German paver specialist Vögele is taking a global view of the construction equipment market, with machines developed for very different markets. A prime example of this is with the Dash 3 models now coming to market. The new SUPER 2100-3 paver is also available as the SUPER 2100-3i, a highly sophisticated machine that meets the European emissions requirements while offering high productivity and performance. At the same time, the company is also offering a heavy duty (HD) version of its proven SUPER 1800-2
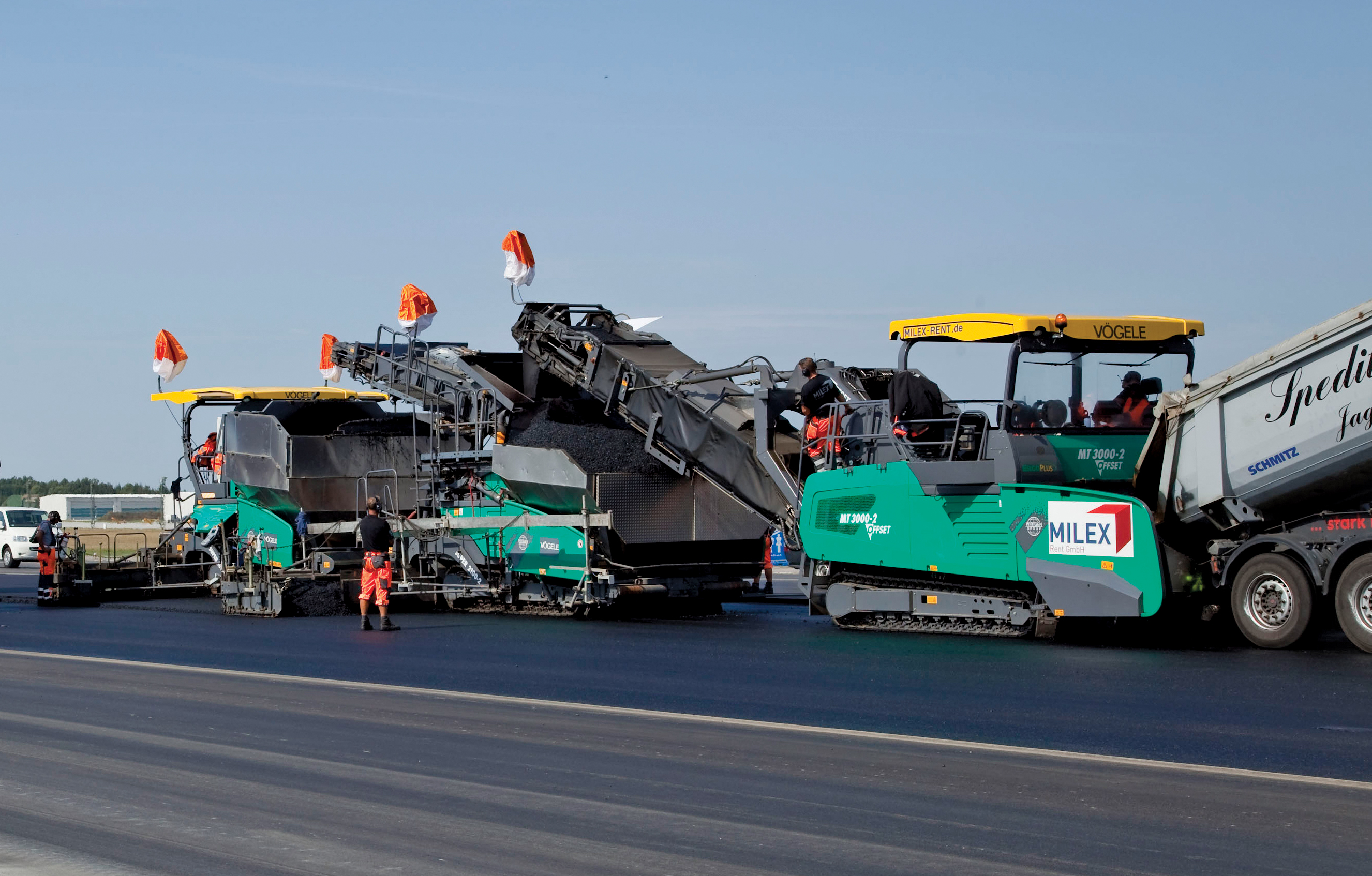
The novel InLine Pave system from Vögele now has acceptance for use on Germany’s road network
German paver specialist Vögele is taking a global view of the construction equipment market, with machines developed for very different markets.
A prime example of this is with the Dash 3 models now coming to market. The new SUPER 2100-3 paver is also available as the SUPER 2100-3i, a highly sophisticated machine that meets the European emissions requirements while offering high productivity and performance. At the same time, the company is also offering a heavy duty (HD) version of its proven SUPER 1800-2 that has been specially developed to meet the requirements of road construction in China, but without compromising on reliability or paving quality. The company also plans to commence construction of a paver designed for the Indian market in its Indian factory in due course.Designed for paving widths of up to 13m, the SUPER 2100-3 is a highway class paver that can deliver up to 1,100tonnes/hour. Precise spreading is claimed across all screed widths and customer can choose from three different screeds, the AB500 and AB600 extending units and the SB250 fixed unit, depending on their needs. These screeds are themselves offered in different configurations: with tamper and vibrators; tamper and one pressure bar, tamper and twin pressure bars. The AB600 is available with a special high compaction variant with tamper and two pressure bars while the SB250 also has a special version, with tamper, vibrator and two pressure bars. The AB500 offers paving widths of 2.55-5m but can be widened to 8.5m with bolt on extensions and the AB600 extends from 3-6m but can have bolt-on units widening it to 9.5m. The basic width of the SB2500 screed is 2.5m and it can be widened as far as 13m using its 1.5m extensions.
One of the key features of the new SUPER 2100-3i is its intelligent emissions control, due to the installation of a new six cylinder
A control makes the hopper sides and the hydraulic hopper front fold up, while the deflectors in front of the tracks are raised, the augers moved into their uppermost position and the screed is raised and locked in place. The paver can then be tracked to the new location, where the operator uses another control to reset the hopper, deflectors, augers and screed to preset levels. Material loading is improved due to the new PaveDock function, which absorbs impacts from the feeder or tipper truck delivering asphalt into the hopper. The system also improved communications between the paver operator and the truck drivers making material deliveries, using a set of signals.
Meanwhile, the Super 1800-2 HD is a heavy duty paver that can be used for placing cold, coarse-grained materials such as cement-treated base (CTB). The paver is designed to cope with the abrasive wear caused by these mixes, increasing its durability. Its SB300HD fixed-width screed is also designed for roadbase applications. It allows thick layers to be paved true to line and level with a maximum degree of pre-compaction. According to the firm, these features make the SUPER 1800-2 HD highly suitable for roadbase jobs.
The material hopper of the SUPER 1800-2 HD has been specially adapted to the feed vehicles used in China. Any mix lorry can dock onto the SUPER 1800-2 HD, as it has extra length at 2.42m and a low feed height of just 560mm. In addition, the wide, oscillating push-rollers can be moved 100mm forwards to optimise material transfer. The hopper can hold up to 15tonnes of material, allowing fast unloading from trucks and ensuring there is sufficient mix while the delivery trucks are being changed over.
The machine is powered by a liquid-cooled
The SB300HD screed has been developed for placing CTB for roadbase and its deep screed plates ensure good floating behaviour. The tamper stroke length can be set to 7, 9 or 10mm, depending on the layer thickness and paving material. Combined with the special tamper geometry, this makes for very high compaction values.
Special applications
One area where Vögele has been developing its InLine Pave system for some years and this uses two pavers, one working directly behind the other. This contrasts with the Dynapac and Sumitomo dual layer paving systems, which are based on a highly modified, single paver fitted with twin screeds and dual hoppers.
The Vögele pavers used for its InLine Pave system are both standard machines, although the first uses a special high compaction screed that ensures the binder course is sufficiently compacted to allow the second machine to operate directly behind without sinking into the hot surface. A material feeder is required to supply the two grades of material, but the key component for the train is the SUPER 2100-2 IP paver with its AB600 High Compaction Screed in TP Plus version. A standard paver with minor modifications, it is also fitted with a special transfer module to carry asphalt over to the second paver in the train. The surface course is then placed on the compacted binder course by either a SUPER 1800-2 or a SUPER 1600-2 paver fitted with a standard AB500 TV extending screed.
Earlier this year, Vögele made a major step forward with this system when it was recognised as a standard road paving method by the Federal Ministry of Transport. This followed on from the earlier acceptance of the Dynapac Compactasphalt dual layer paving technique by the German road authorities.
Following the inclusion of the InLine Pave technique in the German catalogue of standard construction methods, the German Road and Transportation Research Association (FGSV) organised a conference focussing on the subject. The speakers stressed that InLine Pave yields significant advantages in terms of planning, construction, use and costs. This Vögele system is also versatile and allows contractor to lay variable widths from 3.2-8.5m and it can be used to resurface single lanes or roads with several lanes.
Durability is an important aspect due to the stable, interlocking bond between binder course and surface course. This bond ensures that shear stresses are discharged from the asphalt surface course effectively, so that the wearing properties of the asphalt surface course are preserved for a significantly longer period of time. A dual layer paving system also helps minimise rutting, which has been proven in Saxony-Anhalt where hot on hot paving methods have been used on some 1,000,000m2 of road.
High compaction of the lower layer is another key to the service life of the asphalt pavement. Lars Keller, managing director of F Winkler KG, reported, "Measurements have shown that compaction is high throughout the full layer thickness. The resultant degree of density was between 97% and 99% everywhere."
The thinner surface course helps cut costs and speakers from Germany and other European countries confirming that a 20mm surface course on a 20mm thicker binder course produces excellent results, even in the long term. The potential savings are substantial, not only in construction, but also for the road's subsequent maintenance. And using hot on hot paving also helps extend the paving season, as the dual layers feature a greater heat capacity and cool much more slowly than a conventionally built pavement. It is worth noting that similar cost and wear life benefits can be achieved using the rival Dynapac and Sumitomo systems, although the latter has not so far been used outside of the Asian market.