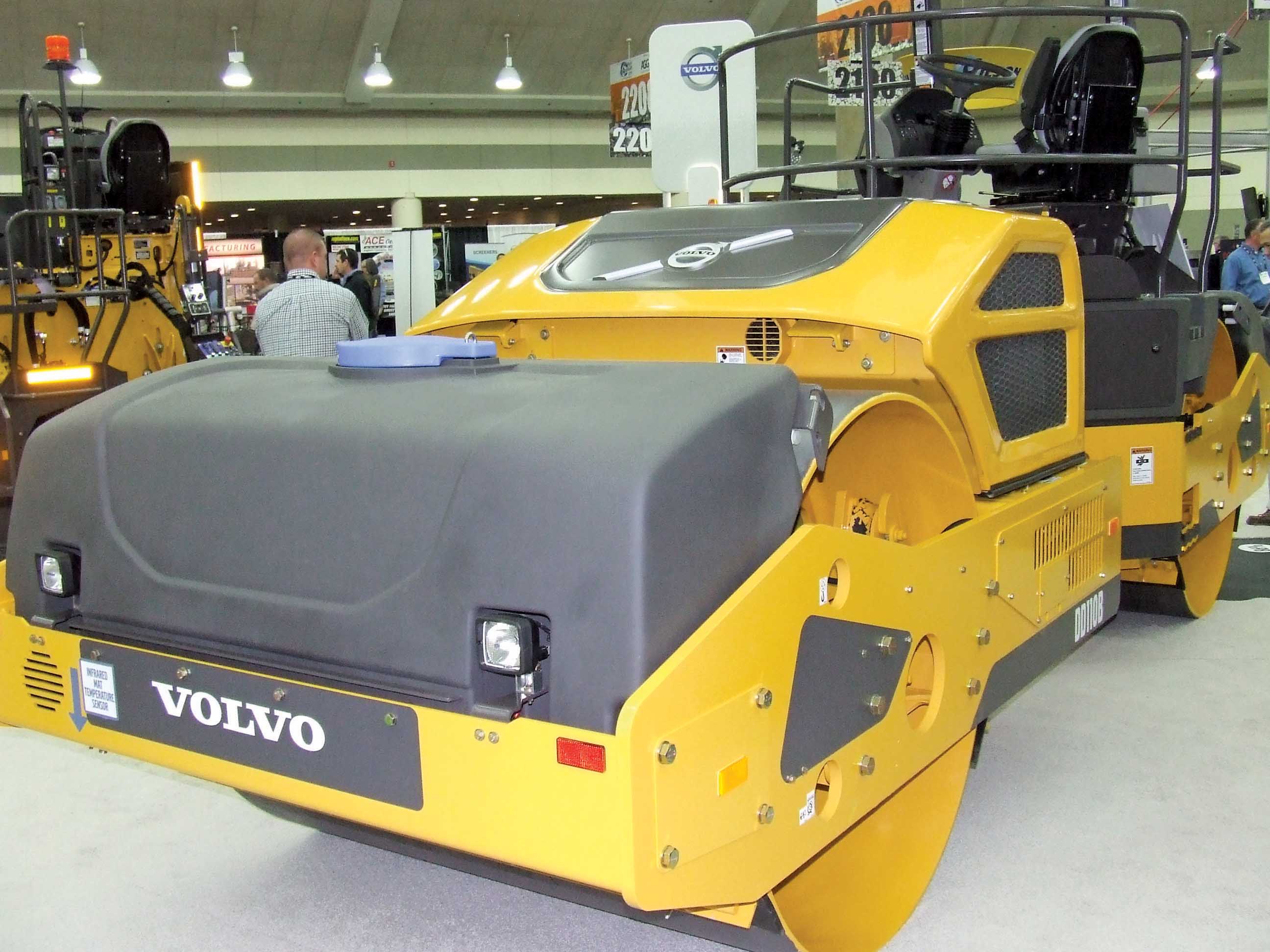
Intelligent compaction technologies continue to advance in sophistication - Mike Woof writes
Ever more sophisticated intelligent compaction technologies are being offered to customers, which can boost working efficiency and help improve construction quality. This is particularly the case for the compaction of asphalt running surfaces. Asphalt cooling leaves only a short time window during which a paved mat can be properly compacted, so intelligent compaction systems offer major gains for contractors and clients alike.
Using intelligent compaction technology a contractor can optimise both the scheduling and the compaction effect of equipment. The technology can boost the calibre of paving by eliminating guesswork, improving quality and increasing productivity.
The latest systems extend beyond the operation of a single unit too as they can optimise the performance of several machines running on a road job.
By employing intelligent compaction systems contractors can ensure that surfaces are compacted while the asphalt is still within the optimum temperature range. The machines can be directed to areas of the roadway that require compacting first, before they cool. Once the mat drops below the optimum temperature, it can no longer be compacted so scheduling a fleet of rollers is crucial to the delivery of a roadway that will last.
Similarly these systems can also provide accurate compaction to grade so that surfaces are neither over, nor under-compacted. This is also crucial to the quality and longevity of a road surface; an under-compacted mat will wear rapidly while over-compaction can crush the aggregates used to make asphalt, again resulting in a poor quality roadway.
Sensors installed on the compactor track the temperature of the mat, while others monitor the drum movement. The system provides a compaction value that can be associated to the density of the mat that has been achieved following compaction. However Tim Hofmann of the firm said, “We relate it to density, but we’re not calling it density.”
The equipment tracks machine location using conventional positioning technology and plots this against the readings recorded from the temperature and vibration sensors. Hofmann said, “You can prove where you’ve been.”
The roller operator first uses the system on a short test strip, which calibrates the unit in accordance with the conditions and materials at the project. The system can then be employed in production to monitor the level of compaction achieved and also show the operator the temperature gradient of the mat.
This sophisticated intelligent compaction system uses data it recovers from sensors mounted on the drum as the basis for the calculations, employing a complex algorithm developed specifically for the task. The sensors determine the rate of acceleration of the compaction drum as it resonates during vibration mode. By establishing the degree of acceleration and feeding this through the algorithm, the system can then deliver a figure for the mat density that has been achieved. Volvo CE says that this is crucial as it allows a contractor to work more closely to the required design specification of the client than with previously available intelligent compaction systems. The algorithm itself formed the centrepiece of the Phd earned by Dr Fares Beainy, based at the University of Oklahoma.
In addition to the sensors monitoring the response rate of the drum, temperature sensors fitted at the front and rear of the compactor accurately plot the temperature of the mat. Dr Beainy explained that this algorithm is more sophisticated than earlier generation intelligent compaction systems providing stiffness calculations rather than density. He said that these earlier generation packages provide values that are not the true metric by which contractors are evaluated and paid.
He said that establishing the density of the mat achieved after each compaction pass has been carried out delivers a far more accurate picture of the work that has been achieved. The system is said to deliver density calculations accurate to within 1.5% of those determined using tried and true core sampling methods.
The system includes a ruggedised android display fitted in the cab of the compactor, which is colour coded. This tells the operator the degree of compaction achieved with each pass, as well as highlighting the temperature of the mat. This allows the operator to see if the density specification has been achieved, as well as showing if any areas of the mat are cooling and require compaction first.
The operator sets the system with the target density and the package has to self-calibrate by being used on a 10m (or so) test strip. Once this has been carried out, Dr Blaine explained that the neural networking nature of the algorithm enables it to learn what constitutes soft or hard on the mat.
With this real-time data, the operator can make any necessary adjustments while the asphalt is being paved. This reduces the occurrence of inadequate densities that drive up project costs, but reduces time spent taking core samples, improves quality, and leads to much greater uniformity than nuclear gauge testing. Calibration data is also saved by the machine, so operators can assign calibrations to certain elements of a job, and switch back and forth between calibrations to meet the demands of specific job elements.
Data gathered from pass mapping, temperature mapping and density mapping is stored on the IC system’s internal hard drive, which provides sufficient space for around seven months of data logging. Data can be backed up to USB drives in VEDA format, the Freeware system promoted by the Federal Highway Administration (FHWA) for IC systems. With optional Differential GPS, the data gathered from Volvo IC is linked to location information accurate to within 0.5 inches. Both Volvo IC packages meet state DOT and FHWA requirements for intelligent compaction specifications.
Density Direct was developed and tested as part of the FHWA Highways for LIFE Technology Partnerships Programme The technology has been used on various full-depth and overlay asphalt pavement projects and later evaluated by independent users at sites throughout the US.