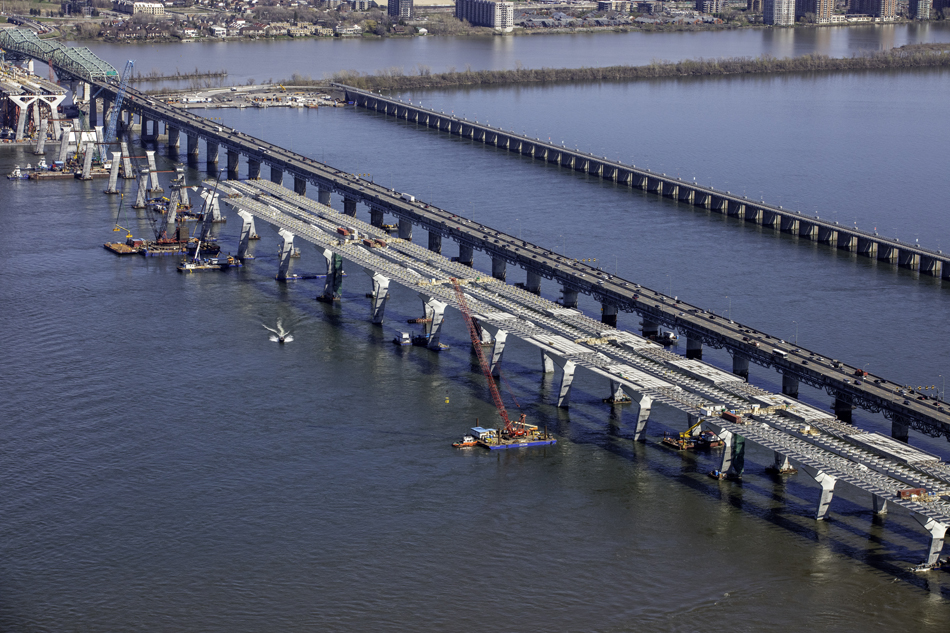
The importance of the new Champlain Bridge to Montreal and Canada can’t be overstated, given the crumbling nature of the not-so-old original Champlain Bridge. The original steel truss affair across the St Lawrence River and the adjacent St Lawrence Seaway canal is “a lifeline for residents and businesses” in greater Montréal, according to the national Auditor General - the public sector spending watchdog. “It accommodates close to 50 million of the 200 million river crossings in the area each year. It also facilitates the movement of imports and exports, with an estimated value of US$15.2 billion every year.”
No doubt the new bridge will be an eye-pleasing piece of cable-stayed engineering. But it also comes with an eye-watering price tag - around $3.24 billion. Procurement and transportation issues, a fast-approaching opening deadline and the cost have made the bridge a focus for critics, politicians and the media.
Signature on the St Lawrence (SSL) is the private consortium for the public-private project and led by Canada-based SNC-Lavalin Group (see Who’s Who box). The new and old bridges are named after the French explorer Samuel de Champlain who founded Quebec City, the Quebec province’s capital, in 1608.
The new bridge will have six vehicle lanes and a separate cycle and pedestrian lane. Design life is 125 years and operation is under a 30-year contract after completion of construction. Work includes construction of a smaller bridge for Île des Soeurs - Nun’s Island - and widening Autoroute 15 through the centre of Montreal.
At the heart of criticism lies a report published in May by the Auditor General which declares that the new bridge is unlikely to be completed by December. To be fair, the Auditor General’s report acknowledged that its analysis was narrowly focussed. It considered only how Infrastructure Canada, the main federal agency in charge
of national infrastructure, “managed selected aspects” of the new bridge to deliver “a durable bridge on time and in a cost-effective manner”.
Importantly, the report continues: “We did not examine the quality of the construction of the new Champlain Bridge; the management of environmental issues; land acquisitions; contractual agreements other than the one with the selected private partner; the planning for demolition of the existing bridge; or the operation, maintenance and rehabilitation plan for the new bridge.”
The report concluded that “Infrastructure Canada did not plan the replacement of the existing Champlain Bridge in a cost-effective manner”. Infrastructure Canada also “did not adequately manage selected procurement risks to mitigate cost overruns and delays”.
Acrimony to agreement
The private partner faced unforeseen events, such as a labour dispute and strikes by construction workers and engineers of the Quebec public service. Other challenges included around 2,500 defects discovered in some prefabricated parts and within the road sections, although these were eventually put right, according to media reports. It didn’t help that additional costs were incurred by contractors because of transportation restrictions of heavily loaded trucks on the Quebec road network and over the old Champlain Bridge.
In March 2017, the private partner sued the government for around $94 million over various issues, noted the Auditor General’s report. By late summer 2017, the private partner reported to the client Department that the project was about eight months behind schedule. But it was still possible to meet the completion deadline through acceleration measures, it stated.
A breakthrough came in March this year when client and private partner reached a settlement, which included an extension to 21 December 2018 for completing bridge construction.
The deal called for a payment to the private partner of around $48 million relating to transportation issues. Another $130 million was paid for “additional acceleration measures, including the recovery of construction delays. Without these additional measures, the existing Champlain Bridge would have required further investments in major repairs to prolong its service life”, the Auditor General said.
Even with the totally focussed cooperation between public and private sectors, the Auditor General remained sceptical that the revised completion date of 21 December would be met. With respect to the bridge’s durability, the department had no assurance from contractors that the new bridge would meet the expected service life of 125 years at the time it signed the contract with the private partner.
Yet the report appears, in its final statement, to back pedal on what it believed was a lack of assurance over service life. “However, from our examination of certain components, we found no evidence that the bridge would not last the expected service life,” is the final word. Faint praise, but praise nonetheless.
Who’s who
Signature on the Saint Lawrence - SSL: the consortium appointed to build the new Champlain Bridge and operate it for 30 years under a public-private contract. It includes SNC-Lavalin (50% shareholder), ACS Infrastructure, Dragados Canada, Flatiron Constructors Canada and EBC. TY Lin International is lead designer. Arup Canada, in collaboration with Danish firm Dissing+Weitling and Montreal firm Provencher Roy, developed the shape and geometry for the new bridge. Overseeing independent engineer is a partnership between the Danish group Ramboll and Canadian engineering firm Stantec. Work includes examining design documents, supervision plans and the management and quality control system.
Will it, won’t it
Yes, it will open on schedule, according to federal and provincial government ministers. They have been lining up to say that the bridge, after more than 40 months of construction, will be ready for Christmas. The consortium, too, has assured Montreal that it is working round the clock to meet the deadline. “What I can tell you… is that the objective remains to deliver the bridge in December 2018,” said Annie-Claire Fournier, a spokesperson for the consortium Signature on the Saint Lawrence.
Failure to open the bridge to vehicular traffic on time means the consortium faces stiff fines, according to media reports: around $77,500 a day for the first seven days followed by $310,000 per day.
This June meant the end of manufacture of the bridge’s 600 box girders for the east and west approaches. It was a two-year job for CANAM, based in Quebec, and its partners - the largest subcontract under the project.
June also marked the end of two years of fabrication of the W-shaped pier caps, using up more than 30,000tonnes of steel. In total, 37 pier caps were fabricated by three Spanish companies: Megusa, Tecade and Dizmar. Each caps weigh around 400tonnes, measuring 11m X 3m. They sit upon transition segments that themselves sit atop the piers.
Pier footings were either prefabricated or poured in situ. The prefabricated ones were positioned with the help of global heavy-lifting specialist
Each footing is 9m X 9m X 2m and comes with a pier starter, giving the overall assembly a height of up to 14m. The weight of a single footing ranges between 600-1,000 tonnes.
Since there were no Canadian vessels that could provide the complex services required for the project, Sarens offered to design and build what it called the Floating Foundation Installer - FFI.
Hard times
Construction of the existing steel truss cantilever bridge, as well as accompanying approaches and the Bonaventure Expressway, started in 1957 and finished in 1962.
Of the old 14.5km-long complex, the bridge is 7.4km with the longest span at 215m. But increasing traffic, along with damage from road salt as well as other factors meant a new bridge was needed – and much sooner than the mid-2020s, as originally thought by the government.
A poor drainage system and a little understanding in the 1960s about how to use de-icing salts have slowly corroded the bridges edge girders. One of the last major upgrades was a three-year $286 million programme that ended in 2017 to upgrade the bridge’s 100 edge girders. Due to the design of the bridge, the girders couldn’t be replaced but instead had to be externally supported. They were reinforced with 94 modular trusses and six shoring systems developed for low-clearance areas.
According to Jacques Cartier and Champlain Bridges, the contractors designed the first modular truss, manufactured in Quebec, and installed it in June 2014 to replace the super beam. Workers first had to dismantle the 75tonne beam and lower it onto a barge for disposal. The beam itself had been in place only since the year before as an emergency stop-gap.
Each 50m-long modular steel truss is 4.7m high and weighs 56,000kg. They rest on the bridge piers and support the full load of the edge girders, compensating for further deterioration of the edge girders.
On a good footing
The FFI transported the 38 footing and initial pier section combinations from the jetty to their final location at the bottom of the Saint Lawrence River. The system consists of a self-propelled catamaran that lifts, transports and installs foundations by its own means. It is outfitted to operate in strong currents and to lift and transport parts that weigh up to 1,000 tonnes. A turntable allows for a 360-degree rotation of the parts being transported.
The FFI consists of two Sarens Modular Barges equipped with eight thrusters, 16 winches, four spuds, two Sarens Multi Lifting Towers with gantry beams and rotation bogies and eight 450T Strand Jacks. The design is a combination of structural maritime engineering with hydraulic and electronic steering systems.
The basic principle of the Multi Lifting Tower (SMLT) is a free standing tower (without guy wires or bracings) or multiple towers with lifting beams on top. The SMLT is often used in combination with strand jacks. The towers are designed to withstand both vertical and horizontal loads. Because the SMLT system is modular, it provides a tailor-made solution for each heavy-lifting problem. Tower sections can be transported on standard trucks and Sarens owns tower sections equivalent to 600m. A standard 100m-high SMLT has a 6,000tonne capacity. All work is executed to the highest ISO/OHSAS standards.
The FFI was moored to the L'Île-des-Soeurs jetty, where it had to transport and place the 38 prefabricated footings to the river bed. The footings were first moved to the end of the jetty onto the loading dock, using Thor the Ant, a super-transporter. The low-level multiwheeled Thor weighs 240tonnes and measures 16m x 8.4m x 2.4m.
The footing assembly was then tied on the FFI with steel cables. Once the assembly was secured, the FFI headed off to the designated location in the river. Fast-flowing water meant that extreme precision was required to stabilise the FFI in the correct position that would offset the power of the water pushing against the FFI and the footing as it was lowered. The FFI was stabilised in its final installation position using a powerful anchoring system of eight anchor winches.
Auld lang syne for old Champlain
Tearing down the old steel truss cantilever Champlain Bridge could be expensive, around $300 million. In the past several years it has cost upwards of $93 million annually to maintain. Different systems are proposed for removing concrete structures, the steel truss assembly and the piers.
First, machinery on the ground will break up and cart away deck sections of approach spans over land.
Next, spans over the water will be deconstructed using a mobile launcher that slides along the spans up to the steel truss section. The launcher will lift a huge cut section of the deck and slide it along to drop it onto a special wheeled transporter that will take it along the bridge, over the truss section and onto the opposite shore for breaking up.
The launcher would also remove the section’s steel girders and modular trusses in this fashion before it would slide onwards to the next deck section. The process would be repeated until reaching the steel truss span rises above the St Lawrence Canal, parallel to the river and which is used by ships, including many ocean- going vessels.
Meanwhile, machinery including cranes on barges that surround the piers would cut up the concrete and load them onto barges for removal. The remaining pier bases, underwater, would have holes drilled into them for explosives. A special “bubble curtain” would surround the area to keep fish away during blasting. Cranes on barges would then reach down to remove the pier base debris.
For the steel span section, first the steel deck would be removed along the entire length of the span, from one pier to the other, leaving the truss frame. The main section of the span would be supported on hydraulics so that when it is cut away, it can be lowered as a complete unit onto a barge for transporting to the shore for cutting up.
The remaining steel sections on each side of the main steel truss span would be deconstructed using the reverse erection cantilever method. Also, the two spans from the truss section to the approach road section would be cut into sections and lowered onto barges.
Finally, the second of the two approach roads would be dismantled using the launcher system.
The old bridge contains 253,000tonnes of concrete, 17,000tonnes of steel and 12,000tonnes of asphalt, according to the agency. The prefeasibility study recommends reusing as much as possible of the material for maintenance of existing structures. However, only around 15% of it can be reused. The rest will be sent off site to provincial Quebec recyclers which will have the capacity to accept all the material.
The part was eventually lowered into place with a hydraulic cable and pulley system as well as hydraulic jacks. Final positioning checks were made with GPS and precision prisms, located on each footing.
The FFI then returned to the dock and repeated the operation with the next footing. Sven Janssens, operations manager for
Sarens, says the job was “a daunting technological and operational feat” that went off flawlessly. “It is by far the most challenging project where I had the opportunity to be a part of at Sarens."
Among the many
For example, on the east approach road, the MLC650 was lifting 200tonne steel girders. Dual MLC650 lifted 80tonne precast concrete segments to construct the cable stayed bridge pylon, followed by a tandem lift to erect the 400 tonne lower cross-beam. Next, the MLC650s were used construct temporary support towers, and to erect 200tonne pier caps and additional girders.
It may be beautiful late summer weather in Montreal, but contractors – and commuters – know that there remains only a limited number of shopping days until Christmas. Everyone is working flat out to make sure that there is a ribbon to cut on what will be Montreal’s long-awaited Christmas present.