Improved surface quality and improved machine design are key trends in the asphalt paving sector, Mike Woof reports There is a big difference in asphalt paving techniques in North America and Europe. In North America, the need to construct long stretches of highway quickly resulted in wide pavers offering high throughput capacity, with compaction equipment then being used to achieve the required density of the various courses. In Europe's highway construction projects, distances tend to be shorter and contr
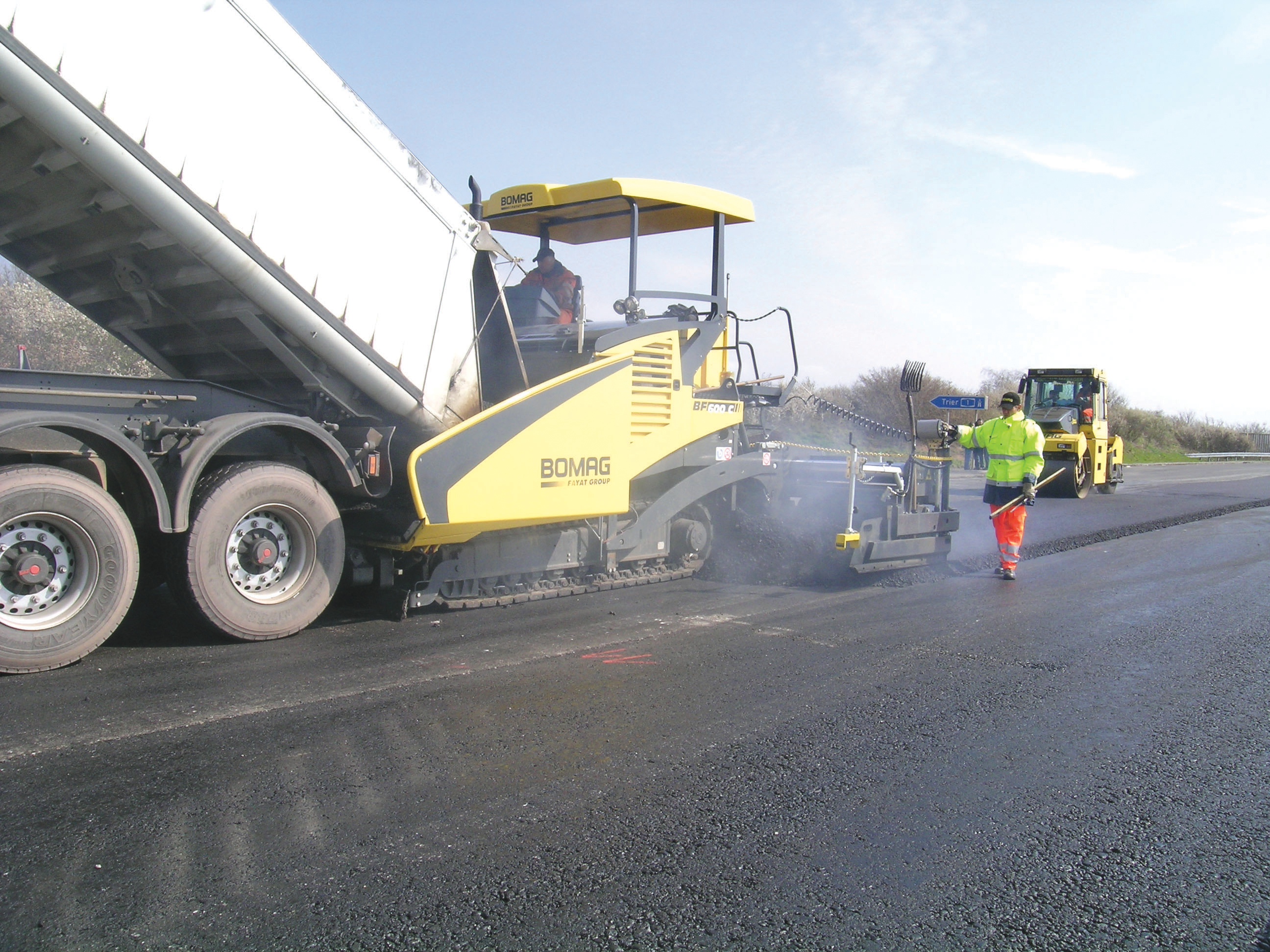
BOMAG has won a red dot prize for product design for the BF600C and the company points out that this is its third new product to have won a major award this year
Improved surface quality and improved machine design are key trends in the asphalt paving sector, Mike Woof reports
There is a big difference in asphalt paving techniques in North America and Europe. In North America, the need to construct long stretches of highway quickly resulted in wide pavers offering high throughput capacity, with compaction equipment then being used to achieve the required density of the various courses. In Europe's highway construction projects, distances tend to be shorter and contractors prefer pavers fitted with screeds that not only lay asphalt but are able to offer a degree of compaction as well.Both the
Larry Jack, Head of
Customers have a choice of a light or heavyweight screed, as well as electric or gas heating. The high performance screed is aimed at European style paving needs and is able to deliver pre-compaction of up to 93%. Four heating elements/screed segments are fitted while a heavy duty generator reduces the time needed to reach operating temperatures. Other screed features include fully automated temperature control, function monitor, an automatic screed control system and a potentiometer for fine adjustment of the screw-type sensors which can be operated from both control consoles.
To minimise fuel consumption, the BF600 features the ECOMODE engine management system with auto-idle technology and combined with the load-sensing hydraulics, this helps lower running costs for the user. Access to the engine and hydraulics for maintenance is said to be good, cutting service times while long service intervals help keep running costs low.
Meanwhile recent screed developments from
The new VB510/EB51 offers working widths from 2.55-5.1m using its hydraulic extension, while mechanical extensions allow a maximum working width of 8.8m.The larger VB600/EB60 can be hydraulically extended from 3-6m, while the use of mechanical extensions allow a maximum working width of 9.7m.
Larger, 380 mm-deep sole plates on both models ensure an even surface and can be specified in Hardox 500 to further extend service life. The sole plates are separate units, making them easier to handle should they need replacing. As before, gas or electric heating systems can be specified. The gas-heated models benefit from improved ventilation due to new air ducts for the tamper meters and baffle plates, while the electric screeds feature new heating elements arranged in a winding pattern. For both screeds the new design is said to provide more uniform heat distribution across the sole plates. Meanwhile, the patented design of screed, torsion housing and telescoping components, which are connected using stiff guide tubes, delivers high torsion resistance. The guide bushings for the force and torque intake are adjustable and will last for the lifespan of the screed according to Dynapac. Even with the screed fully extended, the guide tubes are only expanded to 50% and the firm says that this means that there is no need for screed stabiliser bars, even when using mechanical extensions.
The fixing points for the screed's digital and remote controls are now at the same height, improving control ergonomics for the operator. Pavers featuring Dynapac's proven SPS system come with additional remote control features for material distribution, such as changing the direction of auger rotation or levelling units that can be individually selected from all finisher sides. The height and tilt settings for the limiting plate have been simplified and all settings can be made using a single crank lever. The screed can be set to different mounting sizes using the quick adjustment system without the use of tools.
Working at night is becoming increasingly important given the restriction on daytime working and the need to carry out paving at off-peak hours, with more and more pavers being made available with comprehensive lighting systems.
Visibility for the operator has become another important design trend, with low mounted engines offering better sightlines to the hopper for instance. Roadtec says that the seat design on its latest paver models for the North American market maximises visibility of the rear augers. Paver operators have to quickly visually check the rear auger of their machine to make monitor material levels as this will aid in providing a quality paving job. As a result, Roadtec engineers designed the seats to slide out to the side in a straight line instead of swinging out on an arc. The straight sideways movement of the seat provides the operator with high visibility down the side of the machine and also to the rear augers. This allows the operator to check that the mix is halfway up on the augers over the entire width of the delivery system. Augers should never be buried in mix at any point. Augers should never be raised too high because this could cause mix to push forward under the paver. Too much or too little material around the auger will result in problems in the paved surface. Paving speed, flow gate settings, and feed sensor position regulate material flow. Being able to easily see the augers allows the operator to monitor these variables and to deliver mix evenly across the augers and thus across the entire leading edge of the screed plate, which is important for a segregation-free mat.
Versatility is the key to Vögele's latest paver designs. The conventional SUPER 1800-2 can be fitted with the firm's SprayJet Module, which allows bitumen emulsion to be sprayed and the asphalt wearing course to be paved in a single pass. This equipment is suited for paving thin overlays on spray seal, hot on hot, however it can also provide an economical and clean alternative wherever spraying of tack coat and subsequent paving are required. The SprayJet Module can be removed easily and quickly as well, allowing the machine to be used for conventional paving operations. The module features a large, heated emulsion tank holding a maximum of 2,000litres and five spray bars positioned at the front, the sides and the rear of the SUPER 1800-2. An electronic control system allows the spread rate to be precisely metered, saving materials and minimising spray mist.
The machine is equipped with Vögele's ErgoPlus operating system and the operator only needs to select the rate of spread. Spray pressure as well as emulsion volume are adjusted automatically to the pave speed and pave width. Compressed air reservoirs are fitted to the paver to pressurise the five spray bars, each of which has 20 self-sealing spray nozzles. The spray bars are positioned so that the emulsion film being spread cannot be damaged by the paver's tracks. The design of the spray nozzles and the constant spraying pressure allow uniform operation, making it possible to spray along road kerbs without getting emulsion on the kerb. The SprayJet Module also allows a rate of spread to be selected from 0.2-1.5kg/m2, depending upon the type of emulsion used, the viscosity and the temperature when applied. This allows working paving speeds from 2-20m/minute.
The SUPER 1800-2 with SprayJet Module also features the firm's AB500-2 extending screed, allowing paving widths up to 5m. The screed is offered with tamper and vibrators and with tamper and one pressure bar and features electric heating.
The firm has also developed a special SP250B screed for use with concrete. This paver-compacted concrete (PCC) screed can pave depths of up to 300mm and from 7-7.5m wide and Schug said that unlike conventional roller-compacted concrete (RCC) equipment from other firms, "You don't need a roller working behind it."
Quality is crucial
Some of Caterpillar's competitors focus on the use of materials transfer machinery as a means of minimising segregation in the asphalt mix as well as optimising the temperature gradient across the mat, allowing the paver to deliver a smoother surface. However, Sharp said that contractors can achieve a similar quality surface through efficient use of the paver instead. "Our view is that the contractor doesn't need specialised machines and we focus on technique." For those contractors who prefer using a materials transfer machine (or who have to employ one to meet the written demands of a specification), Caterpillar's dealers can howeversupply the Wyler materials transfer vehicle as the firms have a partnership arrangement.
Surface smoothness is the target for all good paving operations and Jeffrey Voelz, Solutions and Services Consultant for Global Paving said, "Smooth roads last longer," while Sharp added, "It pays off twice, as the road lasts longer and the public sees a difference in ride quality." Sharp said that the high productivity paving in the US does place a focus on consistency, "Some people put down 4-5,000tonnes/day and it's got to be smooth as there is no chance to redo it." The company is looking ahead with regard to future paving techniques and Voelz continued, "We're close to the DoTs here and we're experimenting with warm mix though it's hard to beat hot mix and Superpave." Sharp added that with the competitive price of concrete, some contractors are also considering the use of roller compacted concrete (RCC). He said, "You can spread it with an asphalt paver or a concrete paver or a placer." Training is a key focus for the
Double layer paving Hot on hot paving techniques have been in trials for many years and there have been various attempts to market this technology in the past. However it is only in recent years that two manufacturers, namely Dynapac and Vögele, have developed reliable and practical production solutions. (There is a Japanese hot on hot paving system as well, but this has not been seen outside of the country and little is known about the technology at present.) Numerous trial stretches of hot on hot paving have now been laid using the Dynapac and Vögele equipment in countries including Germany, the Netherlands and the US. As data on the performance of these surfaces is gathered, the benefits will be examined closely in real working applications and specifications can be determined.
Using hot on hot technology provides a strong bond between the binder course and the wearing course, increasing its strength and reducing the risk of early failure. This technology is said to offer a highly cost-effective method for building long-lasting road pavements. During paving the double layer retains its heat well, allowing more time for compaction and for both the Dynapac and Vögele systems, a material transfer vehicle is required to carry the binder material to the paving equipment. However there are important differences between the Dynapac and Vögele systems and the type of compaction required Dynapac's concept is based around a single, highly modified paver equipped with two hoppers and screeds, for the binder course and wearing course respectively. Compaction is then carried out, with the first passes using a modified twin drum roller with extra wide drums, and then by conventional twin drum units. The Vögele system uses two pavers, which have been modified for the purpose. The key feature of the first unit, a SUPER 2100-2, used to lay the binder course is its special high compaction screed. This compacts the binder course sufficiently for the second paver, either a SUPER 1800-2 or a SUPER 1600-2, laying the wearing course to operate on the hot surface without the track problems. Because of the high compaction screed on the first machine there is no need for a roller to operate in between the two pavers and after the second has laid the wearing course, conventional twin drum compaction machines can then be used. Both Dynapac and Vögele say their machines can also be converted back to standard configuration for more conventional duties if required.
Vögele's twin layer, in-line paving system has now been used to resurface some 1,500,000m2 of road surface. The firm's Marketing Manager, Roland Schug said, "We started at the beginning of 1996. We've tried with 10 different construction firms and we've had a wide range of experience. In-line paving is hot on hot as the binder course and the wearing course are applied in one pass. The centrepiece is the screed as you need pre-compaction of the binder layer. The 2100-2 is fitted with a high compaction screed that offers 97-98% compaction and sometimes we've achieved 100%." The twin layer paving technique allows the contractor to apply a thinner wearing course, reducing the thickness from 40-20mm, delivering major savings in material costs according to Schug. "We've done calculations and if you compare compact asphalt with conventional techniques over a 4.5km stretch it saves €60,000. We believe compact asphalt has a big potential for the future."