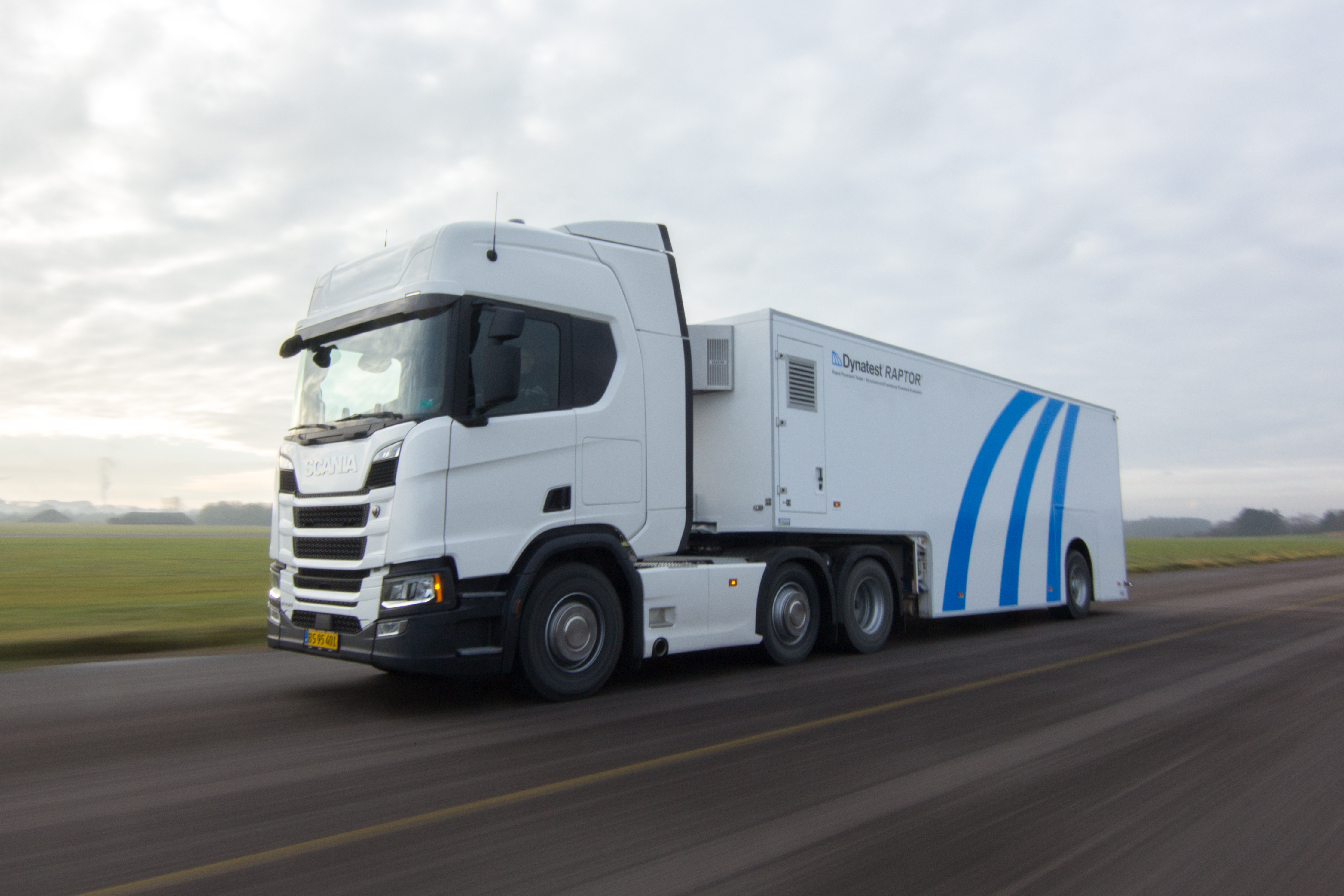
“People have been wanting to do this for years,” said Jack Larsen, Dynatest’s R&D manager. “Many research groups have tried but they have never come up with a good and accurate solution that can compete with the falling weight deflectometer.”
The falling weight deflectometer (FWD) is a tried and trusted way to measure the bearing capacity of a pavement. However, it requires the testing vehicle to stop at every measurement point which means traffic management or even road closures.
Whereas FWDs use seismic sensors which must be touching the road surface before the falling load is deployed, the Raptor uses a laser-based system. Information from a combination of line laser profilers and an integrated digital camera is used to create a topographic image of the road’s surface. As well as measuring bearing capacity, the Raptor system can plot the positions of potholes, cracks and rutting.
The laser line profilers, spread along a stiff beam, provide images at a rate of 4000Hz, giving 1,280 data points for a 150mm-wide section of road. “It gives us a vast amount of data. And the more data you have, the higher the accuracy,” said Larsen.
The Raptor is contained in a semi-trailer, 9.5m long by 2.5m wide by 3.35m high, which can be pulled by a standard truck. “Previously this type of technology has needed large vehicles but we wanted to optimise the size so that it can be useful on smaller roads. This is around the size of a bus so it should be able to go into most cities,” said Larsen. “We hope that organisations which have never used this technology before, like smaller municipalities, will now use this to survey their networks.”
Along the way, Dynatest has developed and patented new technology, for example a way of correlating the topographic images from the different sensors. It has also created a patented calibration technique which involves running the sensor over a long beam with a surface that mimics that of a road.
“If you have to correlate the information from different sensors, you need to know how they are placed and aligned in relation to one another, which isn’t an easy thing to do,” explained Larsen. Dynatest’s system allows calibration in just 15 minutes, which means it can be done frequently, improving the accuracy of the data, says Larsen. To date, Dynatest has trialled the Raptor on around 100km of road around its head office in Copenhagen, comparing the results to FWD measurements and achieving good correlation.
Rather than selling the Raptor to would-be users, Dynatest is offering a road-mapping service. Eventually, it plans to have Raptors based in all the major regions, starting with the US and Europe.
“Making an investment in such an expensive piece of equipment could be too much for a road authority or research organisation,” said Larsen. “This also allows Dynatest to apply its huge experience of pavement consulting to the analysis of the results.”
Dynatest already has potential orders on its desk from road directorates in the US, Europe and the Middle East. In June, the company will be embarking on a tour of Europe where it will be offering local demonstration surveys on 100 - 200km of any type of road for a flat fee of €10,000.
Meanwhile development of the product continues. The Raptor has been designed to run at 80kph (50mph). The Technical University of Denmark is currently modelling responses at different driving speeds so that it can be used at slower driving speeds in built-up urban areas.
A Norwegian company, Elop, has developed a hand-held rolling ultrasound scanner for surveying concrete structures such as bridges and retaining walls. The scanner can ‘see’ the position of reinforcing bars and defects such as air pockets, cracks or delamination and display them in 3D format on a screen in real time.
“There are big advantages in having a rolling system,” said Elop CEO Philippe Olivier. “You can put several together to cover a larger area, or you could connect them to a root to scan large or remote parts of a structure, such as a dam.”
Current methods of non-destructive testing for concrete using ultrasound involve stationary measurements and require post-analysis to get results. Other rolling scanners use ground penetrating radar which are good for detecting rebar, but not so good for defects, according to Olivier.
Elop was set up in 2013 with the aim of producing this device and has received funding first from the Norwegian Research Council and more latterly from the EU Horizon 2020 fund. The company has carried out a field test with engineering company
The challenges of ageing
Researchers at the National Centre for Asphalt Technology (NCAT) in the US are trying to find ways to better mimic the effect of long-term ageing on asphalt.
AASHTO R30, Standard Practice for Mixture Conditioning of Hot Mix Asphalt, is the commonly-used standard for both short-term and long-term ageing. Short-term ageing, which takes place during plant production and construction, is simulated by conditioning loose mix at the compaction temperature for two hours, or at 135°C for four hours. The long-term ageing protocol calls for a compacted specimen to be aged for five days at 85°C.
While a number of research projects have shown that AASHTO R30’s protocol for short-term ageing adequately simulates real life, that isn’t the case for the long-term ageing method.
For long-term ageing, an ongoing NCHRP project, 9-54, recommends loose ageing a mix at 95°C for a period that is governed by climate, depth of asphalt in the pavement and years of service. Surface layers that are four years old would require three to five days for most of the US.However, the length of time these ageing procedures take makes them impractical, according to NCAT researcher Racquel Moraes. NCAT, working with the University of Illinois Urbana-Champaign and MTE Services have devised a test that involves ageing loose mix at 135°C for between eight and 24 hours.
Moraes suggests that other methods could be used for accelerated pavement testing to simulate cyclic actions of thermal oxidation, ultraviolet radiation, moisture infiltration and diffusion. However, the limit of this approach is that it requires special equipment.
www.ncat.us
One of the innovative technologies that Elop has developed as part of the scanner is a broadband transducer which makes it possible to adjust the frequency of the ultrasound according to the type of concrete under investigation. “For concrete, you are normally working at a low frequency, say 100kHz, but depending on the type of aggregate and other factors you might need to go lower,” says Olivier.
Elop is currently refining elements of the scanning system in preparation for selling it. Improvements needed include its weight: the prototype weighs around 8-9kg, whereas the goal is to produce a scanner that weighs less than 5kg. Elop also hopes to develop the display so that different materials – aggregate, steel and water – are represented by different colours.