Ferocious daytime temperatures can provide a tough challenge to construction firms working in desert conditions in Egypt's south. Despite the high daytime temperatures however, Egyptian contractor Orascom has managed to complete an airport project on budget and ahead of schedule, while meeting the client's tight specifications.
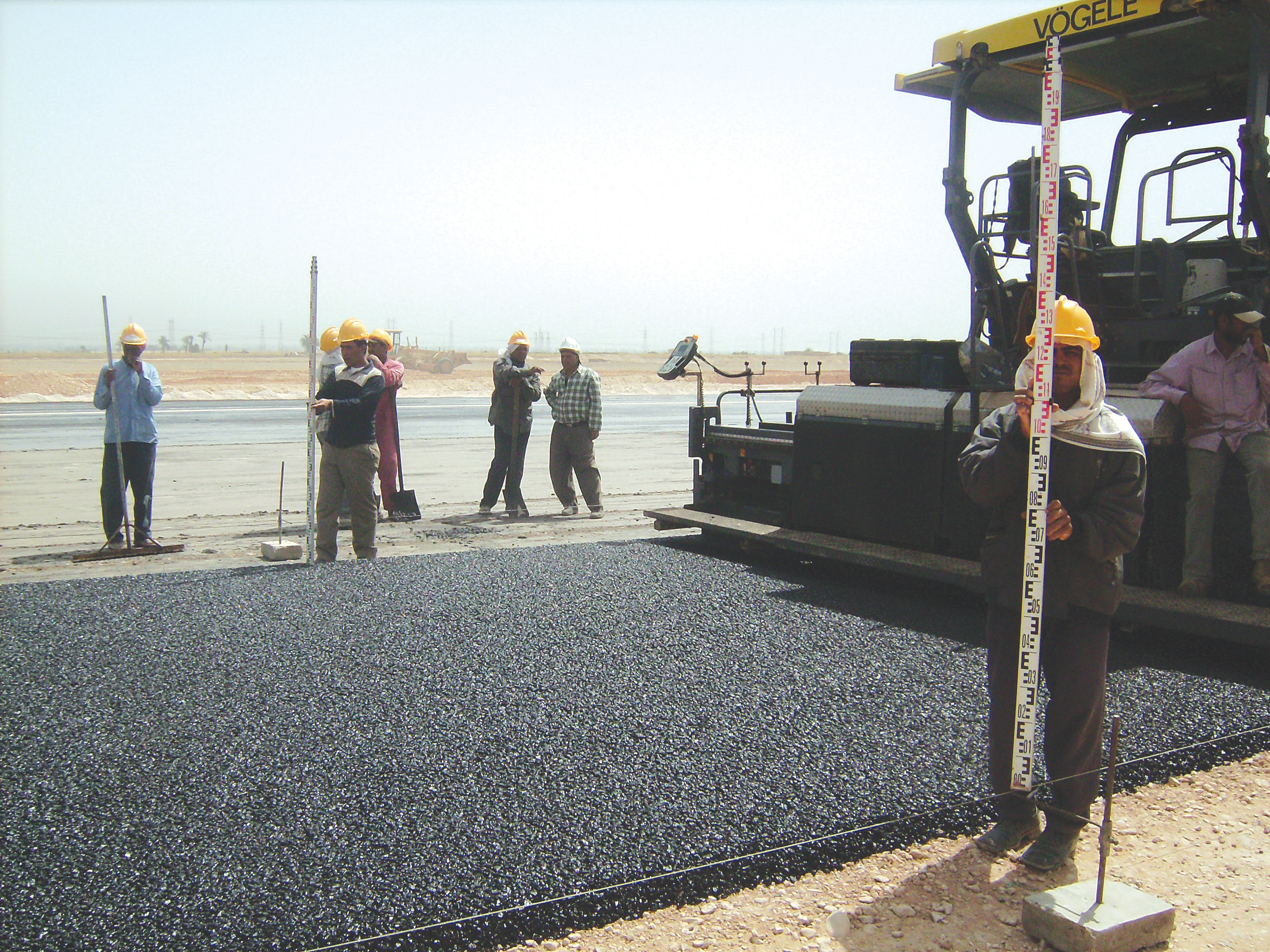
For the asphalt paving duties at the airport Orascom used two Vögele Super 1800-2 finishers working together
Ferocious daytime temperatures can provide a tough challenge to construction firms working in desert conditions in Egypt's south. Despite the high daytime temperatures however, Egyptian contractor 2414 Orascom has managed to complete an airport project on budget and ahead of schedule, while meeting the client's tight specifications. The firm has just completed the project to revamp Suhag Airport in the south of the country. This airport now features a new runway, taxiways and aircraft hard standing, as well as new perimeter and access roads. Orascom carried out all of this work for its client, the Egyptian Army, which will operate the facility as a joint civil/military airport.
Because the operation has employed an all new fleet of machines combined with the latest construction techniques and tight control of specifications, both structural and finish quality are high. According to one of the project team at Orascom, "This is one of the best runways in Egypt." The one year project to rebuild the runway started at the end of 2008 and took one year to complete, with the perimeter road, taxiways and concrete hard standing having all just been completed in May of this year.
In all Orascom says it paved around 34km of roads at the site, including the perimeter road around the airport. The runway itself measures 3km long by 70m wide while there are three taxiways of 400m each and two concrete aircraft parking aprons measuring 37,900m2 for military aircraft and 40,000m2 for civil aircraft.
The runway features three layers of asphalt, a wearing course, binder course and base course. Under this are two layers of compacted soil and aggregates, built to tight specifications to meet Egyptian requirements and regulations. The aircraft parking areas are made of high quality concrete and were laid in two layers, each 150mm thick and with a 700mm structure of earth and aggregate underneath. After laying the concrete was cut with slots every 5m and these were then filled with sealant.
In all nine178 Caterpillar 14M graders were employed to lay out the site and also carry out the majority of the earthmoving duties. Egyptian practice is to make extensive use of graders for earthmoving, so these were key prduction tools. For the surfacing two Vögele Super 1800-2 pavers were used to lay the asphalt while the concrete paving for the aircraft parking areas was carried out with a 2395 Wirtgen SP1500.
In addition, 14 single drum soil rollers and twin drum asphalt rollers of various makes were used for compaction of the earth and asphalt surfaces. A273 Marini Ultima batching plant able to deliver 120tonnes/hour produced the asphalt used on the runway and roadways around the airport, with the high specification concrete coming from an outside supplier.
Because the asphalt and concrete paving work had to be carried out to high specifications, total stations were used to monitor progress throughout and a tolerance of +/- 2mm was allowed on the concrete surface for instance. The concrete paving job was only carried out at night to save the crew from working with the material during the fierce daytime temperatures that can hit peaks of 45ºC.
Orascom had to build five concrete culverts along the length of the runway as well as two for each of the taxiways although these are all for electrical cabling rather than drainage, as rainfall in these desert conditions is a rare event. The new airport is now open to traffic and also benefits from a brand new control tower and terminal building, as well as other new facilities.
Because the operation has employed an all new fleet of machines combined with the latest construction techniques and tight control of specifications, both structural and finish quality are high. According to one of the project team at Orascom, "This is one of the best runways in Egypt." The one year project to rebuild the runway started at the end of 2008 and took one year to complete, with the perimeter road, taxiways and concrete hard standing having all just been completed in May of this year.
In all Orascom says it paved around 34km of roads at the site, including the perimeter road around the airport. The runway itself measures 3km long by 70m wide while there are three taxiways of 400m each and two concrete aircraft parking aprons measuring 37,900m2 for military aircraft and 40,000m2 for civil aircraft.
The runway features three layers of asphalt, a wearing course, binder course and base course. Under this are two layers of compacted soil and aggregates, built to tight specifications to meet Egyptian requirements and regulations. The aircraft parking areas are made of high quality concrete and were laid in two layers, each 150mm thick and with a 700mm structure of earth and aggregate underneath. After laying the concrete was cut with slots every 5m and these were then filled with sealant.
In all nine
In addition, 14 single drum soil rollers and twin drum asphalt rollers of various makes were used for compaction of the earth and asphalt surfaces. A
Because the asphalt and concrete paving work had to be carried out to high specifications, total stations were used to monitor progress throughout and a tolerance of +/- 2mm was allowed on the concrete surface for instance. The concrete paving job was only carried out at night to save the crew from working with the material during the fierce daytime temperatures that can hit peaks of 45ºC.
Orascom had to build five concrete culverts along the length of the runway as well as two for each of the taxiways although these are all for electrical cabling rather than drainage, as rainfall in these desert conditions is a rare event. The new airport is now open to traffic and also benefits from a brand new control tower and terminal building, as well as other new facilities.