Progress has been good for an important underground road link in Finland reports Adrian Greeman. Assuming all goes well, the new Ranta, or Lakeside, tunnel in Tampere will open in full six months early; traffic could be running by the end of this year. Work on transforming the rundown city centre with new developments will get a major boost. It is a major achievement on a four-year-long project bringing significant benefits to one of Finland's largest cities. From the government's point of view the scheme w
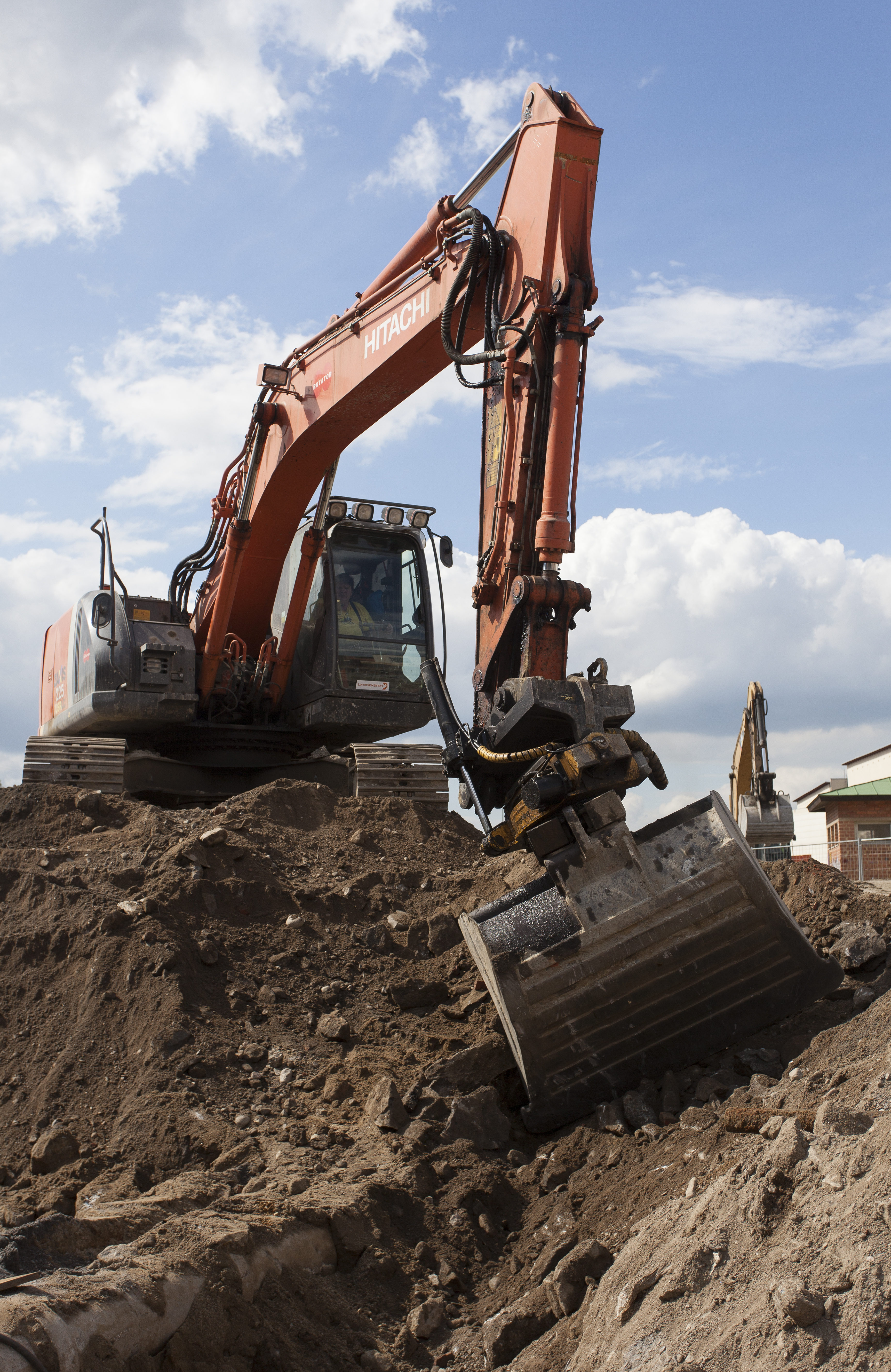
A substantial earthmoving operation has been carried out on the surface
Progress has been good for an important underground road link in Finland reports Adrian Greeman
Assuming all goes well, the new Ranta, or Lakeside, tunnel in Tampere will open in full six months early; traffic could be running by the end of this year. Work on transforming the rundown city centre with new developments will get a major boost. It is a major achievement on a four-year-long project bringing significant benefits to one of Finland's largest cities. From the government's point of view the scheme will improve both long-distance east-west traffic links and the local congestion in the city, on a road which is one of the busiest in Finland. The city is something of a bottleneck for longer distance traffic.
It will also bring financial benefits to the road authority client and to the contractor, who have been working together in a new alliancing system being tried here only for the second time. They share savings.
The project may not be so long as some, but it is crucially sited in the middle of this former industrial city, underneath old buildings, roads, a railway and a river link. The central section dives into a large tunnel over 2.3km and there are partially underground interchanges and ramps excavated at each end. There is provision for a third interchange in the centre, with some ramps pre-excavated for future connections when needed.
It is also critically a key part of the important route 12 highway from Turku port on the Baltic Sea in the west, to Lahti via Tampere, which is in the centre of the more populous south of Finland, in Pirkanmaa region.
Here the road runs across a narrow isthmus separating two great lakes, the Näsijärvi to the north and the Pyhäjärvi on the southern side which dominate the city to the north and south. These are among the largest of Finland's many thousands of lakes.
As well as slowing the traffic, the road, and industrial developments around this narrow neck of land have also previously prevented what is now prime residential land being developed on its north side; when the tunnel is complete in 2017 it will allow major development of some 4,000 apartments to go ahead. These will be of major value. Once the road is replaced and there is only local traffic, the area will be quiet, central and with significant lakeside frontage for the apartment complexes. The site development work will also include landscaping.
Historically, Tampere originated on and around this narrow land connection which is cut by a precipitous rapids channel, the Tammerkoski, draining the higher northern lake into the other. An 18m difference in levels was exploited, first for water mills and then the three major hydropower plants that were built in the 19th century, which in turn led to significant industrial development.
The city has long since been the industrial heartland of Finland, known as its "Manchester" and the hydroelectric plants are still important. Notable factories here include the well-known construction and mining drill rig manufacturer Tamrock, now part of Sandvik. The old buildings still sit near the Tammerkoski though the factory has now mostly moved to a location 7km away.
There are many other metallurgical, mechanical and engineering companies, as well as textiles, pulp and paper, though modern development has taken a path towards information and telecommunications. Heavier industry has moved and as with many cities the centre is ready for redevelopment. Tampere has been keen to get the work done and is paying over 60% of the €180 million project cost, with the rest coming from the central government's Transport Agency. Some European Union money helps with the costs.
The two clients are working together with the contractor and designers in an "alliancing" scheme, a system imported from Australia and one of the first major uses of the method in Europe. The contractor is a joint venture led by Finland's largest civils firm3064 Lemminkäinen Construction management and design company, A-insinöörit and consultant Saanio & Riekkola.
The overall project planning and design was developed over nearly 12 months by the team with construction beginning in October 2013. The scheme comprises a central twin tunnel, each side carrying two-lane bores in one direction.
There are major multilevel junctions at either end with flyover and bridge connections, and lengths of at-grade highway. It all replaces some six existing junctions with traffic lights, one of the main causes of slower traffic flows according to Finnish Transport Agency project engineer for the scheme, Mauri Mäkiaho.
Excavation is needed both for the tunnel itself, cross passages between them and for the sunken parts of the big interchange junctions at either end. A number of small access tunnels, for ventilation and services, are also included; at one point there were around 14 blasting faces being worked, though only for the initial stages.
As everywhere in Finland and other Nordic states, excavation means drill and blast. Virtually the whole country is formed from ancient Baltic shield rocks, granites and gneiss says Mäkiaho, though in this area it is primarily gneiss.
One of the major concerns for risk management on the scheme has been the condition of the rock and its fracturing, particularly for water ingress, as the tunnel alignment runs alongside a very large lake and some 15m underneath the "river" channel which drains it.
Substantial ground investigation was carried out before the contract was let, and then during the alliancing selection process and design development the contractor asked for significantly more to alleviate concerns about the rock condition.
"We did some thousands of holes," said Mäkiaho. "But that is not so unusual for a scheme like this in Finland and particularly when trying to reduce the risk."
Top drilling from grout injection to treat the ground has been carried out at various points, explained Jarkko Meriläinen, one of the project engineers on the scheme. "Rock is variable in condition, not good but not bad either.”
As expected the western end proved more fractured, and even a little more than originally anticipated. But this was easily absorbed by the alliancing framework which had provision for risk distribution and has not caused any holdup.
Treatment was carried out by grouting from above, and also from forward drilling, said Meriläinen. The drilling also allowed pre-assessment of rock condition as the contractor moved forwards.
Probe holes were around 54mm in diameter and 24m deep and were then pressure tested with water, he explains. If there is significant leakage then a pattern of grouting is done from the tunnel face.
To cope with the long hole drilling required, and for the explosives drilling on large tunnel faces over 8m high and 16m across, the project needed some large machines. Ironically these were two Swedish161 Atlas Copco rigs initially, working from the central of three work sites on the project, with bores going in each direction. Both are automated.
But supplementing these the contractor had two brand new machines, and appropriately enough it bought them from the local producer325 Sandvik. Few customers can be quite so much on the doorstep for the local equipment maker. Drilling tools are Sandvik too, though the bits are from local supplier Robit.
The faces were charged by a two-man team working from baskets on a Finnish-made3708 Normet face machine.
The new drill rigs selected were the latest fully automated Sandvik DT1131i three boom units, which use special iSURE tunnel management software for designing and implementing the drill patterns. The design made by the site engineers is uploaded on the machine and used to control the positioning of the booms and the drilling, allowing greater accuracy.
These new machines worked at the ends of the project, each covering the two faces of the main bores and also drilling for the side and access tunnels and for the smaller cross passages too, which are just 11m long, connecting the two directions of the main tunnel. The cross passages are positioned every 190m and are 7.2m wide and 8m high.
One blast/day was used for most of the drilling portion though it would have been possible to go faster if needed. An advantage of the computerised rigs is the accuracy of the drill patterns, which can help reduce vibrations.
The tunnels run underneath housing areas in the middle part of the peninsula, and although it is up to 40m deep, there are still concerns about vibration. "A lot of the houses are founded directly on to the rockhead," said Meriläinen, "so the vibration can carry through quite a lot". Others are on softer ground however.
"Fortunately there are very good records in Tampere," said Mäkiaho, "and it has been possible to determine the way the foundations of most of the buildings were built from those."
Where necessary, he explained that each blast round could be modified according to the circumstances above, to limit the risk of damage.
Many of the explosion sequences were carried out as long blasts, lasting a significant eight seconds, to reduce noise and vibration. With more tightly placed holes the explosion could develop more evenly.
Buildings were instrumented to assess the effects but there were few problems said Mäkiaho. "They were inspected afterwards too but there are no big cracks or problems."
Minimising vibration was also important underneath a railway line. And fine tuning the blasting rounds enabled the spoil size to be reduced making it easier to load according to Meriläinen.
Just after blasting, a thin shotcrete layer was applied for safety – a Normet machine bustled about the site for this work – and a 1m2 pattern of rock bolts for support. These holes were drilled with the main rigs.
Mucking out was carried out using178 Caterpillar and 2394 Volvo loaders which had plenty of room to manoeuvre in the large tunnels. Spoil was disposed of locally, needing to move just 500m to a lakeside dumping area. In fact this material was useful for the city which has had city reclamation works along the lake shore as part of the overall redevelopment scheme.
"We loaded into normal trucks mostly but from some of the worksite locations it was also possible to take some of the spoil with 15tonne articulated Volvo dumptrucks," said Meriläinen, "because the site and the disposal area are more or less directly linked."
Most of around 1 million m3 of spoil from the tunnels was used this way but, "…we also crushed and screened some of the rock to use it for aggregate for the road construction in the tunnels," said Meriläinen.
There was also significant rock produced at either end of the site from the interchanges. These were excavated by conventional benching methods, using smaller surface drills and excavator mounted rock breakers.
"We have a sister company in quarrying and rock supply," said Meriläinen, "and we borrowed the top drills from them."
The western approach interchange also includes a 100m-long section of "artificial" concrete tunnel, which will be backfilled after it is built. There is more soft ground at the surface at the western end but the rockhead also had to be blasted down some 15-20m or so to make space for the concrete tunnel section.
Some of the softer ground was contaminated with industrial products, most of which came from paper processing, and had to be removed to special disposal sites. The presence of this bad ground was known before the work commenced but turned out to be at the maximum end of what was expected.
"But the alliancing process had made sure we were prepared for this and it did not add significant claims or costs," said Mäkiaho.
Work is currently focussed on finishing structures for the interchanges, which is largely civil and concreting, road surfacing and the mechanical and electrical works.
In an alliance the contractor, designer and client sign an agreement to work together, sharing information in a transparent manner and working through the design and construction process as a team. The alliance shares the risks of the project using agreed pain-gain formulas in which cost overruns or schedule and cost savings produce a penalty or benefit for both the client side and the contractor.
"We have modified the Australian method by fixing it to comply with European procurement law but it is similar," explained Mauri Mäkiaho from the Finnish Transport Agency (Liikennevirasto).
"And we have made some trips to Australia to see how it works," said Esko Mulari, Lemminkäinen project director.
"The alliance is created and set up with a chosen contractor before the target price for the job is agreed," said Mäkiaho. "There is a competitive process at the beginning with the contractors assessed on a series of criteria according to technical ability, the nature of the resources and the team they will bring to the project. For the Ranta tunnel this started with a five-way competitive process, narrowed down to two and eventually selecting the Lemminkäinen consortium.”
Starting with an outline design the alliance team then works through the detail design process for several months before the project begins on the ground, particularly examining all the risk elements. For Tampere these included some contaminated ground, the rock conditions, and traffic disruption in the city. Work began in June 2012 on this process and has continued through the project.
The idea is to pin down all the risk elements," said Mäkiaho, "rather than oblige the contractor to price them into the contract with all the possibilities for claims and conflict that means."
He estimated that conventional methods would have resulted in a price tag another third or so higher. "But here as problems emerge you work through them together. Risk in the alliance is just €3 million."
A part of that is simply working side by side and he said, "We hired a big office at the start and we all moved in there for the project. There are also lots of workshops and meetings to work through issues. You use the expertise from all sides coordinated together."
"This is only our second project this way but we are learning all the time from it. Helsinki University has also been studying the way it is going."
Benefits being felt now as the project comes to an end, include better quality construction; time savings, and greater safety.
The alliance also includes a cost gain bonus if there is limited or no maintenance required once the contract is complete. And six months has been shaved from the original time schedule which suits the city.
Elements being considered at present are technical, and mechanical and electrical systems for the tunnel; making them work together is a key in reducing risk.
In January this year there was already some €3 million to be shared among the participants reported Mäkiaho.
In fact he said this has worked really well. "Problems are easier to solve and there is less conflict and sticking to contract barriers. Instead it becomes a technical matter of sitting down around the table to sort out what has to be done and how it might affect the schedule."
"The transport Authority has four projects going like this at present and it has spread quite fast in other sectors too."
Assuming all goes well, the new Ranta, or Lakeside, tunnel in Tampere will open in full six months early; traffic could be running by the end of this year. Work on transforming the rundown city centre with new developments will get a major boost. It is a major achievement on a four-year-long project bringing significant benefits to one of Finland's largest cities. From the government's point of view the scheme will improve both long-distance east-west traffic links and the local congestion in the city, on a road which is one of the busiest in Finland. The city is something of a bottleneck for longer distance traffic.
It will also bring financial benefits to the road authority client and to the contractor, who have been working together in a new alliancing system being tried here only for the second time. They share savings.
The project may not be so long as some, but it is crucially sited in the middle of this former industrial city, underneath old buildings, roads, a railway and a river link. The central section dives into a large tunnel over 2.3km and there are partially underground interchanges and ramps excavated at each end. There is provision for a third interchange in the centre, with some ramps pre-excavated for future connections when needed.
It is also critically a key part of the important route 12 highway from Turku port on the Baltic Sea in the west, to Lahti via Tampere, which is in the centre of the more populous south of Finland, in Pirkanmaa region.
Here the road runs across a narrow isthmus separating two great lakes, the Näsijärvi to the north and the Pyhäjärvi on the southern side which dominate the city to the north and south. These are among the largest of Finland's many thousands of lakes.
As well as slowing the traffic, the road, and industrial developments around this narrow neck of land have also previously prevented what is now prime residential land being developed on its north side; when the tunnel is complete in 2017 it will allow major development of some 4,000 apartments to go ahead. These will be of major value. Once the road is replaced and there is only local traffic, the area will be quiet, central and with significant lakeside frontage for the apartment complexes. The site development work will also include landscaping.
Historically, Tampere originated on and around this narrow land connection which is cut by a precipitous rapids channel, the Tammerkoski, draining the higher northern lake into the other. An 18m difference in levels was exploited, first for water mills and then the three major hydropower plants that were built in the 19th century, which in turn led to significant industrial development.
The city has long since been the industrial heartland of Finland, known as its "Manchester" and the hydroelectric plants are still important. Notable factories here include the well-known construction and mining drill rig manufacturer Tamrock, now part of Sandvik. The old buildings still sit near the Tammerkoski though the factory has now mostly moved to a location 7km away.
There are many other metallurgical, mechanical and engineering companies, as well as textiles, pulp and paper, though modern development has taken a path towards information and telecommunications. Heavier industry has moved and as with many cities the centre is ready for redevelopment. Tampere has been keen to get the work done and is paying over 60% of the €180 million project cost, with the rest coming from the central government's Transport Agency. Some European Union money helps with the costs.
The two clients are working together with the contractor and designers in an "alliancing" scheme, a system imported from Australia and one of the first major uses of the method in Europe. The contractor is a joint venture led by Finland's largest civils firm
The overall project planning and design was developed over nearly 12 months by the team with construction beginning in October 2013. The scheme comprises a central twin tunnel, each side carrying two-lane bores in one direction.
There are major multilevel junctions at either end with flyover and bridge connections, and lengths of at-grade highway. It all replaces some six existing junctions with traffic lights, one of the main causes of slower traffic flows according to Finnish Transport Agency project engineer for the scheme, Mauri Mäkiaho.
Excavation is needed both for the tunnel itself, cross passages between them and for the sunken parts of the big interchange junctions at either end. A number of small access tunnels, for ventilation and services, are also included; at one point there were around 14 blasting faces being worked, though only for the initial stages.
As everywhere in Finland and other Nordic states, excavation means drill and blast. Virtually the whole country is formed from ancient Baltic shield rocks, granites and gneiss says Mäkiaho, though in this area it is primarily gneiss.
One of the major concerns for risk management on the scheme has been the condition of the rock and its fracturing, particularly for water ingress, as the tunnel alignment runs alongside a very large lake and some 15m underneath the "river" channel which drains it.
Substantial ground investigation was carried out before the contract was let, and then during the alliancing selection process and design development the contractor asked for significantly more to alleviate concerns about the rock condition.
"We did some thousands of holes," said Mäkiaho. "But that is not so unusual for a scheme like this in Finland and particularly when trying to reduce the risk."
Top drilling from grout injection to treat the ground has been carried out at various points, explained Jarkko Meriläinen, one of the project engineers on the scheme. "Rock is variable in condition, not good but not bad either.”
As expected the western end proved more fractured, and even a little more than originally anticipated. But this was easily absorbed by the alliancing framework which had provision for risk distribution and has not caused any holdup.
Treatment was carried out by grouting from above, and also from forward drilling, said Meriläinen. The drilling also allowed pre-assessment of rock condition as the contractor moved forwards.
Probe holes were around 54mm in diameter and 24m deep and were then pressure tested with water, he explains. If there is significant leakage then a pattern of grouting is done from the tunnel face.
To cope with the long hole drilling required, and for the explosives drilling on large tunnel faces over 8m high and 16m across, the project needed some large machines. Ironically these were two Swedish
But supplementing these the contractor had two brand new machines, and appropriately enough it bought them from the local producer
The faces were charged by a two-man team working from baskets on a Finnish-made
The new drill rigs selected were the latest fully automated Sandvik DT1131i three boom units, which use special iSURE tunnel management software for designing and implementing the drill patterns. The design made by the site engineers is uploaded on the machine and used to control the positioning of the booms and the drilling, allowing greater accuracy.
These new machines worked at the ends of the project, each covering the two faces of the main bores and also drilling for the side and access tunnels and for the smaller cross passages too, which are just 11m long, connecting the two directions of the main tunnel. The cross passages are positioned every 190m and are 7.2m wide and 8m high.
One blast/day was used for most of the drilling portion though it would have been possible to go faster if needed. An advantage of the computerised rigs is the accuracy of the drill patterns, which can help reduce vibrations.
The tunnels run underneath housing areas in the middle part of the peninsula, and although it is up to 40m deep, there are still concerns about vibration. "A lot of the houses are founded directly on to the rockhead," said Meriläinen, "so the vibration can carry through quite a lot". Others are on softer ground however.
"Fortunately there are very good records in Tampere," said Mäkiaho, "and it has been possible to determine the way the foundations of most of the buildings were built from those."
Where necessary, he explained that each blast round could be modified according to the circumstances above, to limit the risk of damage.
Many of the explosion sequences were carried out as long blasts, lasting a significant eight seconds, to reduce noise and vibration. With more tightly placed holes the explosion could develop more evenly.
Buildings were instrumented to assess the effects but there were few problems said Mäkiaho. "They were inspected afterwards too but there are no big cracks or problems."
Minimising vibration was also important underneath a railway line. And fine tuning the blasting rounds enabled the spoil size to be reduced making it easier to load according to Meriläinen.
Just after blasting, a thin shotcrete layer was applied for safety – a Normet machine bustled about the site for this work – and a 1m2 pattern of rock bolts for support. These holes were drilled with the main rigs.
Mucking out was carried out using
"We loaded into normal trucks mostly but from some of the worksite locations it was also possible to take some of the spoil with 15tonne articulated Volvo dumptrucks," said Meriläinen, "because the site and the disposal area are more or less directly linked."
Most of around 1 million m3 of spoil from the tunnels was used this way but, "…we also crushed and screened some of the rock to use it for aggregate for the road construction in the tunnels," said Meriläinen.
There was also significant rock produced at either end of the site from the interchanges. These were excavated by conventional benching methods, using smaller surface drills and excavator mounted rock breakers.
"We have a sister company in quarrying and rock supply," said Meriläinen, "and we borrowed the top drills from them."
The western approach interchange also includes a 100m-long section of "artificial" concrete tunnel, which will be backfilled after it is built. There is more soft ground at the surface at the western end but the rockhead also had to be blasted down some 15-20m or so to make space for the concrete tunnel section.
Some of the softer ground was contaminated with industrial products, most of which came from paper processing, and had to be removed to special disposal sites. The presence of this bad ground was known before the work commenced but turned out to be at the maximum end of what was expected.
"But the alliancing process had made sure we were prepared for this and it did not add significant claims or costs," said Mäkiaho.
Work is currently focussed on finishing structures for the interchanges, which is largely civil and concreting, road surfacing and the mechanical and electrical works.
Finnish alliance
The Tampere project is not the first alliance in Finland but was among the first two or three, and the largest when it began. The system has been developed for government infrastructure works based on ways of working which evolved originally in Australia.In an alliance the contractor, designer and client sign an agreement to work together, sharing information in a transparent manner and working through the design and construction process as a team. The alliance shares the risks of the project using agreed pain-gain formulas in which cost overruns or schedule and cost savings produce a penalty or benefit for both the client side and the contractor.
"We have modified the Australian method by fixing it to comply with European procurement law but it is similar," explained Mauri Mäkiaho from the Finnish Transport Agency (Liikennevirasto).
"And we have made some trips to Australia to see how it works," said Esko Mulari, Lemminkäinen project director.
"The alliance is created and set up with a chosen contractor before the target price for the job is agreed," said Mäkiaho. "There is a competitive process at the beginning with the contractors assessed on a series of criteria according to technical ability, the nature of the resources and the team they will bring to the project. For the Ranta tunnel this started with a five-way competitive process, narrowed down to two and eventually selecting the Lemminkäinen consortium.”
Starting with an outline design the alliance team then works through the detail design process for several months before the project begins on the ground, particularly examining all the risk elements. For Tampere these included some contaminated ground, the rock conditions, and traffic disruption in the city. Work began in June 2012 on this process and has continued through the project.
The idea is to pin down all the risk elements," said Mäkiaho, "rather than oblige the contractor to price them into the contract with all the possibilities for claims and conflict that means."
He estimated that conventional methods would have resulted in a price tag another third or so higher. "But here as problems emerge you work through them together. Risk in the alliance is just €3 million."
A part of that is simply working side by side and he said, "We hired a big office at the start and we all moved in there for the project. There are also lots of workshops and meetings to work through issues. You use the expertise from all sides coordinated together."
"This is only our second project this way but we are learning all the time from it. Helsinki University has also been studying the way it is going."
Benefits being felt now as the project comes to an end, include better quality construction; time savings, and greater safety.
The alliance also includes a cost gain bonus if there is limited or no maintenance required once the contract is complete. And six months has been shaved from the original time schedule which suits the city.
Elements being considered at present are technical, and mechanical and electrical systems for the tunnel; making them work together is a key in reducing risk.
In January this year there was already some €3 million to be shared among the participants reported Mäkiaho.
In fact he said this has worked really well. "Problems are easier to solve and there is less conflict and sticking to contract barriers. Instead it becomes a technical matter of sitting down around the table to sort out what has to be done and how it might affect the schedule."
"The transport Authority has four projects going like this at present and it has spread quite fast in other sectors too."