Three years ago a welder’s cut halved Canada’s old Port Mann Bridge. David Arminas reports from the banks of the Fraser River. By the time this issue of World Highways reaches you, one of Canada’s iconic steel arch bridges will be a shadow of its former self. It’s been a three-year demolition job since the first cut across the deck of the old Port Mann Bridge just outside the city of Vancouver on Canada’s Pacific coast. A new 10-lane 2.2km Port Mann Bridge opened in 2012 (see box). It runs parallel to the o
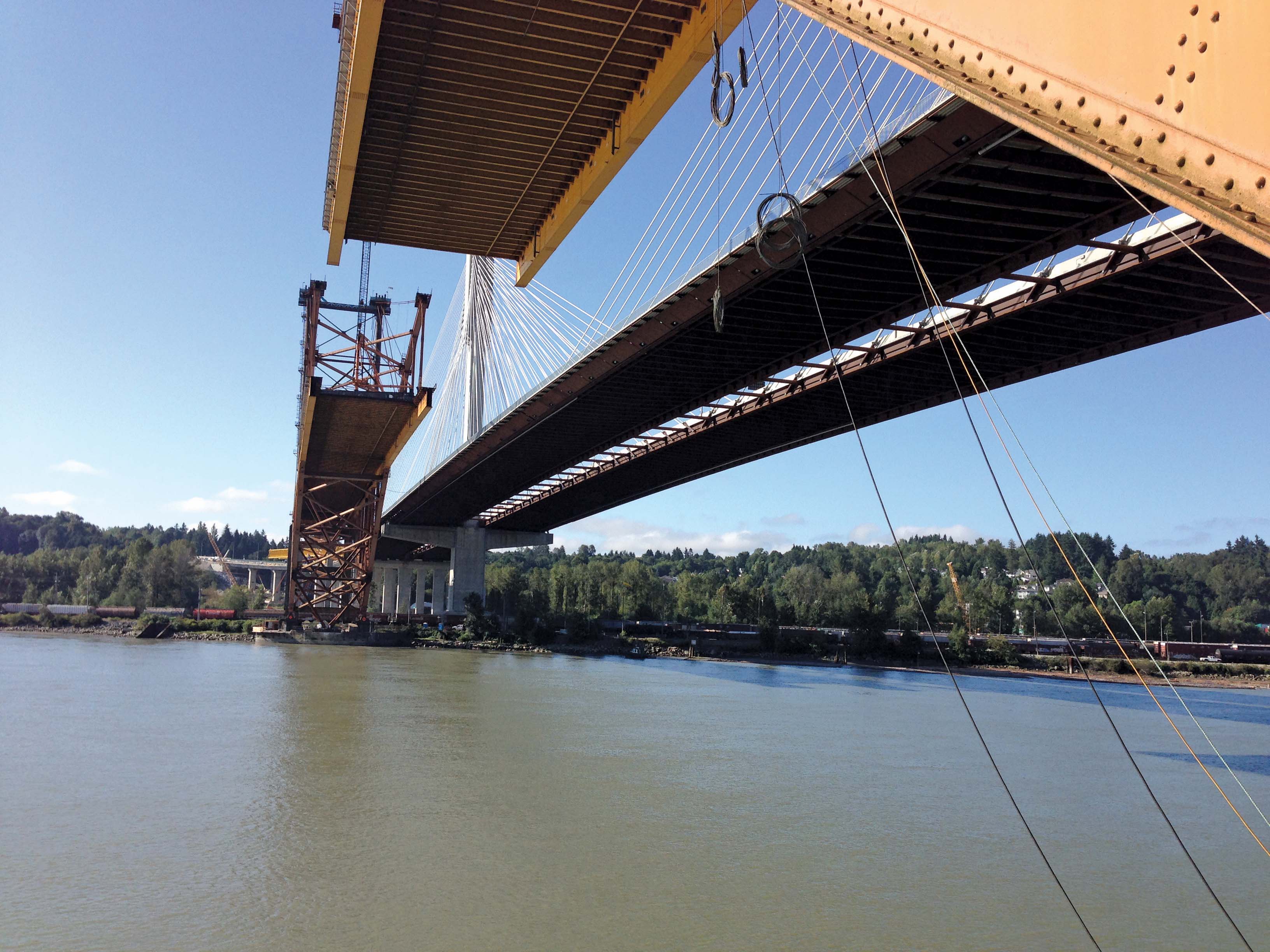
The gap widens as the two cantilevers recede from each other
Three years ago a welder’s cut halved Canada’s old Port Mann Bridge. David Arminas reports from the banks of the Fraser River
By the time this issue of World Highways reaches you, one of Canada’s iconic steel arch bridges will be a shadow of its former self. It’s been a three-year demolition job since the first cut across the deck of the old Port Mann Bridge just outside the city of Vancouver on Canada’s Pacific coast. A new 10-lane 2.2km Port Mann Bridge opened in 2012 (see box). It runs parallel to the old bridge, which is only 20m away. The crossing has been in place since 1964.
Detonation of an old bridge, the usual demolition option, is a high-risk but one-off short-duration event, meaning it is efficient. It is also the safest option because few people are on site at any time, explains David Jeakle, bridge practice lead with McElhanney Consulting Services, in Tampa, Florida. McElhanney, through its Vancouver office, was design engineer on the new bridge and responsible for taking down the old one.
Demolition practices have changed, in both engineering and environmental terms, since the old bridge structure was opened for traffic. Detonation was rejected by owners of the Port Mann Bridge because of concern over fish stocks, in particular that of the salmon, in the Fraser River. The river is also an extremely busy shipping route that must remain open at all times, explains Jeakle during a World Highways visit to his Florida office.
Environmental concerns were voiced also over possible contamination of the river’s ecosystems from asbestos and from lead-based oils and paints. Asbestos was found in trace amounts, usually between the steel road support and the asphalt road coating. Asbestos can be a problem when you blow things up - and can turn into dust,” he says. “Such environmental issues are becoming more important in decisions about building and also taking down older structures.”
Detonation also looked risky because the south approach to the bridge was elevated directly above a busy Canadian National Railways marshalling yard. The bridge’s south pier rested just on shore within the yard. For more than two years, CN Rail has been dealing with bridge workers overhead and has had to rigidly control workers’ access to the south section of the bridge because crews have needed to cross over several rail lines.
One question asked was how to remove deck sections. Options included lowering the spans onto barges and floating them away. The approach span over the rail yard would have to be lifted, rotated and lowered onto barges. “But these were impractical” says Jeakle. “And the main span was really too big to ship anywhere.”
Pretty much all the Dominion Bridge Company drawings existed and were digitised in high resolution. Minute details such as rivet types and temporary brackets could be magnified and identified. “I could identify a plate, where they cut it off and put a cover plate over it. Given the drawings and some photos from the field, I could say, right, remove that cover plate and you should find a nice slot there in which you can lower a piece of steel.
“We hit a couple surprises but usually as a result of changes to the structure after construction, such as different railings or an added piece of pipe or steel here and there. They hung some water pipes and stiffened beams underneath in places, but it was all little stuff.”
The bridge was to be cut in the centre of the middle main span, essentially creating two bridges. The two halves of the bridge would be slowly taken apart, moving backwards towards each half’s main concrete pier.
While the old bridge is in excellent shape, it is a fracture-critical structure with a tension member that runs the full length of the bridge. If that fractures anywhere, the bridge’s structural safety can be compromised heavily, explains Jeakle. “There is no built-in redundancy [in this type of bridge]. It only takes a little undetected fatigue crack to grow for 10 years and then a member eventually just snaps through one cold morning when the wrong size truck rolls over it.”
But the bridge is extremely efficient from an engineering perspective, even if it is a finely balanced structure, he says. They built bridges back then with the absolute minimum of material to reduce cost. That made them tough to design and build but a lot of labour and equipment was used because it was cheap. “Now, we’ll add more steel to minimise the effort to build it. I don’t care whether the plates are 25mm or 35mm thick, just as long as I don’t need specialised equipment to put them in place.”
One of the first concerns is the thickness of steel after half a century of weathering. Jeakle says there were some raised eyebrows when they found the bridge in very good shape, given its design and years. “There was some local corrosion here and there but nothing that we had to account for in the deconstruction. All the steel was generally the same thickness as the day it was installed. Joints and rivets tight, well-sealed up.”
A tied arch bridge works beautifully, with clean load paths. But when you make one cut in the thing and remove one piece, “it can be like a house of cards”, he says. “Most bridge designs now are fairly robust. When we make the final closure in the middle, it really doesn’t change the complete system’s dynamics much. They are inherently stable.”
Given all the issues, “this is a very highly technical and challenging deconstruction from an engineering and contractor perspective”.
Cutting the bridge in half was a hold-your-breath moment because the temporary towers had to take all the load from the original tied cable system. Unknown variables can await you, says Jeakle. “Bearings could be frozen, you don’t know how much support settlement has occurred, what locked-in stresses are there. We were transferring stresses from one system to another (support) system.”
It also required some fine tuning with special jacks around where the cut was to be made to ensure that the cut was a neutral stress point. “Once the cut is made, you release the jacks and let the bridge relax.” The cut’s gap was around 200mm and when the jacks were depressurised, the two bridge ends move towards each other by only around 50-75mm.
The relief cut created in effect two independent bridges. “When we started the day, we had a continuous tied arch bridge. When we ended the day, we had two cantilevered cable-stayed bridges extending out from their piers into the river”
After the cut, construction teams on both bridge halves slowly worked their way backwards towards the main pier until what remains of each half is even more finely balanced upon its pedestal. This is the next critical point and false-work bracings and auxiliary tie-down cables were added to aid support.
Even with the extra falsework, the contractor has had to ask if they could put a truck at a certain lift point on the deck, or a crane here and a welding machine there. “We’d look at it and have to say, not there, but back the crane up 10 feet. You’re always very cognisant of balance and need know where the contractor’s heavy equipment is sitting,” he says. “For example, use that 90tonne crane, but don’t put two out there. Or after you remove this girder, you can bring in a second crane.”
Earlier this year, workers on the North bridge section finished their job by blowing up the concrete pier that was seated in the river.
Work on the south pier continues. In April, explosives were used to send the last girders, 70m long and weighing 600tonnes apiece, to the ground by the river’s edge where they were cut up and removed for recycling.
When World Highways visited the site in June, the temporary support tower system was being lowered. A derrick crane was to be the last piece of equipment to leave the bridge deck and another crane on a river barge stood by ready to “pick the carcass clean”.
Jeakle acknowledges that the project was his first deconstruction contract and a learning experience in many ways, not least of the importance for fast, direct and timely communication between on-site workers and design engineers for deconstruction work. He believes that with environmental issues increasing in importance, detonation of structures may become less the chosen option for demolition.
By the autumn, nothing will remain of what used to be Canada’s longest arch bridge. However, the original 1964 commemorative plaque from the old bridge will be mounted beside one for the new bridge along the new bridge’s pedestrian and cycling path.
A tale of two bridges
In with the new
The new 10-lane 65m-wide Port Mann Bridge opened in 2012 with eight lanes operational. It connects the two small cities of Coquitlam and Surrey near the major Pacific port of Vancouver. Main towers are 75m above the road deck. Main span is 470m, with north and south spans at 190m. At 2.2km, it is reportedly the second longest cable-stayed bridge in North America and was the widest bridge in the world until the 2013 opening of the San Francisco-Oakland Bay Bridge in California. It has separate pedestrian and cycling lanes and can accommodate a light rail transit underneath the spans.
Out with the old
When it opened in 1964, the 2.1km steel-tied arch bridge, was the longest arch bridge in Canada and third-longest in the world. Designed by CBA Engineering, it had an orthotropic deck carrying five lanes of Trans-Canada Highway traffic. It had approach spans of three steel plate girders and concrete deck. The main span was 366m with two 110m spans on either side. Government figures showed the bridge carried around 127,000 vehicles daily, of which around 8% was truck traffic.
Port Mann/Highway 1
Work on both new and old Port Mann crossings have been part of the US$3.3 billion Port Mann/Highway 1 Improvement Project, the largest transportation infrastructure project in history of the Canadian province of British Columbia. Around $2.46 billion has been for new bridge construction.
The rest is for managing the project, overseeing the contractor, purchase of a tolling system, interest costs from the debt and the purchase of properties along the corridor for widening 37km of the TransCanada Highway.
The PMH1 project was originally intended as a public-private partnership but was changed to a design-build contract let by the provincial government’s arms-length Transportation Investment Corporation. TI Corp.is responsible for building and implementing the project, as well as collecting tolls to recoup the project’s costs.
All costs will be recovered by electronic tolls. The design-build contractor for the Port Mann/Highway 1 Improvement Project is Kiewit/Flatiron General Partnership, a joint venture between Peter Kiewit Sons Co. (6472 Kiewit Corporation) and 2758 Flatiron Constructors Canada. 4757 Sanef ITS developed the tolling system and Trans-Canada Flow Tolling is the tolling operator.
An engineer remembers
“I last saw the bridge in 1994 and I’ll be sorry to see it go,” says Gerrit Hardenberg, a civil engineer who arrived in Vancouver from the Netherlands in 1957 to start designing the old Port Mann Bridge. Hardenberg, now 89, was a 31-year-old employee of CB Engineering when he started what turned out to be a seven-year job.
“When I got to Vancouver the bridge was only a sketch and we took the next two years to design it,” he told World Highways, speaking from his home in Dordrecht, close to Rotterdam.
“We used the computer at the University of British Columbia to do some design work. The computer was as big as a large room and it took seven hours to get a print-out of your work.”
Hardenberg can understand that the bridge has to come down, given traffic demands. However, he questions whether the bridge had come to the end of its physical life and if not, he suggested it could have been twinned with a new smaller bridge. “But I suppose it is unpopular to start charging tolls on a bridge that has been free for 50 years.”
Building down to nothing
As World Highways arrived on site, what remained of the bridge appeared as a steel sentinel standing watch on the river’s edge. It looked finely balanced on its concrete pedestal. Contractors high up were dismantling the last temporary support twin tower structure.
At ground level, supporting static falsework could be seen underneath structure. The untreated false-work stood out from the yellow-painted underside of the deck. The falsework is connected in exactly the same places as when the bridge was being built, explained Chad Amiel, a McElhanney bridge engineer in Vancouver.
“When you look at the gusset underneath the bridge, you can see where a plate had been welded for falsework during construction and then cut off, and that is where we’ve welded our own plate for our falsework.”
Up on deck, nearly 40m above the water, an 80tonne Grove wheeled RT890E crane is used for general on-deck lifting and in emergencies it lowers injured workers to ground level. Bridge deck operations stop for safety reasons when winds reach 40kph, but the bridge itself can handle much higher winds. Work stoppages have occurred only about once a month.
Workers on a raised platform were cutting the last cables from the twin temporary support towers and their connecting gantry. A smaller tripping tower had begun lowering the 60m temporary towers which were sitting at a 55-degree angle to the deck. By week’s end, both columns of the temporary support structure would be resting on a saddle at the deck’s edges.
“Our support and tripping towers are in pretty much in the same position as during construction,” said Kiewit general site supervisor Tyler Vander Linde. “But instead of using strand jacks and cables as we do now, they used block and tackle, winches and pullies.”
The temporary towers have been operated by two jacks at deck level, each with a lift capacity of nearly 410,000kg. Ten more jacks sit atop the towers and gantry. The combination allows full control of the temporary support towers to balance what remains of the deck and structure as sections are taken away. A tall barge-mounted crane will soon move in to carry off the dismantled support towers, take away the contractor’s equipment and then “nibble away” at the last bit of deck. By November, the crane will have consumed everything down to the concrete pier. The northern pier stood in the water and was blasted to nothing. But the southern pier is incorporated into a larger bankside concrete retaining structure and will remain intact.
Across the deck, only 20m away, is the new bridge where Vander Linde was responsible for steelwork. Deconstruction of the old bridge is a totally different challenge, he says.
For the new bridge, you can plan-in your site access and temporary works. For the old bridge, you have to do a lot of investigation to make sure everything fits exactly as before. “When you are building a bridge, you have your own QC (quality control manager). Now we are relying on 50-year-old drawings and the bridge being built right those years ago. But there’s been no real surprise,” he says.
“The bridge is actually in great shape, but it just doesn’t have the required car capacity or seismic standard,” says Vander Linde.
He is used to creating bridges, not deconstructing them. As a bridge takes shape, so does an intimacy between worker and creation. With the Port Mann deconstruction, workers are walking in the footsteps of colleagues taken half a century before. In effect, today’s workers are building something that is actually getting smaller.
“You’re closing in on yourself,” he says. By the end of the year, all the will remain will be the sound of the water sliding along the river’s edge.
By the time this issue of World Highways reaches you, one of Canada’s iconic steel arch bridges will be a shadow of its former self. It’s been a three-year demolition job since the first cut across the deck of the old Port Mann Bridge just outside the city of Vancouver on Canada’s Pacific coast. A new 10-lane 2.2km Port Mann Bridge opened in 2012 (see box). It runs parallel to the old bridge, which is only 20m away. The crossing has been in place since 1964.
Detonation of an old bridge, the usual demolition option, is a high-risk but one-off short-duration event, meaning it is efficient. It is also the safest option because few people are on site at any time, explains David Jeakle, bridge practice lead with McElhanney Consulting Services, in Tampa, Florida. McElhanney, through its Vancouver office, was design engineer on the new bridge and responsible for taking down the old one.
Demolition practices have changed, in both engineering and environmental terms, since the old bridge structure was opened for traffic. Detonation was rejected by owners of the Port Mann Bridge because of concern over fish stocks, in particular that of the salmon, in the Fraser River. The river is also an extremely busy shipping route that must remain open at all times, explains Jeakle during a World Highways visit to his Florida office.
Environmental concerns were voiced also over possible contamination of the river’s ecosystems from asbestos and from lead-based oils and paints. Asbestos was found in trace amounts, usually between the steel road support and the asphalt road coating. Asbestos can be a problem when you blow things up - and can turn into dust,” he says. “Such environmental issues are becoming more important in decisions about building and also taking down older structures.”
Detonation also looked risky because the south approach to the bridge was elevated directly above a busy Canadian National Railways marshalling yard. The bridge’s south pier rested just on shore within the yard. For more than two years, CN Rail has been dealing with bridge workers overhead and has had to rigidly control workers’ access to the south section of the bridge because crews have needed to cross over several rail lines.
One question asked was how to remove deck sections. Options included lowering the spans onto barges and floating them away. The approach span over the rail yard would have to be lifted, rotated and lowered onto barges. “But these were impractical” says Jeakle. “And the main span was really too big to ship anywhere.”
Reverse construction
The answer was to take it all down in the reverse order. The bridge was taken apart in the mirror image of its build. “We went through all the original construction plans and photos, studied their construction sequence drawings, shop drawings, and we looked at the bridge’s temporary members during construction, focusing on connections here and there. We knew the bridge could deal with this because it has gone through it once during construction.”Pretty much all the Dominion Bridge Company drawings existed and were digitised in high resolution. Minute details such as rivet types and temporary brackets could be magnified and identified. “I could identify a plate, where they cut it off and put a cover plate over it. Given the drawings and some photos from the field, I could say, right, remove that cover plate and you should find a nice slot there in which you can lower a piece of steel.
“We hit a couple surprises but usually as a result of changes to the structure after construction, such as different railings or an added piece of pipe or steel here and there. They hung some water pipes and stiffened beams underneath in places, but it was all little stuff.”
The bridge was to be cut in the centre of the middle main span, essentially creating two bridges. The two halves of the bridge would be slowly taken apart, moving backwards towards each half’s main concrete pier.
While the old bridge is in excellent shape, it is a fracture-critical structure with a tension member that runs the full length of the bridge. If that fractures anywhere, the bridge’s structural safety can be compromised heavily, explains Jeakle. “There is no built-in redundancy [in this type of bridge]. It only takes a little undetected fatigue crack to grow for 10 years and then a member eventually just snaps through one cold morning when the wrong size truck rolls over it.”
But the bridge is extremely efficient from an engineering perspective, even if it is a finely balanced structure, he says. They built bridges back then with the absolute minimum of material to reduce cost. That made them tough to design and build but a lot of labour and equipment was used because it was cheap. “Now, we’ll add more steel to minimise the effort to build it. I don’t care whether the plates are 25mm or 35mm thick, just as long as I don’t need specialised equipment to put them in place.”
One of the first concerns is the thickness of steel after half a century of weathering. Jeakle says there were some raised eyebrows when they found the bridge in very good shape, given its design and years. “There was some local corrosion here and there but nothing that we had to account for in the deconstruction. All the steel was generally the same thickness as the day it was installed. Joints and rivets tight, well-sealed up.”
A tied arch bridge works beautifully, with clean load paths. But when you make one cut in the thing and remove one piece, “it can be like a house of cards”, he says. “Most bridge designs now are fairly robust. When we make the final closure in the middle, it really doesn’t change the complete system’s dynamics much. They are inherently stable.”
Given all the issues, “this is a very highly technical and challenging deconstruction from an engineering and contractor perspective”.
Hold your breath
Before the bridge was cut in half, each half had to have its own temporary cable tower support system to take the transferred load. The towers were constructed flat on the bridge deck and rotated up into the vertical position using a tripping tower (see site visit box).Cutting the bridge in half was a hold-your-breath moment because the temporary towers had to take all the load from the original tied cable system. Unknown variables can await you, says Jeakle. “Bearings could be frozen, you don’t know how much support settlement has occurred, what locked-in stresses are there. We were transferring stresses from one system to another (support) system.”
It also required some fine tuning with special jacks around where the cut was to be made to ensure that the cut was a neutral stress point. “Once the cut is made, you release the jacks and let the bridge relax.” The cut’s gap was around 200mm and when the jacks were depressurised, the two bridge ends move towards each other by only around 50-75mm.
The relief cut created in effect two independent bridges. “When we started the day, we had a continuous tied arch bridge. When we ended the day, we had two cantilevered cable-stayed bridges extending out from their piers into the river”
Going, going, almost gone
Preparation work included stripping off the asphalt by men in haz-mat protection suits because of asbestos, which also meant the asphalt couldn’t be recycled. Steel was stripped off the bridge, lowered onto barges and sent up river to a recycling depot for quality assessment and then shipped out for formal recycling.After the cut, construction teams on both bridge halves slowly worked their way backwards towards the main pier until what remains of each half is even more finely balanced upon its pedestal. This is the next critical point and false-work bracings and auxiliary tie-down cables were added to aid support.
Even with the extra falsework, the contractor has had to ask if they could put a truck at a certain lift point on the deck, or a crane here and a welding machine there. “We’d look at it and have to say, not there, but back the crane up 10 feet. You’re always very cognisant of balance and need know where the contractor’s heavy equipment is sitting,” he says. “For example, use that 90tonne crane, but don’t put two out there. Or after you remove this girder, you can bring in a second crane.”
Earlier this year, workers on the North bridge section finished their job by blowing up the concrete pier that was seated in the river.
Work on the south pier continues. In April, explosives were used to send the last girders, 70m long and weighing 600tonnes apiece, to the ground by the river’s edge where they were cut up and removed for recycling.
When World Highways visited the site in June, the temporary support tower system was being lowered. A derrick crane was to be the last piece of equipment to leave the bridge deck and another crane on a river barge stood by ready to “pick the carcass clean”.
Jeakle acknowledges that the project was his first deconstruction contract and a learning experience in many ways, not least of the importance for fast, direct and timely communication between on-site workers and design engineers for deconstruction work. He believes that with environmental issues increasing in importance, detonation of structures may become less the chosen option for demolition.
By the autumn, nothing will remain of what used to be Canada’s longest arch bridge. However, the original 1964 commemorative plaque from the old bridge will be mounted beside one for the new bridge along the new bridge’s pedestrian and cycling path.
A tale of two bridges
In with the new
The new 10-lane 65m-wide Port Mann Bridge opened in 2012 with eight lanes operational. It connects the two small cities of Coquitlam and Surrey near the major Pacific port of Vancouver. Main towers are 75m above the road deck. Main span is 470m, with north and south spans at 190m. At 2.2km, it is reportedly the second longest cable-stayed bridge in North America and was the widest bridge in the world until the 2013 opening of the San Francisco-Oakland Bay Bridge in California. It has separate pedestrian and cycling lanes and can accommodate a light rail transit underneath the spans.
Out with the old
When it opened in 1964, the 2.1km steel-tied arch bridge, was the longest arch bridge in Canada and third-longest in the world. Designed by CBA Engineering, it had an orthotropic deck carrying five lanes of Trans-Canada Highway traffic. It had approach spans of three steel plate girders and concrete deck. The main span was 366m with two 110m spans on either side. Government figures showed the bridge carried around 127,000 vehicles daily, of which around 8% was truck traffic.
Port Mann/Highway 1
Work on both new and old Port Mann crossings have been part of the US$3.3 billion Port Mann/Highway 1 Improvement Project, the largest transportation infrastructure project in history of the Canadian province of British Columbia. Around $2.46 billion has been for new bridge construction.
The rest is for managing the project, overseeing the contractor, purchase of a tolling system, interest costs from the debt and the purchase of properties along the corridor for widening 37km of the TransCanada Highway.
The PMH1 project was originally intended as a public-private partnership but was changed to a design-build contract let by the provincial government’s arms-length Transportation Investment Corporation. TI Corp.is responsible for building and implementing the project, as well as collecting tolls to recoup the project’s costs.
All costs will be recovered by electronic tolls. The design-build contractor for the Port Mann/Highway 1 Improvement Project is Kiewit/Flatiron General Partnership, a joint venture between Peter Kiewit Sons Co. (
An engineer remembers
“I last saw the bridge in 1994 and I’ll be sorry to see it go,” says Gerrit Hardenberg, a civil engineer who arrived in Vancouver from the Netherlands in 1957 to start designing the old Port Mann Bridge. Hardenberg, now 89, was a 31-year-old employee of CB Engineering when he started what turned out to be a seven-year job.
“When I got to Vancouver the bridge was only a sketch and we took the next two years to design it,” he told World Highways, speaking from his home in Dordrecht, close to Rotterdam.
“We used the computer at the University of British Columbia to do some design work. The computer was as big as a large room and it took seven hours to get a print-out of your work.”
Hardenberg can understand that the bridge has to come down, given traffic demands. However, he questions whether the bridge had come to the end of its physical life and if not, he suggested it could have been twinned with a new smaller bridge. “But I suppose it is unpopular to start charging tolls on a bridge that has been free for 50 years.”
Building down to nothing
As World Highways arrived on site, what remained of the bridge appeared as a steel sentinel standing watch on the river’s edge. It looked finely balanced on its concrete pedestal. Contractors high up were dismantling the last temporary support twin tower structure.
At ground level, supporting static falsework could be seen underneath structure. The untreated false-work stood out from the yellow-painted underside of the deck. The falsework is connected in exactly the same places as when the bridge was being built, explained Chad Amiel, a McElhanney bridge engineer in Vancouver.
“When you look at the gusset underneath the bridge, you can see where a plate had been welded for falsework during construction and then cut off, and that is where we’ve welded our own plate for our falsework.”
Up on deck, nearly 40m above the water, an 80tonne Grove wheeled RT890E crane is used for general on-deck lifting and in emergencies it lowers injured workers to ground level. Bridge deck operations stop for safety reasons when winds reach 40kph, but the bridge itself can handle much higher winds. Work stoppages have occurred only about once a month.
Workers on a raised platform were cutting the last cables from the twin temporary support towers and their connecting gantry. A smaller tripping tower had begun lowering the 60m temporary towers which were sitting at a 55-degree angle to the deck. By week’s end, both columns of the temporary support structure would be resting on a saddle at the deck’s edges.
“Our support and tripping towers are in pretty much in the same position as during construction,” said Kiewit general site supervisor Tyler Vander Linde. “But instead of using strand jacks and cables as we do now, they used block and tackle, winches and pullies.”
The temporary towers have been operated by two jacks at deck level, each with a lift capacity of nearly 410,000kg. Ten more jacks sit atop the towers and gantry. The combination allows full control of the temporary support towers to balance what remains of the deck and structure as sections are taken away. A tall barge-mounted crane will soon move in to carry off the dismantled support towers, take away the contractor’s equipment and then “nibble away” at the last bit of deck. By November, the crane will have consumed everything down to the concrete pier. The northern pier stood in the water and was blasted to nothing. But the southern pier is incorporated into a larger bankside concrete retaining structure and will remain intact.
Across the deck, only 20m away, is the new bridge where Vander Linde was responsible for steelwork. Deconstruction of the old bridge is a totally different challenge, he says.
For the new bridge, you can plan-in your site access and temporary works. For the old bridge, you have to do a lot of investigation to make sure everything fits exactly as before. “When you are building a bridge, you have your own QC (quality control manager). Now we are relying on 50-year-old drawings and the bridge being built right those years ago. But there’s been no real surprise,” he says.
“The bridge is actually in great shape, but it just doesn’t have the required car capacity or seismic standard,” says Vander Linde.
He is used to creating bridges, not deconstructing them. As a bridge takes shape, so does an intimacy between worker and creation. With the Port Mann deconstruction, workers are walking in the footsteps of colleagues taken half a century before. In effect, today’s workers are building something that is actually getting smaller.
“You’re closing in on yourself,” he says. By the end of the year, all the will remain will be the sound of the water sliding along the river’s edge.