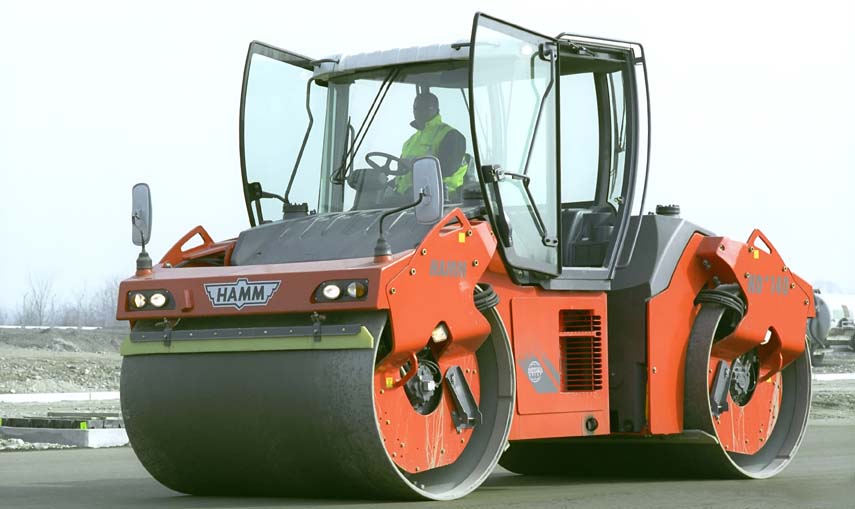
The latest compaction technology offers users the benefits of more accurate performance by combining heat detection and compaction metering with GPS
In Europe several leading manufacturers now offer more accurate compaction technology, with Ammann,Meanwhile,
The package develops Sakai's intelligent compaction (IC) concept, providing users with more efficient operation. The system uses information on soil compaction, aggregate bases and HMA pavement materials and this is combined with a digital measurement system and a global positioning system (GPS) for mapping. Advances in computing power, GPS technology and software have made IC a reality and available electronic compaction data allows a contractor to understand the compaction process in greater depth.
Highway authorities are starting to identify the benefits and are developing IC quality control CIS is factory-installed on the vibratory single drum soil rollers or double drum asphalt rollers, can be used for a variety of applications, and employs GPS position data.
The system is compatible with most GPS systems used in the construction market and includes a large touch screen PC display for the operator, a compaction control value (CCV) sensor and a surface temperature sensor.
AithonMT (machine terminal) software allows the roller to document the compaction process while the AithonPD (plan design) office software is used to generate plan files as well as allowing further analysis of data and preparing reports to quantify results.
The package is a further development of Sakai's compaction measuring system for vibratory rollers. The technology has evolved, based on over 20 years experience of improving compaction for soils, crushed rock and sub-base materials and most recently on asphalt as well.
The system is accelerometer-based and as compaction percentage increases with each roller pass, the drum acceleration increases according to the machine/ground interaction. From this the sensor calculates a CCV that indicates the degree of compaction. This is a relative value which increases with roller passes and can be correlated with data from single point density measurement devices as well as testing equipment.
The new CIS package continuously records all compaction data for the entire project simultaneously, including GPS position, CCV, number of roller passes and surface temperature. This gives the contractor and engineer 100% coverage of the project, unlike conventional nuclear gauges, and the operator can see this data in real-time on a colour screen in the cab. The display provides colour coding of the compaction area so that the operator can see how many passes have been carried out and can also view the surface temperature of the asphalt mat to prioritise the remaining compaction work.
Using the system cuts the risk of over and under compaction and ensures that the work meets the required specification. Recorded information can be downloaded using a USB stick for further analysis.
All the CCV information can also be viewed on a PC screen in real-time, important for mapping the sub-base, and this allows weak areas to be identified and corrected before asphalt paving begins, according to Sakai.
The package has now been extensively tested in the US, including a three-year study with the highway authorities of several states. The results have confirmed the benefits of the technology including reducing paving penalties for the contractor, improvements in quality and savings in compaction costs while reducing the variability of density, according to Sakai.
By comparison, a German customer is now finding out the benefits of using the latest AccuGrade control package on its recently acquired fleet of
Several of the machines were equipped with the AccuGrade grade control system by Zeppelin to meet the needs of a number of key projects. Using the system has cut working costs significantly by reducing the time an operator needs to carry out each job as well as the need for reworking, while ensuring all the compaction is carried out to the necessary specification. The system evaluated the degree of soil compaction and correlates the data with the GPS positioning of the measurement in real time. This helps improve the quality of the compaction, while lowering operating costs, reducing necessary manpower and increasing efficiency.
The AccuGrade compaction GPS mapping and measurement option is now generating increasing market interest in Europe, Asia, Middle East countries as a result and the system is offered as a factory-installed option as well as being available on request from main dealers. The system is currently available on the Cat CS56, CS64, and CS74 and CS76 smooth drum soil compactors.
New in the metal
New model development continues in the compaction sector too. Wacker Neuson says that its new RD16-100 vibratory roller suits duties for compacting surfaces in restricted space areas. This model is the latest addition to the firm's RD16 vibratory roller range and features 1m wide drums. The machine, which features a tight turning circle, can work in restricted space conditions.
The user has the option of one or two vibrating drums and for working on asphalt, productivity levels can be increased by a flow of water delivered by a pressure-driven sprinkler system.
The machine has a double drum drive for optimum traction and is powered by a
Productive rolling
The first Dynapac CC324HF in the UK has been put to work on the new A1073 Spalding to Eye link road in County Lincolnshire, eastern England, by surfacing contractor
Main contractor on the project is Morgan Est and work on the 22km link started in March 2008. Completion is due in late 2010.
The phased approach to the €93.64 million (US$133 million) scheme for Lincolnshire County Council means that surfacing work is already underway.
This dual amplitude, high frequency roller is well suited to the work in Lincolnshire as the machine offers the operator good visibility of the drum. Highly productive, this 8tonne machine replaces the well-proven CC322 and features a modular design that allows it to share components with other models in the Dynapac range. Other features include a 180º swivel and sliding seat to give the operator a clear view of the working area, an LCD display and joystick controls. Easy to operate, the machine can provide a high standard finish to meet compaction specifications for each project.
The machine has a SoftStart function that smoothes the compaction as well as automatic water and vibration control, which have helped work on the A1073 project.
The vibration and frequency on the machine is set using menus on the LCD display, making it easier to use while daily checks on the roller have been improved with ground level water filling point and centralised service points.
Efficient upgrade
Upgrades to Milan's Malpensa Airport in Italy have benefited from the use of the latest technology from the
Key machines working on the project were the Wirtgen KMA220 mobile mixing plant and a fleet of Hamm rollers.
The new Southern Link taxiway now connects the aircraft parking areas to Runway 1 and this means that aeroplanes no longer have to cross Runway 2.
A joint venture group comprising Compagnia Italiana Costruzioni (CIC) and Sirti handled the work. Contractor CIC carried out works on the taxiway and shoulders, the water gulleys, the construction of two bridges allowing the new runway to pass over the railway trench of the Milan-Malpensa line, as well as other ancillary works. Sirti installed the lighting and electrical systems.
Recycled aggregates were used for the construction of the 2.528km long by 30-35m wide taxiway pavement foundations.
Around 500m of the taxiway had already been built as part of a previous tender contract and located 450m from the heading on Runway 2. The work also required the construction of 15m wide shoulders while the taxiway was designed to handle large aircraft such as the huge A380, and the work also included a new 2km perimeter road for fire fighting equipment.
The cement stabilised layers are 640mm thick in total, with 250mm of traditional cement stabilised layers with a grain size of 0-40, 250mm of special cement stabilised layers, again with a grain size of 0-40, but using a different design mix than the previous version. On top of these stabilised layers, 80mm of binder and 60mm of wearing course made with modified bitumen were laid.
In total, the new taxiway required the production of over 27,000m³ of material covering over 54,000m³.
For CIC to meet daily production requirements the company bought its Wirtgen KMA220 mobile mixing plant, and this was the first time the machine was used to produce cement stabilised layers in Italy. However, tests showed that the KMA200 was able to produce material to the very tough specification.
CIC is a long standing Hamm customer and used the 3520 and 3625 models to compact the stabilised layers, while the surface layer operations were performed by a GRW15 rubber-tyred roller as well as brand new 13.5tonne HD140+ VV unit.