Major advances in tunnelling will allow cars to travel underneath the Bosphorus sea channel in Turkey's Istanbul next year when its third road link is opened, writes Adrian Greeman. The Bosphorus is redolent with history and strategic significance. As one of the world's most significant sea connections, linking the landlocked Black Sea to the Marmara Sea and the Mediterranean beyond, it has been vitally important for trade and crucial for military access. It is also one of the biggest obstacles for land tra
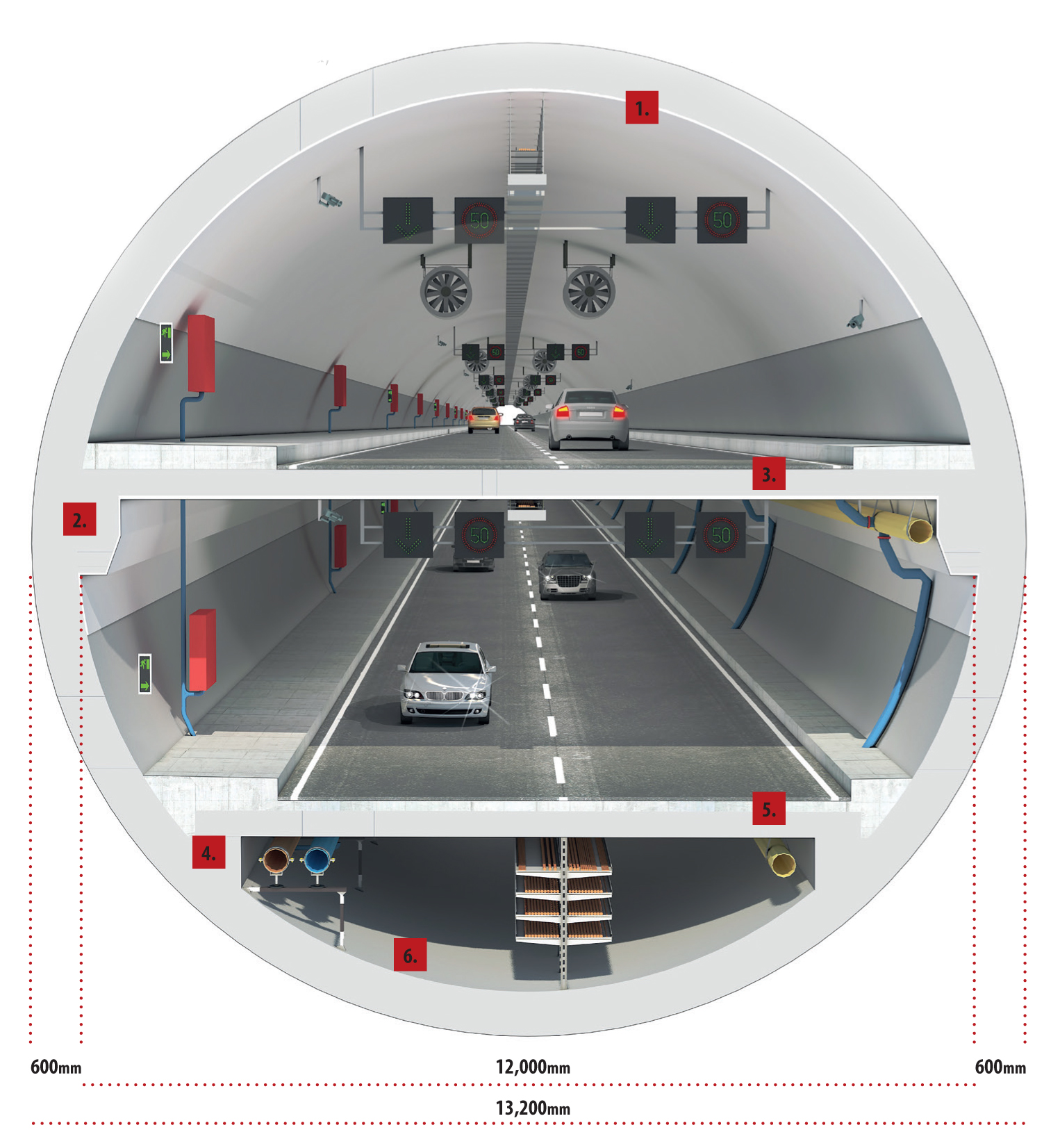
Bored Tunnel (TBM): 1. Precast segment lining (t=600mm) 2. Upper corbel 3. Upper roadway deck (cast in situ) 4. Lower corbel 5. Lower Roadway deck (precast) 6. Utility gallery
Major advances in tunnelling will allow cars to travel underneath the Bosphorus sea channel in Turkey's Istanbul next year when its third road link is opened, writes Adrian Greeman
The Bosphorus is redolent with history and strategic significance. As one of the world's most significant sea connections, linking the landlocked Black Sea to the Marmara Sea and the Mediterranean beyond, it has been vitally important for trade and crucial for military access.
It is also one of the biggest obstacles for land transport, famously separating the Asian and European continents and until the last century dividing the sprawling mass of Turkey's biggest city in two. The two halves of Istanbul still have different characters.
Crossing the Bosphorus has never been easy. The sinuous waterway is between 750m and 3.5km wide and one of the world's busiest shipping channels. In classical times Persian king Darius used linked barges to get his cavalry over, hardly possible nowadays with a constant stream of oil tankers, freighters and occasional naval vessels.
There are bustling ferries of course but it was only in the latter part of the twentieth century that permanent links were made, as first one and then a second high suspension bridge connected its steep banks. For obvious reasons they cross the narrower central channel while a third bridge is now in construction near the Black Sea. That will complete a major ring motorway to divert long-distance transit traffic and trucks from the city centre.
These crossings still mean substantial round trips for many from the busiest parts of the city, which lies at the southern end of the channel. The European side contains the famous Golden Horn inlet and the historic peninsula of one time Constantinople, with its dramatic skyline of ancient mosques, palaces and the 6th century Hagia Sofia; on the Asian side are some of the city's major port facilities and residential areas.
The main airport for Istanbul lies on the Marmara sea coast too while its second, almost as busy, sits on the Asia side. Transit between the two is difficult via the existing bridges.
A road link for these has had to wait. The channel is wide here and a bridge is not really acceptable, as it would block the historic views. But a tunnel is more expensive and until recently not feasible, because of the depth of the water, meaning very high pressures in the fractured rock.
A first Bosphorus tunnel was recently completed in 2013 with a 1.4km immersed tube section for the overall 8.5km Marmary rail tunnel. At 56m deep it is only rivalled by South Korea's Busan-Geoje immersed tube highway tunnel.
For a new road link it has been necessary to go where the channel is even deeper at 64m to the seabed. That will allow an alignment across the southern channel, with a tunnel section of just over 5km long in total. But with 5% maximum gradient even that means a vertical alignment of the tunnel which takes it to a challenging 106m deep point in the rock.
The tunnel is part of an overall 14.6km highway link being built for the Turkish Ministry of Transport. Existing roads along the Marmara coast are being widened to eight lanes to greatly ease traffic congestion from the main Ataturk airport and along the route around the historic peninsula. Traffic will then dip into the tunnel and cross to the Asian city on the far side before connecting onwards to the city's second airport.
"When finished the whole scheme will reduce a journey that currently takes over one and a half hours to just 15 minutes" said Bahriye Yaman. She is TBM methods chief on the project for the Turkish main contractor7010 Yapi Merkezi. The firm is in joint venture with Korean firm SK Engineering and Construction, under the unsurprising name of YMSK JV.
The project is being done as a BOT scheme with a 21-year payback period. Tolls will be $4 and the tunnel will carry only cars and light freight vehicles.
Yaman's part of the project is the most challenging, namely the tunnel itself and particularly the 3.34km-long central bored section which actually passes below the sea. Within this main bore the road is configured on two decks, one for each direction of two lanes and an emergency shoulder. Sealed emergency stairs connect the decks every 200m so that each can serve as an escape route in the event of fire or disaster on the other level.
At either end these two carriageways separate again into individual tunnels constructed by various conventional means including two excavated NATM tunnels of 900m length, cut and cover sections and then open topped sunken approaches. Designer for all the tunnel works is2693 Parsons Brinckerhoff.
Because it will be used only for mini-buses and car traffic the road decks in the main tunnel can be restricted in height to 3.8m but even so the required diameter is significant, some 12m internally. Given a segment lining thickness of 600mm and a 250mm grouted annulus this means a TBM of 13.7m outer diameter was needed, the sixth largest in the world to date, said Yaman.
It has also had to be one of the most advanced. Without significant developments in technology, including new monitoring instruments for the cutterhead, atmospheric pressure for changing cutterdiscs, and built-in access for the diving team, the drive would either have been impossible or have taken very much longer than the 16 months needed.
The problem is water which penetrates all the ground and means the tunnelling is being done as if at the bottom of the sea, with corresponding pressures. About 40% of this drive is through soft alluvial deposits in the channel and the remainder in rock.
"There are cracks throughout the harder rock which means the water penetrates right through," said Yaman.
The Bosphorus is thought to have originated as a river channel initially, carved much deeper during post-glacial times when sea levels rose and the Mediterranean spilled into an isolated lake basin now holding the Black Sea. It may have happened in one cataclysmic inundation – some say the origin of biblical flood myths - or over a long period as sea levels rose. Subsequent inter-sea flows have partly filled the deep channel with sediments, mostly silts and sands.
The rock is mainly weak mudstones and harder sandstone, according to project geologist Ayalin Bakir. It has been shattered by substantial activity in this earthquake prone area where the Turkish tectonic plate crashes into Europe and Arabia. The devastating Izmit earthquake of 1999 just to the south-east was the last in a chain of many events along the fault line.
Extra difficulties for tunnelling are caused by old volcanic intrusions into the cracks, forming sandwiches of very hard rock, some thin and some up to 200m thick. But other cracks are filled with clay sediment. That means the rock face can be banded with layers of extreme hardness and softness.
All that is difficult for a tunnel machine which is designed for one type of ground or another said Gert Wittneben, TBM construction manager with the consortium. It also makes the rock "blocky" with a tendency for large chunks to slip from the face as it is excavated, causing instability and possible damage to the TBM intakes.
"I don't think the face was stable at any point along the route," said Yaman. In some places the clay intrusions also caused clogging.
All this had to be considered when selecting and designing a machine for the drive supporting a mixed face in hard and soft ground at pressure. The choice was a slurry Mixshield machine from Germany's2592 Herrenknecht, to a design which has evolved from a series of increasingly high pressure machines made by the German company, including that for the fourth Elbe road crossing in Hamburg and the Westerschelde in Belgium.
The cutting face has both rock discs mounted on six large arms and soil knives mounted over the spoil entry. Design also took advice from local geology specialists, leading to additional grill bar protection at the front against blocks.
The machine features built-in provision for saturation diving interventions. This is where divers use special gas mixtures and remain in compression, living in a special chamber above ground for up to a month, which allows for more immediate diver responses and longer working as high pressure, in this case up to 10 bar.
But to minimise diving the machine also had capacity to change cutter discs from behind the face at atmospheric pressure. The latter feature was first introduced on the Hamburg machine but in a more limited form for just some of the discs; here it allows outer and centre cutters to be changed and semi-automates the process with hydraulics. A new electronic monitoring system is part of it too, alerting crews when cutters are worn or broken.
That can be bad news as fragments loose in the cutterhead chamber can cause secondary damage, so it is important to stop and change it as quickly as possible.
An onboard rail system brings the pressurised diver transfer module to the face where it locks onto one of two airlocks, one for the main cutterhead and one for the central section. A scissor lift is built in at the end to lift the module to the airlock position.
The rail system can also be used to move the cutter discs which are removed and installed as integral units with their cylindrical housings, weighing over a tonne. "It is a 'luxury' feature," said Herrenknecht technical director Werner Burger, who added that various other hoists and lifts are also used.
All this came into play on the drive after it began in April last year. But first of all the contractor had to set up its sites. The main one is on the Asian side where a 30m-deep starter pit was constructed. A mass of ground anchors in its walls testify to the shattered nature of the rock around.
"It was not easy and took us over a year to excavate," said Yaman.
The 160m-long pit was partly the start point for the 120m-long TBM train but also a transition point into the shorter NATM approach tunnels. Work on those used the additional 40m section of the pit, above which a718 Liebherr tower crane sits.
The straightforward excavations, done with excavators, diverge as they head towards an interchange at the surface. They will be joined to the main bore by a concrete transition section being cast in the pit before it is backfilled.
Two Turkish Tisan portal cranes serviced the TBM drive, one for the general work and one mainly lifting the big segments onto French- made Metalliance rubber tyred transporters. The tunnel is using an eight segment plus half key ring configuration which means they are big segments, each 2m long and 4.2m wide around the ring. With a thickness of 600mm they weigh 14tonnes each.
The site itself is too tightly constrained for manufacture there and so they are made 30km away at a factory run by a Yapi subsidiary, Yapi Prefabrik. Segments arrive by truck with deliveries outside daytime hours of 10am to 5pm when city traffic is heavy.
Among the segments are special monitoring segments with cast-in electronic detectors for corrosion. These permanent monitors will help check tunnel integrity throughout its over-100-year lifespan. They are fitted every 100 rings.
There are also two points in the tunnel where special steel segments replace the normal ones for a seven segment length. These are backplates for special seismic joints for earthquake protection. The seismic joints themselves have been made by SEIBU POLYMER.
In the remaining space on site there is a slurry processing plant where the rock fragments are filtered out. As a slurry machine the TBM delivers its spoil to surface in a suspension of bentonite along pipelines in the tunnel. Separated spoil is loaded onto trucks and taken to a number of old quarries and disposal sites outside the city.
There is room for little else on site. The JV uses concrete from outside for in situ works in the tunnel. These follow on behind the TBM work with corbels added to the walls and then the now completed upper deck was cast using two big travelling gantries, first to assemble reinforcement and then concreting work in 12m sections. The lower deck is prefabricated and is being installed currently.
The TBM drive went extremely well according to Wittneben, averaging about 6.5m daily, just over three rings he says.
The complex machine took a little learning with a contract crew and Herrenknecht support engineers on site for the first 300m of the drive while the Turkish shift crews learned the ropes.
"But it has been virtually all Turkish workers since," he said, "with a very skilled operation."
The slipping face and some breakage did mean diver interventions had to be made several times. One was to deal with damage to the inlet jaw crusher which reduces bigger blocks coming off the face to a size suitable for the 550mm slurry and spoil removal pipeline.
Breakthrough was on 21st August last year into a transition pit on the European side. The big TBM was then cut up and transported back to Germany.
The tunnel is now being fitted with a lower deck and asphalting is underway, as well as the mechanical and electrical fittings for lighting, ventilation and road signs.
Outside work continues too on complex widening works for the highways and some large interchanges. According to Umut Arda Dündar, civil engineer in the technical section, the biggest of these is on the European side to allow access to a new public events area and ferry terminal. "The road has to be lowered by 7m along a 180m length and new pedestrian overpasses have to be built," he explained.
The project is due to open commercially in April 2017 with French company2643 Egis in charge of operations and maintenance.
Seismic activity
The highly active earthquake zone near Istanbul means additional protection is vital for the tunnel, allowing for up to an event of 7.5 magnitude.
To handle this, two points were identified in the tunnels by finite element analysis where maximum movement would occur. At this position an articulating joint is installed, built into a framework of seven special steel rings.
The joint must allow an expansion of up to 75mm or contraction by the same amount, or shear displacement of 50mm. This is achieved by use of a central ring, with two separate sides sealed with flexible joints. The ring is packed closely with hydraulic cylinders which act like shock absorbers to take up the displacements and which can twist to absorb shear.
On either side of this joint is a support ring. Beyond each of those, two further "transition rings" connecting to the main tunnel lining. The units were designed and manufactured in Japan which has long experience in this technology.
The Bosphorus is redolent with history and strategic significance. As one of the world's most significant sea connections, linking the landlocked Black Sea to the Marmara Sea and the Mediterranean beyond, it has been vitally important for trade and crucial for military access.
It is also one of the biggest obstacles for land transport, famously separating the Asian and European continents and until the last century dividing the sprawling mass of Turkey's biggest city in two. The two halves of Istanbul still have different characters.
Crossing the Bosphorus has never been easy. The sinuous waterway is between 750m and 3.5km wide and one of the world's busiest shipping channels. In classical times Persian king Darius used linked barges to get his cavalry over, hardly possible nowadays with a constant stream of oil tankers, freighters and occasional naval vessels.
There are bustling ferries of course but it was only in the latter part of the twentieth century that permanent links were made, as first one and then a second high suspension bridge connected its steep banks. For obvious reasons they cross the narrower central channel while a third bridge is now in construction near the Black Sea. That will complete a major ring motorway to divert long-distance transit traffic and trucks from the city centre.
These crossings still mean substantial round trips for many from the busiest parts of the city, which lies at the southern end of the channel. The European side contains the famous Golden Horn inlet and the historic peninsula of one time Constantinople, with its dramatic skyline of ancient mosques, palaces and the 6th century Hagia Sofia; on the Asian side are some of the city's major port facilities and residential areas.
The main airport for Istanbul lies on the Marmara sea coast too while its second, almost as busy, sits on the Asia side. Transit between the two is difficult via the existing bridges.
A road link for these has had to wait. The channel is wide here and a bridge is not really acceptable, as it would block the historic views. But a tunnel is more expensive and until recently not feasible, because of the depth of the water, meaning very high pressures in the fractured rock.
A first Bosphorus tunnel was recently completed in 2013 with a 1.4km immersed tube section for the overall 8.5km Marmary rail tunnel. At 56m deep it is only rivalled by South Korea's Busan-Geoje immersed tube highway tunnel.
For a new road link it has been necessary to go where the channel is even deeper at 64m to the seabed. That will allow an alignment across the southern channel, with a tunnel section of just over 5km long in total. But with 5% maximum gradient even that means a vertical alignment of the tunnel which takes it to a challenging 106m deep point in the rock.
The tunnel is part of an overall 14.6km highway link being built for the Turkish Ministry of Transport. Existing roads along the Marmara coast are being widened to eight lanes to greatly ease traffic congestion from the main Ataturk airport and along the route around the historic peninsula. Traffic will then dip into the tunnel and cross to the Asian city on the far side before connecting onwards to the city's second airport.
"When finished the whole scheme will reduce a journey that currently takes over one and a half hours to just 15 minutes" said Bahriye Yaman. She is TBM methods chief on the project for the Turkish main contractor
The project is being done as a BOT scheme with a 21-year payback period. Tolls will be $4 and the tunnel will carry only cars and light freight vehicles.
Yaman's part of the project is the most challenging, namely the tunnel itself and particularly the 3.34km-long central bored section which actually passes below the sea. Within this main bore the road is configured on two decks, one for each direction of two lanes and an emergency shoulder. Sealed emergency stairs connect the decks every 200m so that each can serve as an escape route in the event of fire or disaster on the other level.
At either end these two carriageways separate again into individual tunnels constructed by various conventional means including two excavated NATM tunnels of 900m length, cut and cover sections and then open topped sunken approaches. Designer for all the tunnel works is
Because it will be used only for mini-buses and car traffic the road decks in the main tunnel can be restricted in height to 3.8m but even so the required diameter is significant, some 12m internally. Given a segment lining thickness of 600mm and a 250mm grouted annulus this means a TBM of 13.7m outer diameter was needed, the sixth largest in the world to date, said Yaman.
It has also had to be one of the most advanced. Without significant developments in technology, including new monitoring instruments for the cutterhead, atmospheric pressure for changing cutterdiscs, and built-in access for the diving team, the drive would either have been impossible or have taken very much longer than the 16 months needed.
The problem is water which penetrates all the ground and means the tunnelling is being done as if at the bottom of the sea, with corresponding pressures. About 40% of this drive is through soft alluvial deposits in the channel and the remainder in rock.
"There are cracks throughout the harder rock which means the water penetrates right through," said Yaman.
The Bosphorus is thought to have originated as a river channel initially, carved much deeper during post-glacial times when sea levels rose and the Mediterranean spilled into an isolated lake basin now holding the Black Sea. It may have happened in one cataclysmic inundation – some say the origin of biblical flood myths - or over a long period as sea levels rose. Subsequent inter-sea flows have partly filled the deep channel with sediments, mostly silts and sands.
The rock is mainly weak mudstones and harder sandstone, according to project geologist Ayalin Bakir. It has been shattered by substantial activity in this earthquake prone area where the Turkish tectonic plate crashes into Europe and Arabia. The devastating Izmit earthquake of 1999 just to the south-east was the last in a chain of many events along the fault line.
Extra difficulties for tunnelling are caused by old volcanic intrusions into the cracks, forming sandwiches of very hard rock, some thin and some up to 200m thick. But other cracks are filled with clay sediment. That means the rock face can be banded with layers of extreme hardness and softness.
All that is difficult for a tunnel machine which is designed for one type of ground or another said Gert Wittneben, TBM construction manager with the consortium. It also makes the rock "blocky" with a tendency for large chunks to slip from the face as it is excavated, causing instability and possible damage to the TBM intakes.
"I don't think the face was stable at any point along the route," said Yaman. In some places the clay intrusions also caused clogging.
All this had to be considered when selecting and designing a machine for the drive supporting a mixed face in hard and soft ground at pressure. The choice was a slurry Mixshield machine from Germany's
The cutting face has both rock discs mounted on six large arms and soil knives mounted over the spoil entry. Design also took advice from local geology specialists, leading to additional grill bar protection at the front against blocks.
The machine features built-in provision for saturation diving interventions. This is where divers use special gas mixtures and remain in compression, living in a special chamber above ground for up to a month, which allows for more immediate diver responses and longer working as high pressure, in this case up to 10 bar.
But to minimise diving the machine also had capacity to change cutter discs from behind the face at atmospheric pressure. The latter feature was first introduced on the Hamburg machine but in a more limited form for just some of the discs; here it allows outer and centre cutters to be changed and semi-automates the process with hydraulics. A new electronic monitoring system is part of it too, alerting crews when cutters are worn or broken.
That can be bad news as fragments loose in the cutterhead chamber can cause secondary damage, so it is important to stop and change it as quickly as possible.
An onboard rail system brings the pressurised diver transfer module to the face where it locks onto one of two airlocks, one for the main cutterhead and one for the central section. A scissor lift is built in at the end to lift the module to the airlock position.
The rail system can also be used to move the cutter discs which are removed and installed as integral units with their cylindrical housings, weighing over a tonne. "It is a 'luxury' feature," said Herrenknecht technical director Werner Burger, who added that various other hoists and lifts are also used.
All this came into play on the drive after it began in April last year. But first of all the contractor had to set up its sites. The main one is on the Asian side where a 30m-deep starter pit was constructed. A mass of ground anchors in its walls testify to the shattered nature of the rock around.
"It was not easy and took us over a year to excavate," said Yaman.
The 160m-long pit was partly the start point for the 120m-long TBM train but also a transition point into the shorter NATM approach tunnels. Work on those used the additional 40m section of the pit, above which a
The straightforward excavations, done with excavators, diverge as they head towards an interchange at the surface. They will be joined to the main bore by a concrete transition section being cast in the pit before it is backfilled.
Two Turkish Tisan portal cranes serviced the TBM drive, one for the general work and one mainly lifting the big segments onto French- made Metalliance rubber tyred transporters. The tunnel is using an eight segment plus half key ring configuration which means they are big segments, each 2m long and 4.2m wide around the ring. With a thickness of 600mm they weigh 14tonnes each.
The site itself is too tightly constrained for manufacture there and so they are made 30km away at a factory run by a Yapi subsidiary, Yapi Prefabrik. Segments arrive by truck with deliveries outside daytime hours of 10am to 5pm when city traffic is heavy.
Among the segments are special monitoring segments with cast-in electronic detectors for corrosion. These permanent monitors will help check tunnel integrity throughout its over-100-year lifespan. They are fitted every 100 rings.
There are also two points in the tunnel where special steel segments replace the normal ones for a seven segment length. These are backplates for special seismic joints for earthquake protection. The seismic joints themselves have been made by SEIBU POLYMER.
In the remaining space on site there is a slurry processing plant where the rock fragments are filtered out. As a slurry machine the TBM delivers its spoil to surface in a suspension of bentonite along pipelines in the tunnel. Separated spoil is loaded onto trucks and taken to a number of old quarries and disposal sites outside the city.
There is room for little else on site. The JV uses concrete from outside for in situ works in the tunnel. These follow on behind the TBM work with corbels added to the walls and then the now completed upper deck was cast using two big travelling gantries, first to assemble reinforcement and then concreting work in 12m sections. The lower deck is prefabricated and is being installed currently.
The TBM drive went extremely well according to Wittneben, averaging about 6.5m daily, just over three rings he says.
The complex machine took a little learning with a contract crew and Herrenknecht support engineers on site for the first 300m of the drive while the Turkish shift crews learned the ropes.
"But it has been virtually all Turkish workers since," he said, "with a very skilled operation."
The slipping face and some breakage did mean diver interventions had to be made several times. One was to deal with damage to the inlet jaw crusher which reduces bigger blocks coming off the face to a size suitable for the 550mm slurry and spoil removal pipeline.
Breakthrough was on 21st August last year into a transition pit on the European side. The big TBM was then cut up and transported back to Germany.
The tunnel is now being fitted with a lower deck and asphalting is underway, as well as the mechanical and electrical fittings for lighting, ventilation and road signs.
Outside work continues too on complex widening works for the highways and some large interchanges. According to Umut Arda Dündar, civil engineer in the technical section, the biggest of these is on the European side to allow access to a new public events area and ferry terminal. "The road has to be lowered by 7m along a 180m length and new pedestrian overpasses have to be built," he explained.
The project is due to open commercially in April 2017 with French company
Seismic activity
The highly active earthquake zone near Istanbul means additional protection is vital for the tunnel, allowing for up to an event of 7.5 magnitude.
To handle this, two points were identified in the tunnels by finite element analysis where maximum movement would occur. At this position an articulating joint is installed, built into a framework of seven special steel rings.
The joint must allow an expansion of up to 75mm or contraction by the same amount, or shear displacement of 50mm. This is achieved by use of a central ring, with two separate sides sealed with flexible joints. The ring is packed closely with hydraulic cylinders which act like shock absorbers to take up the displacements and which can twist to absorb shear.
On either side of this joint is a support ring. Beyond each of those, two further "transition rings" connecting to the main tunnel lining. The units were designed and manufactured in Japan which has long experience in this technology.