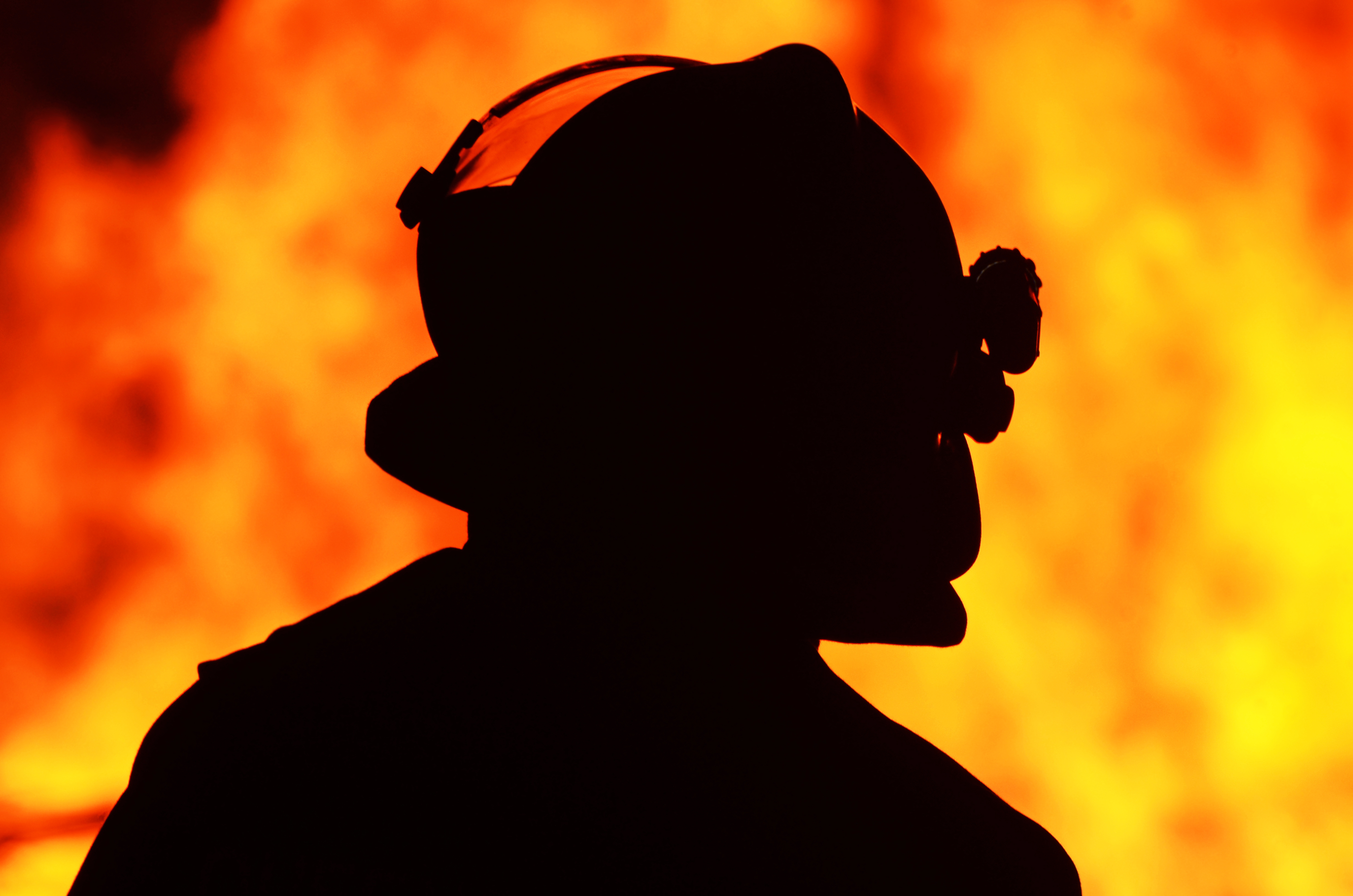
New methods of non-destructive testing for concrete roads and structures offer great hopes for damage assessment and maintenance planning - Kristina Smith looks at two emerging applications, one using lasers, the other ultrasonics
How best is it possible to assess the state of concrete in a road pavement, bridge deck or tunnel wall? One of the most reliable ways is to take a core of concrete from the structure to analyse and test in the laboratory.
One downside to this method is that doing the test creates weak points in the structure that must then be repaired. Another is that the frequency of such cores cannot be too great – so it is possible that some problem areas will be missed.
New technologies from the world of geospatial engineering promise a future where structures can simply be scanned and assessed. It is early days yet but the benefits could be huge. As well as assessing concrete which has deteriorated or been damaged, these methods will allow more effective maintenance planning so that sections of road that need repairing can be targeted before they fail.
Laser scanning to assess concrete damage
When researchers from the
It turned out that the patch in question, though it looked no different to the human eye, was a younger piece of glass, installed to repair a damaged section. Now researchers are trying to use the same effect to work out how the characteristics of concrete have changed, for example if they have been subjected to fire or corrosion due to salts.
“We have been looking at the reflectivity of the concrete and showing that samples that have been subjected to different temperatures, for example, have different characteristics,” explained Gethin Roberts, reader in geospatial engineering at the University of Nottingham. The next steps will be to equate the characteristics to concrete strength.
Should this method be perfected, it will have many benefits over current means of testing which involve taking cores from structures. Using laser scanners means that an almost infinite number of points can be tested, there is no need to create further weak points by coring, and it can also be done at a distance, meaning that people don’t have to approach potentially dangerous structures.
A recent research project, carried out by Roberts with PhD student Wallace Mukupa and Craig Hancock, assistant professor of geospatial engineering , who are both based at the University’s campus in Ningbo, China, looked at fire-damaged concrete. Specimens were heated to various temperatures up to 1,000°C in a furnace and scanned before and after heating. Although concrete does have a good resistance to fire, it does exhibit significant losses of strength when heated above 300°C.
The researchers used two makes of two-phase shift terrestrial laser, a
“A comparative analysis of the laser intensity for heated and unheated concrete showed that the recorded intensity values for heated concrete are higher than those of unheated concrete. In fact, the laser intensity values of heated concrete showed a remarkable increase in the concrete exposure temperatures from 250°C to 1,000°C,” says Wallace Mukupa.
The next step will be to work out the correlation between the reflectivity of the concrete surface and the strength of the concrete. “We have taken some of the concrete specimens and done some strength tests on them to see how that relates to the scan results,” says Roberts. “To move forward we need to work with civil engineering and structures experts to help us understand the characteristics of what we are measuring.”
Ultrasonic pinpoints weaknesses in concrete roads
A research project which aimed to investigate the correlation between the thickness of concrete pavements and their performance made another interesting discovery: ultrasonic shear wave velocity testing can identify changes in the structure of a road, and hence areas where distress could be greater in the future.
Researchers at the
Although it is believed that thicker concrete pavements last longer, there isn’t much data to back this up. “One big reason for the lack of data on the relationship between concrete pavement thickness and performance is the destructive nature of these measurements,” said Lev Khazanovich, a former professor in the University of Minnesota’s Department of Civil, Environmental, and Geo- Engineering. “Concrete thickness is typically assessed by coring - a destructive, expensive, and time-consuming test that only offers widely spaced measurements of thickness.”
Using ultrasonic shear wave tomography devices, commonly known as MIRAs, the researchers measured both thickness of pavement and shear wave velocity (SWV) at the slab surface, as this is an indicator of material properties that can be linked to its strength. They also recorded visual signs of distress.
The surveys took place on sections of Highway 100 and Interstate 394, and on two sections of Highway 60 with over 8000 measurements taken. “We found that both pavement thickness and stress measurements are highly variable, with a half-inch of variation in thickness about every 10 feet (3.05m),” said Khazanovich. “Interestingly, three of the four surveys averaged less than design thickness, which is contrary to typical accounts of contractors building slightly thicker slabs in order to avoid compensation deductions.”
Observation and analysis demonstrated that thicker pavements did not mean better pavement performance: some areas where the pavement was thick showed high levels of distress such as spalling and cracking. The researchers did find some trends related to transverse thickness in one of the roads but overall they reported that the findings in relation to thickness versus performance were ‘inconclusive’.
SWV did prove to be effective in identifying changes in construction. “A drop in the shear wave velocity strength measurement corresponded to an increase in observable pavement distresses such as cracking and crumbling,” Khazanovich said. “This was especially apparent when we were able to easily identify locations of construction changes, where significant changes in shear wave velocity matched up with observable distress.”