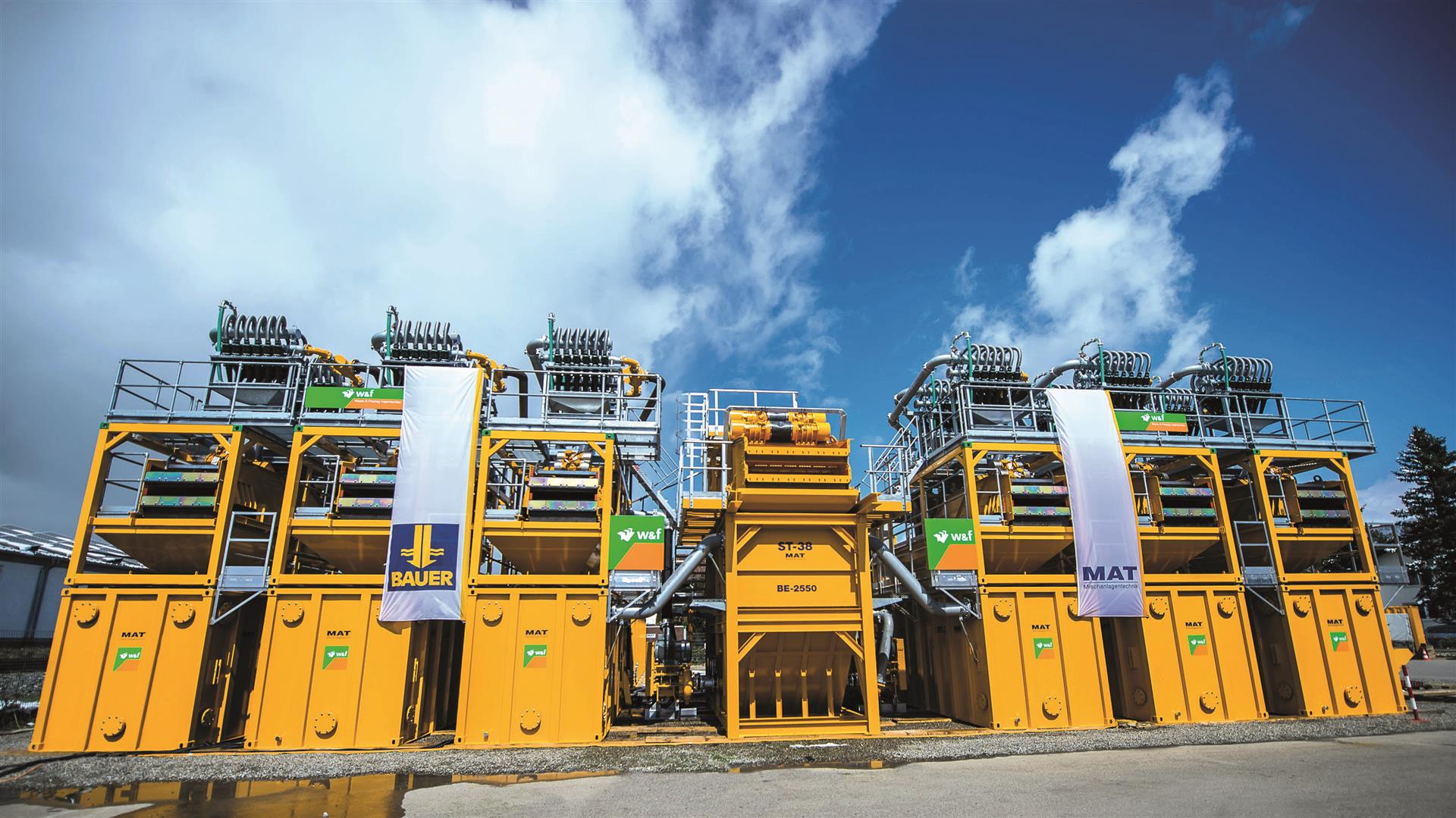
The double-track Eppenberg tunnel in the Swiss canton of Solothurn is about 2.6 km long and is one of the busiest railway routes in Switzerland. Since November 2016, a 2,400tonne tunnel boring machine measuring around 115m long and 12.75m in diameter has been drilling through the mountain. The machine has been operating in the open mode hard rock until now; for the remaining 700m, the fluid-supported slurry technology will be used.
Since August 7, MAT Mischanlagentechnik has been using the BE-2550 – 22m long and 26m wide - for this last but crucial section of the tunnel which is due for a breakthrough this winter. The BE-2550 is made up of six adjoining and identical standalone plants of type BE-425-60 that can move around 2,400m³ of slurry hourly in a closed circuit system. The entire plant was enclosed to cut noise pollution and protect it against ice and snow. The bentonite slurry transports the excavated material continuously to the separating plant via a 3km pipeline. In the separation plant, the bentonite slurry is separated from the soil in multiple processes using screens and hydrocyclone. Thereafter it is once again fed into the slurry circuit and delivered to the TBM cutter head. Two SKC-60-K continuous mixing plants ensure continuous production of bentonite slurry.
Logistics has been a crucial success factor, according to the company. On site, all necessary tools, machine components and construction site equipment, as well as qualified personnel, had to be in the right place at the right time for assembly and commissioning.
Factory acceptance testing took place in Immenstadt, where 25 trucks were loaded in only five working days. Commissioning was done in Switzerland, where every truck arrived at the construction site as scheduled.