor Compactor in May at the 160 Asphaltica exhibition in Verona. Special attention has been paid to reducing the noise levels of the machine and ensuring its long-term performance, says the manufacturer.
A selector switch enables the operator to choose the type of compaction required: circular blow pattern for 100 mm diameter specimen moulds or double concentric circles for 150 mm diameter moulds. The number of blows can be preset on the electronic, microprocessor-based control panel.
The unit is supplied complete with safety guard and safety micro-switch for CE compliance and is fully compliant with current EN, BS and ASTM standards.
Tecnotest will also be introducing customers to its recently launched variable speed testing machine, the T100/E02. With the ability to operate at speeds between 0.01 and 52mm per minute, the machine can be used for a range of testing including compression tests on soil-bituminous mixes; Marshall and indirect tensile tests on asphalt; flexural tests on concrete mortar, natural stones, clay blocks and tiles; and quick triaxial tests.
“There is nothing like this on the market,” said Matteo Dal Ben, road business unit product specialist for Controls who heads up the new centre. “It fills a gap between basic training and university courses.”
Controls has set up the new service in response to enquiries from customers in both the public and private sectors, according to Dal Ben. In particular countries such as Iraq and Dubai in the Middle East and emerging African countries such as Kenya and Tanzania are keen for this type of training.
“The aim is to help people to use the machines better, with a critical knowledge of testing and materials,” said Dal Ben. “It’s not just about how to operate the machines and which buttons to press.”
In many regions, trained and experienced people are in short supply, and this service aims to help laboratories upskill their employees and in turn provide a better service to their customers. For Controls it is also an opportunity to increase its presence in developing markets around the world.
Over the past four months, Controls has developed two modules, both of which are focussed on road paving, as this is the area where it receives most requests for training, according to Dal Ben. The first module provides an overview of the road structure: subgrade, sub-base and an introduction to hot mix asphalt. The second looks at hot mix asphalt, with a focus on Superpave specifications.
The courses will cover current practice, new developments and recent innovations in laboratory testing as well as other construction or pavement engineering topics relevant to the particular organisation. As well as training new recruits to the testing industry, Controls aims to help laboratory managers and technicians meet their Continuing Professional Development (CPD) commitments.
Each of the two-week modules will be a mix of theoretical and practical learning. Around a week will be spent in the classroom and a week in the laboratory, although Controls can adapt the training to suit the needs of the particular client.
Though Controls is able to run courses based round its own head office in Milan, it is more likely that it will be providing the training in its customers’ test laboratories. “This is likely to be a more cost-effective way of delivering training for most customers,” said Dal Ben, who estimates the cost of the teaching will be around US$700/module for each student.
Controls will be drawing on its in-house expertise from within its PAVELAB SYSTEMS division, set up to focus on road pavement testing equipment and techniques. Employees will bring experience gained in sitting on standards committees, setting up testing regimes and offering practical solutions in countries around the world. Professors Maurizio Crispino and Emanuele Toraldo from Politecnico Milano will also be involved in the face-to-face teaching of the courses, which will equip attendees with knowledge of the relevant major international specifications such as ASTM/AASHTO, BS and EN.
Dal Ben expects to deliver the first of the training courses overseas later this year. If the new academy is popular, Controls could develop further modules in the areas of concrete and soil testing. “I am very confident that this will be a success because people are asking for this service and no one else provides it,” he said. “We have had very good feedback so far, from both the lower and upper levels of ministries and large companies.”
Matest
Shear-box compactors have gained popularity over the past few years due to the fact that they can produce specimens that are more representative of those taken from roads. The shearing action of the shear-box compactor replicates field compaction in order to reproduce the properties of field-compacted asphalt in a laboratory.
“Nowadays, there is increasing concern about particle orientation in laboratory compacted hot mix asphalt specimens,” said Matest marketing director Paola Maestroni. “Although the gyratory compactor can produce cylindrical specimens that can be used for several tests, the particle orientation does not resemble a field compacted specimen, and this has resulted in great interest in alterative sample preparation techniques.”
In addition to the shear-box’s ability to produce specimens with more authentic particle orientation, it can also provide a measure of workability. This method also allows a wide range of samples to be produced – a 150mm by 450mm by 185mm piece can be cut into beams, slabs for Wheel Tracking or cored to produce cylinders for AMPT or other tests requiring cylinders.
Matests’s B039A ASC is fully automatic with a touch screen display. It has been designed for ease of use in entering test parameters, acquiring and processing data and generating test reports and data files, says Matest.
Roller compactors also produce specimens with a similar particle orientation to those produced in the field. Matest’s B039 Asphalt Roller Compactor (ARC), which it has recently updated, has several noteworthy features, according to the manufacturer.
Matest’s ARC has an electro-mechanical system, rather than requiring a compressor or hydraulic pressure. Matest was the first to do this, says Maestroni, with benefits including reduced noise compared to a hydraulic roller and elimination of the ‘bounce-back’ issues which used to affect pneumatic machines. The B039 ARC can also compact larger slabs than some competitor machines: 500mm by 400mm.
Another important feature of its ARC, according to Matest, is that a heated roller can be installed on the machine to help make the compacting process more similar to that on site. A vibrating action, sometimes required by researchers, can also be added to the compacting process.
A limitation with roller compactors is that they can only be used for thin slabs. “Once you go above a thickness of 75mm, the uniformity and air void distributions begin to suffer as the specimen becomes less homogeneous,” said Maestroni. “It cannot produce thick slabs that are representative of field compacted asphalt.”
This is where the shear- box compactor comes in as it can be used to produce much thicker specimens. “These machines must be considered as different but complementary,” said Maestroni. “Whilst both are excellent machines, it must be pointed out that they are ideally suited to different specimen geometries.”
Tecnotest
A selector switch enables the operator to choose the type of compaction required: circular blow pattern for 100 mm diameter specimen moulds or double concentric circles for 150 mm diameter moulds. The number of blows can be preset on the electronic, microprocessor-based control panel.
The unit is supplied complete with safety guard and safety micro-switch for CE compliance and is fully compliant with current EN, BS and ASTM standards.
Tecnotest will also be introducing customers to its recently launched variable speed testing machine, the T100/E02. With the ability to operate at speeds between 0.01 and 52mm per minute, the machine can be used for a range of testing including compression tests on soil-bituminous mixes; Marshall and indirect tensile tests on asphalt; flexural tests on concrete mortar, natural stones, clay blocks and tiles; and quick triaxial tests.