The challenging construction of India’s largest road tunnel is part of a vital US$500 million project aiming to connect the isolated northern state of Jammu and Kashmir with the rest of the vast and highly populated country. Guy Woodford reports Travelling on National Highway 1A (NH 1A) in northern India should be the dictionary definition of ordeal. The single lane, narrow and winding road crosses some of the steepest, most treacherous terrain on the planet. The arduous route becomes especially difficult t
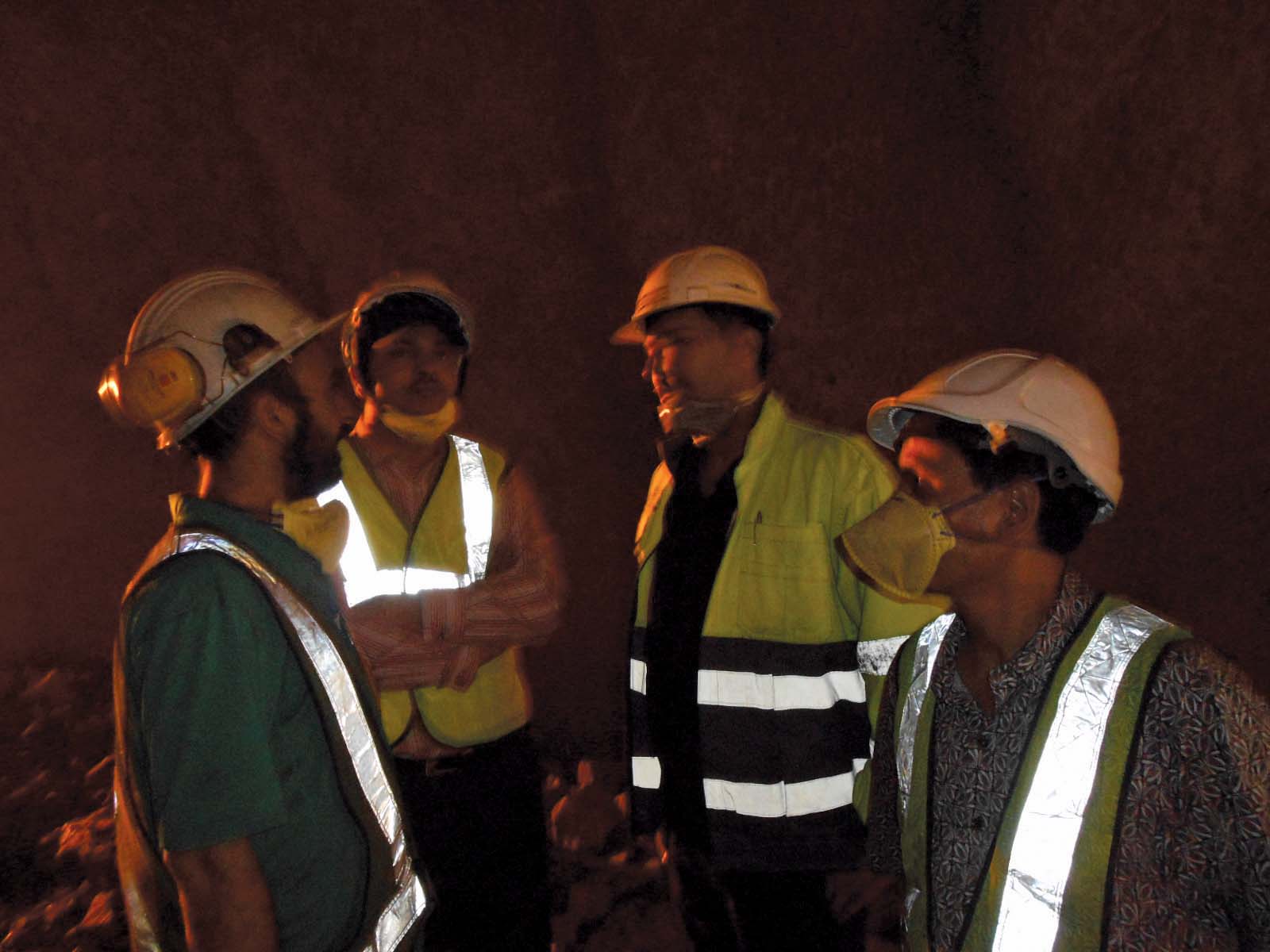
Members of the Chenani-Nashri twin-tube tunnel project team
The challenging construction of India’s largest road tunnel is part of a vital project aiming to connect the isolated northern state of Jammu and Kashmir with the rest of the vast and highly populated country. Guy Woodford reports
Travelling on National Highway 1A (NH 1A) in northern India should be the dictionary definition of ordeal. The single lane, narrow and winding road crosses some of the steepest, most treacherous terrain on the planet. The arduous route becomes especially difficult to navigate between the cities of Srinagar and Jammu – a 288km journey that can take up to half a day due to slow moving traffic and multiple traffic jams.Thankfully a solution is near due to a government initiative to upgrade this stretch of the NH 1A and turn it into a fast, yet also safe, all-year-round highway.
The multi-million dollar upgrade includes expanding the road to four lanes and the installation of several tunnels which together will reduce the total travelling time between the two cities to five hours. Equally important, the project will also make this relatively isolated region in a country boasting the world’s second largest population at 1.21 billion far more accessible to the rest of India.
One of the tunnels now being constructed is between the towns of Chenani and Nashri, which at 9km long will be the longest road tunnel in the country, shattering the previous longest road tunnel record currently held by the 2.5km long Jawahar Tunnel, part of the current and often heavily delayed road connection between Srinagar and Jammu in Jammu and Kashmir state.
A spokesman for the project concession holder said that the new road alignment and twin-tube tunnel between Chenani and Nashri will cut 30km off the distance and two hours off the journey between the towns.
Together with the parallel escape tunnel and cross passages this amounts to a total of 19km of tunnelling.
The spokesman points out, “Tunnelling in the Himalayas is difficult and the Chenani-Nashri tunnel is no exception. The mix of geological formations lead to a lot of distressing and cracking of the rock mass – it’s full of surprises.
Nature does not follow the text books!” The inhomogeneous rock at the tunnel site includes only 26m² of loose ground. There is 506m² of stable ground, 3,428m² of slightly overbreaking ground, 1,411m² of friable and 2,504m² of heavily friable ground, and 673m² of pressure exerting and 435m² of heavy pressure exerting ground.
The project concession holder is a subsidiary of one of India s largest private sector BOT (build-operate-transfer) road operators, engaged in developing designing, operating, maintaining and facilitating surface transportation infrastructure projects in 18 states in India and four other countries.
The concession holder parent company’s objective is to transform India’s road systems and thereby drive economic growth. Coupled with this, it exercises a broad programme of social responsibility through which it provides education facilities and support for communities along the highways it builds.
The Chenani-Nashri tunnel contract was awarded on an EPC (Engineering, Procurement & Construction) basis. Using a fleet of seven Atlas Copco drill rigs, the Chenani-Nashri tunnel is being excavated according to the NATM (New Austrian Tunnelling Method).The fleet includes four Boomer XE3 C rigs with ABC Total (fully automatic) and three Boomer E2 C rigs with ABC Regular (semi-automatic).
A spokesman for the project’s lead contractor said, “Progress all hinges on one thing – the pace of the face drilling rigs. If the rigs stop, everything stops. Our crews have the excavation cycle down to 10 to 12 hours and we are improving steadily. We are looking for three blasting rounds per day with two 12-hour shifts and I’m certain we will achieve it.”
The tunnel enters and exits the mountain at an elevation of 1,200m. When complete it will be 14m wide and 10m high. A smaller, 6x6m escape tunnel is also being built alongside the main tunnel where the lead contractor is using
The rock in this region consists mostly of sandy shale, mudstone, siltstone and soft sandstone, and drilling precision is of the utmost importance to avoid the extra costs associated with underbreak or overbreak.
Another spokesman for the lead contractor points out that this is where the automated features of the Atlas Copco rigs are proving their worth. A typical example, he says, is the Measure While-Drilling (MWD) function on the Boomer XE3 C.
He adds, “This rig has been used at the South Portal to verify what we expected to find in the rock mass. The escape tunnel runs ahead of the main tunnel so the rig is used for probe drilling, checking to see that the rock ahead is what we anticipate.”
To meet the requirements, the lead contractor has developed a skilled drilling crew with the aid of Atlas Copco’s Master Driller training program. Three months prior to the project, and before ever seeing a production drill rig, 30 trainee operators completed all three levels of the course – bronze silver and gold – using an Atlas Copco Boomer drill rig simulator.
It takes at least 15 days to complete the course so the simulator remained on the site for three months to ensure that all drillers were sufficiently trained.
The lead contractor’s spokesman explains how lasers are used to position the rigs at the face. Two alignment plates are mounted on a rig’s boom. When the red laser beam passes through the plates, the boom is parallel to the laser at a known offset.
A single two-boom Boomer E2 C operator can set one boom in place, start drilling, and then turn his attention to the second boom, continuing back and forth throughout the round. The operators can drill 100 holes over the 42m² escape tunnel face in just 90 minutes.
The Boomer XE3 C with ABC Total drills the 76m² main heading with its drill pattern of 152 blastholes in one hour 45 minutes.
Its precision has even allowed the contractor to optimise the drill plan down to 130 holes. “I have an advanced piece of equipment,” the lead contractor spokesman says, “and I am going to exploit it to its full potential.”
The main tunnel is being excavated in two levels with the Boomer XE3 C covering the 6m top heading as well as 4m split bench. Excavation of the escape tunnel is being advanced 200m ahead of the main tunnel and the Boomer E2 C drills the whole face. Blasted rounds vary ranging from 2.5m to 4m.
At the South Portal, the lead contractor spokesman explains that rock support is used to assist natural rock convergence which must be less than two millimetres per month.
Reinforcement consists of two rows of 5m Atlas Copco Swellex PM24 rock bolts, eight in one row and nine in the next. The rows are spaced 2.5m apart where no convergence is noted. Where convergence is noted, the rows are 2m apart.
The rockbolt holes are drilled with the same 51mm bit used for the blastholes. Two bolts are installed in the benches, one on each side. In the escape tunnel, 5m Swellex PM24 bolts are installed in two rows, the first row with six bolts, the second with seven.
Fibre-reinforced shotcrete is applied in two overlapping stages to a thickness of at least 15cm. The first 5cm is applied immediately after bolting. Setup time is fast enough to provide almost immediate support. The lead contractor spokesman said that with proper scaling and bolting, the 5cm fibre-reinforced shotcrete enables them to progress at a good pace safely, saving them the extra step of bolting up mesh.
The second layer of 10cm shotcrete overlaps the initial 5cm shotcreting during the next advance and provides the necessary support until the permanent lining is installed.
In this way, convergence during excavation has been kept to a minimum without compromising on safety or progress. Lattice girders are used wherever movement is anticipated and will become an integrated part of the final tunnel lining.
To speed up work, the lead contractor has also hired four
The lead contractor spokesman adds, “We are in a remote location here with great hardship and logistics difficulties. But we will succeed because we have the best people in the right places. Atlas Copco is doing a good job of supporting us and we challenge each other to achieve excellence every day.”
Of the economic and social impact the completed overall NH 1A upgrade will have, Debabrata Sain, Atlas Copco’s India marketing manager, says, “The 288km distance between Jammu and Srinagar will be reduced to 238k, but more importantly the 12-hour journey will be covered in about five hours, avoiding perilous points such as Khooni Nala, known as bloody path, where shooting stones slide at the speed of a bullet taking a heavy toll on lives. The tunnels will also end the snow-related traffic jams that last several days.”
Sain said shorter travelling distances within Jammu and Kashmir and on to further destinations will save individual citizen and business vehicle fuel costs, vehicle wear and tear costs, and, at the same time, reduce environmental pollution through lower carbon emissions. “There will be other benefits such as increased commerce and tourism, more employment for local people, and skill development among local youths,” he added.
To date, the NH 1A upgrade has employed 649 people from Jammu and Kashmir region, including 281 from the city of Udhampur and 298 from Ramban, a local town. The overall project’s lead contractor has also run local community projects such as free health check-UPS, a water supply initiative for schools, and the building of community halls.
Forever Delayed
It takes ten hours or more to transport a load of fruit or vegetables grown in the Srinagar Valley to Jammu via NH 1A, the Valley’s only link to the Indian market southward. The Traffic jams up at each bend and tailbacks are long on the straights as motorists have to wait in line to pass the numerous Tata trucks typical of the Jammu and Kashmir region.
These ornately decorated trucks are slow as they strain on the mountain grades, their drivers pulling hard on their steering wheels through each tight bend, while other vehicles try to pass, often dangerously close.
The new twin-tube tunnel from Chenani to Nashri will go a long way to relieving these bottlenecks and make the journey both shorter and considerably safer. Of the difference the Chenani-Nashri twin-tube tunnel, within the overall NH 1A upgrade, will make, local truck driver Mushtaq Ali says, “It will save us enormous time, about 250 rupees (US$4.10) in fuel, and in vehicle wear and tear. It will also relieve several bottlenecks on each TRIP.”