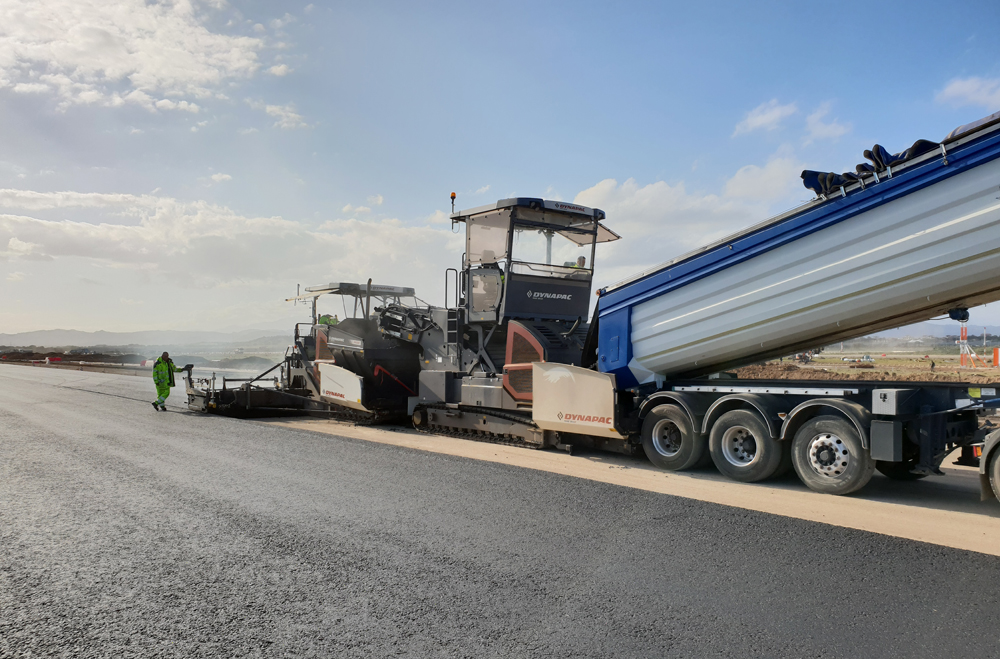
The Italian airport of Olbia on the Costa Smeralda is one of three international terminals on the island of Sardinia and counts the highest number of passengers arriving from abroad, especially during the summer months. The Costa Smeralda is a popular holiday destination in the north-east of Sardinia and the airport carries heavy traffic during peak vacation periods.
Between February and March 2020, Olbia airport was closed to air traffic for just over a month, for resurfacing work and the construction of a 300m runway extension, plus redevelopment of the passenger terminal and the aircraft parking stands.
Italian contractor Pavimental was awarded the package of works to upgrade the airport. Playing a key role in the work was Pavimental’s latest acquisition, an XPRESS 2500 asphalt plant. This fully mobile, self-erecting plant features a nominal production rate of 200tonnes/hour. This plant offers easy transport on wheels and offers solution for short-term sites and is said to be simple and speedy to erect.
The firm was able to improve the efficiency of its operation onsite by carrying out careful preparatory works in late 2019 before the airport was closed. During this period, the mobile Marini Xpress 2500 plant was commissioned onsite, so as to ensure a reliable supply of asphalt.
The old runway surface had to be removed and then the base structure also had to be broken out. This allowed the contractor to provide a redevelopment of the runway structure, allowing it to cope with larger, heavier aircraft. The structural work was important as the runway had not benefited from a major upgrade since its original construction in the 1970s.
Some 35,000tonnes of material was removed in a three day period, including 7,500m3 of the old concrete slab. And in all, 85,000m3 of material was removed from the site prior to the construction of the new runway structure.
Efficient plant
Gianluca Cangemi, the engineer in charge of the Pavimental site explained that the firm opted for the Marini XPRESS mobile plant because it would be able to produce the necessary asphalt quantities for the work, while also being mobile enough to be moved to other sites where Pavimental is also doing airport work. He said that the firm is carrying out airport work in Rome and Naples and has plans for other airport works also. For these jobs, as at Olbia, the quality of the output, the ability to use RAP and the mobility of the plant are key factors according to Cangemi.
The XPRESS 2500 batch plant was used alongside other plants in the area to meet the significant demands of supply, producing around a third of the 70,000tonnes of asphalt needed for the redevelopment, the paving and restructuring of the runway at the Costa Smeralda airport.
Configured for this job, the plant featured wheel-mounted aggregate cold feeders with five separate bins and a bag filter system with 663m2 of filter area. Meanwhile, the main components for the plant all fitted on one trailer unit.
Effective paving
Pavimental carried out the paving work using a fleet of machines from Dynapac. To ensure that the paving quality was optimised, the contractor used a material transfer vehicle (MTV) as a feeder, to deliver a consistent supply of mix to the paver. Using the MTV helped to ensure that the flow rate of material to the paver was more continuous, increasing paving quality. The mix quality also was more homogenous as a result, with less material and heat segregation for the mat.
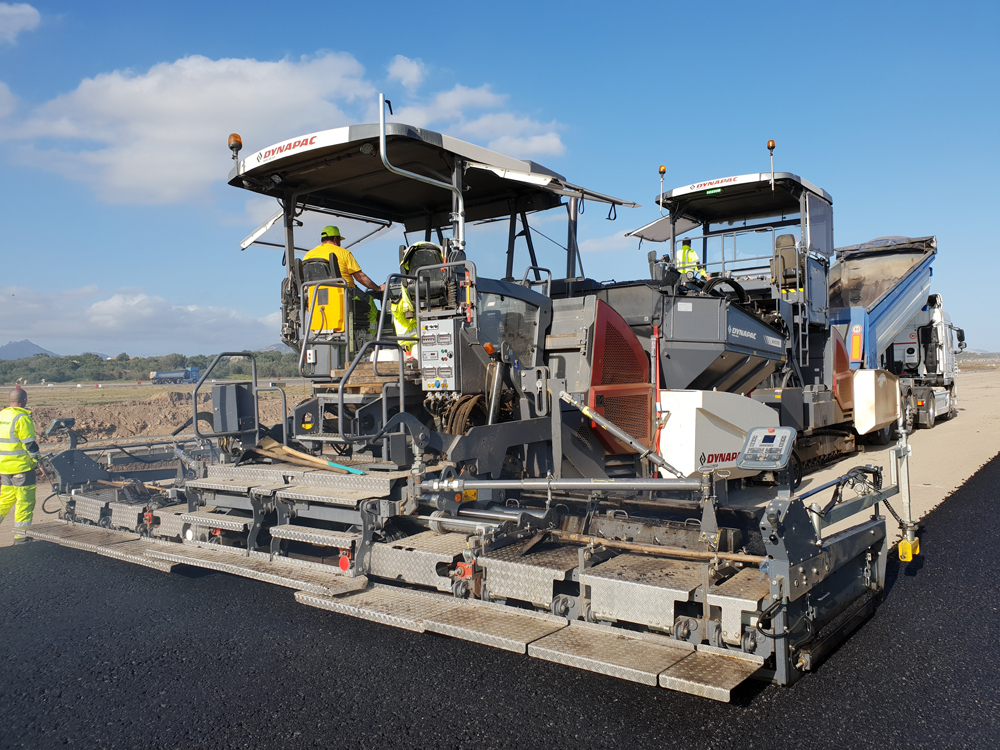
Using the MTV and the paver, the firm was able to improve the quality of the runway, as well as extending the taxiway so as to allow its use by a larger class of aircraft than previously.
The company laid new layers 950mm thick in the centre of the runway, with either cement or lime stabilisation used to suit the local conditions and provide a sound base structure. A 150mm asphalt base layer was placed on top, with an 80mm binder course and a 50mm wearing course on top. Polymer modified bitumen (PMB) was used for all three layers to optimise the mechanical properties of the material.
The firm used a fleet of 40 excavators for the breaking and earthmoving work, ranging from medium-large in size. These loaded a fleet of 58 trucks of various types. Three stabilisers were also used, along with the associated machines and trucks to supply material.
Five Dynapac SD2550CS asphalt pavers carried out the finishing work, in addition to two Dynapac MF2500CS MTVs. Using the MTVs meant that two pavers could operate in echelon for the central section of the runway, ensuring a high-quality hot-to-hot joint. Using the pavers coupled with the MTVs and 13 trucks supplying material allowed 400tonnes/hour of asphalt to be laid. Once the old runway surface and base had been removed, the firm placed a 950mm thick layer of granular base material in the centre of the runway, reducing to 680mm in the lateral areas.
The first stage of the work had to be carried out in a 45-day slot but by using the latest equipment and sophisticated methods, Pavimental was able to reduce the construction time to 40 days. During this time the firm was even able to carry out 115m of the required taxiway extension work.
The contractor also used this opportunity to improve the drainage system, laying around 6km of piping, 6km of new concrete channels for drainage and the latest LED systems. The majority of aircraft land close to the centre of the runway, which is why the focus was on optimising the quality of this stretch of the surface. The firm has refurbished the runway design across a 60m width, with the 20m central section being designed to be the primary load-bearing structure, along with 12.5m adjoining strips on either side, as well as dual 7.5m-wide anti-dust strips.