Effective compaction control is one of a series of technical innovations boosting performance efficiency – Mike Woof writes. Maximising compaction efficiency can be a major cost factor on construction projects. Both for soil and asphalt compaction sectors, the risk from leaving an area under or over-compacted is substantial.
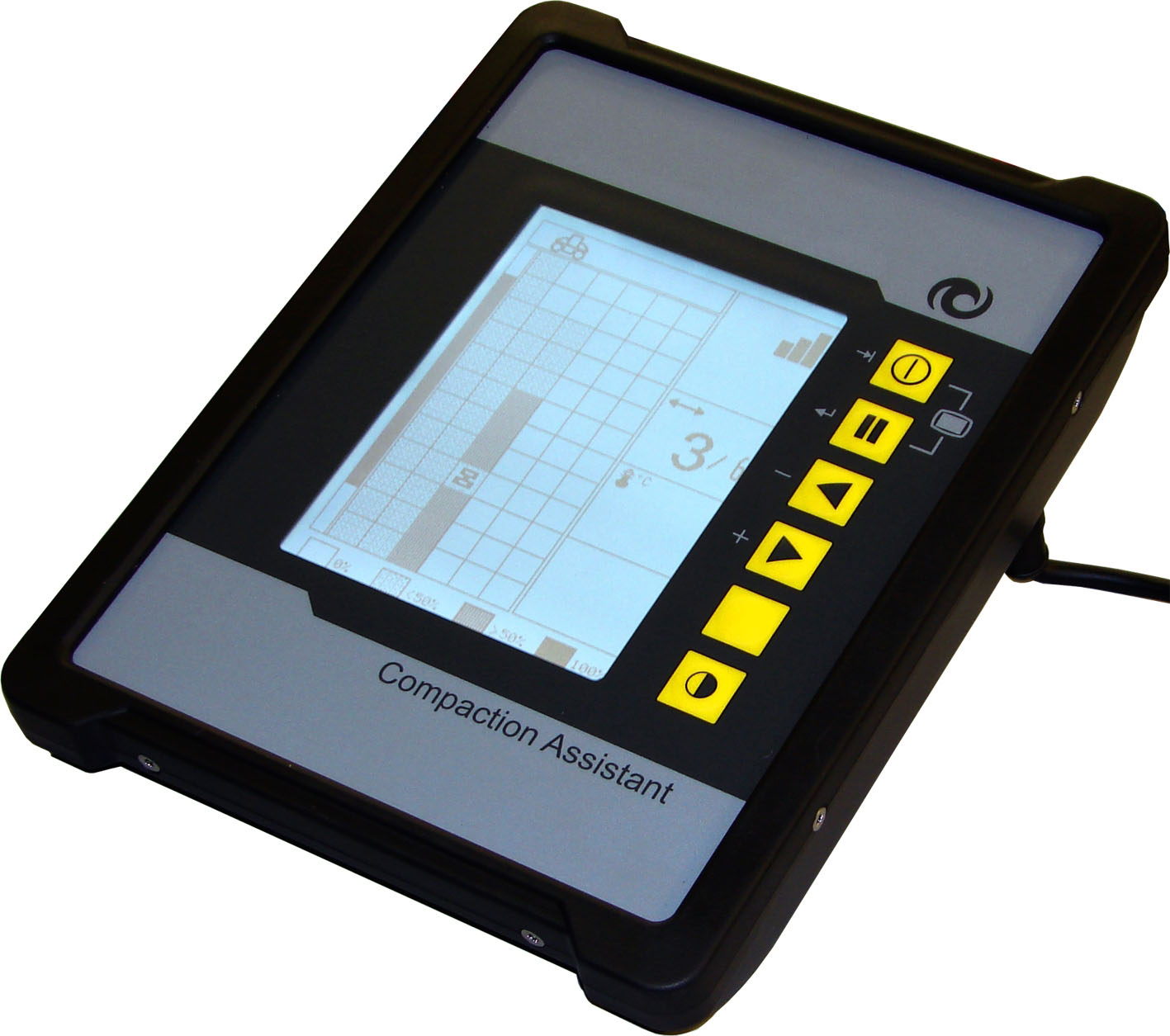
The new MOBA compaction control system can be fitted to any modern asphalt compactor
RSS
Clearly, ensuring that compaction is carried out to the required specification is vital to ensuring a surface will provide the design life and structural performance that is needed.
To help maximise compaction effect, various manufacturers have been fitting compaction meters for some time. These are designed to assess the quantity of compaction work carried out on the area under the drums and provide a guide to the operator as to whether this is sufficient to meet the specification. These use various systems to work and manufacturers are split into different groups on which concept is the most accurate or effective. Overall though, the intended result is the same: to show the operator what work needs to be done. And this is equally true for both soil compaction and asphalt compaction equipment.
The development of GPS and machine control technologies has further added to the benefits available. This allows a site to track the position of each machine and monitor the work carried out across the site. The data can be collected and stored, allowing information to be checked to ensure that work carried out meets specifications. In some operations, compaction data recorded at the machine is even being attached to the digital model of the operation, making it the article of record for the project. Various manufacturers such as6791 Ammann, 172 Bomag, 178 Caterpillar, 206 Dynapac and 228 Hamm have developed their systems for use on soil compactors. Some, like BOMAG and Hamm, have also developed technology with added heat sensing systems, for use in asphalt compaction. Meanwhile 1228 MOBA claims that its new package offers optimised material compaction. The MCA-1000 package is said to allow optimised material compaction in the construction of roads and tarmac surfaced areas. The system records the number of roller passes during the entire project and reconciles target and actual passes. This allows homogeneous compaction of materials, preventing future road damage and all data is shown on the colour display, while the system is designed to be fitted to all modern asphalt compactors. The MCA-1000 reduces operating costs and wear and tear on the machine, and ensures that the operator carries out work to requirements.
In addition, Trimble has added to its portfolio of machine control systems with its CC3900 system, a 3D package for use in asphalt operations. The CC3900 provides visual indications for the operator to roll a more efficient pattern, which Trimble says can lead to increased productivity and fuel savings. The system uses two optional IS310 infrared sensors mounted over the front and rear rollers to measure the temperature of the mat at the time of the compaction.
Temperature readings are relayed and graphically represented on an in-cab display dashboard, indicating which areas should be compacted immediately. Operators can also see the number of passes over a certain area and monitor where they have not overlapped properly or left gaps between passes. The entry-level pass count system can be deployed across the multiple asphalt compactors in a paving contractor’s fleet. Various upgrades such as temperature mapping, higher accuracy mapping, compaction value mapping and a larger display screen are also available. Like the MOBA package, the Trimble system can be fitted to up-to-date asphalt compaction machines from any supplier.
And BOMAG believes it is moving yet another step ahead, with its novel fleet management system, according to the firm. It is worth noting that the BOMAG TELEMATIC package can also be used in a mixed fleet with equipment from other manufacturers, in addition to BOMAG machines. The firm claims that this system allows contractors and rental companies to monitor and schedule service work for their machine fleets. The system makes it possible for operators to check machine location and operating data through the Internet.
Service intervals for all of the machines are saved in the system and a workshop manager can see which piece of equipment is due a service next. The machines can also be set to send an email automatically once they have reached the servicing deadline. This system plans and documents all service work, with the printout providing an overview of costs and operating hours for the machines. Where long standstill periods are identified, the firm can see if there is a problem with truck scheduling or with the machine for example. In addition, the package allows the contractor to invoice for services more quickly.RSS
Effective compaction control is one of a series of technical innovations boosting performance efficiency – Mike Woof writes
Maximising compaction efficiency can be a major cost factor on construction projects. Both for soil and asphalt compaction sectors, the risk from leaving an area under or over-compacted is substantial. Where surfaces are improperly compacted, early problems can occur with areas unable to provide the wear life or structural performance required.Clearly, ensuring that compaction is carried out to the required specification is vital to ensuring a surface will provide the design life and structural performance that is needed.
To help maximise compaction effect, various manufacturers have been fitting compaction meters for some time. These are designed to assess the quantity of compaction work carried out on the area under the drums and provide a guide to the operator as to whether this is sufficient to meet the specification. These use various systems to work and manufacturers are split into different groups on which concept is the most accurate or effective. Overall though, the intended result is the same: to show the operator what work needs to be done. And this is equally true for both soil compaction and asphalt compaction equipment.
The development of GPS and machine control technologies has further added to the benefits available. This allows a site to track the position of each machine and monitor the work carried out across the site. The data can be collected and stored, allowing information to be checked to ensure that work carried out meets specifications. In some operations, compaction data recorded at the machine is even being attached to the digital model of the operation, making it the article of record for the project. Various manufacturers such as
In addition, Trimble has added to its portfolio of machine control systems with its CC3900 system, a 3D package for use in asphalt operations. The CC3900 provides visual indications for the operator to roll a more efficient pattern, which Trimble says can lead to increased productivity and fuel savings. The system uses two optional IS310 infrared sensors mounted over the front and rear rollers to measure the temperature of the mat at the time of the compaction.
Temperature readings are relayed and graphically represented on an in-cab display dashboard, indicating which areas should be compacted immediately. Operators can also see the number of passes over a certain area and monitor where they have not overlapped properly or left gaps between passes. The entry-level pass count system can be deployed across the multiple asphalt compactors in a paving contractor’s fleet. Various upgrades such as temperature mapping, higher accuracy mapping, compaction value mapping and a larger display screen are also available. Like the MOBA package, the Trimble system can be fitted to up-to-date asphalt compaction machines from any supplier.
And BOMAG believes it is moving yet another step ahead, with its novel fleet management system, according to the firm. It is worth noting that the BOMAG TELEMATIC package can also be used in a mixed fleet with equipment from other manufacturers, in addition to BOMAG machines. The firm claims that this system allows contractors and rental companies to monitor and schedule service work for their machine fleets. The system makes it possible for operators to check machine location and operating data through the Internet.
Service intervals for all of the machines are saved in the system and a workshop manager can see which piece of equipment is due a service next. The machines can also be set to send an email automatically once they have reached the servicing deadline. This system plans and documents all service work, with the printout providing an overview of costs and operating hours for the machines. Where long standstill periods are identified, the firm can see if there is a problem with truck scheduling or with the machine for example. In addition, the package allows the contractor to invoice for services more quickly.RSS