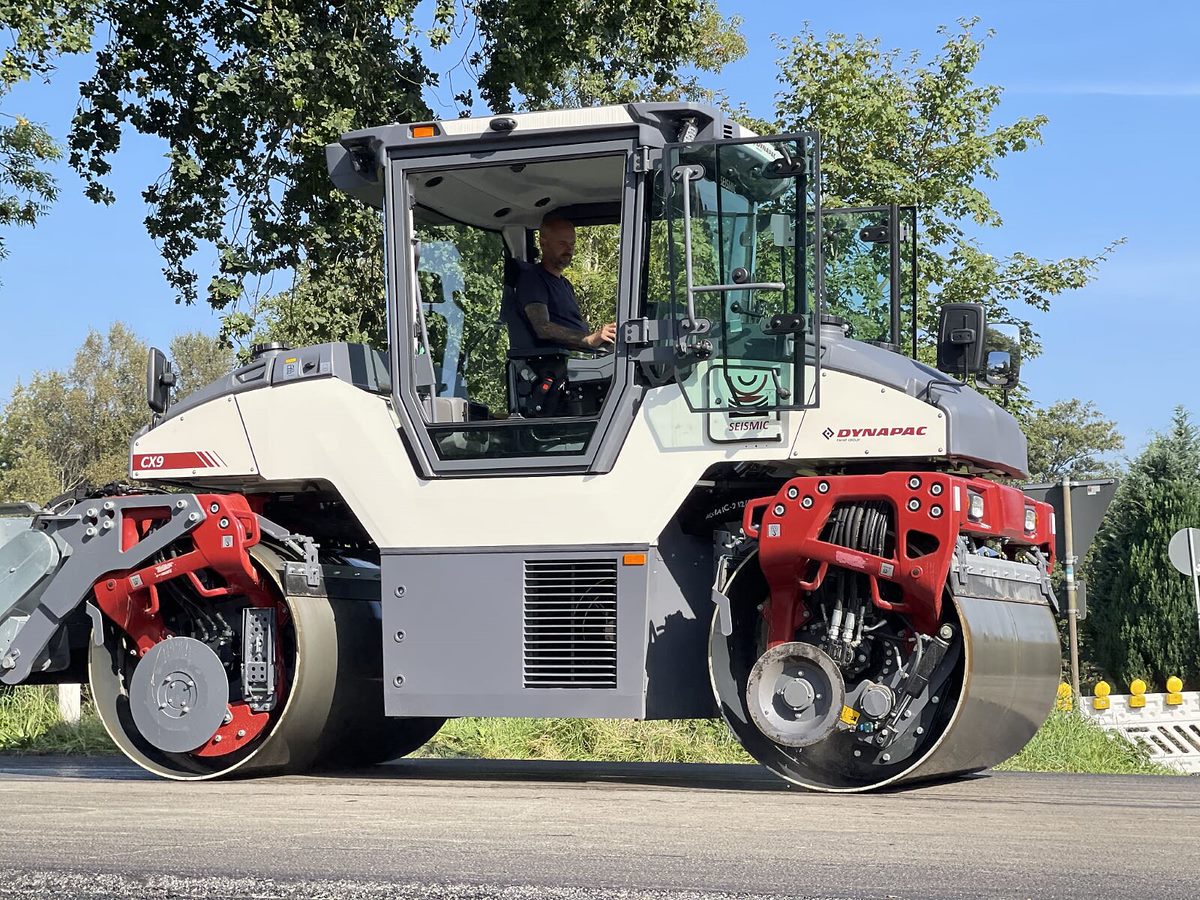
Innovative asphalt compaction machines are now being introduced by several of the major manufacturers, with solutions offering improved working efficiency and performance.
Three of the most innovative developments for asphalt rollers come from Dynapac, BOMAG and Hamm, although new asphalt compactors are also being introduced by other firms such as Ammann and Caterpillar.
For Dynapac, the key advance is the introduction of its Seismic technology to the asphalt compactor range. This system was first developed for its single drum rollers for use in earthmoving applications. The technology uses sensors that determine the resonant frequency of the material underneath the drum and then adjust the compaction forces accordingly. The benefit of the system is that it ensures more efficient compaction as the dynamic forces are optimised to suit the working conditions. The system ensures that the work is carried out to specification, without risking over-compaction. This reduces fuel consumption as well as the number of passes the machine makes.
Developing this system to meet the needs of asphalt compaction has required more development given that the asphalt behaves differently depending on the temperature. A spokesperson for Dynapac said, “It was more complicated and took five years of R&D and needed a lot of testing.”
As temperature is a critical factor for stiffness in asphalt compaction and because the material is in layers, the system required heat sensors to be installed and more complex algorithms to be developed. As with the system for soil compaction, the technology allows drum vibration to match the resonant frequency of the asphalt course to provide optimum compaction. Because the system matches the compaction forces required to the characteristics for a specific section of surface, it also offers a key advantage for the asphalt application as the spokesperson said, “We’re matching the mat frequency with the drum and you’re not going to over-compact so you’re not whitecapping. You get your density numbers a different way by automatically adjusting the frequency.” This avoids the risk of aggregate being cracked or crushed by compaction forces. He added, “The seismic system adjusts the frequency every 0.2 seconds.”
The system is now offered as an option on the new rigid frame CX 8C and CX 9C models, which have drum widths of 1.5m and 1.7m and weights of 8tonnes and 9tonnes respectively. These models have also now been upgraded to the Generation 6 level seen earlier on the 6, 10 and 13tonne class machine. Meanwhile, it is being made standard on the articulated CO2200 VI-CO6200 VI asphalt compactors also.
Note that to meet French requirements, the CX 8C and CX 9C drum steer machines deliver 0.8mm of amplitude and benefit from larger eccentric weights and reinforced bearings. This French market requirement is now the standard for the CX models. The vibration system itself is conventional though and does not require any special maintenance as the core of the technology is in the control unit, while it is said to be simple for the operator to use.
Dynapac says that other key benefits of the seismic option include reduced operating noise, less vibration for the machine (in turned reducing wear and tear and fatigue for the operator) and lower fuel consumption. The spokesperson said, “We estimate around 10% fuel savings.”
The package is only available for vibration type compactors and Dynapac says that the benefits of the Seismic technology are less applicable to oscillation type machines in any case. This is because the latter are not able to cover-compact an asphalt mat in any case.
Coming to the market soon from BOMAG will be a novel braking system, which will be available on the ROBOMAG BW 154 asphalt roller (as well as the ROBOMAG BW 177 soil compactor). The Emergency Brake Assist system scans the construction working environment in real time and identifies moving and static obstacles and objects. Objects that could be put at risk by the machine's movement are detected by the system. If a collision is imminent, the system slows the machine down to a complete stop. By averting potential hazards, the technology marks a significant milestone in enhancing on-site safety. Recognising its added value, the jury at the INTERMAT Awards in Paris honoured the technology with the prestigious Gold Award in the "Roads, Materials and Foundations Industries" category.
In cooperation with selected customers, BOMAG plans to test the Emergency Brake Assist on various construction sites this year. The company's service organisation is also involved in refining the technology for series production, ensuring that customers receive the same first-class service for digital systems as they do for mechanical components.
Emergency Brake Assist is compatible with BOMAG's fifth-generation tandem rollers and therefore independent of use beyond just a fully autonomous asphalt roller. As the technology nears production readiness, the final certification is being worked on in cooperation with experts, which is critical when safety-related innovations are involved.
From Hamm comes a new development in the shape of its HD+ 120i V-VIO-2 HF. This innovative compactor offers the benefits of compaction by vibration and oscillation. While other machines (from Hamm and some competitors) have been able to offer this combination previously, they have been restricted to having one drum for vibration and the other for oscillation. The new HD+ 120i V-VIO-2 however offers both vibration and oscillation on both drums. This allows the operator to combine the compaction types, depending on the application.
Tim Kowalski, product specialist for Hamm at Wirtgen Americas commented, “We can run dual oscillation or you can have vibration and oscillation.” He said that the operator can set the machine so that it delivers vibration at the front and oscillation at the rear and then switches automatically when it reverses direction. He explained that this better suits the machine to use with new mix types, which can prove more challenging to compact with conventional equipment. The operator can switch easily between vibration and oscillation, removing the need to switch machines or deploy an additional machine and another operator on the construction site.
The 12tonne-class machine is powered by a 115kW diesel that meets Tier 4 Final/Stage 5 emissions requirements and features the firm’s efficient Easy Drive operating concept. Featuring 2m-wide drums, high compaction forces are claimed, along with reliability, durability, productivity and ease of maintenance.
A key feature is the versatility as it offers static compaction, oscillation and vibration. This versatility means that the same machine can be used for different asphalt mixes. The combination of vibration and oscillation delivers fast compaction in fewer double passes, suiting it to final compaction. High compaction quality is claimed even at increased working speeds.
The machine has the latest Hamm cab, offering good all round visibility as well as various interfaces to connect telematics systems, fleet management systems and digital applications for controlling and documenting compaction.
Operators can make use of the benefits of oscillation for the compaction of joints or compaction in vibration-sensitive areas such as on bridges. Oscillation also allows compaction at low outside temperatures, since a wider temperature range can be used. The system is effective in preventing particle crushing and over-compaction. It also has benefits when compacting distortion-sensitive materials and reduces noise emissions and vibrations experienced on and around the construction site.
Aimed at the rental market, Ammann’s new light tandem roller is petrol-powered and features side-free drums that enable compaction in the tight jobsites. The Ammann ARX 10.1 StV features the Honda GX630 petrol engine rated at 15.5kW. This reduces ownership costs and meets the latest Stage V/EPA Phase III emission regulations.
The engine is more compact than the diesel machine, allowing cooling from all sides and helping performance in high ambient temperatures. Petrol is also less expensive than diesel, while there is no need for a diesel particulate filter (DPF) and maintenance of a petrol engine is also less costly than for a diesel engine.
The Ammann ARX10.1 StV has its drum consoles installed from a single side. The drums are support-free on the right side. This allows compaction work on tight jobsites. Drum working widths are 900mm and drums are installed in-line. Despite the compact size it has powerful hydraulics and both drums have robust drive motors and a negative parking brake mechanism for safe parking when the engine is switched off.
The vibratory system in the front drum can deliver 16.4kN at 76Hz, sufficient for a range of duties. The rear drum is static and has no vibratory unit. The pressurized water sprinkling system has a tank capacity of 110litres.
Also new from Ammann is the ARP 75 twin drum roller, which offers pivot or crab steer functions and is also available as a combi machine with one steel drum and four rubber tyres.
This model is said to be versatile and productive, suiting jobsites where precise steering is a priority. The new cab is said to offer good visibility and low working noise. Other benefits include well-designed and positioned water tanks that improve sight lines to all drum surfaces and edges.
The ARP 75 operator station extends beyond the 1x1m rule in both directions, boosting safety. The machine features the novel Fingertip Steering (FTS) system, which replaces a steering wheel and allows operators to keep both hands on the armrests. A new touchscreen helps operators control machine functions and allows easy adjustment of vibration, lights, and the firm’s sophisticated ACEforce package that provides Continuous Compaction Control.
The standard operating width of the ARP 75 is 1.5m, although using crab mode can increase working width and enables compaction close to kerbs and obstacles. Machine working width can be increased slightly to enable compaction around obstacles – or it can be expanded by up to 1.22m to a total machine working width of 2.72m. This improves productivity on long, straight jobsites. The two-stage vibratory system offers multiple frequencies to optimise compaction. The ARP 75 has adjustable frequencies ranging from 38-55 Hz. It is able deliver compaction output in the range of 47-92kN/drum.
Power comes from a Kubota V3307-CR-T diesel rated at 54.4kW and that meets Tier 4 Final and Stage 5 emissions requirements, with EGR+DOC+DPF aftertreatment.
Available on the ARP 75 are ACEpro or ACEforce Intelligent Compaction systems. The ACEforce system uses absolute measurement (kB value in MN/m) of compaction results, making it easy to correlate with laboratory tests.
ACEpro is an automated measurement and regulation system. Parameter adjustment is based on continuous measurement of compacted material. Core parameters – such as amplitude and frequency – utilise automatic, stepless regulation.
Both compaction systems are compatible with all major GPS manufacturer´s products to provide mapping and operator guidance.
And Caterpillar is updating its mid-sized CB7, CB8, and CB10 asphalt compactors, with new edge-management options, optional cab, optional split drums, and a sophisticated mapping display.
Management of unconfined edges can help optimise density and deliver better road quality. The vertical edge created by the cut-off wheel helps provide a stable vertical face for joint matching on the next paving pass. The bevel edge options provide sloped profiles for smoother transitions on and off the paved surface. Three versions are available to meet requirements.
The new mapping display provides a new visual for easier recognition and touchscreen capability for simplified setup. Cat Compact helps operators visualise the mat while recording pass-count and temperature data. The system uses infrared temperature sensors and GPS mapping to keep the operator informed of mat temperatures, machine position, pass-count and pass coverage. This system enhances nighttime performance, while also capturing data for future process analysis and quality control documentation. A spokesperson for the firm said, “These are the first compactors from Cat with the latest intelligent compaction system.”
The new dual split-drum option on the front drum can help eliminate tears when manoeuvring around obstacles or when compacting tight turns by reducing the speed of the inner drum half. The split drum option benefits applications that require frequent turning.
The machine also has Caterpillar’s VisionLink system, a cloud-based software application that provides data to a desktop or mobile device, for more efficient fleet management. The system show maintenance needs, machine hours, location, fuel usage, idle time, diagnostic codes, and other machine data to a mobile device, desktop or through an API to other software applications.