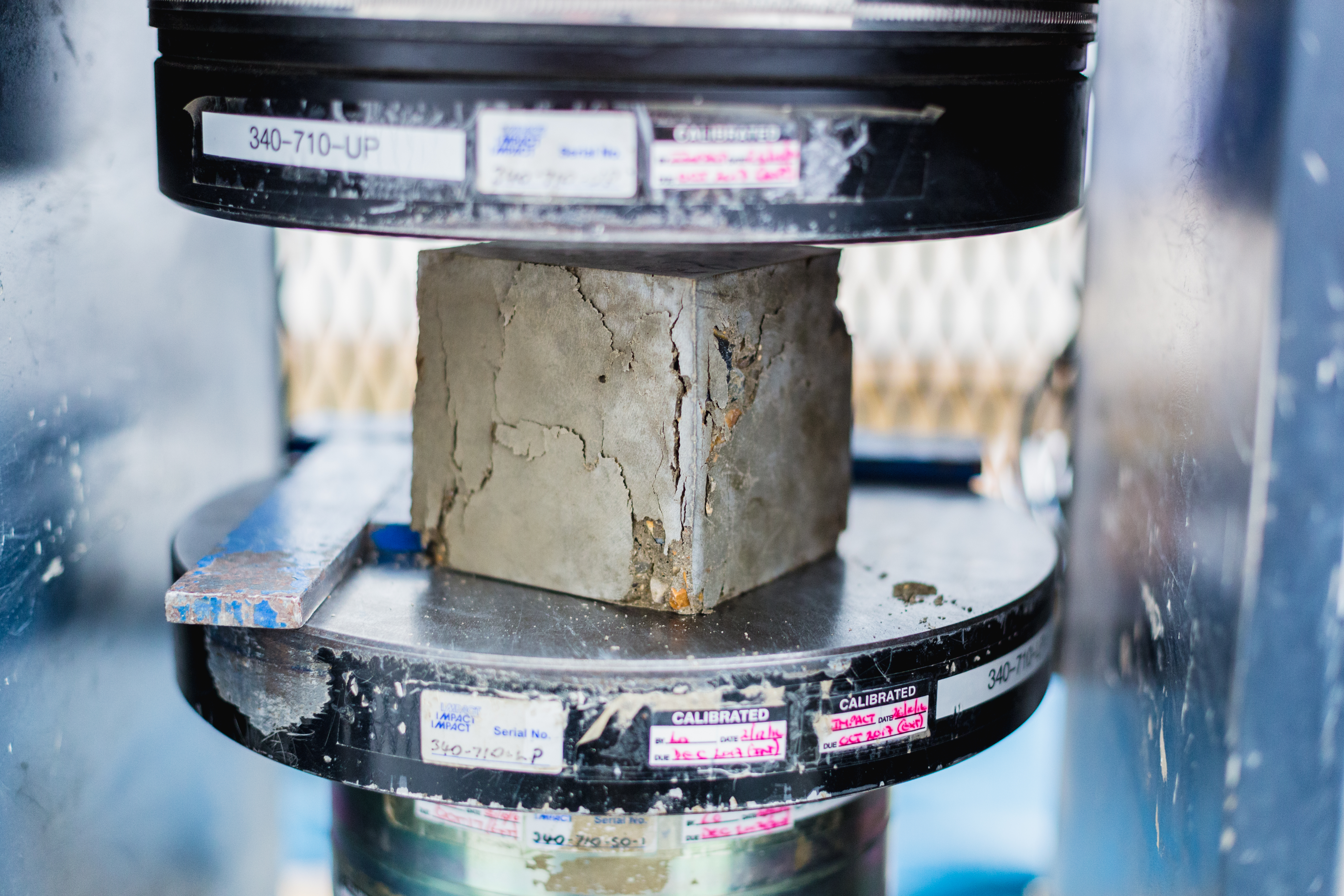
The CET Group has ambitious plans. Over the next four years it wants to double the size of its business, which in the last year turned over £27 million. “There’s a lot of positivity out there,” said Gary Corrigan, managing director of the group’s infrastructure division. “The next five years are going to be very busy.”
The group has six materials testing laboratories, the newest of which is at Colnbrook, near Heathrow. “Heathrow is important to us: we do a lot of work inside the airport for the contractors and some of it is very reactive,” said Corrigan. “Our Heathrow lab gives us the ability to service not only the airport but the Home Counties and down to the West Country.”
At the end of 2016 the UK Government announced a £500 billion pipeline of infrastructure projects, £300 billion of which it projected would be spent before 2021. Of that £300 billion, £91.9 billion is allocated to transport, £12.7 billion of which is for roads.
CET has recently delivered a series of contracts connected to
Other major infrastructure projects also require roads to be surveyed and tested. For example, CET has been carrying out surveys to calculate the residual life expectancy for some of the roads that will be used to carry trucks related to the construction of the HS2 high-speed rail line.
30 years of testing
CET Group has two main strings to its bow: materials testing for infrastructure and insurance-related services such as subsidence investigations and 24/7 emergency home response. It started life as NDT Flexitec in the late 1980s, growing organically and by acquisition, most recently with the purchase of Omega Calibration and Construction Testing Solutions (CTS) in 2016.
Having invested over £150,000 in its new Colnbrook laboratory and with UKAS accreditation granted in August, Corrigan says that CET will be offering clients the full range of testing services, particularly concrete and earthworks. There are two testing machines in the new laboratory: a compression machine and a beam test machine, both supplied by Impact Test Equipment, which is based in Stevenston in Scotland.
The investment also includes spending on training. Some of the 15 technicians are experienced, drawn from CET’s Harrietsham laboratory in Kent or from general recruitment within the industry, while others are new to the sector.
Corrigan, who began working for the company in 1991 as a senior technician, says that there have been few changes in the way that contractors engage with test houses. “We have to be very reactive, as do our customers the contractors, and that’s something that hasn’t changed over the years,” said Corrigan. “Testing can be required at short notice and we have built the company with that flexible approach.”
The biggest change for CET – and some of its competitors – is a move from paper to cloud. “Twenty years ago, everybody was saying we would be paperless in five years but it never really happened – until now,” said Corrigan.
CET spent two years and nearly £200,000 developing its CETi system which it launched a year ago.
With CETi, technicians input data via tablet on site. Once checked, the data goes straight onto the system, with customers alerted that the information is available on the portal.
“The client can get the report sometimes within minutes of finishing the test,” said Corrigan. “We aim to get our reports issued the same day, which is a huge departure from the way it has happened in the past.”
Corrigan said that CETi differs from what others offer because the whole cycle from quotation through to invoice is stored on the system – with clients able to access archived results and other information long-term. “It means that everything is clear and transparent,” said Corrigan.
CETi also allows for information to be summarised and presented in a more accessible way. This enables customers to use the data for trend analysis and other analytics more easily.
Corrigan believes that CET could offer more value to its customers – who are predominantly contractors – if it were involved earlier in a project’s life cycle. “We have a vast amount of experience in this business and if we know what our customers are looking for, we can help and guide them. We can suggest solutions that are more efficient and more cost-effective.”
Lightweight diamond core trailer takes off
Launched three years ago, Xcalibre Equipment’s T4D hydraulically-driven diamond drilling trailer is proving popular around the world. To date, Xcalibre has sold around 50 of the machines to customers in Europe, North America, Australia and the Middle East.
“It’s smaller and lighter than many of our competitors’ products and it’s also controlled by a remote handset which we believe is a safer way of doing things,” says Xcalibre’s Roland Knott.
Xcalibre has been manufacturing diamond coring trailers for nearly 30 years. The drilling trailers are used to take samples from newly laid roads, from existing roads and on airports to create fixing holes for lighting systems.
The T4D, which can drill cores of up to 350mm (13.5 inches) in diameter, also benefits from Xcalibre’s proportional feed control. “When you are drilling into concrete or asphalt, you need to exert the right amount of force on the drill,” explains Knott. “The proportional control allows the machine to optimise the feed pressure.” Xcalibre says that the machine can reduce drilling times by up to 75% when compared to hand-fed machines.
The weight of the unit makes it attractive to customers: because it is below 750kg it is not subject to certain licensing restrictions that may apply, particularly in Europe; and it is also light enough to be manoeuvred and operated by one person.
The T4D is powered by a
Founded in 1987, Xcalibre is based in Coventry, UK, and designs and manufactures a range of specialist diamond drilling equipment for civil and marine environments.
Photonics reveals behaviour of modern concretes
Concrete isn’t what it used to be. Adding fibres, cementitious materials and even particles made from plastic waste is creating new forms of concrete which behave in different ways. Researchers from the Universities of Leeds and Qatar have been working on a project which uses photonics – or optical measurement – to look at the fracture toughness of new forms of composite concretes.
The researchers coated a variety of concrete beams in a birefringent epoxy coating. Birefringent means that the coating can split light waves in different directions, depending on how much stress is acting at that point. A photonic camera then takes a picture which reveals where the stress levels are greatest, before a crack occurs.
Dr Joseph Antony from the School of Chemical and Process Engineering, who led the study, said: “There are other methods to measure stress and strain levels in the engineering sector, but we do not believe any of them can measure shear strain directly with high precision, which is most relevant to assess the failure strength of materials.
“The photonic method we developed can directly measure shear strain, even on opaque materials. Until now, photonic and optical methods of measurement have only been associated with transparent materials.”
Funded by the Qatar National Research Fund, the aim of the study was to find a way of using waste materials to create new composite concretes. Seven mixes were tested, containing steel fibre, fly ash, silica fume, virgin and recycled low density polyethylene (LDPE) and high density polyethylene (HDPE). The LDPE and HDPE was in the form of spherical balls, around 3mm in diameter.
Dr Antony says that the concrete made with the waste polyethylene performed better than traditional concrete, and that the results from the new photonic testing method correlated with conventional methods. And he believes the new method of photonic fracture testing could be useful in other engineering applications including materials, civil, mechanical, electronics and chemical.