Sophisticated dual layer paving technologies currently on the market are said to offer major advantages to road builders. Roads built using twin layer, hot on hot paving techniques can last considerably longer than those constructed using conventional methods.
Contractors and clients also stand to gain from savings on materials costs, through the elimination of the need for emulsion spraying between binder and wearing courses and with the use of thin layer wearing course designs. At present two paver man
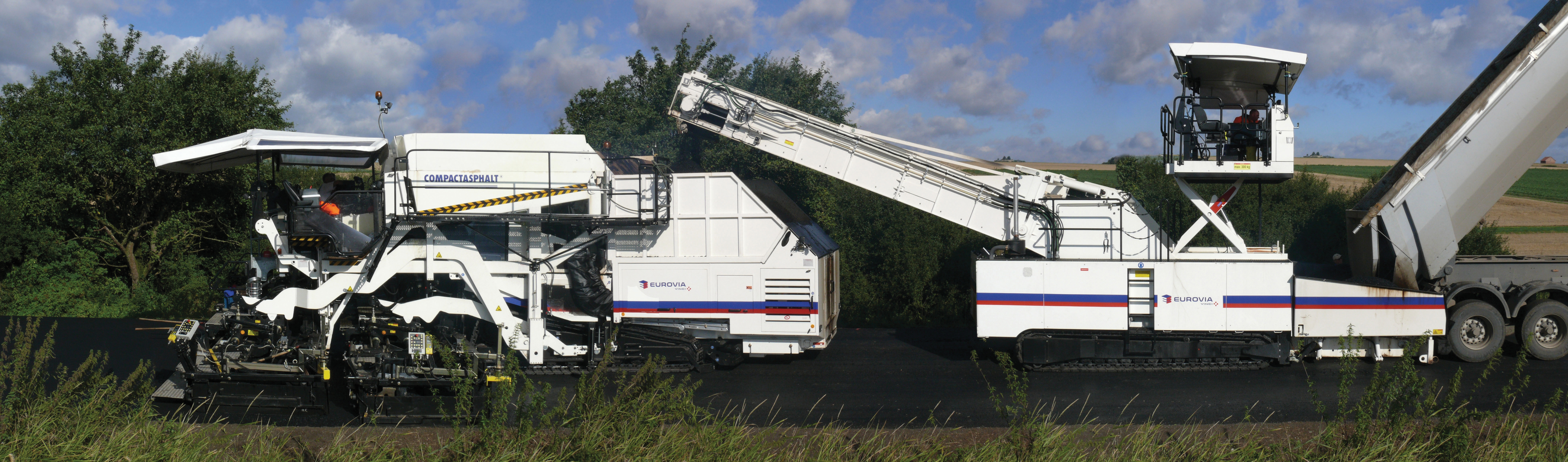
The newer Dynapac duel layer paving system is more compact and versatile than the original equipment and is also based on a standard machine that can be more quickly converted for standard duties
Dual layer paving technology offers major benefits to contractors and clients alike, Mike Woof reports
Sophisticated dual layer paving technologies currently on the market are said to offer major advantages to road builders. Roads built using twin layer, hot on hot paving techniques can last considerably longer than those constructed using conventional methods.Contractors and clients also stand to gain from savings on materials costs, through the elimination of the need for emulsion spraying between binder and wearing courses and with the use of thin layer wearing course designs. At present two paver manufacturers,
Roland Egerväri is in charge of sales support worldwide for Dynapac's dual layer paving system, the Compactasphalt range. He said that there is a major need for the use of new paving technologies such as the Compactasphalt system to cope with growing traffic volumes on the world's roads and Egerväri said, "We have increased traffic and axle loads." Thin wearing course road designs are desirable because these allow for reduced materials usage and help lower paving costs.
However, this system leaves less time for compaction when conventional paving methods are used as the mat cools more quickly. He said, "There is a correlation between the time available for compaction. The thin layer cools too fast for compaction but not with dual layer asphalt paving." The dual layer system however offers a major benefit, by allowing the use of a thin wearing course laid directly on top of the binder layer.
This twin layer method retains heat more effectively than a single layer and as a result, helps extend the paving season through the year (as paving operations can be carried out in temperatures down to 0°C), while also providing a much better interlock between the two asphalt courses. As two layers are laid at the same time, this reduces the length of the paving component of a job and Egerväri said, "You halve the paving time with Compactasphalt." He continued, "The main goal is to prolong the life of the top layer.
It's the most costly as it's made of the most costly materials." As the interlock between the wearing course is much stronger, Egerväri said that the wearing course of a road paved using dual layer techniques will also last longer. Using conventional technology, a properly paved wearing course will last 10-15 years, while the binder course will last 15-25 years. However, using the dual layer system Egerväri said that the wearing course will last as long as the binder layer, 15-25 years, providing considerable cost savings over the life of the road. He said, "You halve the cost of the wearing course material and there is no need to spray emulsions between the binder course and the wearing course." He said that this technology provides a resistance to deformation and thermal distortion.
According to Egerväri, moderate compaction of the binder course of around 92% is key to an effective interlock with the wearing course. He said, "For Compactasphalt we use a feeder and the hopper in the conventional position is used for the binder while the raised top hopper holds the wearing course." A special wide drum roller is used.
The newer Dynapac dual layer paving system is more compact and versatile than the original equipment and is also based on a standard machine that can be more quickly converted for standard duties immediately after the Dynapac dual layer paving system, with conventional compaction equipment then carrying out the final passes.
The development of the Compactasphalt system dates back to the early 1990s and Dynapac unveiled an improved system in 2004 capable of paving widths of up to 13.5m.
However, this was considered too large and too specialised and the firm later developed the current machine, which is based on a DF145CS machine and is capable of paving widths from 3.75-7.5m. He explained, "The main task of the top layer is to make the whole system waterproof and give a good running surface with sufficient skid resistance and you have the highest bitumen content but the lowest resistance to deformation." Using the twin layer paving system allows for other benefits for the contractor and client too as it delivers a better profile while reducing the size of the paving crew required. Tests carried out in the US at the NCAT test facility in Alabama showed that a dual layer surface could last a simulated 25 year traffic load. He said that over a 30 month trial period at the test facility the paved surface showed no signs of deformation, despite carrying 10 million axle loads in this time. The reduced time for paving work using twin layer technology brings other benefits and he added, "You can also release a road to traffic much earlier." Although Dynapac's dual layer system is innovative, it has also been well proven according to Egerväri. He said that apart from the US test facility, it has been widely used on stretches of German highways as well as in India and China. Sections of the A1 autobahn linking the German cities of Bremen and Hamburg, which features some of the highest volumes of heavy truck traffic anywhere in Europe, are being paved using Compactasphalt, in a bid to extend the working life (other stretches feature a concrete surface, again for longevity).
The firm has developed a sophisticated software package to calculate the benefits of Compactasphalt and which contractors and clients can employ to see the advantages of working life and cost the system can deliver.
Meanwhile Vögele also intends to boost use of its rival InLine Pave technology, which also offers dual layer paving capabilities. The company has supplied equipment to contractors that has been used on a variety of operations, particularly in Germany. German contractor Kemna Bau Andreae has used its Vögele paving machinery to carry out a hot on hot process on the B95 federal road close to the city of Leipzig.
Maintaining truck transport of materials alternating between binder and wearing course grades is crucial for effective dual layer, hot on hot paving processes of Rötha and close to Leipzig was in major need of repair over a 4.7km stretch. The project was divided into four sections, three of which were rebuilt using the novel dual layer paving system, while on the fourth, the work was carried out using conventional techniques as the binder course was still intact.
The Vögele InLine Pave train was employed for a road surface rehabilitation of the busy B95 link. The Vögele hot on hot paving method centres on a specially configured SUPER 2100-2IP paver for the binder course, which is equipped with the TP2 Plus version of the firm's AP600-2 extending screed, to allow the necessary precompaction.
The machines used for the InLine paving system are all based on standard units but with modifications, which allow them to carry out the specialised processes. The SUPER2100-2IP is the key to the job due to its specially modified, high compaction screed. To achieve the necessary 98% pre-compaction of the binder course the TP2 version of the AB600-2 screed was used. This features altered tamper stroke lengths, a special tamper geometry and special pulsed-flow hydraulics with two pressure bars for high compaction. This is said to provide sufficient compaction of the binder course so that the second paver can operate directly behind on the newly laid mat without risk of sinking into the hot surface and also without the need for the use of rollers in-between the two pavers. Fitted with two 1.25m bolt-on extensions for this job, the screed was used to pave the full road width on this job.
The Super 1800-2 paver that lays the wearing course is a standard machine and its only special feature is a control system that ensures it maintains an optimum distance from the paver operating in front, to prevent bumping and also eliminate the risk of it operating too far away from the first machine. Meanwhile the MT1000-1 material transfer vehicle is also a standard unit.
Utilisation of the machines is said to be high as they can be used for conventional paving processes with only minimal adjustments required.
The machines are conventional to operate and an experienced paving crew needs only a relatively short training programme to understand the process. However, a key factor for hot on hot paving is the need for efficient logistics on-site. A reliable supply of trucks transporting both binder and wearing course materials is crucial.
For this job the contractor was able to slow the paving speed slightly, so as to better match the material delivery rates from trucks carrying either the binder or the wearing course.
However, as the entire binder and wearing course paving job could be carried out in a single pass with roller compaction then following, the overall construction time for the B95 project was actually reduced.