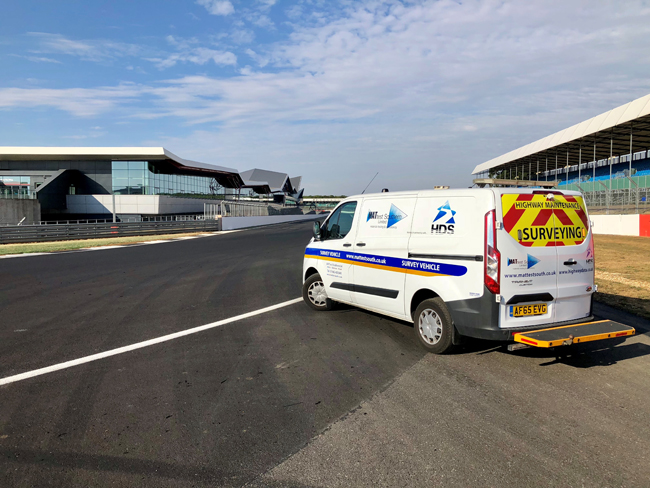
Automated testing is improving safety during paving and saving on testing costs. But it could also help reduce long-term maintenance costs too - Kristina Smith writes
Testing pavements as they are laid can be a hazardous activity. The technician may be on their hands and knees, far behind the main gang, or reaching inside the hopper to measure the temperature of the hot mix or dodging rollers to take density readings.
Ruari Charlseworth, development manager at
That does not need to be the case any longer. MATtest has developed a system that removes the need for human testers, by automating the measurement and collection of data, and then processing to create reports and visual records in 2D and 3D. It’s called Automated Quality Assurance (AQA).
Three major UK contractors are already using the system, with MATtest Southern hoping to sign up a further two in the coming year. “It feels like we are at a bit of a tipping point,” said Charlseworth. “Most of the main contractors are running trials.”
MATtest has also been working on a collaborative research project with national road authority Highways England and consultant Aecom to look at updating testing standards to include non-human forms of testing. In line with UK government policy, Highways England is keen for its supply chain to move to digital ways of working.
AQA takes a variety of data from a host of sensors and measuring devices lined to the asphalt trucks, the paver, the intelligent roller gathered at the time of laying and compaction. Data from automated laser surveys, carried out on specialist vehicles, developed by MATtest and the University of Hertfordshire, are also fed into AQA.
For the macrotexture measurements, a 2D blue laser records the mean profile depth of the road while surface regularity is measured using a high-speed red laser and Doppler System. Data from the laser surveys is combined with GPS coordinates, a digital encoder and HD video to produce 2D and 3D digital reports.
MATtest has also created automated reporting for presenting the data. Currently reports mimic those created by traditional means, comprising lane records, compaction records, rolling straight edge record and a texture record.
As well as producing more complete measurements records – covering the entire pavement area rather than at discreet points – AQA costs less. MATtest charges a day rate for providing the testing and data management services which comes in at 10% lower than the traditional service.
Though it has yet to happen, Charlseworth believes that the data AQA collects and processes will prove useful for the maintenance and repair of road surfaces once they are in use. “Asset management systems look at deterioration, with the first test data usually taken around six months after the road is built,” said. “Our data could give a more accurate point zero for the deterioration curve.
“Because we do automated quality assurance from the subgrade to the surface layer, we could give a huge amount more data which should lead to better allocation of resources in the future to the areas that need it.”
Learning curve
MATtest started working on new forms of pavement testing six years ago. “We wanted to develop more innovative ways to do materials testing,” said Charlesworth.
The first version of AQA was used by Tarmac in Norfolk five years ago. At that time, MATtest built all the measurement devices – such as the GPS tracker and infra-red sensor – itself.
Today, MATtest buys the hardware from MOBA. “It means that we get a warranty and that we benefit from the development work that they do on the hardware,” said Charlesworth.
Initially, MATtest used a system called APEX for tracking the asphalt trucks from a Dutch company called ThunderBuild. More recently, it has developed its own system for recording deliveries, e-load, because the main contractors had invested in their own tracking systems – such as ePOD by PODFather and Teletrac Navman – which overlapped in functionality with APEX.
As well as Tarmac, which uses the system on contracts for Norfolk County Council and Cambridge County Council, MATtest has an eight-system contract with Aggregate Industries which is committed to using AQA on its work for Highways England on the Strategic Road Network. Eurovia has just completed a trial in Hertfordshire on the A505 Offley bypass near Hitchin. MATtest’s aim in providing the testing service is to go beyond the numbers to provide analysis and context, said Charlseworth. “Contractors have bought the hardware themselves, but they run up against the problem that they don’t have the internal expertise to understand and manage the data,” he said. “There’s also the requirement to have third-party assurance, which we provide.”
Customers will also benefit from the fact that MATtest works hard to keep up-to-date with new technologies and opportunities. “We take on the responsibility for capturing new products as they come onto the market,” said Charlseworth.
At the moment MATtest is working with MOBA to fine tune the data presentation for a new MOBA system for measuring thickness. And it is developing a data visualisation tool, so that contractors can ‘see’ data in 3D without having to invest in full BIM software packages.
Although it is concentrating for the time being on its home market, MATtest hopes to offer its services overseas in the future. The first step could be a short one to Ireland with the Middle East also on the hit list.