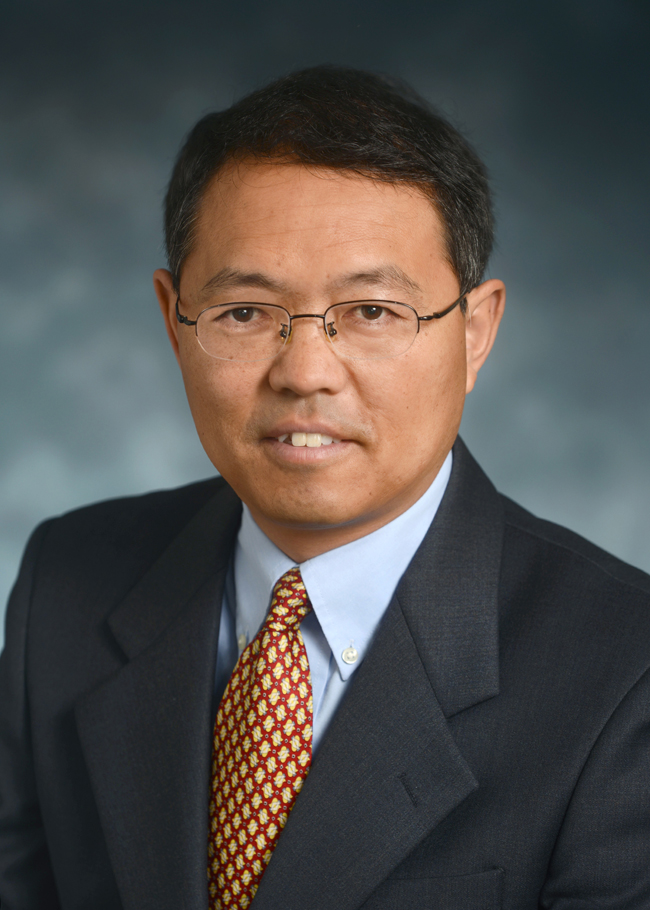
Researchers at the Texas A&M Transportation Institute (TTI) have developed new tests for cracking and rutting, designed to be quick and easy to carry out, using existing laboratory equipment. The most advanced of these is the IDEAL Cracking Test (IDEAL-CT), which could be appearing in specifications in some of the US states in around six months’ time.
“Cracking is a huge problem in the US,” said Fujie Zhou, research engineer at Texas A&M Transportation Institute, an expert in this field who is leading the development of both tests. “Every Department of Transportation is looking for a simple, practical cracking test for use during mix design, quality control and quality assurance.”
The tests have been developed under one of three Innovations Deserving Exploratory Analysis (IDEA) projects managed by the
The most commonly used cracking tests in the US are the Texas Overlay Tests and the Illinois Flexibility Index Test. Both are good tests, according to Zhou, but they each require significant preparation of the specimens before testing, involving notching and – in the case of the Texas Overlay Test specimen – gluing too.
“Based on my experience, the more steps you include in sample preparation, the more potential human error you introduce,” said Zhou, who has been working on cracking-related issues for the last 20 years.
THe IDEAL-CT simply requires a disc-shaped specimen to be moulded, 150mm in diameter and 62mm thick (which is the same size as the specimen required for the Hamburg wheel tracking test). No notching or gluing is required, and the specimen can be tested in a standard indirect tensile strength testing machine.
“We use exactly the same machine, the same test, even the same loading speed,” said Zhou. “The only thing we do differently is use a new way of looking at the data.”
The IDEAL-CT produces a fraction mechanics-based parameter called the Cracking Tolerance Index (CT Index). The larger the CT Index, the better the cracking resistance for the mix.
Most laboratories will have an indirect tensile strength testing machine and, even if they had to buy it new, the cost would be less than $10,000, according to Zhou. This compares to specialised equipment which would cost around $50,000.
Laboratories may need to buy an accessory because the calculation of the CT Index requires that the whole load versus displacement curve be recorded, rather than just the maximum load which is normal for that machine. But this would cost less than $3,500, said Zhou. Alternatively, the load-displacement readings could be recorded manually.
The test has been shown to have good correlation with the existing cracking tests and also with field cracking performance data collected from a number of sources. Independent testing at the National Centre for Asphalt Technology (NCAT) Test Track also verified its correlation with in-field performance. The researchers at TTI ran tests to check its sensitivity to the type of binder used, binder content, RAP proportions and ageing and report that the test is sensitive to these different conditions.
The Coefficient of Variation (COV) for the IDEAL-CT is less than 20%. Although this sounds high, it is actually low, explainED Zhou: “In civil engineering, a COV of less than 20% is pretty good,” he SAID. “When you are producing asphalt mixes, we are talking in tonnes not milligrammes, it’s not like chemistry. Cracking is a localised facture which means that the cracking test is much more variable than other tests such as stiffness or rutting resistance.”
Six DOTs have committed to an implementation programme for the test: Texas, Oklahoma, Virginia, Kentucky, Minnesota and Main. Texas DOT is already planning to use the IDEAL Cracking Test for quality control and Virginia has said that it will specify it for all mixes. Georgia is doing laboratory studies on the test, says Zhou.
TTI published a final report on the new testing method in January this year and there is a draft ASTM standard currently under review.
IDEAL Rutting Test
Having spent two years developing the IDEAL Cracking Test, Zhou and his colleagues have now moved on to create the IDEAL Rutting Test (IDEAL-RT). This can be carried out using a new shear rutting fixture which works with a regular loading frame such as an MTS, UTM or indirect tensile tester.
Currently-used rutting tests, the Hamburg wheel tracking test and the asphalt pavement analyser (APA) require long testing hours and therefore have not often been used for quality assurance and quality control. The new rutting test uses the same sized disc as the cracking test and proposes that the shear strength of the specimen be used as the rutting parameter; the larger the shear strength, the better the rutting resistance of the mix.
Details of the test were due to be published in the Journal of the Association of Asphalt Paving Technologists (AAPT) in March 2019. It shows very good repeatability, explained Zhou, with a COV of 5% and is sensitive to variations in binder properties content, RAP content and ageing.
The goal in developing these two tests is to be able to achieve Balanced Mix Design, a concept which was developed by TTI over a decade ago. This requires mixes to have good resistance to both rutting and cracking, rather than withstand one at the expense of the other.
Zhou hopes that his work can have far-reaching benefit. “If people can use the tests, and everyone benefits from them, I would be very happy,” he said. “The goal is to help contractors build better roads that last longer and that means that every tax payer will benefit.”