A German contractor is now using two novel asphalt paving technologies from Vögele together for key projects
The firm has acquired Vögele’s InLine Pave equipment with its innovative dual layer paving technology as well as one of the SUPER 1800-3i SprayJets for paving a surface course.
This combination of technologies is allowing contractor Rask Brandenburg to carry out fast and efficient road rehabilitation work on some major routes, including a busy Autobahn stretch leading into capital Berlin.
T
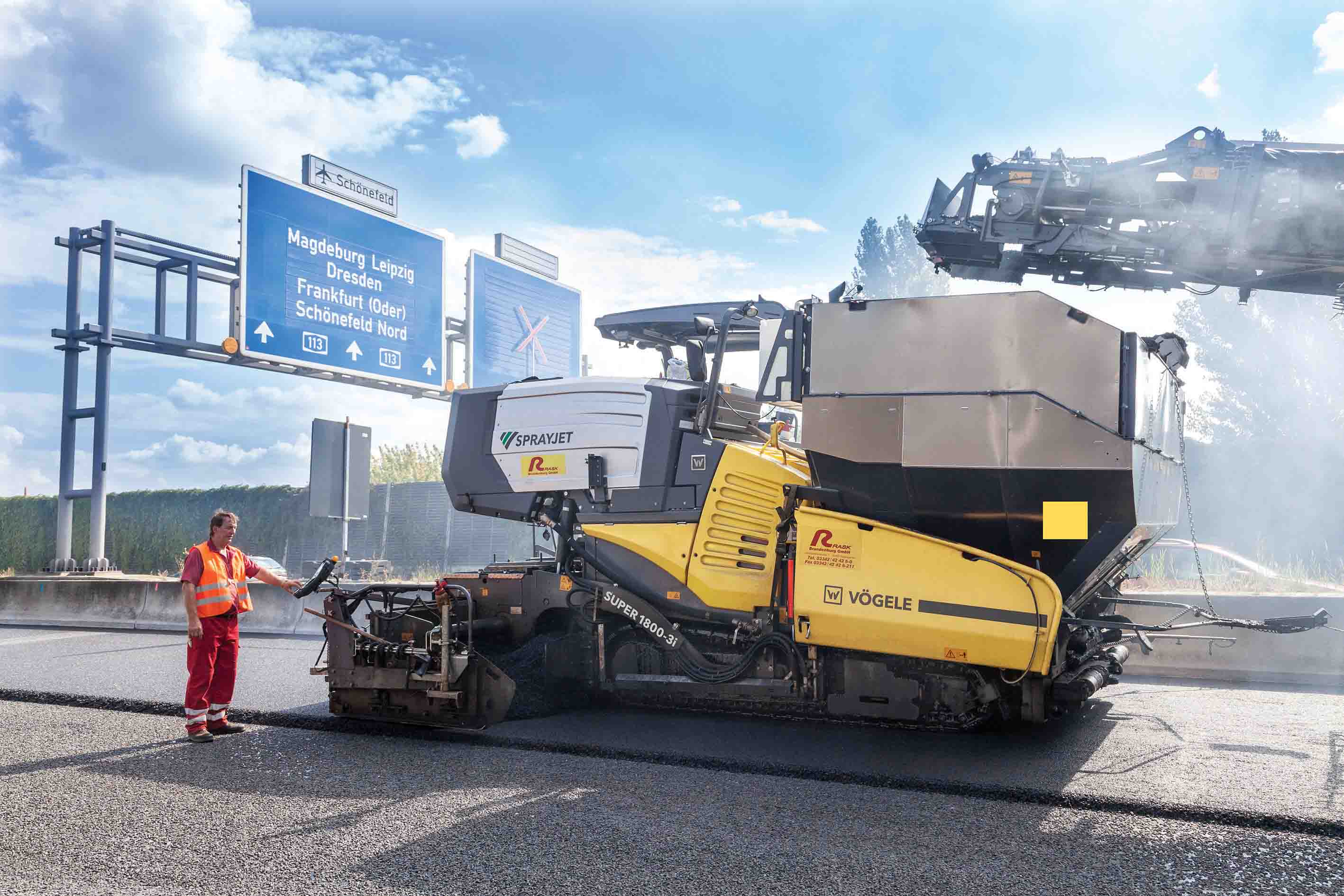
The busy A113 handles traffic for Berlin’s busy Schönefeld airport
A German contractor is now using two novel asphalt paving technologies from Vögele together for key projects
The firm has acquired1194 Vögele’s InLine Pave equipment with its innovative dual layer paving technology as well as one of the SUPER 1800-3i SprayJets for paving a surface course.
This combination of technologies is allowing contractor Rask Brandenburg to carry out fast and efficient road rehabilitation work on some major routes, including a busy Autobahn stretch leading into capital Berlin.
The hot-on-hot dual layer (inline) paving technology allows for a very strong bond between the binder layer and thin layer wearing course, boosting wear life and cutting materials costs. The stronger bond allows high performance from thin wearing courses, lowering materials costs for this high grade asphalt. A further cost saving comes from eliminating the need for an emulsion layer and the technique can offer a very long-lasting and effective paving solution as a result.
The Vögele system of dual layer paving uses two pavers, with one following immediately after the other. The first paver lays the binder layer and then uses a special high compaction screed to ensure that the surface has reached sufficient density for the second machine to run directly on top, without its tracks causing deformation. Following behind, the second paver lays the wearing course, with sensors making sure that it does not touch the first machine. Meanwhile a material transfer vehicle runs in front of both pavers and supplies asphalt continuously to both machines, with an additional feed belt mounted on the first paver to carry the wearing course material to the second.
This technique can be used to build new highways as well as to rehabilitate existing roads, with the paving being carried out directly onto a freshly milled road surface. The technique allows quicker construction as the two layers are paved together, reducing traffic disturbance on busy routes. However this method also requires more efficient logistics so as to ensure the two materials are delivered to the pavers on time.
Meanwhile Vögele has also developed an efficient system for paving thin overlays with its latest SprayJet machines. And German contractor Rask Brandenburg has also invested in this technology so that it can offer a wider range of paving and road repair solutions.
The machines behind these modern methods of road rehabilitation are the SUPER 1800-3i SprayJet paver (for thin overlay) and the Vögele InLine Pave train (for compact asphalt pavements). The latter comprises a Vögele MT 3000-2i Offset PowerFeeder, a SUPER 2100-3i IP for placing binder course and another Vögele paver for the surface course. Bernd Malcharek, president of Rask Brandenburg explained that having these two technologies in its fleet allows the firm to handle a wider array of road repairs. Rask Brandenburg can take on conventional paving jobs, as well as being able to pave thin overlays and dual layer work.
The firm is already making extensive use of this equipment. Within just a few weeks after shipment, the SUPER 1800-3i SprayJet had already clocked 600 operating hours on spray paver jobs and using the hot-on-hot InLine Pave technology.
For the dual layer method the binder and surface courses are paved in a single pass, so the two Vögele pavers work in line with just a few metres between them and one lane can remain open to traffic. Rask Brandenburg is using a Vögele MT 3000-2i Offset PowerFeeder with pivoting conveyor and automatic distance control to ensure a continuous supply of material, allowing the paver operators to concentrate entirely on the paving work.
The key component of the InLine Pave process is the SUPER 2100-3i IP for placing binder course. This machine has an entirely redesigned transfer module with a heated conveyor system that has been extended by 1m. It transfers the mix for the surface course to the downstream paver. At a defined point, the new transfer module can easily be removed, a feature that boosts utilisation and allows the contractor to handle conventional jobs with the same machine. A further modification is that the height of the seats on the two operator's platforms can now be adjusted hydraulically, providing a better view of the working area.
Equipped with an AB 600 TP2 Plus Extending Screed, the SUPER 2100-3i IP places a highly compacted binder course and the surface course paver can travel over it without rolling. The firm has developed innovative high compaction technology due to its novel pulsed-flow hydraulics. In this step, the asphalt is pre-compacted during paving by a tamper and two pressure bars.
To meet Rask Brandenburg’s requirements, Vögele adapted the technology on the SUPER 1800-3i SprayJet to allow the machine to take over the job of paving the surface course in the InLine Pave train (but not in spray mode).
For spray applications, the paver is equipped with a removable SprayJet module, which enables it to simultaneously pave and accurately spray the emulsion.
The InLine package has been used successfully by Rask Brandenburg for the A 113 Autobahn in Berlin. The paving train rehabilitated several stretches of the busy route that totalled 2km in length and were opened to traffic on schedule.
The firm has acquired
This combination of technologies is allowing contractor Rask Brandenburg to carry out fast and efficient road rehabilitation work on some major routes, including a busy Autobahn stretch leading into capital Berlin.
The hot-on-hot dual layer (inline) paving technology allows for a very strong bond between the binder layer and thin layer wearing course, boosting wear life and cutting materials costs. The stronger bond allows high performance from thin wearing courses, lowering materials costs for this high grade asphalt. A further cost saving comes from eliminating the need for an emulsion layer and the technique can offer a very long-lasting and effective paving solution as a result.
The Vögele system of dual layer paving uses two pavers, with one following immediately after the other. The first paver lays the binder layer and then uses a special high compaction screed to ensure that the surface has reached sufficient density for the second machine to run directly on top, without its tracks causing deformation. Following behind, the second paver lays the wearing course, with sensors making sure that it does not touch the first machine. Meanwhile a material transfer vehicle runs in front of both pavers and supplies asphalt continuously to both machines, with an additional feed belt mounted on the first paver to carry the wearing course material to the second.
This technique can be used to build new highways as well as to rehabilitate existing roads, with the paving being carried out directly onto a freshly milled road surface. The technique allows quicker construction as the two layers are paved together, reducing traffic disturbance on busy routes. However this method also requires more efficient logistics so as to ensure the two materials are delivered to the pavers on time.
Meanwhile Vögele has also developed an efficient system for paving thin overlays with its latest SprayJet machines. And German contractor Rask Brandenburg has also invested in this technology so that it can offer a wider range of paving and road repair solutions.
The machines behind these modern methods of road rehabilitation are the SUPER 1800-3i SprayJet paver (for thin overlay) and the Vögele InLine Pave train (for compact asphalt pavements). The latter comprises a Vögele MT 3000-2i Offset PowerFeeder, a SUPER 2100-3i IP for placing binder course and another Vögele paver for the surface course. Bernd Malcharek, president of Rask Brandenburg explained that having these two technologies in its fleet allows the firm to handle a wider array of road repairs. Rask Brandenburg can take on conventional paving jobs, as well as being able to pave thin overlays and dual layer work.
The firm is already making extensive use of this equipment. Within just a few weeks after shipment, the SUPER 1800-3i SprayJet had already clocked 600 operating hours on spray paver jobs and using the hot-on-hot InLine Pave technology.
For the dual layer method the binder and surface courses are paved in a single pass, so the two Vögele pavers work in line with just a few metres between them and one lane can remain open to traffic. Rask Brandenburg is using a Vögele MT 3000-2i Offset PowerFeeder with pivoting conveyor and automatic distance control to ensure a continuous supply of material, allowing the paver operators to concentrate entirely on the paving work.
The key component of the InLine Pave process is the SUPER 2100-3i IP for placing binder course. This machine has an entirely redesigned transfer module with a heated conveyor system that has been extended by 1m. It transfers the mix for the surface course to the downstream paver. At a defined point, the new transfer module can easily be removed, a feature that boosts utilisation and allows the contractor to handle conventional jobs with the same machine. A further modification is that the height of the seats on the two operator's platforms can now be adjusted hydraulically, providing a better view of the working area.
Equipped with an AB 600 TP2 Plus Extending Screed, the SUPER 2100-3i IP places a highly compacted binder course and the surface course paver can travel over it without rolling. The firm has developed innovative high compaction technology due to its novel pulsed-flow hydraulics. In this step, the asphalt is pre-compacted during paving by a tamper and two pressure bars.
To meet Rask Brandenburg’s requirements, Vögele adapted the technology on the SUPER 1800-3i SprayJet to allow the machine to take over the job of paving the surface course in the InLine Pave train (but not in spray mode).
For spray applications, the paver is equipped with a removable SprayJet module, which enables it to simultaneously pave and accurately spray the emulsion.
The InLine package has been used successfully by Rask Brandenburg for the A 113 Autobahn in Berlin. The paving train rehabilitated several stretches of the busy route that totalled 2km in length and were opened to traffic on schedule.