Preserving the unspoiled Mullum Mullum Valley was the major consideration when deciding to build a traffic tunnel The answer to one of the major issues facing construction of the A$2.5 billion EastLink route in Australia was simple: construct a tunnel. While it was expensive, those involved realised they had little option but to go underground to protect the environmentally sensitive Mullum Mullum Valley, an untouched area of wood and bushland in Melbourne. EastLink, the 39km toll road project on the easter
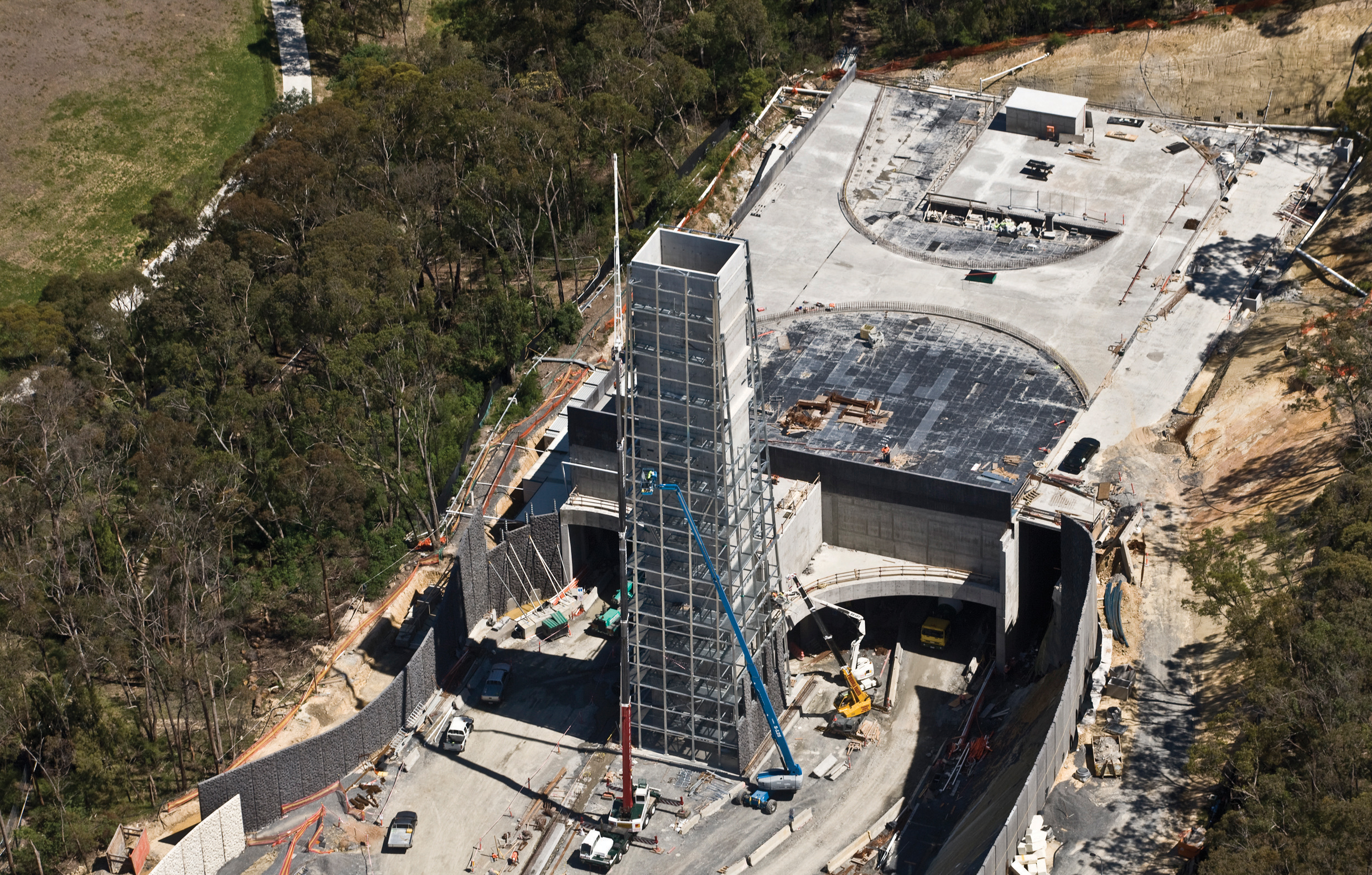
Each tunnel bore has a special ventilation building at the exit: air and car exhaust fumes are dispersed via 47m high ventilation stacks. (Pic: Heaven Photography)
Preserving the unspoiled Mullum Mullum Valley was the major consideration when deciding to build a traffic tunnel
The answer to one of the major issues facing construction of the A$2.5 billion EastLink route in Australia was simple: construct a tunnel. While it was expensive, those involved realised they had little option but to go underground to protect the environmentally sensitive Mullum Mullum Valley, an untouched area of wood and bushland in Melbourne.EastLink, the 39km toll road project on the eastern side of the country's second biggest city, is aimed at easing increasing traffic congestion on existing roads. It opened in July.
To deliver the route, the Victoria state government decided on the public-private partnership (PPP) approach. It set up SEITA (the Southern & Eastern Integrated Transport Authority) to oversee the work with ConnectEast as the concessionaire and the joint venture
To help build positive interest in the twin 1.6km long tunnels, SEITA invited the community to submit nominations for their names. More than 2,000 entries were received and Tim Pallas MP, Victorian Minister for Roads and Ports, eventually chose Melba (after the legendary Australian opera soprano Dame Nellie Melba) for the inbound tunnel and Mullum Mullum for the outbound tunnel. That was the easy part.
In engineering terms the $400 million tunnel was the most complex of the EastLink construction work and the largest single element, with various alignments being discussed. In the end, a 1.6km long alignment was chosen and that proved more expensive than thought on tendering.
The project was completed in just three years following site build-up which started in February 2005. The first heading was excavated by August that year and breakthroughs occurred in October and November 2006. The tunnels were fully completed and operational in April 2008.
The tunnel has three lanes in each direction and twin tunnel bores of over 16m across. Each bore has a special ventilation building at the exit end incorporating giant fans to capture air leaving the tunnel and car exhaust fumes within it. These are dispersed via 47m high ventilation stacks, which were originally some 50m from the ends of the tunnels but which were moved closer once TJH started detailed design work.
Les Bull, SEITA's director of engineering for the northern half of the project, which included the tunnel section, said: "It was a pretty innovative design which simplified a rather complex cocoon-like arrangement in the initial scheme. I think it was better." The move had cost advantages for the contractor; was favourably received by local residents after they had seen various 3-D visualisations and, importantly, it also had construction advantages. Construction work required almost continuous 24-hour working to be economical and to match the fast pace of work on the rest of the road.
But hard rock tunnelling is noisy, and this would be more apparent in the Mullum Mullum Valley, which has little more than a few bird noises in it at night. However, by constructing the ventilation buildings early and fitting them with special three-layered roller doors with a large insulating air gap, which could be closed at night, the sound of the machinery in the tunnels could be contained to no more than the required 10 decibels above background noise.
The 70m long ventilation buildings, which span across both parallel tunnel bores, were used to stockpile a night's worth of the rock cuttings and fragments carved out at the tunnel face and from the benches that followed on behind. Next day they were removed by trucks along with the cuttings coming off the day shift excavation.
The spoil was produced by four large roadheader machines, which have rotating toothed heads on the end of large booms, and were used to cut the rock rather than tunnel boring machines (TBMs), as these would have proved costly.
Ed Taylor, a John Holland engineer, who was tunnel engineering manager for the project, said that the biggest roadheaders available (350kW units) were able to handle most of the rock in the tunnel: mudstone, siltstone and a little sandstone, which is typical of what underlies much of Melbourne's east side. It is between 60MPa and 120MPa, with some close to 200Mpa (the compressive strength of most concrete is 30MPa to 50MPa).
The roadheaders were fitted with scoop arms at the front and conveyors at the back, which meant easy loading straight into the 35tonne articulated dump trucks TJH used for moving the spoil. Using the roadheaders also meant cleaner cutting as their computerised controls could form the top heading of the tunnel with close precision and little overbreak.
However, at some points the rock became too hard, and here drill and blast had to be used. A boomer was moved up to drill the holes pattern for blasting, although times for this were restricted and special measures were taken to inform people in the vicinity.
Once a 6m deep top heading was done by either method the rest of the tunnel depth was removed in benches using excavators fitted with hydraulic breaker hammers.
In all cases in the tunnel, rock faces were supported with rock bolt anchors (a special resin-embedded type of bolt was mainly used) and then shotcreted. Bolts were installed by an automated rig, which meant no worker had to go under the rock until it was supported: this and other stringent measures in the tunnel proved highly successful in making it almost completely safe, a significant achievement in one of the most dangerous sectors of construction.
The tunnel was also required to be fully 'tanked', or watertight, rather than allowing water in and draining it out, and to achieve this meant having a rounder cross section for the tunnel and using a membrane lining sealed behind a permanent inner concrete lining. Installing a membrane without damage is particularly difficult on the bottom of the tunnel, so a fleece was used behind the membrane to protect it from the rough shotcrete.
To prevent workers fitting reinforcement from treading on the membrane, the contractor devised a system of precast curved floor units 8m wide and 2m long, which were installed either by a small crane or with a purpose-built gantry. The units were transported into the tunnel by a specially made up frame modification to the dump trucks.
They sat on two temporary blocks on the membrane and were then grouted in. A flat top to the unit allowed trucks to run by, and two edges took temporary rails on which a large gantry could be supported. There were two gantries for each tunnel, one a set of platforms from which the rest of the fleece and membrane could be installed and welded to the floor and already installed wall sections.
Behind came a formwork gantry which held in place a 15m length of steel shutter for the curved inner lining to be poured. The shutter moved on after ten hours ready to set up again during a 24-hour cycle.
For the cross passages between the two tunnel bores (every 120m), required in case of fire or other disaster, the excavations were started from the top headings and finished using a fifth roadheader. A complex piece of formwork was used to block them out as the main form passed so that the reinforced openings could be made as part of the main wall, with the insides finished later.
During construction the passages were used so that dump trucks could pass between the bores: one as a "dirty" haul tunnel and the other for "clean" concreting.
Once the tunnel lining was completed the curved invert was backfilled to road level using the spoil from the still continuing faces. In this new platform a trench was made for drainage and the multiple electrical and communications cables needed in a modern tunnel.