More sophisticated compaction technologies are now coming to market, offering
a wide range of benefits to users
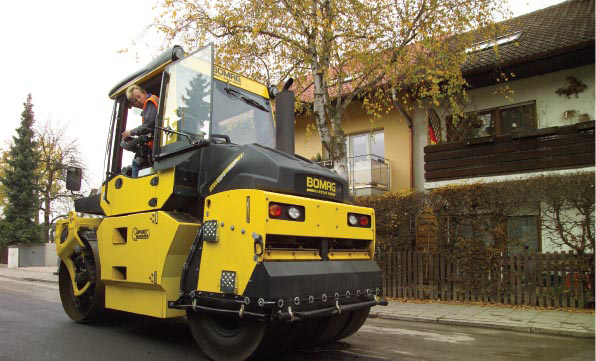
More sophisticated compaction technologies are now coming to market, offering a wide range of benefits to users
More sophisticated compaction technologies are now coming to market, offering a wide range of benefits to users
While asphalt paving techniques vary widely between North America and Europe, there is greater commonality in the compaction methods required. New developments in compaction rollers are offering contractors using both North American and European style paving techniques major gains in quality.According to Robert Horan, a regional engineer for the US-based Asphalt Institute, intelligent compaction technology represents the future for highway construction. Horan presented a paper at the World of Asphalt conference and exhibition in Orlando, Florida in March detailing the benefits of intelligent compaction, as shown by extensive research and field trials. Horan is convinced that intelligent compaction will be of vital importance in future highway construction projects. "I believe that in the future you're going to see more smart and intelligent technology on rollers," he said.
Intelligent compaction is needed because it tackles the shortcomings of conventional equipment and can deliver proper in-place density to allow good surface performance according to Horan. He said, "Good compaction is vital for good performance.
Conventional compaction has shortcomings and many times we don't get the density we require, so service life suffers."
Horan explained that compactor operators have a difficult job because they often have little information about the surface they are working on. He said, "Roller operators often don't meet specifications because they're getting no feedback from the machine and many times they under compact or over compact the surface."
There are shortcomings with current methods used for testing compaction densities. The problem is that core tests can only be carried out after a surface has been laid, by which time it is too late to change compaction methods. Horan said, "If you're doing the tests after compaction, what are you going to do about solving problems?"
He continued, "Intelligent compaction is the key. The technology can be used for both single and twin drum rollers."
Horan explained that accelerometers can be used to measure vibration and response in the asphalt and this can be linked to a GPS system so that the machine records data on the densities for each area. This can be further backed up by thermal monitoring equipment mounted on the machine that records the temperature of the asphalt. Many of the leading compaction equipment manufacturers are now developing intelligent compaction technologies with some systems for twin drum asphalt rollers already on the market and several more coming shortly.
Using intelligent compaction technology allows for high quality on thin lift construction techniques. The latest GPS systems are very accurate according to Horan and he said that heat monitoring systems means operation can be prioritised to ensure effective compaction. But Horan admitted that there are limitations with the currently available thermal gauges and said, "The problem is that we're more interested in the internal temperature of the asphalt rather than the surface temperature. However, we're looking at that."
Tests carried out in the US state of Minnesota proved the benefits of some of the latest intelligent compaction technologies according to Horan. For these tests a
Horan explained that the benefits of using this technology, from Sakai or competing systems from other manufacturers such as
In the metal
New machines are being introduced by several of the leading roller manufacturers, with some intelligent compaction systems coming to market now.The Swiss-based Ammann Group says its family of articulated asphalt rollers is complete following the launch of the 7.1tonne AV70X and 8tonne AV80X models and the 10.5tonne AV110X and 13tonne AV130X heavy vibratory tandem rollers. All of the new machines are high-performance compactors that are said to be highly manoeuvrable and versatile. The engines are mounted at the rear of the chassis to maximise service access, and the driver's cab insulation affords effective protection against noise and heat. Both the AV70X and the AV80X4 offer vibration performance of 0.62/0.3mm and 48/63 Hz while the former has a working width of 1.45-1.75m and the latter offers working widths of 1.6-1.9m.
BOMAG is introducing a number of improved models to its line-up and its improved 7tonne class roller models offer higher performance and a wider option range than before. The BW154ACP combination roller features pivot steer and customers for this model can opt for the sophisticated BOMAG Asphalt Manager control package, which automatically optimises compaction.
The kneading effect of the extra wide tyres also allows for effective surface sealing as coverage is maximised while the use of large diameter tyres helps ensure that compaction is even. High wheel loads of 900kg/tyre maximise compaction effect while fully adjustable scrapers prevent any dirt build-ups on each tyre. Another important option is a thermal apron system for the tyres that can be lowered to prevent fast cooling in cold weather or on windy days and raised when conditions are good.
As with BOMAG's other recent compaction machines, the BW154ACP features a high comfort, high visibility cab with ergonomically-designed controls and a mini steering wheel which allow the operator to work for a full shift with a minimum of fatigue. An array of other options is available including drum edge lighting and by-pass filters. The precision spreader option is patented due to its novel vibrating screen system, which is said to allow an even and precise finish and uniform chip distribution, allowing for the construction of high quality, skid-resistant surfaces.
Dynapac has four new tandem rollers aimed at asphalt compaction duties, with two models in the 7-8tonne class and two in the 8-9tonne class. Customers can choose from standard or split drum versions for each of the two weight classes and the firm claims that the machines can deliver high quality finishes. Other features include Tier emission compliant engines, comfortable cabs and good access to service points.
Hamm is also offering a sophisticated compaction control system in the shape of its innovative HCQ Hamm Asphalt Navigator. The system offers new measurement and documentation capabilities due to the use of a GPS receiver. The HCQ Hamm Asphalt Navigator can record the number of passes and determine the temperature over an area of asphalt being compacted. The system uses the information to produce a priority map with colour codes that show the roller operator where to drive the machine. The technology follows on from Hamm's proven systems for the soil compaction market where the company has had success with its HCQ GPS navigator, which ensures continuous compaction control.
The company also plans to capitalise on the success of its HD series compaction machines with the introduction of the improved HD models. Designed for the 12tonne and 14tonne weight classes, these new models offer increased power, improved operator comfort and better all-round visibility over the HD machines being replaced. The HD120 weighs in at 12.9tonnes and features 1.9m wide drums while the HD140 is slightly larger and weighs 13.8tonnes, with 2.14m wide drums.
There are three basic versions available, as vibratory rollers (VV), as oscillating rollers (VO) and as a high-frequency version for the US market. The operator is able to opt for drum oscillation or conventional vibration on either or both of the drums if required, with the different capabilities suiting different applications.
The frequency and amplitude of the vibratory drives can be adjusted independently for both drums, allowing performance to be matched to the requirements of the asphalt. Hamm is also offering a high-frequency version of the HD concept for the US market where high productivity paving is carried out, requiring faster compaction rates. And drum oscillation will also be available on further additions to the HD range as these come to market.
Improved ergonomics are said to reduce operator fatigue and make the machine easier to use for longer periods while the cab has been further increased in size and the access height has been lowered by 250mm. The new three point articulation joint is located close to the centre-point of the machine and allows for a better weight distribution in turns. Power for both models comes from a four cylinder diesel rated at 100kW and which meets the Tier 3 exhaust and noise emission requirements.
In addition, the firm is introducing a compact finishing roller, the HD14TT to its CompactLine. Designed for finishing work, this 4tonner is an articulated model with an operating width of 1.28m. Features include ergonomic controls as well as high comfort, visibility manoeuvrability and productivity. This rubber wheeled roller also features all the proven characteristics of the prize-winning CompactLine such as an optimum view due to its slim-line front end, its low machine height or the central suspension point for easy loading.
The larger DD24 double-drum compactor weighs 2.6tonnes and has 1.2m wide drums with two vibration frequencies (55Hz and 67Hz) for different surfaces.