More efficient and productive compaction solutions are coming to market shortly, Mike Woof reports. Several key trends are emerging in the asphalt compaction market with the development of the latest generation machines. Performance and productivity remain key issues for compactor manufacturers with firms keen to maximise output from their latest units.
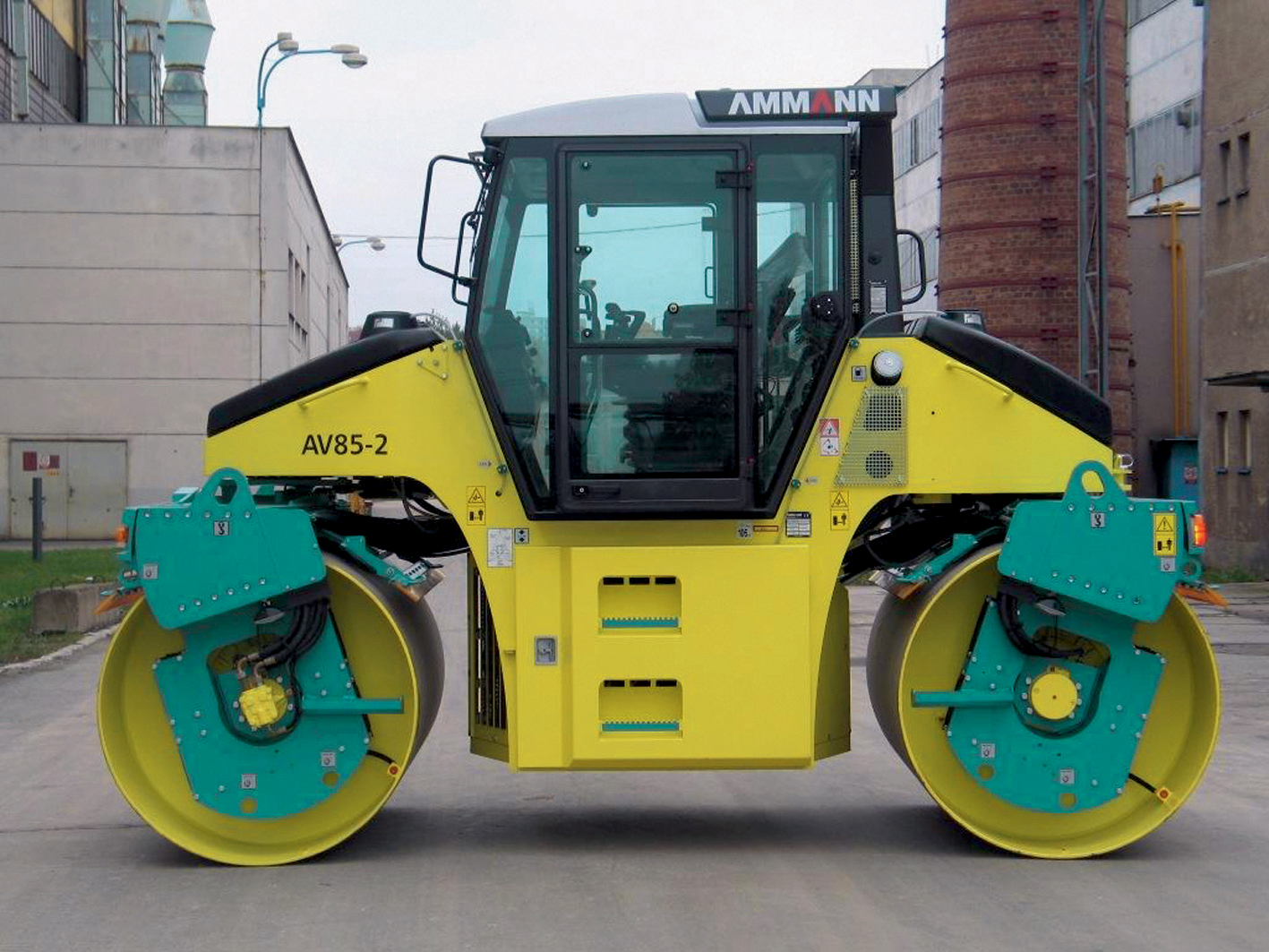
Ammann's drumsteered models offer steplessly adjustable crab steering
More efficient and productive compaction solutions are coming to market shortly, Mike Woof reports
However, it is intelligent compaction technology that offers the most radical potential for change in road construction practices. A number of the leading firms have designed sophisticated compaction controls and taken these technologies one step further by integrating the systems into smart packages that optimise performance. According to Jean-Claude Fayat, president of the
The systems use a combination of equipment to measure compaction carried out and monitor the heat of the asphalt mat while GPS tools provide location. Using this technology together allows the operator to optimise the job by prioritising work and compacting areas of asphalt that are cooling before moving to the warmer areas of the mat.
The benefits to the client of using such technology are substantial. This ensures that compaction can be carried out to specification before the mat cools. Most of the latest systems will document the work carried out, showing the contractor what compaction has been done and providing a digital record that can be stored and checked if required. Because of the potential this offers for smart construction techniques, number of manufacturers are working on developing systems at the moment and these will be brought to the market in due course. At present however, the firms
With the increasing sophistication of construction operations and an ever greater reliance on software to manage projects more effectively, the demand for intelligent compaction equipment will continue to grow. The latest construction software allows the 3D model to be used as the document of record for a project and this is now being accepted by some of the more forward thinking highway authorities around the world, particularly in some US states and European nations.
For the contractor it means that the portion of the design model relating to the compaction job can be downloaded straight into the computer mounted on the machine. The roller operator can follow the guidance instructions of the road design from the original software model as set out by the engineer and ensure that any work is carried out precisely to the required specification.
The roller operator can also allow the machine to react to workflow changes on-site and schedule compaction tasks to ensure that the coolest areas of the asphalt mat behind the paver are tackled on a priority basis. This way compaction is not only carried out to the specification, but is also ordered within the limited time window afforded by the cooling of the asphalt mat. By using the latest smart compaction technology to the full, the need for re-working areas that have not met specification can be reduced, making substantial cuts in materials, fuel consumption and labour costs as well as shortening construction times and speeding project delivery.
As the data flow from intelligent compaction machines can be two-way this offers additional gains to the construction firm. Comprehensive compaction data from the asphalt rollers can be downloaded in real-time back into the 3D software, along with other recovered data from earthmoving machines earlier in the construction process for example.
This is significant and will further boost the quality of information available for the 3D model as a project's document of record. For highway authorities, this will provide speedy access to a complete record of construction data for each project. In the event of any problems occurring with a section of highway (or airport runway) at some later stage, full analysis of information recovered from the machines will provide a comprehensive guide to what work was carried out and help pinpoint the reasons for early failure. Combined with the reduced environmental impact from a more efficient project implementation, this offers contractors a string of potential gains.
ASPHALT GOING GREEN
With environmental factors becoming more of an issue and new regulations and requirements forcing the industry to change, smart compaction machines form a part of the picture. Compaction equipment can also offer more direct benefits to reducing the environmental profile of a construction operation and another interesting development is of a prototype hybrid asphalt roller built by BOMAG, using one of its twin drum asphalt compactors as a base. Using a hybrid drive in an asphalt compactor offers an effective way to reduce fuel consumption and as these machines have to be heavy to do their job, the weight of a battery pack or a bank of capacitors can take the place of steel ballast without impeding performance.The operating cycle of an asphalt compactor, with its repeated forward and reverse cycles, particularly lends itself to the use of regenerative braking and flywheel technology seen in some hybrid vehicles to store energy and to allow this to be re-used. Because of this, a hybrid drive-train offers far greater potential for fuel savings and emissions reduction when installed in an asphalt compactor than in a passenger car for example. In a passenger car the weight of the batteries provides a limiting factor on performance and working efficiency, whereas fitting batteries or capacitors in an asphalt compactor will play a secondary role as necessary ballast.
Testing of BOMAG's prototype will provide actual data on how much fuel could be saved in this type of operating cycle. But with the cost of fuel continuing to increase in Europe and parts of Asia in particular, the premium purchase price of the hybrid asphalt compactor would likely be offset by its lower fuel costs in service. Hybrid construction machines have been seen in prototype form for some years and are now coming to market. It is worth noting that
Meanwhile in the US while fuel costs remain low, the low emission benefits of the hybrid asphalt compactor would be of interest to contractors operating in states where regulations are stricter, most particularly California.
Only when BOMAG has carried out extensive site testing of its prototype and factored in the reductions in cost from manufacturing in production volumes will it be possible to determine accurately the payback time for a hybrid machine. However, it seems likely that other firms will also look to develop hybrid asphalt compactor prototypes in due course.
FINISHING SCHOOL
Quality of finish remains a key focus for asphalt compaction, given that this produces the highway's final running surface and another noticeable trend in the asphalt compaction sector is the development of a new generation of rubber tyred rollers. Several major manufacturers are now introducing improved machines of this type to meet a growing resurgence in demand for these units and particularly for surface finishing applications. In past years the European market for rubber tyred rollers declined and this was due in part to the earlier generation machines which featured mechanical drives and were not able to deliver the smooth stopping and starting required to provide an optimum finish.Advanced hydrostatic drives offer progressive control, preventing the formation of ripples in asphalt surfaces. The hydrostatic drives also make the machines smoother to operate, helped by larger cabs and the latest ergonomic controls and overall design.
One key introduction comes from Ammann, which has improved on its earlier AP240H with the launch of its new AP240-2H and is said to offer greater operator comfort and controllability.
The high quality ergonomics provide the driver with a large cab, rotatable seat and adjustable steering column and pedals. A hydrostatic drive system provides the gentle starting and stopping performance required for the rubber tyred roller, where harsher speed changes would leave marks. Its operating weight depends on the needs of the application as the machine can be equipped with ballast and in use will weigh from 9.6-24tonnes. The AP240-2H also offers a working width of just over 2m and is powered by a
From Dynapac come three new rubber tyred asphalt compactors driven through hydrostatic transmissions by emission compliant engines that were initially developed for the Brazilian market. However Dynapac said that it has seen customer demand for rubber tyred units grow in other markets too and now plans to market the units worldwide. The CP224, CP224W and CP274 models offer an effective solution for providing a high quality finish, with compaction widths ranging from 1.8-2.3m and maximum operating weights from 21-27tonnes. High performance and good fuel economy is claimed while dualcircuit braking provides full braking effect even if one circuit is disabled.
The rollers are built on a modular basis and share components and sub-systems with other Dynapac machines, reducing costs in servicing and spare parts holding. These compactors can be used for a wide variety of finishing and sealing applications, with an accurate control system as well as the additional options of DCA-A compaction analyser and temperature sensor.
The full equipment package allows the machine to deliver optimum density and surface texture while this unit also provides documentation of work carried out for later analysis.
From Hamm comes the compact but productive GRW280 rubber tyred roller, the product of a three year development programme.
Depending on the quantity of ballast loaded, this rubber tyred roller offers operating weights from 10-28tonnes and can be reconfigured quickly to suit different application requirements. The user can also select concrete, steel or water ballast, depending on the application due to the firm's sophisticated new loading concept. The machine provides effective compaction, with steering systems and tyre positioning configured so that wheel paths overlap in straight operation as well as in turns. The design of the machine has also been carefully established through an intensive prototyping process.
MODEL CHANGES
Other new model introductions include an addition to Ammann's line of heavy articulated tandem rollers with the 12tonne the AV120X.Like its siblings this features a split drum design and steplessly adjustable crab steering. The engine is positioned at the rear of the chassis area for ease of servicing access while effective noise and heat maximizes operator comfort. The AV120X has a working width of between 1.880-2.204m and features a direct drive system with twin pumps for high performance and reliability.
BOMAG's new 10tonne pivot-steered tandem roller has been developed from the successful BW174AP. The new ECOMODE system makes the BW174AP economical to run, with tests showing fuel savings of over 20% in comparison with conventional machines. An active engine management package delivers power as required and cuts engine output, using an intelligent sensor system. This monitors power requirements and automatically adjusts the speed of the Kubota engine, as well as reducing in-cab noise levels. The BW174AP is also equipped with the firm's sophisticated ASPHALT MANAGER control package to further ensure high performance.
Hamm's new HD+ line-up is a 10 model range of mid-sized, articulated tandem rollers, weighing from 9-14tonnes. The firm has re-designed the articulation joints to improve weight distribution and stability, as well as boosting compaction performance. The steering offset feature in crab mode has also been increased while the machines deliver higher productivity than before and the bigger water tank allows operation for a full shift without need for refilling. The HD+ range now includes a high-frequency version for the US market, where paving production rates are higher and compaction machines need to be able to keep pace.
JCB Vibromax has also launched the new heavy duty VMT860 to further enhance its range of double-drum vibratory compactors. Replacing the VMT850 and powered by the recordbreaking, low consumption JCB Dieselmax engine, the new model boasts excellent vibration performance.
The company, which offers 60 Germanengineered high performance soil and asphalt compactors, says the new model is able to operate with low frequency and high amplitude for large asphalt or standard soil applications and at an optimised amplitude on high frequency for standard asphalt jobs. The VMT860 also boasts large fuel and water tank capacities of 240litres and 1,070litres respectively to enable productive operation throughout the working day, "without costly and time-consuming interruptions for refilling." It has been specifically designed for the compaction of sub-bases up to the final rolling of asphalt materials in areas such as yards, access roads, residential streets, car parks, motorways and airports.
With a drum width of 1,675mm, the VMT860 weighs in at 8.75tonnes with standard ROPS protection and 9.25tonnes with the optional full ROPS/FOPS cabin. Vibration is powered through a single-piece shaft with overturning weights to ensure maximum compaction performance from a robust design which keeps maintenance to a minimum. The electrically-controlled hydrostatic direct drive on both drums gives the operator the flexibility of double, single-front or single-rear vibration.
"Operator comfort is achieved courtesy of a vibration-isolated, spacious and ergonomic driver stand with two seats, one central driving lever and a swivelling steering wheel. The optional ROPS/FOPS cabin provides enhanced safety and weather protection," says JCB.