Tunnelling technology is seeing major developments that will boost construction efficiency - Mike Woof writes
Both in tunnel drilling and TBM systems, new machines are now being built that offer major gains in performance. Sandvik is introducing a number of major new models developments to its tunnelling drill range. Three new tunnelling jumbos are now available that suit different drilling requirements, the DD422iE, DT912D and DT922i.
The firm says that its advanced DD422iE rig offers major advantage
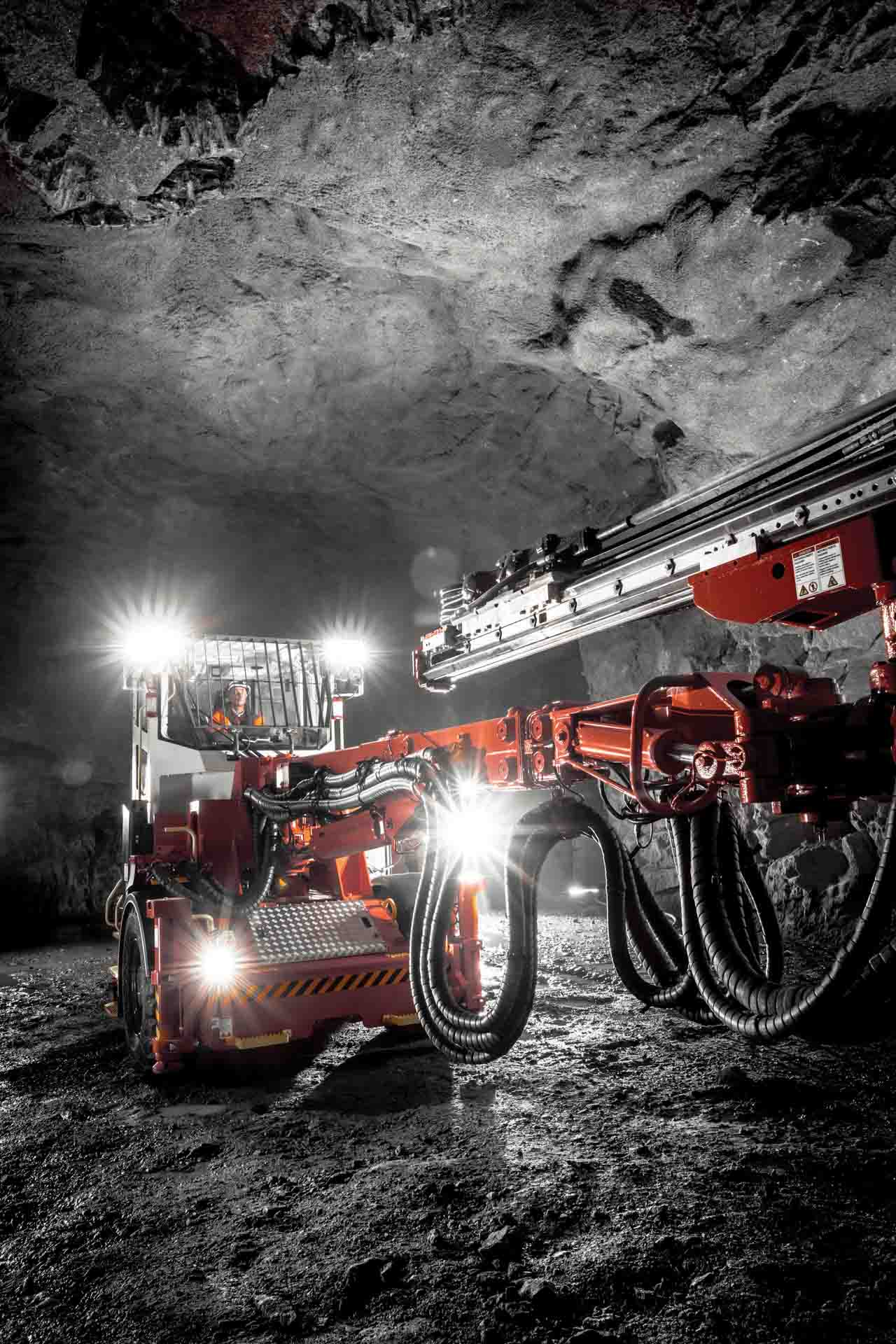
The new Sandvik DT912D and DT922i rigs feature sophisticated drilling technology
Tunnelling technology is seeing major developments that will boost construction efficiency - Mike Woof writes
Both in tunnel drilling and TBM systems, new machines are now being built that offer major gains in performance.325 Sandvik is introducing a number of major new models developments to its tunnelling drill range. Three new tunnelling jumbos are now available that suit different drilling requirements, the DD422iE, DT912D and DT922i.
The firm says that its advanced DD422iE rig offers major advantages for operation in tunnel jobs. With its battery power, the DD422iE jumbo can be driven to and from the face without any exhaust emissions, reducing ventilation needs. The machine also produces less heat than a diesel powered drill, offering further benefits for underground use.
For safety the battery features molten salt technology, which reduces the risk of fire. The battery is recharged in just 10 minutes during the drilling cycle as the rig is linked to an underground electrical supply when drilling. Regenerative braking also helps charge the battery.
The single boom DT912D offers high reach and is powered by a fuel efficient diesel that is Tier 4 Final compliant. This 24tonne rig is also equipped with an onboard compressor and water-tank for air-mist flushing. The machine is equipped with Sandvik’s latest, state-of-the-art control system and is said to offer high quality operation in tunnelling work.
The diesel-hydraulic machine features air-mist flushing and is designed for fast and accurate drifting and production drilling of 12-125m² cross sections. It is equipped with a high frequency RD525 rock drill and is powered by a 205kW196 Cummins diesel. The firm claims that the engine allows high performance and productivity as well as low fuel consumption. As standard, the jumbo has an electric controlled drilling system with added automatic functions, including one-hole automatics. It is also equipped with a SB150 universal boom for large, optimally shaped coverage and full automatic parallelism. In addition to face drilling, the versatile boom may also be used for crosscutting, bolt-hole drilling and extension drilling.
The rig has a 4m³/min onboard compressor and a 1,000 litre water tank for air-mist flushing, allowing it to operate independently from the tunnel infrastructure. This allows a longer drilling period from one set up, boosting cycle time efficiency and machine versatility. The compressor has the patented Sandvik Compressor Management System, which the firm claims can cut fuel consumption by up to 25%.
The machine can also move quickly to and from the face on its four-wheel-drive articulated carrier. The ergonomic FOPS/ROPS compliant cabin is available with a lifting system for better visibility. The rig also has the proven Sandvik Intelligent Control system Architecture (SICA), with built-in diagnostics and user-friendly controls.
Customers for the DT912D can select different instrumentation levels. These include the silver package for drilling angles and depth monitoring, while the gold package offering semi-automatic drilling according to drill plan. The platinum package has the advantage of automatic boom movements and drilling cycle. The gold and platinum packages are integrated with the Sandvik iSURE tunnel management tool for accurate drilling, charging and blasting plans. The iSURE system provides data collection and analysis reports for improving the work cycle and process and can be complemented with the new geoSURE rock mass analysis and visualisation system.
Meanwhile the 30tonne DT922i tunnelling jumbo offers high performance and productivity according to the firm. Said to be versatile and productive, this machine is fully automated machine and has been designed to help optimise drilling operations. The rig is mounted on a manoeuvrable articulated carrier with hydrostatic transmission and is equipped with a fast and adaptive drilling control, as well as a multi-voltage option.
The machine is fitted with an RD525 rockdrill that offers high penetration rates as well as long tool life. It has two SB100i booms with an easy-to-use control system that offers three different modes for manual boom control, allowing a drilling coverage of 9.05m high by 14.8m wide. As with the new DT912D, the DT922i has the firm’s SICA control system.
Other features include a large cab with low noise levels and good all round visibility, sophisticated controls with a large graphic touch screen and joystick steering, as well as low energy LED lighting,
Other new technologies for use in tunnel drilling from Sandvik include the iSCAN 3D scanning and navigation system as well as new drill tools. The iSCAN system generates a 3D point cloud when the rig is driven to a new tunnel advance. Each new scan is added to the reference model, which also shows the rigs exact position at accuracy as high as 10mm. Underbreak and overbreak can be identified onboard and corrective actions can be taken immediately. According to Sandvik, using the iSCAN system can shorten each drilling cycle by 15-30 minutes, offering massive cost savings.
The newly-introduced top centre drill bits benefit from a novel raised front design. This has two or three front buttons raised a few millimetres above the gauge buttons located on the periphery of the bit. Additionally, the front buttons are set at a slight angle relative to the symmetric axis of the bit.
The firm says that the raised front drills a slightly recessed hole bottom pattern, which alters the rock-breaking action and improves performance. The bit also has a new cemented carbide grade GC80 that combines toughness with a softer centre, extending service life and grinding intervals.
2592 Herrenknecht has constructed a new tunnel boring machine (TBM) with a diameter of 15.87m. When in use this will be the largest TBM ever operated on a tunnel project in Europe.
The 4,800tonne machine has been constructed for the Santa Lucia Tunnel in the Apennines in Italy and is the largest machine ever made at Herrenknecht’s Schwanau plant. It has a diameter 200mm larger than the previous record holder for Europe, the 15.62m diameter TBM used for the Galleria Sparvo project, also in Italy. This new TBM will be used to drive a 7,528m long tunnel through heterogeneous subsoil for a road project located close to the city of Florence. The machine has been supplied to construction firm Pavimental and will be used to carry out a project for its client3623 Autostrade per l'Italia. The machine features an EPB shield and has a drive power of 8,750kW, while it can deliver a torque of 101,296kNm and has a 410tonne cutting wheel.
When this machine starts in operation, it will be one of 13 TBMs from Herrenknecht tunnel borers operating in Italy. Of these, eight have diameters of more than 8m.
This new large TBM will be used on a project for Autostrada A1 and will drive the longest of the 44 new road tunnels being constructed for the project. When the Santa Lucia Tunnel opens to traffic in 2019, it will cut the journey time from Bologna to Florence by 30%.
Both in tunnel drilling and TBM systems, new machines are now being built that offer major gains in performance.
The firm says that its advanced DD422iE rig offers major advantages for operation in tunnel jobs. With its battery power, the DD422iE jumbo can be driven to and from the face without any exhaust emissions, reducing ventilation needs. The machine also produces less heat than a diesel powered drill, offering further benefits for underground use.
For safety the battery features molten salt technology, which reduces the risk of fire. The battery is recharged in just 10 minutes during the drilling cycle as the rig is linked to an underground electrical supply when drilling. Regenerative braking also helps charge the battery.
The single boom DT912D offers high reach and is powered by a fuel efficient diesel that is Tier 4 Final compliant. This 24tonne rig is also equipped with an onboard compressor and water-tank for air-mist flushing. The machine is equipped with Sandvik’s latest, state-of-the-art control system and is said to offer high quality operation in tunnelling work.
The diesel-hydraulic machine features air-mist flushing and is designed for fast and accurate drifting and production drilling of 12-125m² cross sections. It is equipped with a high frequency RD525 rock drill and is powered by a 205kW
The rig has a 4m³/min onboard compressor and a 1,000 litre water tank for air-mist flushing, allowing it to operate independently from the tunnel infrastructure. This allows a longer drilling period from one set up, boosting cycle time efficiency and machine versatility. The compressor has the patented Sandvik Compressor Management System, which the firm claims can cut fuel consumption by up to 25%.
The machine can also move quickly to and from the face on its four-wheel-drive articulated carrier. The ergonomic FOPS/ROPS compliant cabin is available with a lifting system for better visibility. The rig also has the proven Sandvik Intelligent Control system Architecture (SICA), with built-in diagnostics and user-friendly controls.
Customers for the DT912D can select different instrumentation levels. These include the silver package for drilling angles and depth monitoring, while the gold package offering semi-automatic drilling according to drill plan. The platinum package has the advantage of automatic boom movements and drilling cycle. The gold and platinum packages are integrated with the Sandvik iSURE tunnel management tool for accurate drilling, charging and blasting plans. The iSURE system provides data collection and analysis reports for improving the work cycle and process and can be complemented with the new geoSURE rock mass analysis and visualisation system.
Meanwhile the 30tonne DT922i tunnelling jumbo offers high performance and productivity according to the firm. Said to be versatile and productive, this machine is fully automated machine and has been designed to help optimise drilling operations. The rig is mounted on a manoeuvrable articulated carrier with hydrostatic transmission and is equipped with a fast and adaptive drilling control, as well as a multi-voltage option.
The machine is fitted with an RD525 rockdrill that offers high penetration rates as well as long tool life. It has two SB100i booms with an easy-to-use control system that offers three different modes for manual boom control, allowing a drilling coverage of 9.05m high by 14.8m wide. As with the new DT912D, the DT922i has the firm’s SICA control system.
Other features include a large cab with low noise levels and good all round visibility, sophisticated controls with a large graphic touch screen and joystick steering, as well as low energy LED lighting,
Other new technologies for use in tunnel drilling from Sandvik include the iSCAN 3D scanning and navigation system as well as new drill tools. The iSCAN system generates a 3D point cloud when the rig is driven to a new tunnel advance. Each new scan is added to the reference model, which also shows the rigs exact position at accuracy as high as 10mm. Underbreak and overbreak can be identified onboard and corrective actions can be taken immediately. According to Sandvik, using the iSCAN system can shorten each drilling cycle by 15-30 minutes, offering massive cost savings.
The newly-introduced top centre drill bits benefit from a novel raised front design. This has two or three front buttons raised a few millimetres above the gauge buttons located on the periphery of the bit. Additionally, the front buttons are set at a slight angle relative to the symmetric axis of the bit.
The firm says that the raised front drills a slightly recessed hole bottom pattern, which alters the rock-breaking action and improves performance. The bit also has a new cemented carbide grade GC80 that combines toughness with a softer centre, extending service life and grinding intervals.
TBM advance
The 4,800tonne machine has been constructed for the Santa Lucia Tunnel in the Apennines in Italy and is the largest machine ever made at Herrenknecht’s Schwanau plant. It has a diameter 200mm larger than the previous record holder for Europe, the 15.62m diameter TBM used for the Galleria Sparvo project, also in Italy. This new TBM will be used to drive a 7,528m long tunnel through heterogeneous subsoil for a road project located close to the city of Florence. The machine has been supplied to construction firm Pavimental and will be used to carry out a project for its client
When this machine starts in operation, it will be one of 13 TBMs from Herrenknecht tunnel borers operating in Italy. Of these, eight have diameters of more than 8m.
This new large TBM will be used on a project for Autostrada A1 and will drive the longest of the 44 new road tunnels being constructed for the project. When the Santa Lucia Tunnel opens to traffic in 2019, it will cut the journey time from Bologna to Florence by 30%.