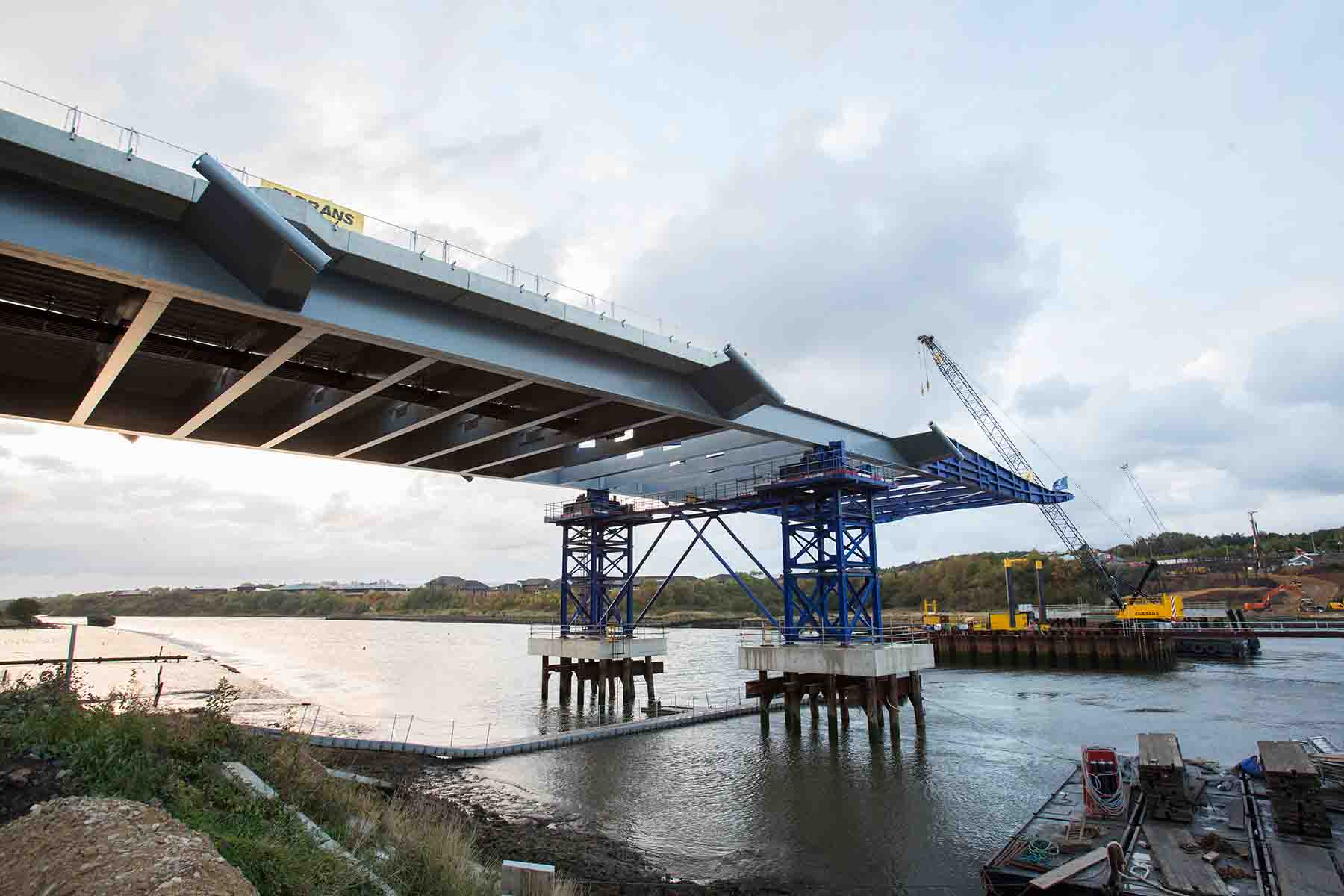
Raising the bridge’s 100m-tall pylon promised to be a stunning visual sight, but also a tricky operation dictated by extremely variable local weather. World Highways went to press just before the operation, but not before the pylon had arrived by barge on January 7.
It had completed a two-day crossing of the often unpredictable North Sea from the Belgian port of Ghent where it was fabricated.
Once in place, the 1,550tonne steel pylon will form the backbone of the New Wear Crossing – no of_ cial name yet – across the River Wear in the heart of Sunderland in north-east England.
The two-span cable-stayed bridge will be 105m high and supported by a single double pylon. It will have four vehicle lanes, as well as dedicated cycle and pedestrian routes. The structure is part of a strategic transport plan to link the port of Sunderland and Sunderland city centre with the A19 main road. The 336m steel and concrete bridge will be part of 2.8km of new road layout connecting the city’s Castletown area on the north shore of the River Wear with Pallion on the south shore. Width will be 25m and the longest span 240m. Completion is set for the spring 2018.
Work started on the bridge in May 2015. However, it was three years before construction started that the Ministry of Transport had approved a new bridge across the Wear. Four _ rms -
Work started in April 2016 on a huge cofferdam in the middle of the river to allow work on the main pylon’s foundations. Once the space was secured from the river, construction began on two tusk-like structures that form the base for each of the two legs of the 105m pylon. Giant steel formwork moulds were _ xed to the cofferdam’s _ oor and into which the tusks were fabricated.
Engineers fashioned 75tonnes of reinforcing steel into each of the moulds and then poured into the moulds upwards of 300m³ of concrete - about 37 truckloads from
Formwork was later removed to reveal the two tusks, each more than 8m tall protruding well over the top of the cofferdam’s wall, says Stephen McCaffrey, project director of the FVB joint venture.
Meanwhile, on the south embankment, workers are assembling the second of the bridge’s two deck sections. Teams are working within welding tents along the length of the second deck to fix huge steel sections together. Once the second deck is complete this spring, it will be launched – slid - out across the river, right behind the first section.
Last October, it took seven hours for hydraulic jacks to ease the 2,500tonne first deck section out from land where it was constructed. It now sits with around 120m of its 230m-long steel structure jutting out across the water. The deck is being balanced in place over the water with a series of temporary supports constructed within the riverbed. Moving the first section forward is allowing assembly of the second section. Once the 105m high A-frame pylon is raised into position, the extended bridge decks will then be pulled into position across the width of the river.
The permanent deck is 186m long and the temporary ‘nose’ - used to allow the deck to land on the temporary supports - is 37m long. The temporary ‘tail’ that connects the jacking system to the deck is 7m long.
The first deck section’s frame consists of 38 cross-beams, measuring 20m long by 2m deep. Each of the first section’s main girder sections - running along the length of the deck – measure 15m by 1.8. All the steel, along with hundreds of smaller steel components, was delivered locally from Sunderland. Of the first deck section’s 2,500tonnes, around 1,350tonnes consists of 212 precast concrete units that form the road bed. Another 256 concrete units - weighing 1,600tonnes - will be added to the bridge deck before the next launch across the River Wear. The remaining 172 concrete panels will then be installed after the bridge deck is in its final position.
So far, says Stephen McCaffrey, work is on schedule. Around 25 people are expected to be directly involved in the 24-hour operation to lift the pylon into place, he said. Positioning of the pylon will be “very complex” and “not straightforward”.
A bridge too far
The original award-winning bridge was to have two curving and intersecting steel towers – 187m and 140m tall – making the structure the tallest bridge in the UK. The deck surface of the 3.2km-long bridge would have been between 16-20m above the water.
The design was a collaboration between Spence Associates and structural engineers
The unusual design beat off 35 participants to win first prize in the New River Wear Crossing Competition, sponsored by the prestigious Royal British Institute of Architects (RIBA), in 2005. In consultations with the public, people preferred local architect Stephen Spence’s design ahead of a less expensive and architecturally straightforward beam bridge.
In July 2008, the UK government, through the
Local media reported that the city’s council leaders were concerned that the neither of the two contractors bidding for the project – Northern Ireland-based Graham and Vinci of France – had submitted a tender within the €138 million budget. The price tag inched upwards towards €155 million. Spence’s award-winning design was scrapped in favour of a less complicated cable-stayed bridge that could be built within budget.
As noted by Wells in his university lecture, the overall weight of the original competition for a new bridge was 8,000tonnes. The later design weighed in at only about 5,000tonnes, thanks to reinforcement methods. Also, its low level to the water meant that it could be launched from the river bank. Sunderland City Council will hold a consultation to eventually find a name for the new bridge.
Easy does it
Victor Buyck Steel Construction, working with Farrans Construction, spent a year fabricating the pylon at its canal-side yard in Ghent. Apart from the 1,550tonnes tonnes of steel, around 550tonnes of concrete went into making the pylon that, because of its size, had to be constructed in the open air.
Also because of its size, Sarens, a global heavy lifting and engineering transport specialist, was called in to gingerly shift the completed pylon onto two canal barges for transport along the canal to the sea port.
“The sheer size and weight of the pylon meant that it was never going to be an easy task,” says Jim Kilcar, bridge supervisor for Atkins, which is supervising the New Wear Crossing project for Sunderland City Council.
“The pylon was inched out over two days while ballast was adjusted on the two barges to keep everything balanced. It was a very measured and steady operation, but it’s only when you’re up close to it that you can really appreciate just how big it is.”
During the load-out operation, the pylon was supported on a series of computerised wheeled units, which gradually rolled the enormous structure onto the barges over the two days. Once the pylon was in place, the barges were then rotated into position on the canal and the pylon was lowered to enable it to travel under several relatively low bridges on its three-hour journey to the port of Ghent.
The pylon was in Ghent for several weeks being prepared for its journey across the North Sea to England’s northern coastal port of Sunderland. Sarens transferred the pylon onto one, larger seagoing barge – “Louis”. At 100m long, 33m wide and with a deck area of 3,000m², Louis can handle up to 15,000tonnes of cargo. The pylon was fastened down in preparation for its sea voyage, explains Patrick Van Severen, project director for Victor Buyck.
When the pylon arrived about 1.5km off the coast at Sunderland, it was met by harbour tug boats which brought it into port. On a specific high tide, it was next carefully towed about 4.5km upriver to the site of the cofferdam, between Pallion and Castletown.
Arrival at last
Arrival of the huge white A-frame pylon at the project’s river crossing point was “a milestone”, said Stephen McCaffrey, project manager for the FVB joint venture, formed by Farrans Construction and Victor Buyck Steel Construction to build the bridge.
Farrans Construction is a building and civil engineering contractor across the UK and Ireland. Victor Buyck is based in Belgium and specialises in major structural steelwork, especially steel bridges. The FVB joint venture is supported by a design team led by Buro Happold Engineering and Roughan & O'Donovan.
UK-based Lanes Group was contracted to carry out specialist drainage on the riverbanks. Work includes desilting drainage pipes and carrying out CCTV drainage surveys. Lanes Group is also providing specialist drainage support for another major UK bridge project, the Mersey Gateway Project, now under construction, to span the River Mersey between Runcorn and Widnes on England’s north-west coast.