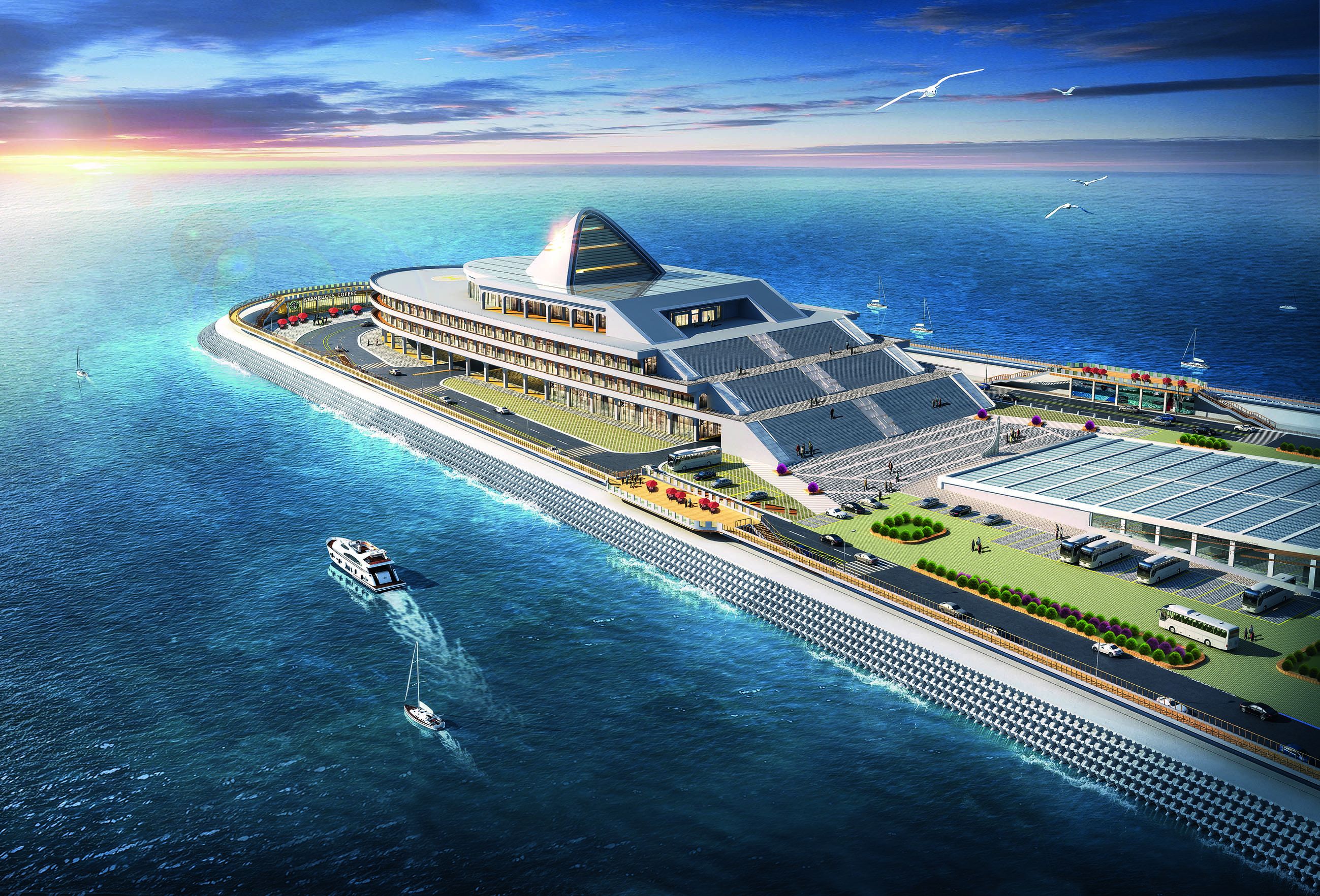
David Arminas reviews progress
China’s Spring Festival, or Lunar New Year, is celebrated with the usual enthusiasm and spectacular fireworks. But celebrations will be particularly joyous for many people in the southern Pearl River
People now rely on a ferry, a hydrofoil or an extensive drive of up to four hours to and from the mainland onto Hong Kong island by way of several small bridges.
The new 55km road, bridge and tunnel link spans the delta’s Lingdingyang channel via three cable-stayed bridges and one undersea tunnel (see box). A 38km main bridge-tunnel complex crosses over the delta between Zhuhai and Macao on the western side and Hong Kong on the eastern side. The 29.6km main section is in Zhuhai waters and comprises 22.9km of bridge work including three cable-stayed bridges with spans ranging from 280-460m, viaducts spanning 75m and 110m, a 6km tunnel and two artificial islands.
The second artificial island close to Hong Kong will host a customs and immigration terminal and allow direct access to Hong Kong International Airport. Commuters will take only around 45 minutes to get to Zhuhai from Hong Kong Airport, compared to four hours at present.
The Pearl River empties into the South China Sea, one of the world’s busiest maritime regions. The undersea tunnel is, in part, to accommodate heavy shipping traffic up the Pearl River without the encumbrance – and risk – of vessels having to negotiate bridges. Traffic congestion should also be alleviated at the crossing’s Hong Kong-Shenzhen border checkpoints for Hong Kong’s airport.
The HZMB has been a long time coming. Construction began in December 2009. However, delays occurred up to 2011 because of a legal challenge over the bridge’s environmental impact. Work intensified in 2011 when construction formally began on the Hong Kong side of the project. The final bridge tower was completed in June 2016. The immersed tunnel consists of 33 elements, including 28 straight and five curved, for a total length of nearly 5.7km. The final tunnel element was installed in May last year.
Construction of the main 29.6km section consisting of the 22.9km bridge section and the 6.7km tunnel (including the tunnel's exit and entrances) was finished in July 2017.
The original cost was estimated at nearly US$16 billion, but construction delays of up to two years added around $1.5 billion, according to estimates by Hong Kong’s Transport and Housing Bureau in November last year. The project costs will be shared by mainland authorities Hong Kong and Macao.
The Beijing government sees the HZMB as key to developing what it calls a Greater Bay Area incorporating Hong Kong and Macao as well as nine fast-growing industrial cities in Guangdong Province. With a population of about 67 million, the area boasted a gross domestic product of $1.38 trillion in 2016 - about 10% of China’s overall economy.
HZMB should be of particular economic benefit to the former Portuguese colony Macao that reverted back to Chinese rule at the end of 1999. Macao has long been seen as a casino town languishing economically in the shadows of its booming Shenzhen and Hong Kong cross-delta neighbours.
Experience counts
The central element of the project is the 6km immersed tunnel, the longest in the world and with a design life of 120 years. The tunnel, as well as the bridge, can withstand earthquakes of up to 8.0 on the Richter Scale. The bridge, too, has been designed to handle wind speeds of 200kph.
The channel is one of the busiest shipping routes between the Pearl River and South China Sea. Because of this, the six-lane tunnel is 45m below the water’s surface near the western area of the approach flight path for Hong Kong’s airport on Chek Lap Kok Island. Two artificial islands form the transitions between the tunnel and bridge structures.
The tunnel’s elements were manufactured on land near the sea at a site that had a dry dock. German-based formwork specialist
Peri used two hydraulically-operated shuttering machines to make the 33 tunnel elements. Each standard element is 180m long, 38m wide, 11.4m high and weighs around 72,000tonnes. Manufacturing was done by
what Peri calls the “incremental launching method”.
Peri’s production line could manufacture two tunnel tubes side by side and consisted of a centrally-positioned service gallery. This hydraulically-operated formwork solution consists of several main structural components: slab formwork, two external and three internal sets of formwork.
In addition, two different sets of stopend formwork ensured correct positioning for making a seal between the individual segments as well as at both ends of each element.
Together with the 50m-long truss girders in the centre, the internal formwork forms a horizontal moving device to return to the concreting position after each operation and retract into the prefabricated reinforcement cages.
The benefit of the process, according to Peri, is that the bottom plate, external walls and slab can be constructed monolithically and, in particular, without anchors. As a result, thousands of tie-points were eliminated which minimises the potential for leaks.
The completed elements – with temporary seals at both ends - were moved hydraulically onto pontoons in a drydock, refloated and towed into position in the river. The elements were then sunk into position on the seabed, connected and the seals removed.
Construction of the tall side and centre walls for the tunnel openings on the islands, as well as the breakwater, was carried out using mobile Peri Portal Formwork Carriages.
The six-lane road is around 56m wide as it comes off and on the bridge at a 3% gradient. The portals have 300m-long side walls as well as a 300m-long wall separating the road directions; the walls are 2.5m thick. The central separating wall - taller than the other two walls - also supports the portal’s roof. Peri used SB4 architectural concrete quality with a clearly structured joint and tie arrangement to ensure water impermeability in the long term.
Construction of the extensive architectural concrete walls was carried out largely without cranes. Peri designed mobile portal wall formwork carriages which operated independently of each other. The system consisted of components from Peri’s Variokit Engineering Construction system, Vario Girder Wall Formwork system and SK anchor technology. Concreting was done in regular cycle lengths of 15m while the entire height of each wall section was constructed in one pour.
Paving for performance
The main bridge deck section on the Chinese mainland side was completed last summer.
The deck required the most stringent specifications to handle extreme conditions such as high air temperatures and humidity, as well as high salt content in the air. Expected heavy traffic loads on the bridge and extreme vibrations caused by strong winds along the Lingdingyang channel also affected pavement design.
Factoring in anti-deformation and anti-rutting requirements meant the challenges mounted for whichever company supplied the pavement.
The bridge’s steel box-girder design means that the pavement is getting a double hit from its environment, explains Jia Lu, Shell
Bitumen’s senior application specialist regional technology Asia. “Pavement temperature could be 5-10°C higher than normal pavement structure. Because the top of the pavement is suffering a heat exchange from solar radiation and radiation from the water, as expected.
“But at the same time, the special chamber structure of the box beam makes it more difficult for the bridge including the pavement to dissipate its heat soak,” says Lu.
Shell rose to this challenge with its Shell Bitumen 60-70, Shell Cariphalte polymer modified bitumen products, Shell Flintkote Bridgecoat and Shell Spramul TCX-1 tack coat. The deck used enough bitumen to produce 700,000m² of asphalt.
“Shell Flintkote bridge coat was applied directly onto the concrete surface of the deck as a waterproofing system in the Hong Kong section,” says Lu. “Shell Cariphalte and TCX-1 were applied on the waterproofing layers and specially developed geosynthetic waterproofing materials.
A Stirling job
Main bridge deck waterproofing was done by UK coating manufacturer Stirling Lloyd, recently acquired by GCP Applied Technologies.
Carl Pearse, Stirling Lloyd’s regional manager for the Asia Pacific region where he has been working with contractors for several years, says there has recently been a surge in demand from highway and bridge developments in Asia.
“Our experience of waterproofing steel orthotropic bridges with Gussasphalt and Mastic Asphalt in similar environmental conditions has helped us secure a number of recent competitive tenders,” says Pearse. The Hong Kong-Zhuhai-Macao Bridge at 500,000m² is the largest single bridge deck project in which the company’s Eliminator waterproofing system has been applied.
“Eliminator is based on the company’s Esselac resin technology, which protects against corrosion and contributes to achieving a predicted minimum 120-year design life,” says Pearse. “The system holds a decade-long, successful track record both globally and on major bridges in Hong Kong in similar marine environments.”
Eliminator waterproofing was applied to around 500,000m² of the three steel navigation bridge sections in mainland China waters. Other sections of this continuous almost-50km route include the concrete viaduct stretches and tunnel. The process starts with the sanding down of any rust to reveal bright steel to the specified profile. The surface profile is then verified before the application by roller of anti-corrosion metal primer Zed S94 which enhances the strong bond of the subsequent Eliminator membrane to the deck.
In situ quality assurance checks are conducted pre-, during and post-application to ensure a high-quality and effective application.
“Pre-application adhesion checks are conducted, before the primer is applied to the full deck to confirm the adhesion values that will be achieved. Once the required value has been confirmed, the primer is applied to the full deck followed by the distinctive yellow first coat of the Eliminator waterproofing membrane. This is spray applied to the required thickness.
Wet film thickness gauges ensure the specified dry film thickness is achieved across the area. Once cured, checks are made to confirm a defect-free, full coverage application before the second coat - a pigmented white membrane - is applied. This provides an extra protection against the unlikely incidence of pinholes, which are invisible to the naked eye, enabling better quality control and ensuring an even thickness.
“Working in Asia’s warm climate, means that the fast curing flexible resins harden within minutes and fully cured in just half an hour,” explains Pearse.
To ensure an unblemished finish first time, the detailed central areas and edges were sprayed using hand-guns. However, due to the large scale of the application, the main deck areas were sprayed using automated spray machines.
“To complete the waterproofing, a thinner layer of red Tack Coat No. 2 is applied. This tack coat dries quickly to a hard surface, which is resistant to the wheel loads of the asphalt paving plant.”
The 230°C hot-poured asphalt is applied directly to this heat-activated tack coat. As it cools, a strong chemical bond is formed, allowing the entire pavement system to dissipate the considerable stresses and strains from traffic loading and structural movements.
While a project on such a scale as the HZMB can make life easier and – hopefully – more prosperous, there are often glitches along the way. However, regardless of the project's major travails, harried commuters between Hong Kong, Zhuhai and Macao will sigh with relief as they cruise along the new mega-crossing for a minor half hour.
Boundary Crossing Facilities
The main HKZM bridge including a tunnel runs from Zhuhai and Macao across the delta to a 150hectare artificial island next to Hong Kong’s airport. The island is, in fact, the border crossing into Hong Kong as well as the access point to the airport. Around 250,000 passengers and 60,000 vehicles are expected to pass daily through the 40,000m² passenger clearance building which lies under an intricate and structurally complicated steel roof.
A Leighton-Chun Wo Joint Venture is responsible for construction of the $1.08 billion building and associated works. Hong Kong-based Leighton Asia is part of the Australian group CIMIC - Construction, Infrastructure, Mining and Concessions – a subsidiary of
Included in the building works are drop off deck and area footbridges as well as a district cooling system for the Hong Kong Boundary Crossing Facilities. The scope includes bored pile foundations, reinforced concrete structures, profiled steel roof, curtain walling and glazing, architectural finishes and mechanical and electrical work.
Each curved steel roof segment, manufactured on mainland China, is 60m x 25m and weighs around 670tonnes. Because of the closeness of the building to the airport runways, a height restriction meant cranes could not hoist the segments into place. Instead, they were moved horizontally onto twin rails, slid into position and then hydraulically jacked up into their final position.
There were eight main contractors whose own BIM programmes were combined into one overall BIM platform from
Key players
The Dragages-China Harbour-VSL joint venture was awarded a contract worth nearly $1.4 billion in 2012 to design and build the 9.4km Hong Kong viaduct section of the bridge. It runs from the International Airport Island to the boundary of Hong Kong territorial waters and is the largest single design and build contract awarded in Hong Kong.
The joint venture is also carrying out the electrical and mechanical engineering works, the installation of marine navigational aids, a ship-impact protection system, as well as the maintenance and monitoring management systems for the structure of the bridge. Ove Arup & Partners Hong Kong was also involved in design work. Meanwhile
Fast and spectacular
Shell Bitumen have been involved with the bridge deck project since 2013. “We were providing technical support and consulting on materials selection and design,” notes Jason Wong, global vice president for Shell Bitimen.
Apart from his professional connection to the bridge through Shell Bitumen, Wong, who is 46 and born in Hong Kong, has a very personal interest in the project. He remembers the long journeys as a child from Hong Kong to visit his cousins in Macau, around 65km away and just off China’s southern coast.
“The ferry ride took four hours and the sea could get very, very rough,” he recalls. “People would be vomiting into the sea. It was not a pleasant voyage.”
The often-bumpy hydrofoil ferry route, although a vast improvement on those ferry ship days, still takes about an hour, he says. But when the bridge is opened this year, Hong Kong to Macau will be an easy and smooth - as well as spectacular - half-hour drive.