Turkey’s longest, and what will be the world’s fourth longest, highway tunnel is being built under Mount Ovit in the northeast of the country. Sandvik Construction is playing a vital role in the construction of the giant new structure, which will enable all-year-round access to what is a relatively remote and often snow-blocked part of Anatolia
Having had their freedom of movement blighted for many years by wintertime snow blocking the D925 highway, along with narrower roads and passes, at Mount Ovit, resi
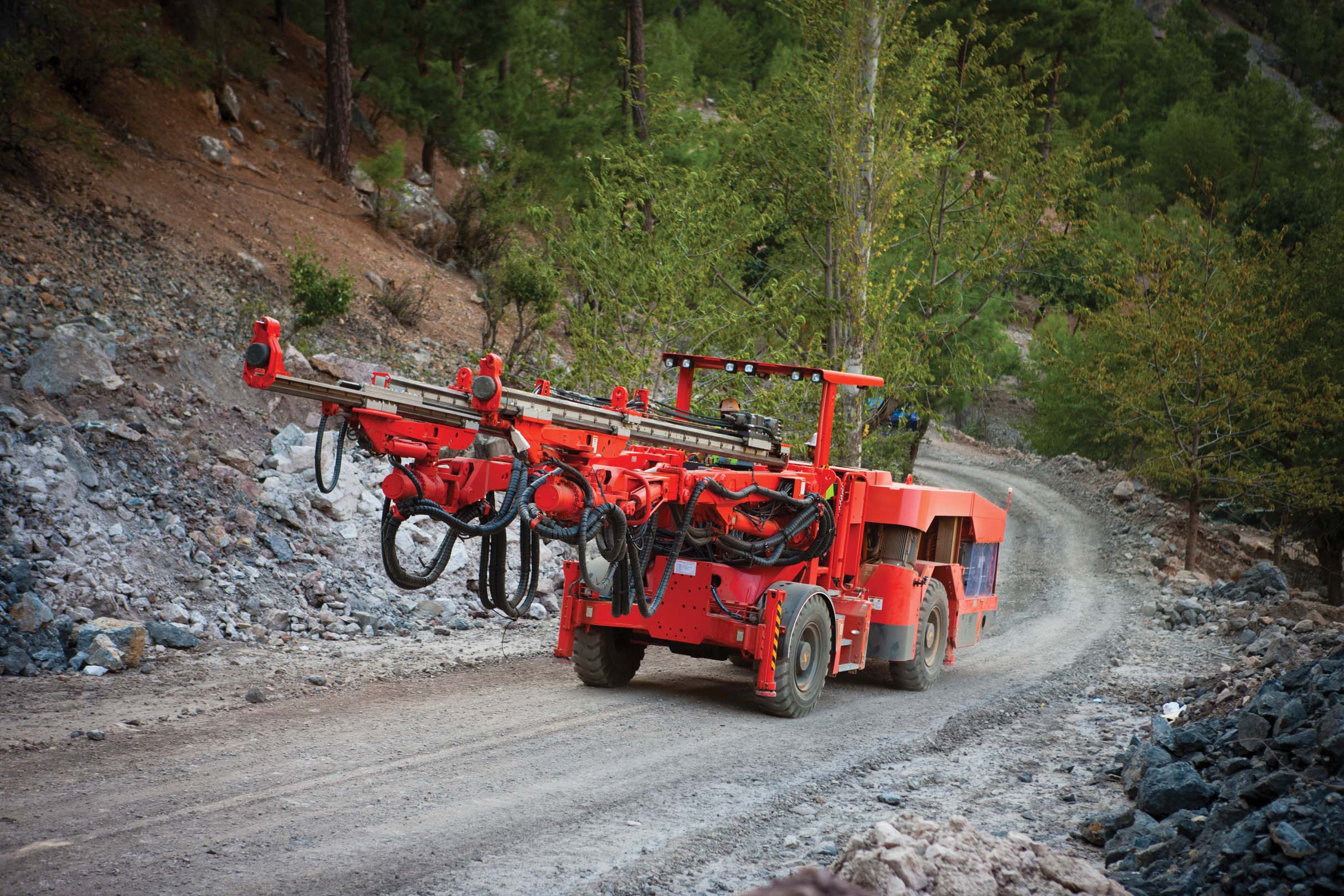
The Sandvik DT820 is a two boom electro-hydraulic jumbo for fast accurate drilling in tunnelling and cavern excavation. Its powerful 4-wheel drive centre articulated carrier ensures rapid and safe tramming with good balance even in uneven terrain
Turkey’s longest, and what will be the world’s fourth longest, highway tunnel is being built under Mount Ovit in the northeast of the country. 2403 Sandvik Construction is playing a vital role in the construction of the giant new structure, which will enable all-year-round access to what is a relatively remote and often snow-blocked part of Anatolia
Having had their freedom of movement blighted for many years by wintertime snow blocking the D925 highway, along with narrower roads and passes, at Mount Ovit, residents of eastern Anatolia must have been hugely relieved two years ago when325 Sandvik drill-rigs deployed by the CMA contracting joint venture began driving under Mount Ovit at the start of the Ovit Tunnel project. Currently the main transport to the region from the main Turkish business cities of Ankara and Istanbul is restricted to air, water via the Black Sea coast, and a long coastal road. But now the countdown is on to complete a tunnel road link planned since 1880, more than 40 years before the end of the Ottoman Empire. The current D925 highway was constructed in 1930 over Mount Ovit pass at 2,600m above sea level, and needed 1,500 workers to complete it.
The new improved €150 million D925 highway project will link Ikizdere, in Rize Province, and Ispir, in Erzurum Province, for the first time providing an all-year, all-weather link and boosting the local economies.
In addition to various road improvement projects along the route, the Ovit Tunnel is the key element in the new link. It comprises two 14.7km long tubes and, on completion, will be the longest tunnel in Turkey and the fourth longest globally.
The tunnel plan is mainly straight with slight curves at each end to reach the optimum portal positions. The two bores are connected by crosscuts at intervals of 250m to enable escape routes and to provide services accommodation. In profile there will be a grade, chiefly to facilitate drainage, of 3.5% for the first 7km from the main northwest portal, and of 1.0% for 5.5km from the other portal. At the high point, 2,500m above sea level, there will be a 1,700m long drive, 8m square in order to facilitate emergency egress and ventilation. This replaces the original plan for an access shaft as it was decided this would be too deep and difficult to access high up in the mountainous terrain.
Contractor CMA (4144 Cengiz Insaat and 3340 Makyol) is responsible for the whole tunnel and highway construction project, and the client and owner is TCK, the Turkish national General Directorate of Highways.
The project management structure is substantially affected by the two construction sites, at each tunnel portal, being remote from each other, especially in winter. Thus the site at the south-east portal has its own tunnelling and mechanical chiefs: Ferhat ahinba and Murat Ozan respectively. The project is led on site by Alper Eryiit as project manager, supported by chief engineer Kerim Tütüncü. In the management structure under Kerim Tütüncü there is Muharrem Tezcan as tunnelling chief engineer and Sedat Seker as chief mechanical service engineer.
Of the joint venture participants, Makyol has 42 years of experience in many heavy construction projects, making it one of the oldest and most experienced contractors in Turkey with many completed highway projects. Makyol also has international experience in Albania, Algeria, Azerbaijan, Iraq, Morocco, and Oman.
Tunnelling and mining specialist Cengiz was founded in 1980 and has been involved in many tunnelling, highway, mining and infrastructure projects, including work in Azerbaijan, Bulgaria, Bosnia-Herzegovina and Iraq as well as throughout Turkey.
The two tunnels are actually being driven as four drives with two partial faces in each. The full excavation dimensions of each horseshoe-shape drive are 8.4m height x 11.78m width, plus trenches on each side to provide space for future drains. First a top heading is driven to a height of 5.9m followed by a bench of 2.5m height, a contractual distance of 250m behind. A ramp between the two facilitates access for the drill-rig and mucking out.
Most of the tunnelling is carried out by drill-and-blast using four Sandvik DT820 rigs with standard manual controls, one for each of the current main tunnel excavation drives. However the rigs also carry out any necessary rock bolting and excavation of crosscuts between the two bores.
The decision to go for Sandvik Construction equipment is attributed to both a strong relationship between Sandvik Construction Turkey and the Cengiz Group, but the delivery times for the ordered rigs were also very important. In addition to the four tunnelling and one surface drill rig used on the Mount Ovit site, Sandvik has also sold another three tunnelling rigs and a surface rig to Cengiz for a tunnelling project in Bosnia-Herzegovina.
The Sandvik Construction Turkey tunnelling team, consisting of Erdinç Çetin, Ouz Arslan and Burak Özgür, most closely associated with the Mount Ovit project, said that the 1700m new access drive to the centre of the main tunnel drives will enable CMA to test the newer DT921i tunnelling drill rig. This will be equipped with Sandvik’s advanced iSURE control software for fully automatic operation requiring minimal human intervention. Then, CMA will transfer the DT921i rig to granite faces in the south-east end of the planned tunnel.
In addition to the four DT820 tunnelling drill rigs, a Sandvik DX700 top-hammer surface-drilling rig has been employed to excavate rock from the portals and associated cuttings.
There is a long tradition of drill-and-blast tunnelling in Turkey, and for such an important project CMA needed the best. “We were looking first for well qualified operators,” said Alper Eryiit. “But sometimes training is necessary for which Sandvik is supporting us.”
Most of the rock to be excavated is expected to be granitic, both standard granite and porphyritic, or basalt, generally making good ground for drill-and-blast tunnelling. However there are some fracture zones between the main rock masses.
CMA employs Sandvik ballistic bits of 45mm diameter for blast holes, and 51mm in diameter for rock-bolt holes. Using 4.9m-long drill rods, each round is drilled to a depth of up to 4.5m. This achieves an advance of 7-8m per day on all four current faces. As of early 2014, some 6.2km of advance had been achieved, in totalling all four faces. Blasting is scheduled twice a day, usually meaning that there is a blast every 12-hour working shift.
The joint venture’s mechanical maintenance chief, Sedat eker, said that the hard and abrasive rock had taken some toll of drill consumables. Even so, on average each blast hole bit lasts 400-600m without grinding. “Earlier there had been shank breakage problems while drilling in the very hard rock, but since the adoption of the new design (Sandvik Alpha 330) of rock tools, there have been no more problems.”
Sandvik Construction Turkey’s rock tools sales engineer Ouzhan Öztürk said, “While they were using R38-R32 standard rock tools they had really big shank adaptor and rod failure problems due to very hard rock conditions - the very hard granite. Most of the rod failures were because of the bending of the rods in the deviated holes. That was also the reason of the shank adapter failures.”
“After that, we tested the new Alpha 330 rock tools at the site, and with these tools they have minimised the hole deviation problems and consequently minimised the rod and especially shank adapter failures.”
“Now, they are using only Alpha 330 tools for their underground drill rigs. This system has decreased their consumption, especially for rods and shank adapters, accelerated the drilling process, increased the hole quality which, in turn, is increasing the blasting efficiency and at the end decreasing the whole tunnelling process costs.”
Alpha 330 rock tools are designed especially for 45mm-diameter drilling with high-power (20kW+) drills. Sandvik’s particular expertise in steel metallurgy together with state-of-the-art CAD/CAM procedures has resulted in optimised geometry resulting in higher stiffness and longer service life than the earlier R32 design, also a Sandvik innovation.
Project manager Alper Eryiit of CMA said that although the rock is generally massive and hard, it can be variable. “There are about 70 metres of soft ground at the portals, requiring special support measures. The rock was very abrasive between 300 and 350 metres in from the northwest portal. It took about four hours to drill a round until 250 metres, but on hitting the granite from 250 metres it took three-and-a-half hours. I would prefer moderate rock conditions for optimum progress, with two-and-a-half hours to drill a round rather than the three-and-a-half to four hours in granite. But the rock is changing and we are quite okay now. Overall we expect 75% of the drives to be in granite and 25-45% in basalt.”
CMA tunnelling chief Muharrem Tezcan reported that the normal drill patterns included 100-140 blast holes in the top-heading wedge cut, and 40-50 parallel holes in the bench. He explained that the blasting itself employs micro gel-style explosive in 38mm-diameter capsules as these produce lower air pollution, allowing the face to be approached earlier for support work and mucking out. Around 200kg is used in each top-heading blast. Initiation uses one electronic detonator attached to a non-electric circuit.
At the south-east portal there is up to 350m of overburden superficial and a large fracture zone, making tunnelling more problematic. “We have suffered from water penetration and collapses,” said Eryiit. “The ground has changed to basalt with an alteration and fracture zone, but we are still continuing with drill-and-blast. Basalt actually occurs at both ends.”
To a considerable extent, the CMA tunnelling team has to be ready to tackle whatever it encounters. Eryiit added, “There has been limited site investigation due to the great overburden, of up to 900 metres, meaning that there would be long investigation hole lengths with difficult access. This is partially why we are keen to check the performance of intelligent jumbos in the emergency access drive.”
Sandvik tunnelling team member Erdinç Çetin added, “Sandvik iSURE offers many more possibilities to check hole length and drilling performance. It gives far better control of the whole drilling and blasting process and therefore gives good opportunities for process performance improvement.”
A typical tunnelling cycle starts with drilling the top-heading first followed by blasting and loading out. The newly blasted surfaces are scaled with an excavator-mounted hydraulic breaker. Then a primary lining of sprayed concrete, reinforced with polypropylene fibres, is applied up to the face for safety. Next the bench face undergoes the same sequence.
Meanwhile systematic rock bolting, using the Sandvik DT820 drill-rigs, is carried out up to 15m behind the face, together with welded steel-mesh sheet installation and fibre-reinforced sprayed concrete according to the determined rock type. Split-set-type rock bolts are normally installed.
Although the more difficult rock types necessitate increasing measures such as higher rock bolt density and thicker sprayed concrete, the most unstable zones require different approaches. In soft rock and zones with high overburden self-drilling anchors (SDAs) are used to avoid having the drill hole stand open before installing the bolt. Using SDAs the drill-bit employed is sacrificial and the rebar drill steel is grouted in place immediately to secure early support.
In addition, within the ‘overburden area’ umbrella support is installed with lengths of rebar over the next stretches to be excavated. In all cases the versatile Sandvik DT820 drill rigs carry out all drilling and bolt installation.
CMA has its own workshops and maintenance crew on site, but supported in the case of drilling equipment by Sandvik. Frequently used consumables and service parts such as drill requirements and machine filters are stocked in the sites at both ends of the tunnel route but larger or less frequently needed parts are supplied by Sandvik from its depot in Trabzon. CMA uses original parts for all drill rig requirements.
CMA chief of mechanical maintenance Sedat eker said, “We are quite happy with Sandvik’s performance in service and that of the equipment. There is usually same-day service response from the Trabzon depot.”
Two spare drills are available on site to permit overhauls in the workshops every 500 hours of operation.
If view of the remote location of the sites, all workers usually remain in site accommodation, working 13 days out of 14 on 12-hour shifts.
The support elements described earlier provide the required support during construction and as a base for the final structure. CMA will install cast-in-place concrete to a depth of 460mm using travelling formwork made in Turkey. First, however, a plastic waterproofing membrane is installed over a smooth layer of sprayed concrete. This provides a drainage passage to the main drains to be installed at the foot of each tunnel wall alongside service ducts.
CMA mobilised on its two construction sites and camps in 2012 with a groundbreaking ceremony on 12 May attended by national and local dignitaries. The tunnel is scheduled to be open for traffic in November or December 2015, in time for the winter snows, necessitating tunnelling to be complete by the mid-summer of that year.
Having had their freedom of movement blighted for many years by wintertime snow blocking the D925 highway, along with narrower roads and passes, at Mount Ovit, residents of eastern Anatolia must have been hugely relieved two years ago when
The new improved €150 million D925 highway project will link Ikizdere, in Rize Province, and Ispir, in Erzurum Province, for the first time providing an all-year, all-weather link and boosting the local economies.
In addition to various road improvement projects along the route, the Ovit Tunnel is the key element in the new link. It comprises two 14.7km long tubes and, on completion, will be the longest tunnel in Turkey and the fourth longest globally.
The tunnel plan is mainly straight with slight curves at each end to reach the optimum portal positions. The two bores are connected by crosscuts at intervals of 250m to enable escape routes and to provide services accommodation. In profile there will be a grade, chiefly to facilitate drainage, of 3.5% for the first 7km from the main northwest portal, and of 1.0% for 5.5km from the other portal. At the high point, 2,500m above sea level, there will be a 1,700m long drive, 8m square in order to facilitate emergency egress and ventilation. This replaces the original plan for an access shaft as it was decided this would be too deep and difficult to access high up in the mountainous terrain.
Contractor CMA (
The project management structure is substantially affected by the two construction sites, at each tunnel portal, being remote from each other, especially in winter. Thus the site at the south-east portal has its own tunnelling and mechanical chiefs: Ferhat ahinba and Murat Ozan respectively. The project is led on site by Alper Eryiit as project manager, supported by chief engineer Kerim Tütüncü. In the management structure under Kerim Tütüncü there is Muharrem Tezcan as tunnelling chief engineer and Sedat Seker as chief mechanical service engineer.
Of the joint venture participants, Makyol has 42 years of experience in many heavy construction projects, making it one of the oldest and most experienced contractors in Turkey with many completed highway projects. Makyol also has international experience in Albania, Algeria, Azerbaijan, Iraq, Morocco, and Oman.
Tunnelling and mining specialist Cengiz was founded in 1980 and has been involved in many tunnelling, highway, mining and infrastructure projects, including work in Azerbaijan, Bulgaria, Bosnia-Herzegovina and Iraq as well as throughout Turkey.
The two tunnels are actually being driven as four drives with two partial faces in each. The full excavation dimensions of each horseshoe-shape drive are 8.4m height x 11.78m width, plus trenches on each side to provide space for future drains. First a top heading is driven to a height of 5.9m followed by a bench of 2.5m height, a contractual distance of 250m behind. A ramp between the two facilitates access for the drill-rig and mucking out.
Most of the tunnelling is carried out by drill-and-blast using four Sandvik DT820 rigs with standard manual controls, one for each of the current main tunnel excavation drives. However the rigs also carry out any necessary rock bolting and excavation of crosscuts between the two bores.
The decision to go for Sandvik Construction equipment is attributed to both a strong relationship between Sandvik Construction Turkey and the Cengiz Group, but the delivery times for the ordered rigs were also very important. In addition to the four tunnelling and one surface drill rig used on the Mount Ovit site, Sandvik has also sold another three tunnelling rigs and a surface rig to Cengiz for a tunnelling project in Bosnia-Herzegovina.
The Sandvik Construction Turkey tunnelling team, consisting of Erdinç Çetin, Ouz Arslan and Burak Özgür, most closely associated with the Mount Ovit project, said that the 1700m new access drive to the centre of the main tunnel drives will enable CMA to test the newer DT921i tunnelling drill rig. This will be equipped with Sandvik’s advanced iSURE control software for fully automatic operation requiring minimal human intervention. Then, CMA will transfer the DT921i rig to granite faces in the south-east end of the planned tunnel.
In addition to the four DT820 tunnelling drill rigs, a Sandvik DX700 top-hammer surface-drilling rig has been employed to excavate rock from the portals and associated cuttings.
There is a long tradition of drill-and-blast tunnelling in Turkey, and for such an important project CMA needed the best. “We were looking first for well qualified operators,” said Alper Eryiit. “But sometimes training is necessary for which Sandvik is supporting us.”
Most of the rock to be excavated is expected to be granitic, both standard granite and porphyritic, or basalt, generally making good ground for drill-and-blast tunnelling. However there are some fracture zones between the main rock masses.
CMA employs Sandvik ballistic bits of 45mm diameter for blast holes, and 51mm in diameter for rock-bolt holes. Using 4.9m-long drill rods, each round is drilled to a depth of up to 4.5m. This achieves an advance of 7-8m per day on all four current faces. As of early 2014, some 6.2km of advance had been achieved, in totalling all four faces. Blasting is scheduled twice a day, usually meaning that there is a blast every 12-hour working shift.
The joint venture’s mechanical maintenance chief, Sedat eker, said that the hard and abrasive rock had taken some toll of drill consumables. Even so, on average each blast hole bit lasts 400-600m without grinding. “Earlier there had been shank breakage problems while drilling in the very hard rock, but since the adoption of the new design (Sandvik Alpha 330) of rock tools, there have been no more problems.”
Sandvik Construction Turkey’s rock tools sales engineer Ouzhan Öztürk said, “While they were using R38-R32 standard rock tools they had really big shank adaptor and rod failure problems due to very hard rock conditions - the very hard granite. Most of the rod failures were because of the bending of the rods in the deviated holes. That was also the reason of the shank adapter failures.”
“After that, we tested the new Alpha 330 rock tools at the site, and with these tools they have minimised the hole deviation problems and consequently minimised the rod and especially shank adapter failures.”
“Now, they are using only Alpha 330 tools for their underground drill rigs. This system has decreased their consumption, especially for rods and shank adapters, accelerated the drilling process, increased the hole quality which, in turn, is increasing the blasting efficiency and at the end decreasing the whole tunnelling process costs.”
Alpha 330 rock tools are designed especially for 45mm-diameter drilling with high-power (20kW+) drills. Sandvik’s particular expertise in steel metallurgy together with state-of-the-art CAD/CAM procedures has resulted in optimised geometry resulting in higher stiffness and longer service life than the earlier R32 design, also a Sandvik innovation.
Project manager Alper Eryiit of CMA said that although the rock is generally massive and hard, it can be variable. “There are about 70 metres of soft ground at the portals, requiring special support measures. The rock was very abrasive between 300 and 350 metres in from the northwest portal. It took about four hours to drill a round until 250 metres, but on hitting the granite from 250 metres it took three-and-a-half hours. I would prefer moderate rock conditions for optimum progress, with two-and-a-half hours to drill a round rather than the three-and-a-half to four hours in granite. But the rock is changing and we are quite okay now. Overall we expect 75% of the drives to be in granite and 25-45% in basalt.”
CMA tunnelling chief Muharrem Tezcan reported that the normal drill patterns included 100-140 blast holes in the top-heading wedge cut, and 40-50 parallel holes in the bench. He explained that the blasting itself employs micro gel-style explosive in 38mm-diameter capsules as these produce lower air pollution, allowing the face to be approached earlier for support work and mucking out. Around 200kg is used in each top-heading blast. Initiation uses one electronic detonator attached to a non-electric circuit.
At the south-east portal there is up to 350m of overburden superficial and a large fracture zone, making tunnelling more problematic. “We have suffered from water penetration and collapses,” said Eryiit. “The ground has changed to basalt with an alteration and fracture zone, but we are still continuing with drill-and-blast. Basalt actually occurs at both ends.”
To a considerable extent, the CMA tunnelling team has to be ready to tackle whatever it encounters. Eryiit added, “There has been limited site investigation due to the great overburden, of up to 900 metres, meaning that there would be long investigation hole lengths with difficult access. This is partially why we are keen to check the performance of intelligent jumbos in the emergency access drive.”
Sandvik tunnelling team member Erdinç Çetin added, “Sandvik iSURE offers many more possibilities to check hole length and drilling performance. It gives far better control of the whole drilling and blasting process and therefore gives good opportunities for process performance improvement.”
A typical tunnelling cycle starts with drilling the top-heading first followed by blasting and loading out. The newly blasted surfaces are scaled with an excavator-mounted hydraulic breaker. Then a primary lining of sprayed concrete, reinforced with polypropylene fibres, is applied up to the face for safety. Next the bench face undergoes the same sequence.
Meanwhile systematic rock bolting, using the Sandvik DT820 drill-rigs, is carried out up to 15m behind the face, together with welded steel-mesh sheet installation and fibre-reinforced sprayed concrete according to the determined rock type. Split-set-type rock bolts are normally installed.
Although the more difficult rock types necessitate increasing measures such as higher rock bolt density and thicker sprayed concrete, the most unstable zones require different approaches. In soft rock and zones with high overburden self-drilling anchors (SDAs) are used to avoid having the drill hole stand open before installing the bolt. Using SDAs the drill-bit employed is sacrificial and the rebar drill steel is grouted in place immediately to secure early support.
In addition, within the ‘overburden area’ umbrella support is installed with lengths of rebar over the next stretches to be excavated. In all cases the versatile Sandvik DT820 drill rigs carry out all drilling and bolt installation.
CMA has its own workshops and maintenance crew on site, but supported in the case of drilling equipment by Sandvik. Frequently used consumables and service parts such as drill requirements and machine filters are stocked in the sites at both ends of the tunnel route but larger or less frequently needed parts are supplied by Sandvik from its depot in Trabzon. CMA uses original parts for all drill rig requirements.
CMA chief of mechanical maintenance Sedat eker said, “We are quite happy with Sandvik’s performance in service and that of the equipment. There is usually same-day service response from the Trabzon depot.”
Two spare drills are available on site to permit overhauls in the workshops every 500 hours of operation.
If view of the remote location of the sites, all workers usually remain in site accommodation, working 13 days out of 14 on 12-hour shifts.
The support elements described earlier provide the required support during construction and as a base for the final structure. CMA will install cast-in-place concrete to a depth of 460mm using travelling formwork made in Turkey. First, however, a plastic waterproofing membrane is installed over a smooth layer of sprayed concrete. This provides a drainage passage to the main drains to be installed at the foot of each tunnel wall alongside service ducts.
CMA mobilised on its two construction sites and camps in 2012 with a groundbreaking ceremony on 12 May attended by national and local dignitaries. The tunnel is scheduled to be open for traffic in November or December 2015, in time for the winter snows, necessitating tunnelling to be complete by the mid-summer of that year.