Rapid growth in a major Australian city in recent years has created new problems for the infrastructure and especially transport Expansion in the city of Brisbane, the Queensland state capital and the third largest city in the country, is set to continue and some 1,500 people arrive/week from within Australia and from other parts of the world. At this rate by 2026 the city's population should increase by 1.4 million: at present it is 1.8 million. To cope, the Queensland government and city council have ini
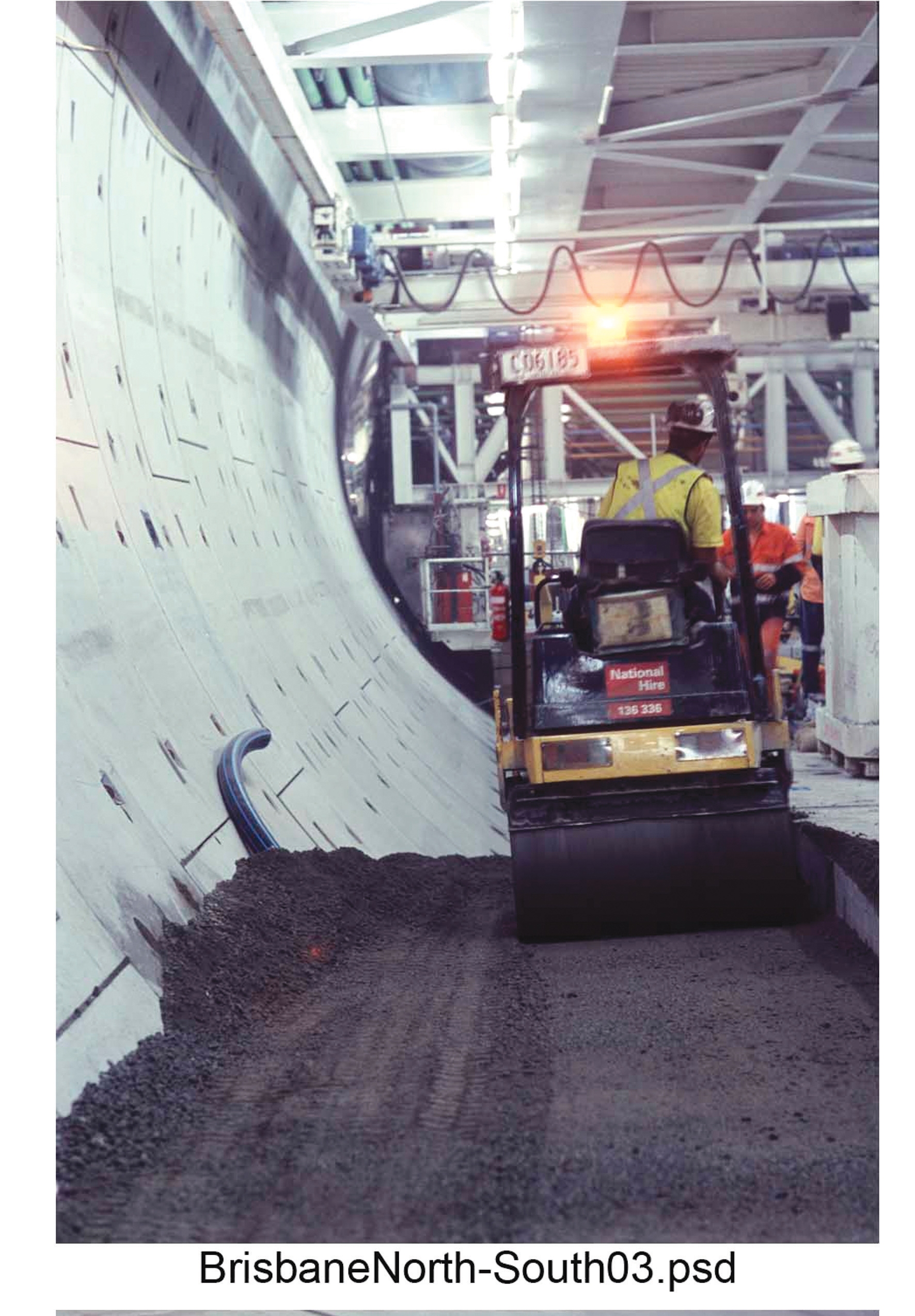
The new tunnel link will be the longest in Australia when complete
Rapid growth in a major Australian city in recent years has created new problems for the infrastructure and especially transport
Expansion in the city of Brisbane, the Queensland state capital and the third largest city in the country, is set to continue and some 1,500 people arrive/week from within Australia and from other parts of the world. At this rate by 2026 the city's population should increase by 1.4 million: at present it is 1.8 million.To cope, the Queensland government and city council have initiated a major programme of upgrades within a new Transport Programme, and for this car-based city, spread wide on the eastern coast, this means primarily roads and new motorways.
In the city there is the TransApex plan to upgrade roads; outside the local motorway network is being expanded, and new links are planned for the airport.
The first-stage city plan is to relieve central congestion by taking traffic underneath the now well developed centre in a new tunnel running north-south under the Brisbane river. The 4.8km long twin-bore connection will be the longest in Australia when completed in 2010. Connectors and interchanges at the ends of the scheme bring the total length to 6.8km.
The road will will be a much-needed additional link across the winding Brisbane river and will join the Inner City Bypass in the north to the Pacific Highway running out of the city southwards and on to the Gold Coast holiday resorts and commuter areas.
There are too few crossings at present and although the Pacific Highway has a bridge which continues on into the city along the Riverside Expressway, this is often congested. Another well known bridge, the immediate post-war steel Jim Story steel truss across the river, is too small for modern traffic loads.
The tunnel passes underneath the Jim Story Bridge and its Highway 15, following the same line running down the centre of the long thin peninsula of Kangaroo Point. The residential area of the Point is formed by a sharp turn on the river in the north which then almost doubles back on itself, just west of the cluttered high rise central business district.
Brisbane City Council believes that demand will make the link self-financing so the project will be a toll road, built as a public-private-partnership under a 45-year concession with the RiverCity Motorway (RCM) group.
RCM let the A$2 billion (US$1.93 billion) design and construction project to a joint venture comprising
"We were given a very short delivery time," said construction director Adam Hudson for the JV, "beginning work in August 2006 and with a completion date for October 2010." At present the contractor hopes to pull even that date forwards, finishing at the end of 2009.
Main tunnelling work for the project began in February this year when the first of two huge 12.4m diameter hard rock tunnel boring machines (TBMs) began its drive south from a cramped site at Bowen Hills at the northern end of the scheme, passing first of all under the agricultural and general showgrounds and on towards the river. A second machine began work shortly afterwards.
Two TBMs are being used to maintain speed on the job rather than run a single machine one side and then drive back to form the other two lane bore. Each will drive 4km of the total 4.8km tunnel length in two phases. A middle section where a junction joins the tunnel to roads halfway down Kangaroo point is being built with roadheaders. The two TBMs will be pulled through this section which is wider than the standard drive, to complete the section on the other side.
The rock they are going through is tough and, as it happens is known as Brisbane Tuff, a fused volcanic ash. There is also metamorphic rock to go through of about the same hardness.
To speed the drive the machines are of a relatively advanced telescopic with their cutting wheel heads separated from the section behind by a telscopicing intermediate section. This means the machine can continue cutting while the segment erector for the precast tunnel lining, is still at work.
"Rock grippers on the middle section hold allow the forward head section to be jacked forwards to put pressure on the cutting head, while the segment erector is static," said Martin Wieser, TBM project manager at the site.
Once each nine section concrete ring is complete the jacks are withdrawn on the grippers and both the head and the gripper section are pushed forwards together by a second set of jacks pushing on the newly installed lining. But sometimes the machine will be used in single mode only, without the grippers if the rock is not strong. "The rock is expected to be fairly sound but does have faulting and cracks," said Wieser.
There is also a chance that this could mean water inflow particularly at the deepest 60m point of the drive where the machines are just under the river. In case this happens the two Herrenknecht TBMs have been built with special seals for the front part of the machines allowing the head sections to resist up to six atmospheres of pressure. If they have to be used, and Wieser is hoping that it will not be necessary, the machine will have to work in single mode, or stop while grouting operations are carried out through the front of the machine. On board drills allow forward grouting or probe drilling operations to test the rock ahead. Both TBMs are just a couple of hundred metres into the rock at present but with performance climbing, Hudson wants to achieve 20m/day in double action mode.
Meanwhile, seven roadheaders machines are busy on the central junction halfway along the project to make sure the main part is excavated in time for the arrival of the TBMS which must be dragged through the 800m section. Some of the roadheaders are also being used to create cross passages between the two two lane tunnel bores. These are at frequent 120m intervals, now the safety standard in Australia for escape passages in case of fire.
Outside, the project has had to create a soundproofed disposal facility for the muck to prevent local disruption, including sound boarding the conveyors that bring the material out from the tunnels to the loading area. Trucks for carrying away the rock chips are brought in on dedicated slip roads that will eventually form part of the complex interchanges for the tunnel entrances at either end. The contractor's work includes construction of these bridge links using a special launching gantry.
The tunnels will be fitted with a host of electronic control and detectors systems including video incident spotting systems and variable message and variable speed equipment, the latest radio interrupt transmitters for emergency messages and heat detectors. "We are also installing a deluge system which dumps a huge amount of water very quickly onto a fire," said Hudson.