Twin-layer paving offers high quality, long lasting road surfaces to be constructed. Paver manufacturer Dynapac is one of the pioneers of the twin-layer paving technique, which it calls Compactasphalt. According to Dynapac this method offers major benefits to contractors and clients alike as roads surfaced using this technique last longer and are cheaper to maintain. To ensure contractors have maximum utilisation of their machines, Dynapac offers a modular paver system that can be operated using the convent
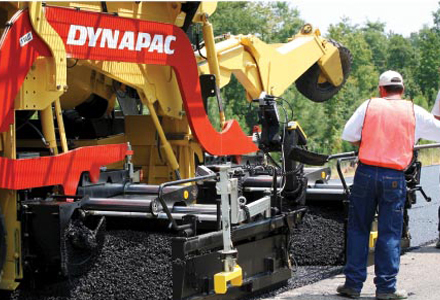
Twin-layer paving offers high quality, long lasting road surfaces to be constructed
Paver manufacturerThe twin layer paving method offers a radical solution to pavement quality and was patented in 1993 by Professor Elk Richter, Erfurt, Germany.
The method involves the binder and the wearing course being applied to the loadbearing layer one after the other in a single pass. This contrasts with conventional roadbuilding, which involves two separate passes and where the wearing course is applied after the binder has cooled. A requirement is that you can not drive over the uncompacted binder course before the wearing course is laid. After 15 years of test results, the method is now officially approved in Germany and included in the official ZTV Asphalt Regulations. Professor Richter's twin layer technique was developed as a solution to the shortcomings of conventional paving methods, which are particularly acute in bad weather. Using double layer paving can cut surfacing time in half and help to reduce highway traffic jams while there are several technical benefits. This method makes use of the heat in the thick binder layer that has just been laid to gain time for the compaction of the two upper layers, a major benefit when paving in poor weather conditions.
With the conventional paving method, the binder layer can cool before the wearing course is applied and in cool weather this may lead to uneven and insufficient compaction.
Good compaction of the asphalt layer is crucial but rollers take time to do their job properly. The cooling of the asphalt reduces the degree of compaction and with it the durability of the road surface.
According to Roland Egervári, paver product specialist at Dynapac, "By laying the binder and the wearing course at the same time we apply 12cm of asphalt in one pass. Because the asphalt is thicker, the useful compaction time is extended by a factor of at least seven." He added that this is particularly useful for roadbuilding in bad weather, when the asphalt temperature falls rapidly.
As the two layers are applied hot-on-hot, the twin layer method also makes it possible to reduce the thickness of the uppermost layer to 20mm, as opposed to 40mm with the conventional method. Wearing course mixes are costly so reducing the quantities of material required presents substantial savings for the contractor and client. Compared with conventional paving methods, the double layer also gives better bonding between the individual layers, helping to prevent crack formation in the road surface.
Road surfaces made of properly compacted asphalt last longer and on average, the loadbearing layer will need to be replaced after 40-50 years, the binder layer after 15-25 years and the wearing course after 10-15 years. This means that the wearing course will need replacing at least once during the normal service life of a binder layer.
However Johan Arnberg, vice president paving & recycling at
With this method we can extend the service life of a wearing course substantially, under certain conditions even to match that of the binder layer. So over the entire lifecycle of a road, the operator could save one complete re-laying every 25 years."
Evaluation of a long-term trial with Compactasphalt on a stretch of road in Alabama, USA, provides strong evidence of the method's benefits. The trial stretch, built with a Dynapac paver, was driven over continuously by 60tonne trucks, simulating an 18 year service life in just two years but despite this hard test the section showed no signs of fatigue in the form of tracks or cracks. According to Dynapac the result further reinforces the cost benefits of twin layer paving for the life of a roadway. "The long-term maintenance of a road is an important cost factor for the owner," explained Egervári.
There are other benefits too, with deformation problems being minimised due to the more homogenous densities achieved in the wearing course and binder course while properties such as skid-resistance are extended. As the system reduces mix temperatures it helps cut emissions, while lowering the mix temperature by 10°C will save around 0.23litres of heating/tonne of material according to Dynapac. In addition, the greater durability of the wearing course also saves energy costs as there is a reduced need for road repairs and maintenance works. Another saving comes from removing the need for bitumen emulsion, which is sprayed on the binder layer for conventional paving methods.
And by reducing the thickness of the asphalt binder course from 100-80mm, substantial savings in material costs can be achieved.
The technique is now well proven and by the end of 2007, Dynapac machines had laid 5,000,000m² of compacted asphalt in Germany, China, Poland and Russia. In Germany, Dynapac has supplied three large F300CS pavers in the Compactasphalt specification.
The firm is continuing to develop its technology too and is launching a modular Compactasphalt TP2500 extension to be used with their standard DF145CS paver for smaller working widths. This will allow contractors to use Compactasphalt paving techniques on regular roads and at a lower cost than with Dynapac's much larger F300CS system. The contractor can adapt the DF145CS paver quickly to the Compact asphalt specification when required and can use it in standard trim for more general paving duties.
This will offer further cost benefits for contractors and clients.
For the Compactasphalt specification, Dynapac's proven F300CS paver features two hopper modules to hold the materials for the binder layer and the wearing course. The machine also has two screeds; a high-density screed for the binder layer and a conventional screed for the wearing course. The screeds are adjusted relative to each other to ensure that the paved thickness of the two layers is constant and in this form the machine can pave a maximum width of 13M.The new TP2500 module+paver is suitable for working widths of 2.55-7.5m. This smaller class is more versatile and more common and the firm expects to see strong demand for the unit in the Compactasphalt specification.