The efficiency of asphalt compaction performance has improved immeasurably in recent years with the development of more effective equipment. Manufacturers have honed the designs of the machines, making them easier and more comfortable to operate, improving visibility and also tackling issues such as maintenance downtime by making the equipment more reliable and quicker to service.
However one of the biggest advances in compaction performance has come not from the machines, but from the control and measur
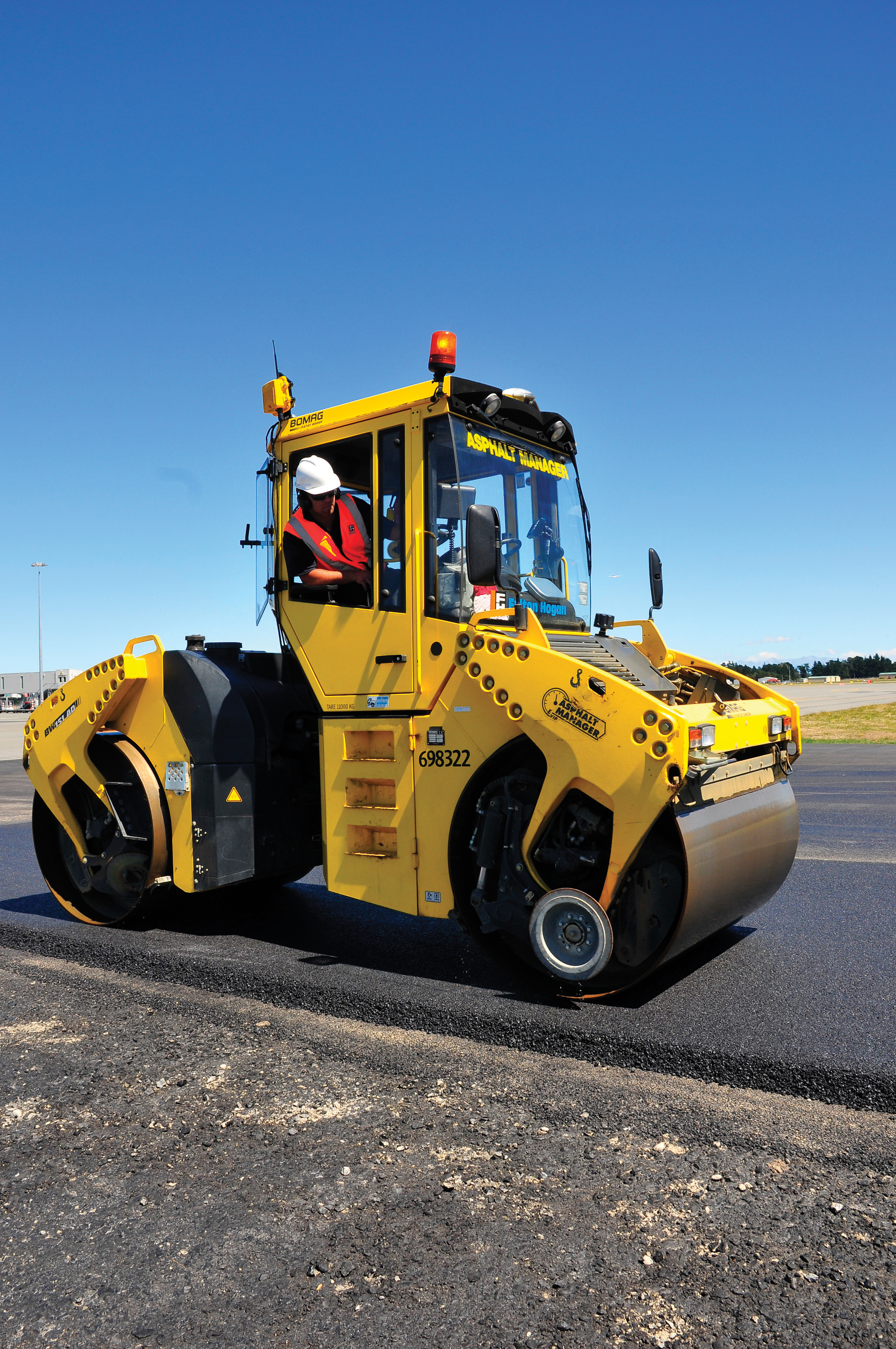
The new Trimble compaction monitoring system can combine GPS position data with heat measurementto ngive an operator an effective guide that boosts working efficiency
The latest developments in asphalt compaction technology allow contractors to boost performance - Mike Woof reports
The efficiency of asphalt compaction performance has improved immeasurably in recent years with the development of more effective equipment. Manufacturers have honed the designs of the machines, making them easier and more comfortable to operate, improving visibility and also tackling issues such as maintenance downtime by making the equipment more reliable and quicker to service.However one of the biggest advances in compaction performance has come not from the machines, but from the control and measurement systems that give operators feedback as to the work carried out. Assessing the quality of the compaction work provides a key step in assuring project specifications are met. And if that monitoring system is provided in the cab of the compactor to give the operator a running guide to work in real-time, efficiency can be raised higher still. The European manufacturers
By giving operators data on the degree of compaction carried out so far and the amount needed to bring the mat to grade and the localised temperature of the mat, these latest control systems can ensure work scheduling becomes more efficient. Rapidly cooling areas of the mat can be prioritised for compaction first, while the controls minimise the risk of overcompaction (and crushing aggregates) or undercompaction and leaving air voids in the mat.
There are two main schools of thought on how best to assess the degree of compaction and this has been the subject of debate between the various suppliers. However it is clear that if one of the modern compaction analysis packages is used, the results will be superior to work carried out at projects using old style machines.
At the recent
For this, a combination of GPS, compaction monitoring and heat sensors are used to provide the equipment with the necessary data.
Meanwhile BOMAG introduced its new Asphalt Manager II package, aimed at use in heavy twin drum asphalt compactors. This system is said to determine drum energy vectors and also displays the EVIB stiffness value in real time. By using the package, smoothness and density targets can be achieved using manual and automatic modes while minimising passes and preventing crushing of the aggregate.
So far
The firm's new CCS900 3D compaction control system was unveiled at CONEXPO-CON/AGG 2011 and can also boost working efficiency.
Trimble claims that the system eliminates the guesswork involved in old-style asphalt compaction processes and allows contractors to achieve finish consistency across the mat while realising the required specification.
As with the packages developed by Dynapac and Hamm for example, this new Trimble system provides a visual indication for the operator to roll a more efficient pattern. According to Trimble this allows the operator to boost productivity while reducing compaction time and fuel usage.
The Trimble system can be specified with two optional IS310 infrared sensors mounted over the front and rear rollers to measure the temperature of the mat at the time of the compaction. The temperature readings are displayed in the cab, showing the operator the areas that have to be compacted first. Operators can also see the number of passes carried out over a certain area and monitor where they have not overlapped properly or left gaps.
The firm offers an entry-level pass count system for use on multiple asphalt compactors in a fleet. Various upgrades such as temperature mapping, higher accuracy mapping, compaction value mapping and a larger display screen are also available.
Whichever of these modern compaction analysis tools is used, the contractor and client will both see the benefit. Work will be finished to specification, more quickly and more efficiently, reducing costs for the contractor and allowing firms to benefit from bonuses where these are available. At the same time, clients will see better road surfaces that last longer and with reduced incidences of early failure or surface problems due to under- or over-compaction issues.