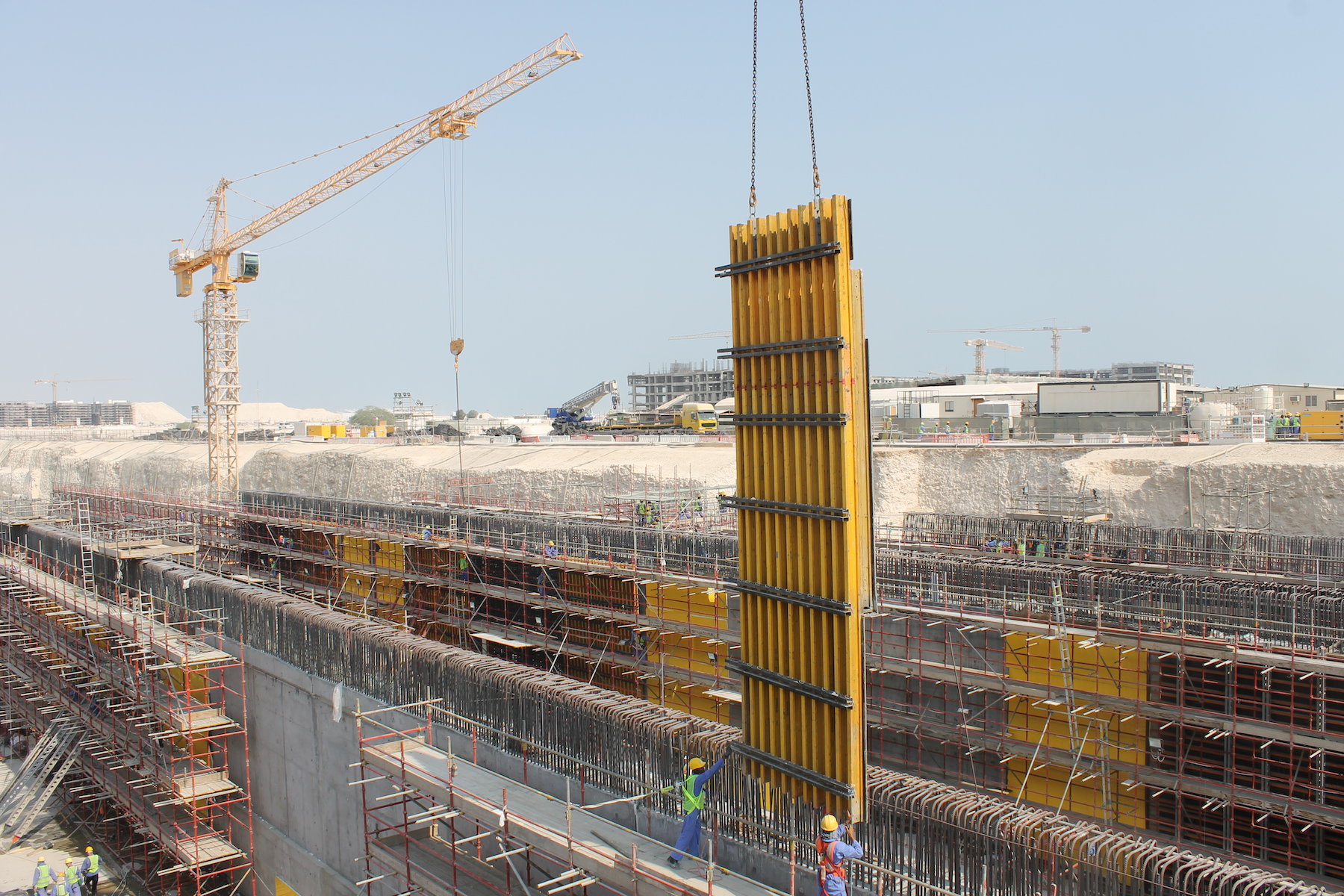
The formwork system was supplied by ULMA, which supplied its equipment for the construction of the
The tunnel project consisted of the construction of a cut-and-cover road-rail tunnel, including the mechanical systems and services necessary for the A3 Expressway. The tunnel is 655m in length and is 45m wide, with separate tubes that run alongside each other. The central tube is dedicated to light rail traffic, with twin lines that run in each direction. The project is extensive and its construction required 300,000m³ of concrete. The construction of this new underground infrastructure posed a challenge due to a combination of complex ground conditions with a high water table and the need for fast track building.
Close collaboration between ULMA and its distributor in this area of the Middle East, DELMON, has been an important factor for the comprehensive formwork solution provided for this construction project. The ULMA and DELMON team supplied the necessary formwork for the walls and slabs of the central tube, measuring 20m in width, as well as the lateral tubes, each of which are 13m wide. The walls are 2m thick at the base, and thin to 1m at the highest point of 13m. The ceiling slab, 1.8m thick, was built to be straight, though slightly inclined, throughout almost the entire length of the tunnel.
The client required that all tunnel sidewalls, even for those reaching 13m tall, be executed in a single pour. At these heights the fresh concrete can exert enormous pressure on the formwork, and with more than 3.6km of sidewall to pour, the solution had to be robust, yet quick to install and easy to use. Components of the beam formwork system ENKOFORM V-100 were used to withstand all of the pouring pressure required. According to ULMA, the simplicity of the system provided a level of productivity that exceeded customer expectations.
With the client’s requirements at the forefront, the solution that provided savings in the set-up and take-down for every pour.
Close collaboration between ULMA and its distributor in this area of the Middle East, DELMON, has been an important factor for the comprehensive formwork solution provided for this construction project. The ULMA and DELMON team supplied the necessary formwork for the walls and slabs of the central tube, measuring 20m in width, as well as the lateral tubes, each of which are 13m wide. The walls are 2m thick at the base, and thin to 1m at the highest point of 13m. The ceiling slab, 1.8m thick, was built to be straight, though slightly inclined, throughout almost the entire length of the tunnel.
The client required that all tunnel sidewalls, even for those reaching 13m tall, be executed in a single pour. At these heights the fresh concrete can exert enormous pressure on the formwork, and with more than 3.6km of sidewall to pour, the solution had to be robust, yet quick to install and easy to use. Components of the beam formwork system ENKOFORM V-100 were used to withstand all of the pouring pressure required. According to ULMA, the simplicity of the system provided a level of productivity that exceeded customer expectations.
The ceiling slab measuring, 30,000m2 with a thickness of 1.8m, was built at a height of 9m aboveground. The T-60 Shoring Towers proved very useful for this situation. These towers were combined with a pre-assembled table formwork system transported by bogie to save both time and work.
With the client’s requirements at the forefront, the solution that provided savings in the set-up and take-down for every pour.