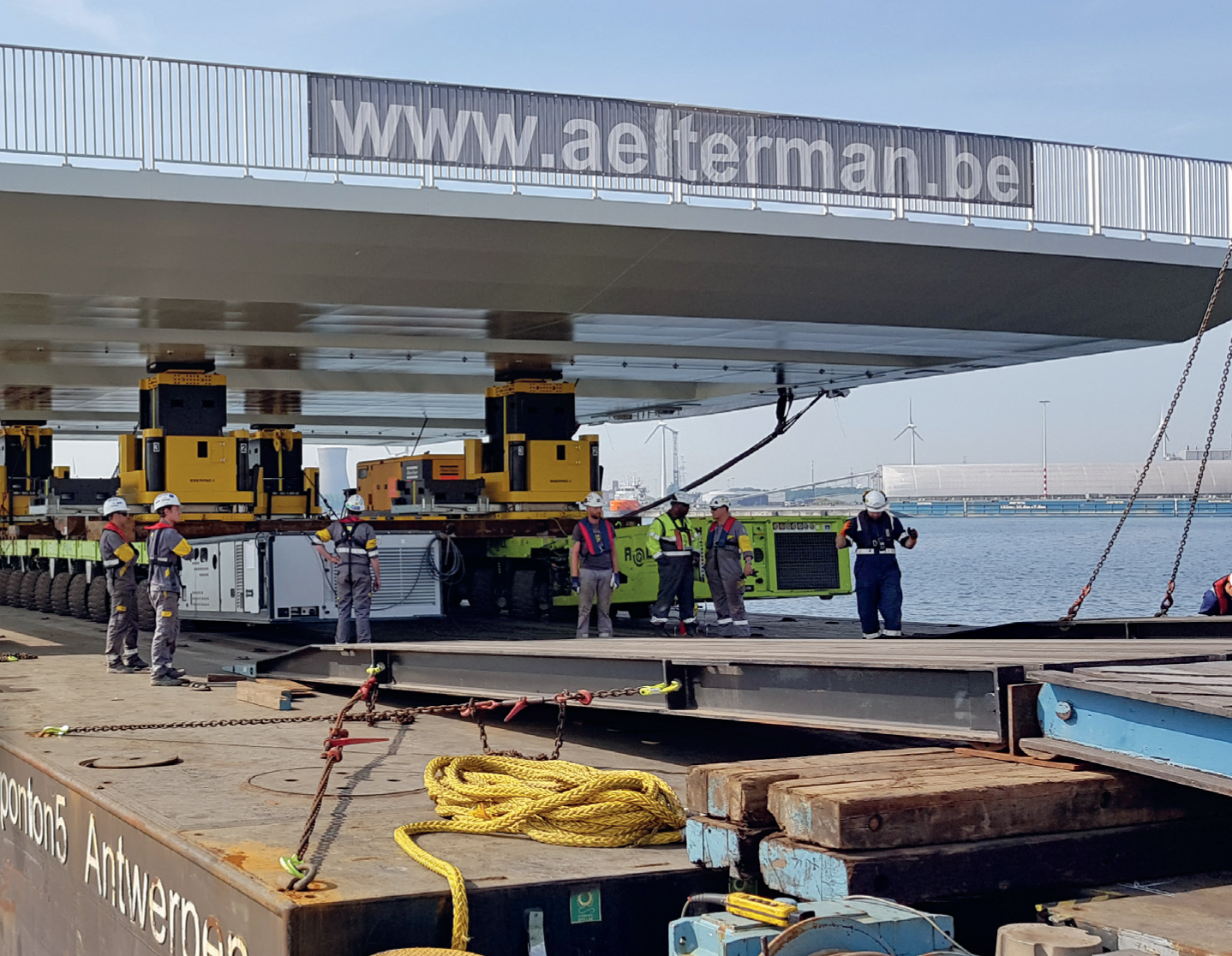
Only when the deck of the new Londenbrug Bridge is raised do travellers see the poem by Antwerp poet Stijn Vranken. It is written large on the underside of the 300tonne prefabricated steel deck.
People waiting for a ship to pass the raised bridge now contemplate the poem’s message about ships transporting goods and people to and from the four corners of the world. A large part of Antwerp’s commerce remains based on moving people and objects, including even bridge decks, long distances.
The port’s newest Londenbrug (London) Bridge – there have been two previous ones - is part of the city’s Noorderlijn transport initiative. The mobility plan includes a tram connection between Antwerp city centre, the historic port area of Het Eilandje and the north of the city. Londenbrug Bridge connects Kattendijkdok basin with the Willemdok basin, all within the Het Eilandje - translated literally as Little Island because Antwerp’s oldest port area is surrounded by water.
Commercial shipping activity is now mostly outside the historic Het Eilandje. But regeneration of the area into a more people-oriented environment requires better, and more, public transportation, including pedestrian, cycling and tram infrastructure.
The original Londenbrug Bridge was built in 1913 and supported a train track for the movement of goods. It was replaced in 1978 by a folding bridge with no tracks that was similar in design to a new pedestrian bridge recently installed in Kiel, Germany.
The 105m-long wooden plank Hörnbrücke - Hörn Bridge - is a three-segment bascule bridge that folds in the shape of the letter ‘N’. It is operated by cables that retract to pull back the three sections, 26m in total length and weighing 54tonnes, to allow ships to pass. The operation is done with two hydraulic motors, 44kW each.
However, the 1978 Londenbrug Bridge couldn’t accommodate a tram line, so a new deck was in order, a more traditional bascule structure. It is larger and wider and weighs 300 tonnes. It consists of two single vehicle lanes, two foot-and-cycle paths and the all-important tram line running in the middle. The front splints, or balance pins, of the bridge weigh 135tonnes apiece, with another 230tonnes of ballast needed to open the bridge.
Other major alterations included strengthening the original bridge foundations and moving the bridge’s fulcrum to the other side of the dock so that the bridge now opens from the opposite side to the 1978 version.
In the past, the bridge was driven by an electric motor. Today, this is done by two hydraulic jacks to ensure that the bridge opens and closes in around three minutes.
Canal transportation
Transporting the new bridge deck the 50km from Ghent to Antwerp by canal was challenging. This was less because of its weight and more because of the obstacles around or over which it had to be manoeuvred.
The new deck was manufactured by steel construction company Aelterman at its Ghent facility which has a quayside ro-ro facility. This allowed transportation company Victrol to move the deck to Antwerp by canal pontoon. Handling the bridge itself was the responsibility of Roll-iT which used Enerpac’s jack-up technology to assist in negotiating obstacles en route.
Roll-iT is jointly operated by Aertssen Kranen, of Antwerp-based Aertssen Group, and Ivens Transport & Kraanbedrijf, part of the Ivens Group. Both companies operate in the construction, transport and crane rental sectors. Roll-iT specialises in complex transportation solutions requiring the use of SPMT units - self-propelled modular transporters.
Enerpac is a division of Actuant, a US$1.5 billion global manufacturing company in Menomonee Falls in the US state of Wisconsin. Enerpac manufactures and distributes high-pressure hydraulic products, from small cylinders to computer-operated lifting and positioning systems.
“Our biggest challenge was to lift the bridge over the Kattendijkdok lock and the historic lockkeeper’s cottage that acts as the control tower for the Londenbrug Bridge,” said Tom Van Runckelen, Roll-iT project manager.
“It was impractical to use a crane for this given the level of disruption to local traffic and services it would have caused. Instead, we decided to use the Enerpac jack-up to lift the bridge over the obstacles as required. It also had the advantage that we could use the jack-up as an integral part of the complete bridge transport and installation system,” he said.
At the Aelterman steelworks, Roll-iT used two 12-axle SPMTs in conjunction with an Enerpac JS-250 jack-up system. This combination lifted the deck from the manufacturing area and moved it along to the ro-ro quay where is was put onto Victrol’s pontoon. When the bridge deck was securely fastened on the pontoon, the jack-up towers were fully lowered to improve the stability of the pontoon.
Avoiding obstacles
The Enerpac’s JS-Series jack-up system is a multi-point lifting system comprising four jack-up towers, one positioned under each corner of a load. The lifting frame of each jack-up tower contains four hydraulic cylinders, which lift and stack steel barrels.
The load is lifted in increments as barrels are automatically inserted and stacked to form the lifting towers. The JS-250 has a lifting capacity of 250tonnes per tower, giving a total lift capacity of 1,000tonnes up to a height of 10m.
The ability to raise the jack-up to 10m was important. Avoiding obstacles when entering and leaving the Kattendijkdok and the height of the Londenbrug Bridge lockkeeper's cottage meant that Roll-iT needed to raise the bridge deck at least 7.5m to ensure complete clearance.
Runckelen acknowledged that before the lifting began, they were concerned about stability of the load during pontoon transportation which, he explained, is critical.
“The pontoon’s maximum allowable tilt when the jack-up towers were raised to 7.5m was 5% at 2.9°. We arranged the positions of the jack-up towers under the bridge deck to ensure we kept within the tilt limits. We’d also factored in some movement by the jack-up system and were pleasantly surprised when the jack-up towers were extremely stable when lifting and lowering,” he said.
“But the jack-up was very stable and well within the lateral movement we’d allowed for the lift. It was also surprisingly quick. Raising and lowering the bridge deck was completed in a fraction of the time we’d expected.”
Time for transportation was a key factor. The bridge deck had to be transported within 24 hours to prevent disruption to ships docking at Kattendijkdok lock. In fact, the 50km canal voyage was completed within only seven hours.
On arriving at Londenbrug Bridge, the raised bridge deck was moved closer to the left-hand side of the lock and positioned above its final resting position. Over the next few hours, the bridge deck was progressively lowered into position.
First, 3.2m jack towers were inserted beneath the deck and the 7.5m Enerpac jack-up towers lowered to rest the deck on the shorter towers. The jack-up system was removed and in its place 2.4m pot towers were positioned to take the weight of the deck while the jack towers were lowered to 2.4m.
Finally, the jack towers took over. The pot towers were removed and the towers jacked down to 1.1m to complete the bridge deck installation.