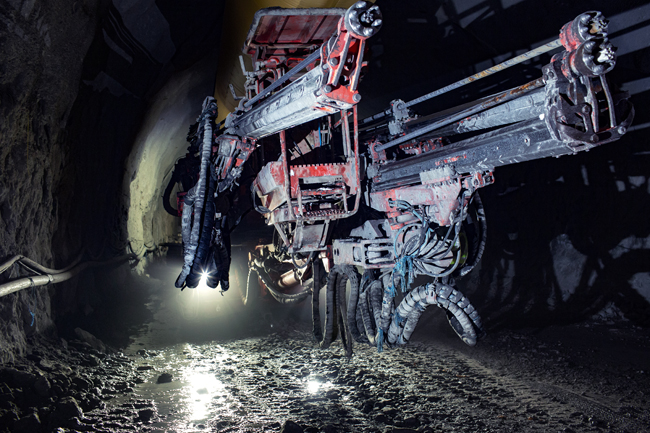
Czech contractor Metrostav recently achieved 105m of tunnel excavation in a record-breaking six days. But it will be consistent performance and progress that will see Iceland’s Dyrafjordurgong Tunnel in the remote Westfjords region open on time and on budget.
The 5.3km Dyrafjordurgong Tunnel is costing around €69 million and due to open in September 2020. It should make the biggest economic impact on the region since the 9.1km Vestfjardagong Tunnel opened in 1996. It will save around 25km and 45 minutes of driving along what is now a mountainous, partly gravel road with high winds and frequent snowfall.
The mountain through which the tunnel is being excavated is principally basalt, the most common volcanic rock on the planet. Although the rock isn’t tough, there is a lot of variety, from coarse crystal several millimetres wide to much finer-grained basalt. Some less-common minerals, including chabazite and the calcium-rich thomsonite, have been found in cavities and pockets within the basalt. This means the tunnelling team needs a process to analyse the rock and the profile following each blast.
“Each round of planning, drilling, charging, blasting, clearance and reinforcing takes around seven hours,” says Josef Malknecht, Metrostav project manager.
“We’ve completed a round in as few as six hours and 16 minutes and we aim to achieve a minimum of 5m progress on each round. We plan for 80m progress per week, but our goal is to achieve consistent weekly progress of 90-95m over the long term,” says Malknecht. “Time is short and any breakdown can undo weeks of good progress.”
Continual progress is paramount because with a single-face operation, any equipment problem halts the entire operation. Metrostav needs a drilling jumbo capable of consistent performance. The team chose a new Sandvik DT1131i as its sole tunnelling jumbo. Only one operator is needed to control the entire drilling process with multiple booms. Also, purchasing a new machine reduces the risk of downtime.
”We can take the data from the actual drill, look at the penetration rate and learn something from the drilling to improve things next time. For at least three months of the year, south portal access roads are usually closed, with scheduled opening windows of just a few days every four weeks,” Malknecht says. “With transport options limited, we have to stock up on supplies and pay close attention to maintenance and the reliability of everything we need. We used Sandvik rigs on our previous tunnel project, so we knew we could rely on them as a partner for this project, too.”
“Our operators are able to manage multiple booms from a single comfortable position,” says Metrostav site manager Tomáš Janoušek. “This is important for us as a small team.”
Sandvik's solution was one Sandvik DT1131i tunnelling jumbo - suitable for tunnels of 20-177m² and one Sandvik DT1130-SC as a backup. Engineers use iSURE tunnel management software to create the drill patterns and blast design and to analyse feedback from the DT1131i.
Land surveyor Lubomír Krchňavý says iSURE software is a major improvement on previous tools. “It has improved functionality, but most importantly it’s much more accurate,” he says. “We make one drill pattern and then it is very easy to modify that to make another,” he added. “We can take the data from the actual drill, look at the penetration rate and learn something from the drilling to improve things next time.”
Also, iSURE automatically creates folders for the curve table, tunnel profiles, drill plans, navigation laser data, navigation sets and related files such as photographs.
Sandvik’s Ari Laitinen, business development manager, Underground Drilling, says he is pleased to see a customer getting the full benefits from the combination of Sandvik DT1131i and iSURE drill and blast design software. “It is nice to see customers make the plan at the bottom of the blasting round, gaining the full pull-out and good profile quality after blasting,” he says.
Laitinen is also pleased to see the customer consider the total cost of ownership. “Metrostav sees beyond the net penetration rate,” he says.
Remote Norway
Norway’s northern community of Bratland sees hundreds of visitors in the summer looking to walk the mountains as well as swim, sail and fish in the clear water of the fjords. But family vehicles often mingle with large trucks along the narrow access roads in the area, only 10km south of the Arctic Circle.
PNC Norge has the contract to renovate one such road. Route 17 is a coastal road that is slipping slightly and runs at its narrowest past the Liafjellet, a tall mountain with a steep face.
Avalanches in winter often completely close the access road, cutting off communities and businesses north of the area. At these times, the only form of transport is aircraft and boat, both of which are often delayed or cancelled due to poor weather.
Norbert Hoerlein, site project manager, has been working in the tunnelling industry for 20 years, mostly in Austria and Germany. It’s his and PNC’s first tunnel project in Norway. “The US$330 million project is a 5km stretch of road that will travel through two mountains – 1.9km through Liatind, plus a 400m tunnel through Bakliholtan and then bridging over the Olvikvatnet lake,” he says. The road will be 8.5m wide – better for large trucks – and avoid the avalanche-prone steep mountain face.
The main challenge during the tunnelling process is to get as little over-profile and under-profile as possible,” says site engineer Ines Hagspiel. “That’s why we need a drill rig that is very accurate, so that we only get a minimal theoretical profile,” she says.
“The common rock here is gneiss and mica schist – old, solid rock, perfect for building tunnels. The Sandvik equipment can drill 5m blasts at a time – quite a difference from the 1m or 2m blasts Hoerlein is used to in central Europe.”
“This is why the technology is so important here,” Hoerlein says. “In Austria and Germany, where you can only drill 1m at a time, you can’t go too far wrong with each blast. But here in Norway, if you drill by eye only, you can quickly end up 1m away from your planned track. You need technology to make accurate, fast progress.”
PNC has been trialling Sandvik iSURE software, made possible by the jumbo’s onboard 3D scanning system. “The benefit of a 3D scanner is the possibility for immediate reaction, correction and speed of process – that’s the main thing,” says Marin Kulaš, the onsite geodata senior surveyor contracted by PNC.
“It helps the operator see the contour, if there’s an under-profile or an over-profile and he or she can react in place in real time. And the scan is like a fingerprint, so during the next round when the scanner makes a scan, it searches for identical points between the point cloud and the previous scan. Then you’re ready for the next round. The whole process of the navigation by scanner is under four minutes. That’s fast,” says Kulaš.
iSURE 3D reporting tools also make it easier to keep clients informed, increasing the trust between client and contractor because it’s a transparent way of working and makes that process simple. “You deliver accurate information about the project in a straightforward way and then you can arrive at solutions together,” Hoerlein says.
“We deliver a 3D model of our tunnel to the client,” says Hagspiel. “With it we can show them where we have under-profile and over-profile and where we may have to drill new holes for reblasting.”
For this tunnelling project, the first for PNC in Norway, Sandvik provided the new Sandvik DT1131i three-boom jumbo along with rock tools, drill bits and rods. Sandvik iSURE software and 3D scanner were trialled for the first time here in a project of this nature, offering high-level planning and analysis capabilities. Sandvik also supplied technical support and onsite training for operators at the site, working to ensure that the equipment, systems and support met the specific needs of the customer.
“It’s an absolutely stable system,” says Hoerlein. The iSURE system can measure the exact position of the bolts, which in turn can be delivered to the client in 3D imaging to a very high accuracy. “Otherwise, a surveyor has to measure tens of thousands of bolts and guess where the end sits in the mountain. This is one step into the future already.”